Принцип работы доменной печи. Конструкция доменной печи и ее вспомогательных устройств Что представляет собой современная доменная печь
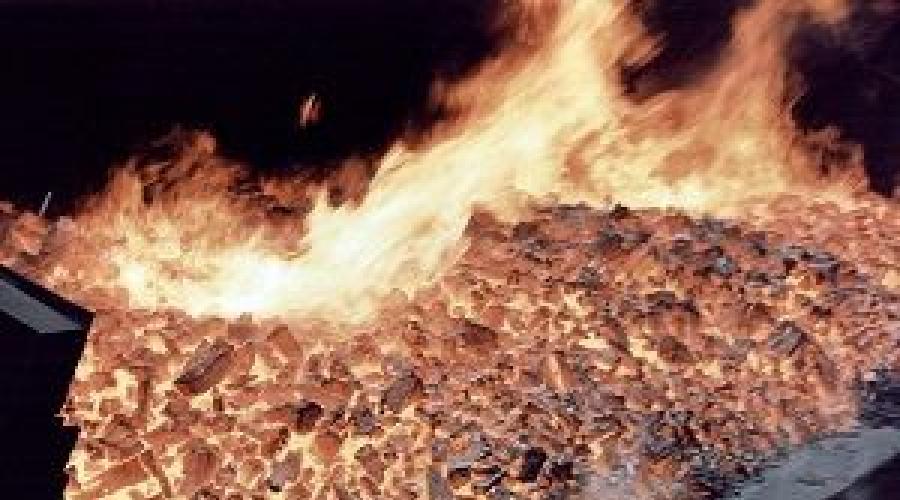
Читайте также
Шихтовые материалы в – доменную печь загружают сверху, снизу подают воздух для сжигания топлива. Продукты доменной плавки - жидкий чугун и шлак - выпускают снизу. Профиль внутреннего, плавильного пространства доменной печи выбран таким образом, чтобы в нем происходило равномерное опускание загруженных материалов и равномерное распределение выделяющихся
Рис. 16. Профиль доменной печи:
1 - колошник; 2 - шахта; 3 - распар; 4 - заплечики; 5 - горн
Рис. 17. Общий вид доменной печи:
1 - летка для выпуска чугуна; 2 - фурменное устройство для подачи комбинированного дутья; 3 -цилиндрическая часть колошника с защитными плитами; 4 - большой коиус колошника; 5 - малый конус колошника; 6 - устройство для вращения приемной воронки; 7 - приемная воронка; 8 - скип; 9 - наклонный мост; 10 - межконусное пространство; 11 - летка для выпуска шлака; 12 - площадка
Газов по сечению печи. Газы поднимаются снизу вверх. Профиль печи. На рис. 16 представлен профиль современной доменной печи . Верхняя часть печи называется колошником (от слова колоша: так называли короба, в которых перевозили уголь для загрузки в печь).
Через колошник печи, имеющий форму цилиндра, производится загрузка шихты и отводятся газы. Ниже колошника расположена UiaxTai представляющая собой усеченный конус, расширяющийся книзу. Такая форма шахты позволяет материалам расползаться в стороны и свободно опускаться вниз. Кроме того, расширение шахты устраняет уплотнение шихты. Наиболее широкая часть печи - распар - представляет собой короткий цилиндр, необходимый для создания плавного перехода от нижнего широкого основания шахты к сужающимся заплечикам - части печи, которая представляет собой усеченный конус с широкой частью вверху и узкой внизу. Если бы шахта непосредственно соединялась с заплечиками, то в месте их соединения образовывался тупой угол, в котором задерживались опускающиеся сырые материалы. Наличие распара сглаживает переход и устраняет мертвое пространство. Заплечики приобрели сужающуюся конусообразную форму потому, что в них происходит резкое сокращение объема загруженных материалов в связи с выгоранием кокса и образованием жидких продуктов плавки.
Нижняя часть печи представляет собой цилиндрический горн, в котором накапливаются жидкие продукты плавки - чугун и шлак. В нижней части горна расположены отверстия - летки для выпуска чугуна, в верхней части горна находятся фурмы, через которые в печь подается воздух.
Рассмотрим более подробно устройство основных частей доменной печи, общий вид которой представлен на рис. 17.
Фундамент печи. Современная печь вместе со всеми сооружениями и металлоконструкциями, футеровкой и находящимися в ней шихтовыми материалами и продуктами плавки может иметь массу до 30 тыс. т. Эта масса должна быть равномерно передана грунту. Нижнюю часть фундамента (подошву) делают в виде восьмиугольной бетонной плиты толщиной до 4 м. На подошву опираются колонны, поддерживающие металлические конструкции печи (кожух).
Верхняя часть фундамента - пень - представляет собой монолитный цилиндр из жароупорного бетона, на котором и находится горн печи.
Горн (рис. 18) может быть разделен на три части. Нижняя, плоская часть горна - это лещадь, на которой находится жидкий чугун и шлак. Лещадь выдерживает ¦большое давление чугуна. Она выкладывается из углеродистых блоков снаружи, изнутри из крупноразмерного высокоглиноземистого кирпича, содержащего более 45% AI2O3. Общая толщина лещади достигает 5,5 м. Лещадь находится под воздействием высоких температур и гидростатическим воздействием жидкого чугуна. Жидкий
Рис. 18. Схема горна доменной печи:
I - бетонная подошва печи; 2- пень печи; 3- углеродистые блоки лещади горна; 4- высокоглиноземистый кирпич; 5 - чугунные плитовые холодильники
Чугун проникает между кирпичами по швам и расклинивает кладку. Происходит разрушение лещади, особенно сильное в первое время после начала работы. Для сохранения лещади в печи поддерживают «мертвый слой» жидкого чугуна толщиной до 1000 мм, который не выпускают из печи. На крупных печах лещадь полностью выкладывают из углеродистых огнеупоров.
Вторая нижняя часть горна - от лещади до леток (металлоприемник) - служит копильником для расплавленного чугуна и шлака. Металлоприемник выкладывается из углеродистых блоков на углеродистой пасте. Фурменные проемы, чугунные и шлаковые летки выкладываются шамотным кирпичом. Внизу кладка имеет толщину до 1500 мм, в верхней части 325 мм. Кладка лещади и металлоприемника охватывается плитовыми холодильниками, представляющими собой металлические плиты с трубами, по которым циркулирует вода.
Между лещадью и пнем в некоторых печах помещают металлические плиты с пазами для воздушного охлаждения. Снаружи плитовые холодильники и горн заключены в металлический кожух из листов толщиной 40-50 мм. Для компенсации теплового расширения кладки нижней части горна между холодильниками и кладкой
Оставляют зазор ~100 мм, который заполняется плотно утрамбованной углеродистой массой. В нижней части горна на расстоянии 600-1700 мм от лещади располагаются отверстия - летки для выпуска чугуна и шлака. В печах с объемом до 2000 м3 делают одно отверстие, в более крупных печах - до четырех. Через чугунные
Чугун. Чугунная летка обрамляется стальной литой рамой, прикреп-
Ленной к кожуху печи (рис. 19). Проем рамы футеруется высокоглиноземистым кирпичом. Оставляют сквозной канал шириной 300 и высотой 400-500 мм, который забивают огнеупорной массой. Для выпуска чугуна в нем прорезают отверстие диаметром 50-80 мм. После выпуска чугуна канал летки вновь забивают огнеупорной массой.
Выше уровня чугунной летки на 1400-1800 мм располагаются шлаковые летки, предназначенные для выпуска верхнего шлака. Шлаковые летки располагаются под углом 90° друг к другу и под углом 60° к чугунной летке. На печах среднего размера делают две, а на больших печах одну летку для выпуска шлака.
Рис. 19. Устройство чугунной леткн: ЛеТКИ 18 20 раз B CyT-
/- футляр нз огнеупорной массы; 2- КИ ВЫПуСКаЮТ ЖИДКИЙ
Огнеупорная кладка; з - рама; 4 - холодильник
В проем шлаковой летки устанавливается шлаковый прибор, схема которого приведена на рис. 20. Основные части шлакового прибора: медная водоохлаждаемая фурма, медный холодильник, чугунный холодильник с залитым спиральным змеевиком для воды, чугунная водоохлаждаемая амбразура, с помощью которой прибор
Крепится к кожуху печи. Конусную полость шлакового прибора набивают огнеупорной масой, в которой прорезают отверстие для выхода шлака из печи. Шлаковая фурма закрывается металлической пробкой с помощью стопорного устройства. В крупных печах выпуск шлака происходит вместе с чугуном из одной летки.
Рис. 20. Схема шлакового прибора:
1 - чугунная водоохлаждаемая амбразура; 2 - чугунный холодильник; 3 - медный холодильник; 4 - медная водоохлаждаемая фурма
Фурмы. В верхней части горна на расстоянии 2700-3500 мм от оси чугунной летки расположены по окружности печи фурмы для подачи в печь горячего воздуха, природного газа, пылевидного или жидкого топлива. Число фурм зависит от размера печи и составляет от 18 до 42. Воздух к печи подается в кольцевой воздухопровод внутренним диаметром до 1650 мм, окружающий доменную печь. От воздухопровода с помощью фурменных приборов дутье поступает в печь. Фурменный прибор (рис. 21) состоит из водоох- лаждаемой литой медной фурмы с внутренним диаметром до 200 мм, которая выступает внутрь печи из кладки на 300 мм. Фурма крепится в холодильниках. Холодильники способствуют охлаждению кладки горна, находящейся в непосредственной близости к очагам горения, позволяют установить фурму в гнезде и устранить выдувание газа из печи. Холодильник делается составным. Воздух к фурме подается по стальному футерованному соплу, которое подсоединено к подвижному колену. При помощи тяг и пружин сопло прижимается к фурме. Для смены сопла или фурмы колено должно быть оттянуто назад при помощи шарнирного сое-^ динения с переходным патрубком. Патрубок соединяется с фурменным рукавом, подсоединенным к кольцевому воздухопроводу. В торце фурменного прибора имеется гляделка для наблюдения за процессом сгорания топлива. При подаче в печь газа или мазута через фурму пропускают трубки, по которым подают топливо. Каждый
Фурменный прибор оборудован устройством для измерения и регулирования расхода воздуха.
Заплечики. Кладку заплечиков выполняют в один кирпич толщиной 345 мм. Кладка охлаждается плитовы – ми ребристыми холодильниками. Как показывает опыт, огнеупорная кладка заплечиков подвергается интенсивному износу и быстро выгорает. На оголенных местах на поверхности холодильников образуется защитный слой
Рис. 21. Устройство фурменного прибора:
1 - медная воздушная фурма; 2, 3 - холодильники; 4 - сопло; 5 - подвижное колено; 6 - переходный патрубок к воздухопроводу
Из шлака и шихтовых материалов (гарнисаж), который и защищает холодильники от действия высокой температуры и жидких продуктов плавки.
Распар. Стенки распара имеют значительную толщину - до 690 мм, они выкладываются из шамотного кирпича и охлаждаются мараторными холодильниками, в торцы которых залиты огнеупорные кирпичи. Кожух шахты опирается на массивное металлическое мараторное кольцо и передает на него давление кладки и конструкций верхней части печи. Кольцо опирается на колонны.
Шахта. Шахту выкладывают шамотным кирпичом. Ее толщин^ ЬГНк!>кНёЙ lIiiCTH зависит от способа охлаж- дения и может изменяться от 690 до 1020 мм, вверху толщина кладки 920 мм. Почти по всей высоте шахты на две трети от распара устанавливают холодильники в шахматном порядке. Между кожухом и кирпичной кладкой или между кирпичами и холодильниками оставляют зазор 50-60 мм, заполненный шамото-асбестовой набивкой для компенсации теплового расширения кладки шахты. Кладка шахты сильно изнашивается под влиянием потока раскаленных газов, несущего мелкие твердые частицы материалов. В нижней части шахты и в распаре шамотный кирпич может разрушаться вследствие era взаимодействия со шлаком. В верхних и средних горизонтах шахты может происходить, разрушение кладки из-за отложения сажистого углерода по реакции 2СО = = С02 + С.
Разрушению кладки способствует также отложение в швах кладки оксида цинка, образующегося вследствие окисления цинка, испаряющегося при плавке. Средняя продолжительность кампании шахты 4-5 лет. Снаружи кладка шихты заключена в прочный кожух. С помощью системы брызгал кожух поливают водой, которая стекает вниз в короба, приваренные внизу шахты.
Колошник. Футеровка колошника выполняется из стальных плит, предохраняющих конструкцию печи от ударов сырых материалов, засылаемых в печь. Между плитами и кожухом печи делают слой кладки из шамотного кирпича. Верхняя часть кожуха печи называется куполом. К нему крепится кольцо засыпного аппарата. Купольная часть изнутри футерована чугунными плитами с залитым в них кирпичом.
Кожух печи. Всю печь охватывает сварной кожух, выполненный из листов толщиной от 20 до 50 мм.
Современная цивилизация неразрывно связана с развитием техники производства, невозможной без совершенствования орудий труда и материалов, используемых для их изготовления.
Среди всех материалов природного происхождения или созданных человеком, самое значимое место занимают черные металлы – сплав железа и углерода с присутствием других элементов.
Сплавы, в составе которых часть углерода составляет 2 – 5%, относятся к чугунам, при наличии углерода менее 2% сплав относится к сталям. Для плавки металлов используется специальная технология доменного производства.
Азбука производства
Доменная плавка – это процесс производства чугуна из железной руды, перерабатываемой в доменных печах или, как их еще называют, домнах.
Основными материалами, необходимыми в процессе такого производства, являются:
- топливо, в виде получаемого из каменного угля кокса;
- железная руда, являющаяся непосредственным сырьем для производства;
- флюс – специальные добавки из известняка, песка, а также других материалов.
В доменные печи железная руда попадает в виде сплавленных между собой кусков мелкой породы – агломератов или окатышей, в виде рудных комков. Исходное сырье загружают в колошник доменной печи послойно, чередуя со слоями кокса и с послойным добавлением флюса.
Примите к сведению: флюс необходим для того, чтобы заставить всплыть пустую породу и различные примеси, которые называются шлаком.
Всплывший на поверхности раскаленного чугуна шлак, сливается до того, как металл застынет. Загружаемый для плавки чугуна материал из железной руды, кокса и флюса, называют шихтой.
Доменная печь, имеющая в профиль сходство с башней с широким основанием, внутри выкладывается огнеупорным материалом – шамотом.
Основными элементами конструкции являются:
- заплечики;
- распар;
- колошник;
- шахта
- горн.
Распар - это самая широкая часть доменной печи. В нем плавится пустая порода руды и флюса, в результате чего из них получается шлак. Для предотвращения воздействия высоких температур на кладку и кожух печи, применяются холодильные установки с циркулирующей водой.
Доменная шахта строится в форме расширяющего внизу конуса – такое устройство домны позволяет шихте свободно опускаться во время процесса плавки. Образование чугуна, который в процессе плавки спускается в горн, происходит в распаре и заплечиках. Для удержания находящейся в распаре и шахте твердой шихты, заплечики имеют форму конуса, с расширением к верху.
Как работает
В домну шихта засыпается через колошник непрерывными порциями.
Для обеспечения непрерывности работы, возле домны устанавливается склад для окатышей (агломерата), флюса и кокса – бункер, предназначенный для составления шихты.
Поставки сырья в бункеры, как и подача шихты к засыпным устройствам на колошник, производится по непрерывной схеме с использованием транспортеров.
Опускаясь под своей массой, шихта попадает в среднюю часть печи, где под воздействием горячих газов, образующихся в результате сгорания кокса, железорудный материал нагревается, а оставшиеся газы выходят через колошник.
В горне, который находится внизу печи, располагаются аппараты для подачи под давлением горячих воздушных потоков – фурмы. В фурмах имеются окошки с термостойкими стеклами, позволяющие производить визуальный контроль процесса.
Обратите внимание: для защиты от воздействия высоких температур устройства охлаждаются водой по имеющимся внутри каналам.
Сгорающий в горне кокс дает необходимую для плавления руды температуру, превышающую +2000 гр.
В процессе горения происходит соединение кокса и кислорода с образованием углекислого газа.
Воздействие высокой температуры на углекислый газ превращает последний в отнимающий у руды оксид углерода и восстанавливает железо. Процесс образования чугуна происходит после прохождения железа сквозь слои раскаленного кокса. В результате такого процесса, железо насыщается углеродом.
После того как чугун в горне накопился, жидкий металл выпускается через находящиеся внизу отверстия – летки. В первую очередь через верхнюю летку выпускается шлак, а затем, через нижнюю летку – чугун. По специальным каналам чугун сливается в размещенные на железнодорожных платформах ковши и транспортируется на дальнейшую обработку.
Литейный чугун, который в дальнейшем будет использован для производства отливок, попадает в разливочный аппарат и, застывая, превращается в бруски – чушки.
Для производства стали используется чугун, который называется переделочным – он составляет до 80% производства.
Переделочный чугун транспортируется в сталелитейный цех с конверторами, мартеновскими или электрическими печами. В современных, огромного размера домнах для поддержания процессов горения используется не только потоки горячего воздуха, но и чистый кислород, применяемый вместе с природным газом.
Такая технология позволяет расходовать меньшее количество кокса, но является технологически более сложной. Поэтому для контроля процесса производства, выбора оптимальных режимов плавки используются компьютеры, способные вести одновременный анализ работы всех систем.
Смотрите познавательное видео, в котором описываются принцип работы и нюансы функционирования доменной печи:
Производительность определяется размерами печи. Максимальная мощность наблюдается при объеме печей шахтного типа 2-5 тыс. куб. м. Их диаметр составляет 11-16 м, высота – 32-37 м.
Схема домны
Шахтная печь состоит из следующих элементов:
колошника;
шахты;
распара;
заплечиков;
горна;
лещади.
Колошник
– один из элементов рабочего пространства, на котором предусматривается определенный уровень материалов, распределяющихся по сечению шахты.
Шахта
– цилиндрическая часть домны, где поддерживается температура, достаточная для плавления шихты. В этой же части печи происходит восстановление железа.
Распар – наиболее широкий участок конструкции, предназначенный для основных процессов плавления. Ниже находятся заплечики, способствующие перегреву и перемещению расплава и шлака на следующий участок конструкции.
Горн размещается над лещадью, которая представляет собой кладку, выполненную с применением шамотного кирпича. Горн является той частью печи, где собираются и . Между заплечиками и горном находятся фурмы для подачи горячего (воздуха, обогащенного кислородом) и природного газа.
Принцип работы
Шихта поддается с помощью скипового подъемника и попадает в приемную воронку. Состав шихты представлен известняком, коксом, офлюсованным агломератом и рудой. Возможно добавление окатышей.
Конусы колошника (большой и малый) работают поочередно, передавая смесь материалов в шахту. В процессе работы домны происходит постепенное поступление шихты. Нагрев осуществляется в результате горения кокса, сопровождающегося выделением тепла.
Температура горнового газа находится в пределах от 1900 до 2100 градусов Цельсия. В его состав входят N 2 , H 2 и CO. При движении в слое он не только способствует ее нагреву, но и запускает процессы восстановления железа. Высокая температура газа достигается за счет высокой температуры воздуха, находящегося в воздухонагревателях (1000-2000 градусов).
Газ температурой 250 - 300 градусов, поступающий из печи, колошниковый, после удаления пыли – доменный. Низшая теплота сгорания доменного газа соответствует 3,5 - 5,5 МДж/м 3 . Состав бывает различным, определяется в результате подачи природного газа и обогащения дутья кислородом, представлен такими веществами:
N 2 – 43-59 %;
CO – 24-32 %;
CO 2 – 10-18 %;
H 2 – 1-13 %;
CH 4 – 0,2-0,6 %.
В основном газ необходим для придания определенной температуры насадкам доменных воздухонагревателей. В сочетании с природным или коксовым газом его применяют для различных печей, в т. ч. термических и нагревательных.
Поступившее в нижнюю часть домны железо подвергается плавлению и накапливается в горне в виде чугуна. Жидкотекучий шлак образуется из окислов , железа, соединенных с , и остается на поверхности чугуна, т. к. имеет меньшую плотность.
Периодически чугун и шлак выходят через соответствующие летки – чугунную, шлаковую. В случаях, когда количество шлака незначительное, используется только чугунная летка. Отделение шлака происходит на разливочной площадке. Температура чугуна в жидком виде находится в пределах от 1420 до 1520 градусов.
Высокая производительность доменной печи достигается за счет наличия мощных воздухонагревателей, являющихся теплообменниками регенеративного типа. Нередко воздухонагреватели домны называют кауперами в честь их создателя.
Каупер – вертикально расположенный кожух в форме цилиндра, созданный из листовой и насадки из кирпича. Камера горения воздухонагревателя, а именно – ее нижняя часть, состоит из горелки и воздухопровода горячего дутья. В поднасадочном пространстве применены клапаны, что позволило обеспечить соединение с отводом к дымовому борову и воздухопроводом холодного дутья.
Современный вариант шахтной печи изготавливается с четырьмя кауперами, работающими попеременно: нагрев насадки одного из двух кауперов происходит за счет поступления нагретых до высокой температуры дымовых газов, через третий каупер проникает нагреваемый воздух. Четвертый каупер является резервным.
Продолжительность дутья составляет 50-90 минут, затем охлажденный каупер нагревается, дутье осуществляется в следующем наиболее горячем каупере. При разогреве работает горелка, дымовые газы без препятствий проникают в дымовой боров через открытый клапан. В это время клапаны, находящиеся на воздухопроводах горячего и холодного дутья, закрыты.
В результате сжигания топлива образуются продукты горения, которые перемещаются вверх и поступают из камеры горения в подкупольное пространство, затем опускаются и нагревают насадку. Только после этого продукты топлива, имеющие температуру 250-400 градусов, поступают в дымовую трубу через дымовой клапан.
Во время дутья происходит обратный процесс: дымовой клапан закрыт, горелка не работает, при этом клапаны, установленные на воздухопроводах горячего, холодного дутья, открыты. Холодное дутье в поднасадочное пространство подается под давлением 3,5-4 ат, затем перемещается через разогретую насадку и в нагретом виде через камеру горения проходит в воздухопровод горячего дутья, откуда подается в печь.
В определенных условиях могут происходить увлажнение дутья и обогащение азотом или кислородом. При использовании азота удается экономно расходовать и контролировать процесс плавления в доменной печи. Экономия кокса возможна и в результате обогащения дутья кислородом до 35-40 % при сочетании с природным газом. Путем повышения влажности до 3-5 % удается получить более высокую температуру нагрева дутья в каупере. Такие результаты достигаются благодаря интенсификации лучистого теплообмена в насадке.
Высота кауперов составляет около 30-35 м, диаметр – не более 9 м. Верхнюю и нижнюю части насадки выполняют из динасового или высокоглиноземистого кирпича и огнеупорного соответственно. Из насадочного кирпича, имеющего толщину 40 мм, создают ячейки 4545, 13045, 110110 мм. В доменных печах применяются и другие насадки, а именно – насадки, состоящие из блоков с шестью гранями, с горизонтальными проходами и круглыми ячейками. Также используются насадки, основа которых – высокоглиноземистые шарики.
На каждый кубический метр объема кирпичной насадки предусмотрена примерная поверхность нагрева 22-25 кв. м. Объем домны в 1-2 раза больше объема насадки каупера. Например, при объеме печи 3000 куб. м объем каупера составит около 2000 куб. м (3000/1,5).
Самыми распространенными являются кауперы, оснащенные встроенной камерой горения. Среди их основных недостатков – чрезмерный нагрев свода, деформация камеры горения в результате долгой работы печи. Горелка каупера бывает выносной, также камера горения может располагаться под куполом. При наличии выносной горелки обеспечиваются высокая стойкость и удобство, но цена таких устройств наиболее высокая. Кауперы, оснащенные подкупольной камерой горения, самые дешевые, но процесс эксплуатации более сложный, т. к. горелка и клапаны расположены достаточно высоко.
В процессе дутья температура, до которой нагревается воздух (1350-1400 градусов), постепенно уменьшается и находится в пределах от 1050 до 1200 градусов. При использовании домны, работающей стационарно, таких перепадов избегают путем регулирования температуры. Нужные показатели появляются в результате добавления холодного воздуха, поступившего из воздухопровода холодного дутья. Снижается температура дутья до 1000-2000 градусов, а вместе с ней и содержание холодного воздуха в смеси.
Ориентировочный материальный баланс получения чугуна в домне
Рассмотрим тепловой баланс выплавки 1 кг чугуна. При составлении балансов учитываются , агломерат, чугун, шлак и доменный газ.
Окатыши: оксид железа (III) – 81 %, диоксид кремния – 7 %, оксид кальция – 5 %, оксид железа (II) – 4 %, оксид и оксид – 1 %, оксид марганца – 0,3 %, оксид фосфора – около 0,09 %, сера – около 0,03 %.
Агломерат: оксид железа (III) – 63 %, оксид железа (II) – 16 %, оксид кальция – 10 %, диоксид кремния – 7 %, оксид алюминия – 2 %, оксид магния и оксид марганца – 1 %, оксид фосфора – около 0,25 %, сера – около 0,01 %.
Чугун: железо – 94,2 %, углерод – 4,5 %, марганец – 0,7 %, кремний – 0,6 %, сера – около 0,03 %.
Шлак: оксид кальция – 43 %, диоксид кремния – 36 %, оксид алюминия – 10 %, оксид магния – 7 %, оксид марганца – 2 %, оксид железа (II) и сера – 1 %.
Доменный газ: азот – 44 %, – 25,2 %, углекислый газ – 18 %, водород – 12,5 %, метан – 0,3 %.
Произведем анализ расхода топлива в результате применения офлюсованного агломерата. Затраты топлива в определяются, исходя из расхода природного газа и кокса (510-560 кг у.т./т сплава), в сумме с расходом газа, направленного на отопление воздухонагревателя (90-100 кг у.т./т сплава), за исключением выхода доменного газа (170-210 кг у.т./т сплава). В результате общий расход выглядит следующим образом: 535 + 95 - 190 = 440 (кг у. т./т сплава).
Учитывая то, что на производство кокса и агломерата уже ушло определенное количество топлива (около 430-490 кг на 1 т сплава и 1200-1800 кг на 1 т сплава соответственно), общий расход первичного топлива, необходимого для получения тонны сплава, составляет: 440 + 40 + 170 = 650 (кг у.т./т), из которых 170 и 40 кг у.т./т, пересчитанные на тонну сплава, затрачиваются на производство и кокса.
Производительность домны оценивают по коэффициенту использования полезного объема (КИПО). Показатель рассчитывают как отношение полезного объема конструкции к выплавке чугуна в течение 24 часов. Для современных печей нормой является показатель 0,43-0,75 куб. м сут./т. Чем ниже КИПО, тем эффективнее используется печь.
Логичнее рассматривать показатель как отношение производительности к единице объема. Удобнее применять показатель удельной производительности домны (Пу = 1/ КИПО), значение которого составляет 1,3-2,3 т (куб. м/сут.).
Экономия топлива возможна при соблюдении таких рекомендаций:
Повышение давления газа на колошнике до 1,5-2 атм (за счет уменьшения объема газов удается сократить удаление колошниковой пыли или увеличить расход дутья);
применение пылеугольного топлива в горне для экономии около 0,8 кг кокса на килограмм пылеугольного топлива;
повышение температуры, до которой нагревается воздух в кауперах, для уменьшения расхода кокса;
применение теплоты отходящих газов кауперов с целью повысить температуру воздуха и доменного газа до их подачи в камеру горения;
подача нагретых восстановительных газов таким же образом, как в печах металлизации (удается снизить расход кокса, возможна экономия до 20 % топлива);
применение физической теплоты огненно-жидких шлаков (решение данной проблемы является перспективным, но пока что не реализовано по причине периодического выхода шлаков).
Доменная печь, или, как её часто называют, домна, предназначена для выплавки железа из железной руды. Происходит это в результате химических реакций, протекающих при высокой температуре. На заключительной стадии процесса выплавленное железо насыщается углеродом и превращается в чугун (см. Железо, сталь, чугун).
Доменная печь.
В домне расплавляют, как правило, не железную руду, а агломерат (спекшуюся в куски мелкую руду) или окатыши (комки сферической формы, получаемые из мелкой руды или тонкоизмельченного концентрата). Их загружают в печь послойно, перемежая коксом. Так же послойно в домну добавляют флюсы - известь, песок и некоторые другие вещества. Для чего они нужны?
Вместе с агломератом и окатышами в домну Попадает порода, не содержащая железа. Металлурги называют её пустой породой. Её надо удалить, чтобы она не попала в чугун при его затвердевании. Флюсы заставляют пустую породу и некоторые другие ненужные вещества (все это называют шлаком) всплывать на поверхность жидкого металла, откуда шлак уже нетрудно слить в специальный ковш. Итак, агломерат (или окатыши), кокс, флюсы входят в смесь материалов, которая загружается в домну и называется шихтой.
Домна напоминает большую круглую башню и состоит из трех основных частей: верхняя часть - колошник, средняя - шахта и нижняя - горн. Внутри доменная печь выложена (футерована) огнеупорной кладкой. Чтобы предотвратить разгар кладки и защитить кожух печи от высоких температур, используют холодильники, в которых циркулирует вода.
Через колошник порциями, по нескольку тонн в каждой, в домну загружается шихта. Загрузка идет непрерывно. Для этого возле доменной печи устраивают бункер - склад, куда доставляют агломерат (или окатыши), кокс и флюсы. В бункере из них при помощи автоматизированных вагонов-весов составляют шихту. В бункеры больших современных домен сырье подается непрерывно - транспортерами. Также транспортерами в современных домнах подается шихта из бункера на колошник. В старых домнах для этого применяются вагончики-скипы, которые курсируют по наклонным рельсам.
Под действием собственного веса шихта опускается, проходя через всю домну. В средней части печи - шахте - её омывают идущие снизу вверх газы - продукты горения кокса. Они нагревают шихту, а затем уходят из домны через колошник. Но самое главное происходит в нижней части домны - горне.
Здесь в кожухе домны имеются фурмы - специальные устройства для подачи в печь сжатого горячего воздуха. В фурмах устроены окошки, защищенные стеклами, через которые доменщики могут заглянуть внутрь печи и увидеть, как идет процесс. Чтобы фурмы не сгорели, их охлаждают водой, протекающей по каналам внутри фурм.
Горячий воздух нужен для того, чтобы еще сильнее подогреть шихту перед расплавлением. Это позволяет снизить расход дорогостоящего кокса и повышает производительность домны. Кроме того, для еще большего снижения расхода кокса в домну вводят в качестве источника тепла природный газ или мазут. Воздух перед подачей в фурмы нагревают в высоких башнях, заполненных внутри кирпичом, - воздухонагревателях.
В горне домны сгорает кокс (а также природный газ или мазут), развивая очень высокую температуру - свыше 2000 °C, под действием которой руда полностью расплавляется. Сгорая, кокс соединяется с кислородом воздуха, и образуется углекислый газ. Под влиянием высокой температуры углекислый газ превращается в оксид углерода, который отнимает у железной руды кислород, восстанавливая железо. Стекая вниз через слой раскаленного кокса, железо насыщается углеродом и превращается в чугун. Жидкий чугун скапливается на дне горна, а на его поверхности собирается слой более легкого шлака.
Когда в горне накопится достаточное количество чугуна, его выпускают через отверстия в нижней части горна - летки. Сначала выпускают шлак через верхнюю летку, потом чугун через нижнюю. Далее чугун попадает в канавы, откуда его сливают в большие чугуновозные ковши, стоящие на железнодорожных платформах, и отправляют на дальнейшую обработку.
Если чугун предназначен для изготовления отливок - литейный чугун, - он попадает в разливочную машину, где застывает в виде брусков - чушек. Если же чугун предназначен для передела в сталь (передельный чугун), его транспортируют в сталеплавильный цех. Там он попадает в мартеновские печи, конвертеры или электропечи (см. Электрометаллургия). Из всего количества выпускаемого чугуна примерно 80% приходится на долю передельного.
Первая домна Магнитогорского металлургического комбината, вступившая в строй в 1932 г., имела объем 900 м 3 . В 1986 г. на Череповецком металлургическом заводе начала работать домна «Северянка» объемом 5500 м 3 , одна из самых больших в мире.
Раньше доменные печи выпускали чугун каждые 3–4 ч. С увеличением их объема выпуск чугуна ускорился - каждые 2 ч. Большие домны - объемом 3000 м 3 и более - выпускают чугун практически непрерывно.
В современных гигантских домнах для поддержания горения применяют не только нагретый воздух, но и природный газ вместе с чистым кислородом. Это повышает производительность агрегата, снижает расход кокса, но в то же время затрудняет управление технологическим процессом. Поэтому сейчас в доменных цехах все чаще появляются электронные вычислительные машины. Они анализируют показания многочисленных приборов, контролируют ход процесса, выбирают наилучшие режимы плавки.
13. Доменная печь, ее устройство и работа.
Доменная печь является шахтной печью, которую выкладывают в стальном корпусе шамотным кирпичом. У доменной печи выделяют (рис. 7, а) колошник, шахту, распар, заплечики и горн. Черезколошниковый затвор в доменную печь загружают шихту.Шахта имеет форму усеченного конуса, расширяющегося книзу, что способствует свободному опусканию шихты по мере плавления. На уровнераспара изаплечиков образуется губчатое железо, которое затем науглероживается, плавится и стекает в горн. Заплечики от распара суживаются к горну, поэтому твердая шихта удерживается в распаре и шахте.
В горне на лещади 6 накапливается жидкий чугун. Его плотность 6,9 г/см 3 , а плотность шлака около 2,5 г/см 3 , поэтому над чугуном находится слой шлака. Накопившийся шлак периодически выпускают черезлетку 5,Рис. 7
а чугун - через летку 1. Окислительное дутье для горения топлива подается через фурмы4 под давлением до 500 кПа; оно предварительно нагревается в регенеративных печах - воздухонагревателях. Эти же фурмы используют для подачи в печь природного газа и других топливных добавок (мазута, пылевидного топлива). На колошнике находитсязасыпной аппарат 3 игазоотвод 2 для доменного (колошникового) газа. Главной характеристикой печи является ее полезный объем - внутренний объем, исчисленный по полезной высоте печи.
Доменный процесс. В печи непрерывно движутся: сверху вниз - поток шихты, снизу вверх - поток газов, образующихся при горении топлива и реакциях с составляющими шихты. Сущность доменной плавки состоит в восстановлении железа из оксидов в руде, науглероживании железа и ошлаковании пустой породы и золы топлива.
Восстановление оксидов и образование чугуна начинается с восстановления оксидов железа монооксидом углерода в средней части шахты. При опускании шихты к распару эти реакции развиваются и протекают быстрее:
3Fе 2 О 3 + СО = 2Fе 3 О 4 + СО 2 +dН;
Fе 3 О 4 + СО = ЗFеО + СО 2 -dН;
FеО + СО =Fе + СO 2 +dН.
Науглероживание железа начинается в шахте вслед за его восстановлением с образованием карбида железа по реакции:
3Fе + 2СО =Fе 3 С + СО 2 .
14. Получение стали в кислородных конвертерах.
В производстве стали широко используют кислородно-конвертерные процесс ы. Стационарный конвертер (рис. 8) имеет два бандажа 4, каждый из которых опирается на два ролика 1. Горловина конвертера имеет симметричную форму. Внутри стального кожуха конвертеры выкладываются смолодоломитовым кирпичом. Летка 3 предназначена для слива готовой стали.
Вместимость кислородных конвертеров
от 50 до 400 т. Сущность кислородно-конвертерного
процесса заключается в том, что
загруженную в конвертер шихту продувают
сверху струей кислорода под давлением
до 1,5 МПа. Большое давление кислорода
обеспечивает хорошее перемешивание
металла. В начале продувки окисляются
кремний, марганец и другие элементы,
которые переходят в шлак. После первого
периода продувки кислородом
(длится 16 мин), фурму поднимают,
наклоняют конвертер, сливают шлак и
берут пробу металла. В конвертер
добавляют известь, ставят его вновь в
вертикальное положение, вводят
фурму и начинают второй период продувы
кислородом. Во второй период продувки
продолжаются реакции окисления
примесей, выгорает углерод, идут
реакции шлакообразования и другие
физико-химические процессы. В конце
второго периода продувки в конвертер
вводят часть раскислителей. После
удаленияРис. 8
фурмы конвертер наклоняют, берут контрольную пробу стали и выпускают сталь в разливочный ковш, где завершается процесс ее раскисления ферромарганцем, ферросилицием или комплексными раскислителями.
Общая продолжительность составляет 40...60 мин, а продолжительность продувки кислородом - 18...30 мин. Преимущества: хорошее качество, высокая производительность и меньшая себестоимость. Недостаток: большой угар металла (6...9%).