Химические методы обработки металла. Способ химического фрезерования деталей Установки для химического фрезерования
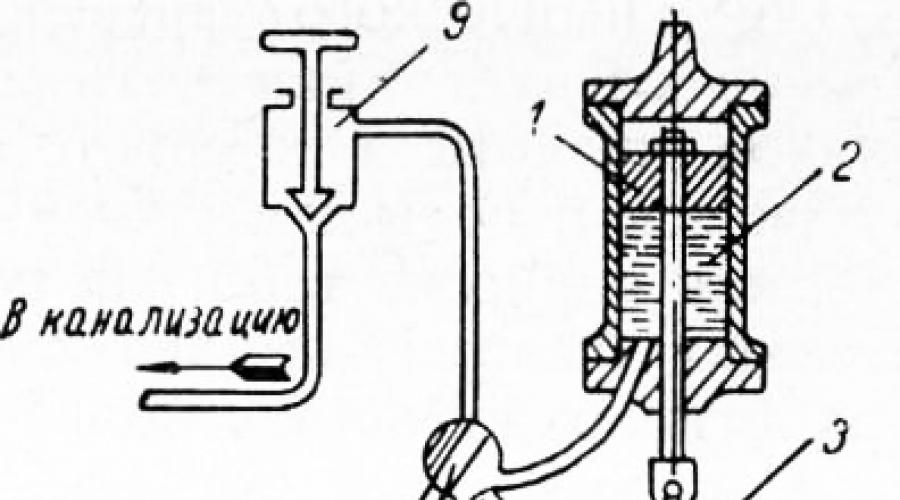
Читайте также
На сайте изложены основы технологии гальванических покрытий. Подробно рассмотрены процессы подготовки и нанесения электрохимических и химических покрытий, а также методы контроля качества покрытий. Описано основное и вспомогательное оборудование гальванического цеха. Приведены сведения по механизации и автоматизации гальванического производства, а также санитарии и технике безопасности.
Сайт может быть использован при профессиональном обучении рабочих на производстве.
Применение защитных, защитно-декоративных и специальных покрытий позволяет решать многие задачи, среди которых важное место занимает защита металлов от коррозии. Коррозия металлов, т. е. разрушение их вследствие электрохимического или химического воздействия среды, причиняет-народному хозяйству огромный ущерб. Ежегодно вследствие коррозии выходит из употребления до 10—15 % годового выпуска металла в виде ценных деталей и конструкций, сложных приборов и машин. В отдельных случаях коррозия приводит к авариям.
Гальванические покрытия являются одним из эффективных методов защиты от коррозии, они также широко применяются для придания поверхности деталей ряда ценных специальных свойств: повышенной твердости и износостойкости, высокой отражательной способности, улучшенных антифрикционных свойств, поверхностной электропроводности, облегчения паяемости и, наконец, просто для улучшения внешнего вида изделий.
Русские ученые являются создателями многих важнейших способов электрохимической обработки металлов. Так, создание гальванопластики — заслуга академика Б. С. Якоби (1837 г.). Важнейшие работы в области гальванотехники принадлежат русским ученым Э. X. Ленцу и И. М. Федоровскому. Развитие гальванотехники после Октябрьской революции неразрывно связано с именами ученых профессоров Н. Т. Кудрявцева, В. И. Лайнера, Н. П. Федотьева и многих других.
Проделана большая работа по стандартизации и нормализации процессов нанесения покрытий. Резко увеличивающийся объем работы, механизация и автоматизация гальванических цехов потребовали четкого регламентирования процессов, тщательного отбораэлектролитов для нанесения покрытия, выбора наиболее эффективных способов подготовки поверхности деталей перед осаждением гальванических покрытий и заключительных операций, а также надежных методов контроля качества изделий. В этих условиях резко возрастает роль квалифицированного рабочего-гальваника.
Основной задачей данного сайта является помощь учащимся технических училищ в овладении профессией рабочего-гальваника, знающего современные технологические процессы, применяемые в передовых гальванических цехах.
Электролитическое хромирование является эффективным способом повышения износостойкости трущихся деталей, защиты их от коррозии, а также способом защитно-декоративной отделки. Значительную экономию дает хромирование при восстановлений изношенных деталей. Процесс хромирования широко применяется в народном хозяйстве. Над его совершенствованием работает ряд научно-исследовательских организаций, институтов, вузов и машиностроительных предприятий. Появляются более эффективные электролиты и режимы хромирования, разрабатываются методы повышения механических свойств хромированных деталей, в результате чего расширяется область применения хромирования. Знание основ срвременной технологии хромирования способствует выполнению указаний нормативно-технической документации и творческому участию широких кругов практических работников в дальнейшем развитии хромирования.
На сайте развиты вопросы влияния хромирования на прочность деталей, расширено использование эффективных электролитов и технологических процессов, введен новый раздел по методам повышения экономичности хромирования. Основные разделы переработаны с учетом nporpecсивных достижений технологии хромирования. Приведенные технологические указания и конструкции подвесных приспособлений являются примерными, ориентирующими читателя в вопросах выбора условий хромирования и в принципах конструирования подвесных приспособлений.
Непрерывное развитие всех отраслей машиностроения и приборостроения обусловило значительное расширение области применения электролитических и химических покрытий.
Путем химического осаждения металлов, в сочетании с гальваническим созданы металлические покрытия на самых разнообразных диэлектриках: пластмассах, керамике, ферритах, ситалле и других материалах. Изготовление деталей из этих материалов с металлизированной поверхностью обеспечило внедрение новых конструктивно-технических решений, улучшение качества изделий и удешевление производства аппаратуры, машин, предметов широкого потребления.
Детали из пластмасс с металлическими покрытиями широко используются в автомобилестроении, радиотехнической промышленности и других отраслях народного хозяйства. Особенно большое значение процессы металлизации полимерных материалов приобрели в производстве печатных плат, являющихся основой современных электронных приборов и радиотехнических изделий.
В брошюре даны необходимые сведения о процессах химико-электролитической металлизации диэлектриков, приведены основные закономерности химического осаждения металлов. Указаны особенности электролитических покрытий при металлизации пластмасс. Уделено значительное внимание технологии производства печатных плат, а также даны методы анализа растворов, применяемых в процессах металлизации, и способы их приготовления и корректирования.
В доступной и увлекательной форме сайт знакомит с физической природой в особенностями ионизирующей радиации и радиоактивности, с влиянием различных доз радиации на живые организмы, способами защиты и предупреждения лучевой опасности, возможностями использования радиоактивных изотопов для распознавания и лечения заболеваний человека.
Состав для очистки поверхности из бетона, кирпича и гипса методом химического фрезерования, удаление цементной пленки, активация адгезии, подготовка поверхности под гидроизоляцию, очистка фасадов от высолов и цементного налета минеральных оснований: бетона, кирпича, керамики, природного и искусственного камня, гипса, шифера, а также для борьбы с грибковыми и плесневыми образованиями. Состав также используется для очистки металла, керамической, чугунной, эмалированной и акриловой сантехники от налета ржавчины.
Применение и свойства
Адгезия - Материал предназначен для очистки цементной пленки, устранения "холодного шва", создания монолита и повышения в 1,5-3 раза адгезии слоев монолитного бетона, цементных, гипсовых и магнезиальных стяжек пола.
Подготовка основания - под нанесение гидроизоляционных материалов проникающего (пенетрирующего) действия, цементных, эпоксидных, полиуретановых и акрилатных наливных полов и шовных герметиков. Исключает необходимость использования грунтовок.
Удаление плесневых и грибковых образований с бетонных, гипсовых и кирпичных поверхностей. Работает в комплексе с биоцидными и антисептическими материалами "АрмМикс".
Устранение высолов с бетона и кирпича - очищает поверхность кирпича и бетона от солей, работает в комплексе с гидрофобизатором .
Удаление налета ржавчины с металла, с акриловой, эмалированной, чугунной и керамической сантехники
При проведении бетонных работ, часто возникают ситуации, когда нет возможности провести работы по заливке всего объекта сразу, без перерывов. В результате этого, при последующей заливке, в месте контакта старого и нового слоев бетонирования возникает холодный шов. Холодный шов, как правило, ведет к потере прочности соединения и нарушения водонепроницаемости (что проявляется в появлении протечек).
Другая проблема, с которой часто сталкиваются наши клиенты - это проведение отделочных работ по бетонной поверхности. Через 8 часов после схватывания бетона, на его поверхности образуется цементная пленка, которая препятствует адгезии, то есть уменьшает сцепление бетона и отделочного материала. Если ее не удалить, то соединение будет непрочным и велика вероятность отслоения и разрушения штукатурки или пола (стяжки). Для удаления цементной пленки, как правило, используют механические способы удаления (механическое фрезерование бетона) или применяют кислоты (обычно соляную). Оба этих способа имеют свои недостатки: первый связан с применением дорогостоящей техники (песко- или дробеструйных машин) и ослаблению конструкции, второй - с вредным воздействием кислот и растворителей на конструкцию и рабочих.
Мы предлагаем решение проблемы холодного шва и удаления цементной пленки путем химического фрезерования поверхности при помощи состава "АрмМикс Очиститель". Это готовый к применению состав на водной основе, изготовлен из сложных полифункциональных кислот. Не имеет запаха, не оказывают вредного воздействия на человека и окружающую среду. Разрешен к применению и эксплуатации Минздравом РФ для внутренних и наружных работ при строительстве и ремонте жилых, общественных и промышленных зданий и сооружений. Не содержит соляной, уксусной, лимонной, ортофосфорной кислот и растворителей разрушающих бетон.
Достоинства и качества
Растворение цементной пленки без разрушения цементного камня. Открытие пор и адгезионная активация строительных оснований. Удаление высолов с фасадов (кирпичные, бетонные, каменные основания) зданий. Удаление ржавого налета с поверхностей.
Состав - кислотный очиститель розового цвета с рН=1-2 растворяет цементную пленку, открывает поры и увеличивает глубину проникновения покрытий в бетон, увеличивает прочность сцепления с основанием.
- Исключение ручной механической очистки и машинного фрезерования, песко-, дробе-, гидро- и гидропескоструйной обработки, применения для насечки поверхности бетона алмазного инструмента и перфораторов.
- Устранение необходимости применения штукатурной сетки.
- Снижение трудоемкости и стоимости работ.
Способ применения
- Работы производить при температуре окружающего воздуха от +5°С до +30°С.
- Поверхность основания механическим способом очистить от осыпающихся частиц, загрязнений и обеспылить.
- Кистью, валиком или распылителем в один или несколько проходов нанести на основание состав "АрмМикс Очиститель" до растворения цементной пленки и высолов и открытия пор и микротрещин.
В процессе очистки происходит химическая реакция с выделением углекислого газа. - Смыть остатки реакции водой.
Сушка на воздухе
- перед нанесением минеральных стяжек, штукатурок, плиточных клеев, герметиков и наливных полов - 1 ч;
- перед нанесением полимерных наливных полов и герметиков - до необходимой остаточной влажности бетона.
Дополнительная информация о товаре
Требования безопасности:
Состав пожаробезопасен. Работы производить, соблюдая требования безопасности при работе с кислотами с рН=1-2. Работать в спецодежде, защитных очках и резиновых перчатках. При попадании состава в глаза, на кожу или слизистые оболочки промыть их водой. Беречь от детей.
Ориентировочный расход
0,1 - 0,3 л/м 2 .
Упаковка
п/э канистры 1л, 5л и 10л
Транспортирование и хранение
Упакованный состав транспортируется автомобильным, железнодорожным и другими видами транспорта в соответствии с правилами перевозок и крепления грузов действующими на данном виде транспорта. Упакованный состав хранится в сухих помещениях при температуре не ниже +5°С в условиях, обеспечивающих сохранность упаковки и защиту от увлажнения.
Гарантии изготовителя
Гарантийный срок хранения состава - 1 год со дня изготовления. Допускается наличие осадка. Не замораживать. Оттенки цвета состава не регламентируются.
Стоимость
К атегория:
Химическая обработка
Химическое фрезерование, штамповка, полирование
При химическом фрезеровании съем металла осуществляется погружением заготовки в травильный раствор. Участки, не подлежащие травлению, изолируют соответствующими защитными покрытиями. Неизолированными остаются контуры, по которым происходит растворение металла. Этот процесс позволяет изготовлять детали повышенной твердости миниатюрных и весьма крупных размеров и тонкостенных, механическая обработка которых является весьма трудоемкой.
Химическое фрезерование применяют для контролируемого удаления материала с получением деталей заданных размеров преимущественно с фасонными поверхностями, уменьшения толщины ребер до величин, которые механической обработкой, штамповкой и литьем получить невозможно: для обработки гофрированных стенок, образования уступов под соединение нескольких деталей в одну, для получения отверстий различных форм, глубоких и узких пазов, обработки тонких полосок и крутых скосов и для получения деталей с переменным сечением. Кроме того, химическую обработку применяют для удаления нарушенного слоя, остающегося на поверхности после механической обработки, и для получения заданного рельефа на поверхности (химическое клеймение).
Этим способом можно обрабатывать все металлы и сплавы, в том числе химически стойкие, жаропрочные, а также на алюминиевой и медной основе. Однако в зависимости от состава обрабатываемого материала изменяются и состав раствора, и режимы обработки.
Обработка сварных деталей возможна, если сварка произведена без каких-либо дефектов, в противном случае химическое фрезерование сварного шва может привести к образованию раковин или местному растравливанию.
Химическое фрезерование позволяет выдерживать допуски от ± 0,015 до ±0,5 мм. Шероховатость химически фрезерованной поверхности находится в пределах 4-5-го классов. Производительность в среднем составляет 0,025-0,1 мм/мин.
Следует иметь в виду, что колебания толщины заготовки и волнистость ее поверхности воспроизводятся после химического фрезерования. Поэтому, если допуски готовых деталей жесткие, необходимо предварительно устранять разнотолщинность заготовок механической обработкой.
Оборудование. Травильные растворы для обработки весьма агрессивны, поэтому емкости для них должны быть изготовлены из жесткого поливинилхло-рида (винипласта) или фторопласта-4. Крупногабаритные ванны целесообразно изготовлять стальными с облицовкой химически стойкой силикатной эмалью марки ЛК-1 или 105 или фторопластом ЗМ.
Толщина облицовки эмалью должна быть в пределах 0,8-1,2 мм, а фторопластом ЗМ -400-500 мк. Технология покрытий эмалью и фторопластом освоена ленинградскими предприятиями, в частности Ленхим-пищекомбинат успешно облицовывает большие емкости химически стойкой эмалью. Травильные растворы нагревают до 60-70° С, используя пароводяную рубашку или трубчатые нагреватели с погружением их в рабочий раствор. Нагреватели также должны быть защищены химически стойким покрытием.
Пары, возникающие в результате растворения металла, должны надежно отсасываться через гидрофильтры. Вытяжная система и фильтры также должны изготовляться из химически стойких материалов. Фланцевые соединения необходимо снабдить прокладками из химически стойкой резины или комбинированными прокладками из фторопласта и резины.
Приспособление для регулирования скорости погружения деталей в ванну
Заготовку, подвергаемую химической обработке, погружают в ванну с раствором с определенной скоростью. Величина скорости погружения при этом не всегда должна быть одинаковой, ее изменяют в зависимости от заданного режима.
Для обеспечения необходимой скорости погружения заготовок в раствор, а также для осуществления плавного и бесступенчатого изменения скорости рационализаторами В. К- Самотесовым и А. П. Поповым внедрено приспособление.
Конструкция его несложна и позволяет регулировать скорость погружения заготовок в раствор в пределах от 0 до 10 м/мин. Приспособление состоит из цилиндра с поршнем, центробежного насоса, двухходового крана и дросселя. Цилиндр крепится неподвижно на корпусе ванны или укрепляется на специальной стойке, подающейся к ванне.
Работа приспособления при погружении заготовки состоит из следующих операций. Рукоятка двухходового крана из положения I переводится в положение II. В этом положении подача воды в цилиндр прекращается. В то же время из нижней полости цилиндра вода уходит через трубопроводы и дроссель. Под действием груза и обрабатываемых заготовок, закрепленных на приспособлении, поршень начнет медленно опускаться. Скорость опускания регулируется дросселем. При подъеме деталей из ванны рукоятка двухходового крана из положения II переводится в положение, и тогда в нижнюю полость цилиндра под поршень от центробежного насоса через двухходовой кран подается вода под давлением 0,6-0,8 атм, что обеспечу вает быстрый подъем деталей из ванны.
Растворы. Для химического фрезерования стальных заготовок из углеродистых сталей удовлетворительные результаты получены в результате применения растворов сернокислой меди, персульфатов калия, натрия и аммония, хлорного железа и хлористого натрия.
Для обработки меди и латуни применимы 10%-ные растворы хлорноватокислого калия, смешанного в равных объемах с 4%-ным раствором соляной кислоты.
Для химического фрезерования стали марки Х18Н9Т необходима смесь азотной и соляной кислот.
Рис. 1. Приспособление для погружения заготовок при химической обработке.
Для химического фрезерования алюминия и его сплавов следует применять смесь сернокислой меди, соляной кислоты и хлористого натрия или растворы каустической соды и соляной кислоты.
Исследование процесса показывает, что для каждого металла и сплава существует оптимальная концентрация. Так, для алюминия оптимальной концентрацией каустической соды является 300 г/л, для силумина - 400 г/л, для дюралюминия - 500 г/л. Дальнейшее повышение концентрации раствора снижает производительность процесса.
Оптимальная концентрация соляной кислоты составляет 30%, а температура 40 °С. С повышением температуры производительность процесса возрастает. Однако следует иметь в виду, что с повышением температуры увеличивается активность выделения вредных газов, особенно хлора. Поэтому практически проводить обработку в соляной кислоте при температуре выше 40 °С нельзя.
Технологический процесс химического фрезерования может несколько видоизменяться в зависимости от конкретных условий. Между тем основные операции и их последовательность остаются неизменными.
Первой операцией в технологическом процессе химического фрезерования должна быть контрольная. Заготовки после механической обработки необходимо тщательно контролировать, чтобы убедиться в отсутствии дефектов материала и механической обработки. Устанавливается разнотолщинность заготовок из листа. После измерения толщин назначают режимы обработки. Затем тщательно обезжиривают заготовки органическим растворителем. Если имеются места, покрытые слоем окалины, необходимо ее предварительно удалить. После очистки быстро наносят защитное покрытие. Материалы для защитных покрытий выбирают в зависимости от требуемой глубины обработки и агрессивности применяемых растворов.
В случае применения сильных кислот и глубокой обработки в качестве защитного покрытия пригоден фторопласт ЗМ. Наносят фторопластовое покрытие обливом, окунанием или с помощью распылителя. Для повышения вязкости суспензии до 14 сек. по вискозиметру ВЗ-4 в нее вводят пластификатор. Это позволяет нанести за один раз слой толщиной 30 мк, что вполне достаточно для получения многих деталей. В исключительных случаях для очень надежной защиты требуется 6-8 слоев (0,18-0,24 мм). После нанесения каждого слоя покрытие подвергают сушке при 120 °С и термической обработке при 260 °С. Продолжительность термической обработки составляет 45 мин.
При неглубоких съемах металла можно применять покрытие на основе резинового клея 88 или нитроклея АК-20. После нанесения защитного покрытия заготовки подготовляют к обработке. Для этого сначала над заготовкой с нанесенным покрытием закрепляют жесткий накладной трафарет, по которому очерчивают острым ножом определенные участки, подлежащие обработке. С этих участков защитное покрытие затем снимают, а подготовленные к химической обработке заготовки погружают в раствор.
Процесс химического растворения можно разделить на три периода. Вначале происходит растворение окис-ной пленки, имевшейся на поверхности металла, причем растворение это, как правило, протекает медленно. Далее накопляются газообразные продукты реакции на поверхности металла (обычно водород). На образование газообразных продуктов значительное влияние оказывает состояние поверхности. Серьезную роль играет и накопление числа катодов местных элементов на поверхности металла за счет разъедания металла и обнажения более благородных примесей или же за счет электрохимического обмена с электролитом. Второй период характеризуется подвижным равновесием между факторами и является установившимся процессом. Третий период характеризуется падением скорости реакции, уменьшением концентрации электролита и образованием на металле толстого слоя продуктов реакции.
Следует иметь в виду, что при химической обработке скорость растворения сплава по всей поверхности не одинакова. Одна из причин этого состоит в том, что трудно сохранить одинаковую температуру во всех точках обрабатываемой поверхности.
В процессе растворения поверхность металла разогревается, причем температуры раствора и металла не совпадают. Ухудшает условия теплоотдачи неравномерно выделяющийся водород. В местах, где температура выше, скорость растворения увеличивается. Все это приводит к неточности растворения, иногда выходящей за пределы требуемого допуска. Поэтому в ряде случаев необходимо принять ряд мер (перемешивание или циркулирование раствора, снижение концентрации и температуры раствора, правильное размещение нагревателей, контроль температуры в отдельных местах и др.), позволяющих уменьшить перепад температуры.
После выгрузки деталей из раствора их нужно тщательно промыть холодной водой, нейтрализовать остатки солей, вновь промыть холодной и горячей водой, высушить и снять защитное покрытие растворителем или сдирая покрытие.
Фотохимическая штамповка. Сущность ее заключается в нанесении защитного подслоя с последующим нанесением светочувствительного слоя, копировании и травлении.
Технологический процесс изготовления деталей состоит из следующих основных операций:
1. Подготовительные операции (нарезка материала на заготовки, полирование пластин с двух сторон, обезжиривание органическим растворителем, протирка мелом, промывка проточной водой, сушка).
2. Покрытие заготовок с двух сторон с помощью распылителя нитроклеем АК-20.
3. Нанесение тонкого слоя светочувствительной эмульсии в центрифуге. Эмульсия состоит из фотожелатина - 140 г/л, двухромовокислого аммония-15 г/л и 25% раствора аммиака.
4. Копирование в светокопировальной установке изображения с негатива (пленки). Если необходимо экспонировать на обе стороны заготовки, то для точного совпадения изображения с обеих сторон две негативные пленки предварительно приклеивают к узкой полоске материала такой же толщины, как и заготовка. Заготовку вставляют между негативами.
5. Проявление в воде при температуре 60-70 °С в течение 2-3 мин.
6. Окрашивание фиолетовым красителем в течение 2 мин. при 20 °С и закрепление в растворе следующего состава (в г):
7. Промывка проточной теплой и холодной водой и сушка на воздухе.
8. Удаление клея с пробельных мест тампоном, смоченным ацетоном.
9. Травление заготовки раствором хлорного железа уд. веса 1,33-1,55 с последующей промывкой и сушкой. Продолжительность травления устанавливается опытным путем.
10. Удаление защитного слоя погружением детали в ацетон.
Процесс фотохимической штамповки нашел применение на ряде заводов, в частности на ленинградском заводе «Вибратор» для изготовления различных приборных деталей из меди, латуни и бронзы толщиной до 0,2 мм.
В Новосибирском электротехническом институте для изготовления деталей из алюминиевого сплава Д16 этот процесс несколько изменен. Защиту не подлежащих травлению мест осуществляют электролитическим меднением. Для этого после закрепления эмульсии заготовки обжигают при 350-400 °С, удаляют окисный слой раствором и осаждают контактную медь в составе: и после тщательной промывки производят электролитическое меднение при плотности 2-3 а/дмг.
Удаляют эмульсию 15%-ным раствором каустической соды. Травление в местах, незащищенных медью, производят в 30%-ной соляной кислоте при 25-30 °С. В Ленинградском оптико-механическом объединении фотохимической штамповкой изготовляют из стальной фольги прецизионные детали фотоаппаратуры. С этой целью листы стальной фольги толщиной 0,05-0,2 мм покрывают слоем светочувствительной эмульсии. Контуры деталей печатают контактно на эмульсионном слое через негатив. Затем производят задубливание эмульсионного слоя и проявление в теплой воде с добавлением 1% метилвиолета до обнаружения контура детали на незадубленных участках. Растворение осуществляют в следующем растворе:
Температура раствора должна быть 15-20 °С, анодная плотность тока - 20 а/дм2, расстояние между электродами- 10 мм, продолжительность травления - 15-20 мин.
Этот метод применяют также для изготовления фильтровальных сеток из стали Х18Н9Т. В качестве светочувствительной эмульсии используют двухромово-кислый калий 10 г/л и поливиниловый спирт 70 г/л. Отпечатанный контактным путем рисунок сетки обрабатывают в растворе хромовой кислоты. Изоляцию осуществляют перхлорвиниловым лаком. Травление производят в ортофосфорной кислоте 600 г/л при плотности тока 100 а/дм2 (из расчета только площади отверстий). Катодами служат пластины из стали Х18Н9Т. Температура раствора 40 °С. Удаление защитного покрытия производят 10%-ным раствором каустической соды при 60-70° С.
Фотохимическая штамповка находит все большее применение в производстве электронных деталей, в оптико-механической и авиационной промышленности. Этот метод весьма экономичен при изготовлении тонкостенных деталей из металлической фольги толщиной от 0,01 до 0,2 мм. Точность изготовления - 0,01 мм с гладкими кромками, без заусенцев. Изготовление деталей сложных форм не требует квалифицированных рабочих. Нет необходимости и в штампах.
Химическое полирование. Одним из наиболее перспективных методов чистовой отделки деталей машин и приборов является химическое полирование. Возможность одновременной обработки большого количества деталей сложной формы и любых размеров, высокая производительность процесса, ненужность источников постоянного тока и контактирующих приспособлений и ряд других достоинств заставляют развивать исследовательские работы с целью усовершенствования химического полирования.
Лучшие результаты ныне достигнуты в области полирования алюминия и его сплавов, а также хромоникелевых нержавеющих сталей.
Сущность изобретения: способ вклгоча: ет нанесение на поверхность защитного покрытия, разметку и вырезку контура зоны химического фрезерования, сетчатое нарушение защитного покрытия внутри контура зоны фрезерования и травления металла на необходимую глубину при одновременном удалении защитного покрытия с зоны фрезерования отслаиванием. 2 ил., 1 табл.
СОЮЗ СОВЕТСКИХ
СОЦИАЛИСТИЧЕСКИХ
РЕСПУБЛИК (51) С 23 F 1/02
ГОСУДАРСТВЕННОЕ ПАТЕНТНОЕ
¹ 990871, кл, С 23 F 1/02, 1979.
Изобретение относится к химической обработке материалов и может быть применено в машиностроении для химического фреэерования, Известен способ и устройство для автоматического химфрезерования поверхности сложной кривизны, по которому нанесенный на поверхность детали защитный материал срезается лазером с эон, подлежащих химфрезерованию.
Однако срезание лазером защитного материала со всей поверхности подлежащей химической обработке, как предусмотрено в этом способе, малопроизводительно, т,к. энергия лазерного луча в момент удаления покрытия концентрируется на малой площади.
Наиболее близким к предложенному является способ получения деталей с участками переменной толщины путем химического травления, включающий предварительное нанесение защитного покрытия на участки поверхности, не подлежащие травлению и последующее его удаление отслаиванием.
«,5U 1791467 А1 (54) СПОСОБ ХИМИЧЕСКОГО ФРЕЗЕРОВАНИЯ ДЕТАЛЕЙ (57) Сущность изобретения: способ включает нанесение на поверхность защитного покрытия, разметку и вырезку контура зоны химического фреэерования, сетчатое нарушение защитного покрытия внутри контура зоны фрезерования и травления металла на необходимую глубину при одновременном удалении защитного покрытия с зоны фрезерования отслаиванием. 2 ил., 1 табл.
Удаление защитного покрытия в этом случае производится двумя способами: с равнотолщинных эон покрытие удаляется до процесса травления, а в процессе травления отслаивается защитное покрытие только с участка переменной толщины (клина), при- 4 чем производится эта операция с помощью О специального устройства, включающего электродвигатель, подвижную платформу, ф раму, вал для намотки защитного покрытия. О
К недостаткам известного способа можно отнести высокие трудо- и энергозатраты, связанные с необходимостью применения комбинированных методов снятия покры- Ф тия, использование специального устройства и связанные с этим монтажные работы, а также ограниченность применения только для деталей клиновидной формы.
Цель изобретения — повышение производительности и упрощение процесса.
Поставленная цель достигается тем, что в способе химического фрезерования деталей, включающем нанесение на поверхность защитного покрытия, разметку и
1791467 вырезку контура зоны химического фрезерования, травление металла на необходимую глубину при одновременном удалении защитного покрытия с зоны фреэерования отслаиванием, перед травлением металла проводят сетчатое нарушение защитного покрытия внутри контура зоны фрезерования.
Отличительными признаками изобретения является то, что перед травлением металла проводят сетчатое нарушение защитного покрытия внутри контура зоны фрезерования, Положительный эффект от использования прецполагаемого изобретения возникает вследствие повышения производительности процесса химфрезерования за счет исключения трудозатрат, связанных с удалением защитного материала с зон, подлежащих химическому фрезерованию, которое по предлагаемому способу осуществляется одновременно с растворением металла без дополнительного воздействия.
Химическое ф резерован ие деталей осуществляется в специализированной линии химического фрезерования.
На фиг.1 показан пример технологической планировки линии, на которой осуществляется способ; на фиг.2 — пример крепления детали для транпортировки по операциям техпроцесса химфрезерования, Линия химического фрезерования содержит ванны 1-4 для технологических растворов (число ванн определяется технологическим процессом и требуемой производительностью и может быть более указанного на рис.2), автооператор 5, перемещающийся вдоль линии по направляющим 6, 7, стенд контроля, имеющий две стойки 8 и 9, манипулятор 10 со сменным рабочим органом 11. Для крепления детали
12 используется рамка 13, имеющая механизм разворота 14, с зажимами 15, 16, 17.
Для транспортировки детали 12, закрепленной в рамке 13, вдоль линии автооператором 5 имеется траверса 18, связанная с рамкой 13 гибкими подвесками
19. Для монтажа детали 12 в рамку 13 служит монтажный стол 20. Для нанесения покрытия на деталь 12 имеется специальная камера 21. Для управления линией применен компьютер(управляющий вычислительный комплекс) 22, на который поступает информация с приборов контроля толщины деталей, контроля состояния защитного покрытия, контроля параметров технологических растворов и т,д.
Пример, Проводилось химическое фрезерование детали, изготовленной иэ алюминиевого сплава АМг-6, с исходной толщиной листа 8 мм, Состав сплава, мас.,4: медь 0,1, марга. нец 0,5-0,8; железо 0,4; кремний 0,4; титан
5 0,02-0,1; магний 5,8-6,8; бериллий 0,02-0,05; остальное алюминий.
Деталь имеет три зоны химфрезерования глубиной 2,1 мм, 3,4 мм, 5,9 мм.
На деталь 12 в камере 21 наносилось
10 пульверизатором защитное покрытие— эмаль КЧ 7101 с вязкостью 45 с по В3-4.
Покрытие наносилось в три слоя с сушкой каждого слоя 40 мин при 50 С и окончательной сушкой 6 ч при 80 С, Толщина пленки
15 180-200 мкм.
Монтаж покрытой детали 12 в рамку 13 проводился на монтажном стенде 20 в горизонтальном положении. Далее осуществлялась разметка зоны химфрезерования
20 с максимальной глубиной удаления металла и прорезка контура рисунка на защитном покрытии электровыжигательным карандашом "Силуэт". На поверхность зоны наносился рисунок в виде сетки с прореэа25 нием покрытия до металла. Расчет размеров
В ячеек сетки проводился с учетом фактора травления (отношение величины бокового подтравления а к глубине травления h), определенного на образцах, причем глубина
30 травления h принималась равной глубине растворения металла с наименьшей по глу- . бине зоны (2,1 мм). — — — — = 3,11 а 6,53
Размер ячейки определялся;
B=2xf=3,1 1 х2=6,22 мм
Размер ячейки принимался равным 6
По окончании процесса нанесения рисунка на зону, предназначенную для обработки, рамка 13 с деталью 12 перемещалась автооператором 5 по ваннам в соответствии
45 с технологическим процессом, Химическое фрезерование и отслаивание покрытия проводилось в ванне состава, г/л:
Едкий натрий 150-200
Триэтаноламин 20-30
50 Тиомочевина 6-10
Температура химфрезерования — 80 С
Аналогично проводилась разметка, нарушение сплошности покрытия и химфрезерование двух последующих зон.
55 Готовая деталь имела четкий контур химфрезерования с чистотой обработки поверхности R
Для подтверждения снижения трудозатрат проведена экспериментальная работа в условиях лабораторной базы
1791467 организации "Гермес". Сущность работы заключалась в сравнении трудозатрат хрснометрированием при хим резеровании традиционным способом (в соответствие с
ОСТ 92-4555-75) и способом, описываемым в изобретении. Работа проводилась на образцах из сплава АМг6, размерам 100х50х8 мм, В качестве защитного покрытия применялась эмаль КЧ-7101 (3 слоя). Размер "окна" фрезеруемой зоны 50х30 мм, глубиной сьема — 3 мм.
Результаты эксперимента приведены в таблице, Из приведенных данных следует, что при том >ке качестве поверхности трудозатраты в предлагаемом способе в среднем ни>ке на 10 $, т,e. и роизводител ьн ость труда возрастает. При больших габаритахдеталей и сложном контуре положительный эффект заметно возрастает.
Предложенный способ позволяет noeb сить производительность, снизить трудозат5 раты, упростить процесс химфрезерования, Формула изобретения
Способ химического фрезерования деталей, включающий нанесение на поверхность защитного покрытия, разметку и
10 вырезку контура зоны химического фреэерования, травление металла на необходимую глубину при одновременном удалении защитного покрытия с зоны фрезерования отслаиванием, отличающийся тем, 15 что, с целью повышения производительности и упрощения процесса фреэерования, перед травлением металла проводят сетчатое нарушение защитного покрытия внутри контура зоны фрезерования, 1791467
Заказ 135 Тираж Подписное
ВНИИПИ Государственного комитета по изобретениям и открытиям при ГКНТ СССР
113035, Москва, Ж-35, Раушская наб„4/5
Произаодстаанно-иадатальскиа комбинат "Патант", r. Ужгород, ул.Гагарина, 101 !
Редактор А. Егорова
Составитель И. Скоробогатов
Техред М.Моргентал Корректор С. Лисина
Похожие патенты:
Изобретение относится к химическому травлению, а именно к растворам для травления толстопленочных металлосодержащих покрытий, преимущественно для фотолитографического травления серебросодержащих покрытий на подложках из алюмооксидной керамики
Изобретение относится к травильным растворам и способам клеймения изделий из стали и меди и ее сплавов, покрытых цинком, кадмием, серебром, оловом и его сплавами, и может быть использовано в радиотехнической промышленности, приборостроении, авиационной промышленности и в других областях народного хозяйства для нанесения знаков, характеризующих изделие
Изобретение относится к травильным растворам и способам клеймения изделий из алюминия, титана и легированной стали и может быть использовано в радиотехнической промышленности, приборостроении, авиационной промышленности и в других областях народного хозяйства для нанесения знаков, характеризующих изделие
Изобретение относится к области металлургии. Для обеспечения благоприятных значений потерь в сердечниках на холоднокатаном стальном листе образуют резистную пленку для изготовления канавки путем травления, при этом в резистной пленке образуют открытую часть стального листа, содержащую первую область, ориентированную в направлении ширины листа, и множество вторых областей, начинающихся от первой области, причем ширина первой области и вторых областей составляет от 20 мкм до 100 мкм, и расстояние от концевой части одной из вторых областей до концевой части смежной с ней другой области из вторых областей составляет от 60 мкм до 570 мкм. 2 з.п. ф-лы, 7 ил., 1 табл.
Изобретение относится к производству листа из текстурированной электротехнической стали. Для снижения потерь в железе материала стальной лист толщиной 0,30 мм или менее содержит пленку форстерита и покрытие, создающее напряжение на поверхности стального листа, линейные канавки, сформированные с интервалом в 2-10 мм на поверхности листа в направлении прокатки для модификации магнитного домена, при этом глубина каждой из линейных канавок составляет 10 мкм или более, толщина пленки форстерита в нижней части линейных канавок составляет 0,3 мкм или более, общее напряжение на стальном листе, создаваемым пленкой форстерита и покрытием, составляет 10,0 МПа или выше в направлении прокатки и доля потерь на вихревые токи в потерях в железе W17/50 стального листа составляет 65% или менее в переменном магнитном поле 1,7 Тл и 50 Гц, создаваемом в стальном листе в направлении прокатки. 2 н. и 1 з.п. ф-лы, 3 табл., 1 пр., 2 ил.
Изобретение относится к области металлургии. В настоящем изобретении разработан лист электротехнической текстурированной стали, который может поддерживать низкое значение потерь в сердечнике, собранном в виде фактического трансформатора, и имеет отличные характеристики потерь в сердечнике действующего трансформатора, в котором толщину (мкм) пленки a1 изолирующего покрытия на дне линейных канавок, толщину (мкм) пленки a2 изолирующего покрытия на поверхности стального листа в частях, отличающихся от линейных канавок, и глубину (мкм) a3 линейных канавок регулируют таким образом, чтобы они удовлетворяли соотношениям: 0,3 м к м ≤ a 2 ≤ 3,5 м к м и a 2 + a 3 − a 1 ≤ 15 м к м. 2 з.п. ф-лы, 2 табл., 2 ил., 1 пр.
Химическими называются методы обработки материалов, в которых снятие слоя материала происходит за счет химических реакций в зоне обработки. Достоинства химических методов обработки: а) высокая производительность, обеспечиваемая относительно высокими скоростями протекания реакций, прежде всего отсутствием зависимости производительности от величины площади обрабатываемой поверхности и ее формы; б) возможность обработки особо твердых или вязких материалов; в) крайне малое механическое и тепловое воздействие в процессе обработки, что делает возможным обработку деталей малой жесткости с достаточно высокой точностью и качеством поверхности.
Размерное глубокое травление (химическое фрезерование) является наиболее распространенным методом химической обработки. Этим методом целесообразно пользоваться для обработки поверхностей сложных в плане форм на тонкостенных деталях, получения трубчатых деталей или листов с плавным изменением толщины по длине, а также при обработке значительного числа мелких деталей или круглых заготовок с большим; количеством обрабатываемых мест (перфорация цилиндрических поверхностей труб). Путем местного удаления этим методом из лишнего материала в ненагруженных или малонагруженных можно снизить общий вес самолетов и ракет, не снижая их прочности и жесткости. В США использование химического фрезерования позволило снизить вес крыла сверхзвукового бомбардировщика на 270 кг. Этот метод позволяет создавать новые элементы конструкций, например листы 1 переменной толщины. Химическое фрезерование находит применение также при изготовлении печатных схем радиоэлектронной аппаратуры. В этом случае у панели из изоляционного материала, покрытой с одной или двух сторон медной фольгой, травлением удаляют заданные схемой участки.
Технологический процесс химического фрезерования складывается из следующих операций.
1. Подготовка деталей к химическому фрезерованию для обеспечения последующего плотного и надежного сцепления защитного покрытия с, поверхностью детали. Для алюминиевых сплавов эту подготовку осуществляют: обезжириванием в бензине Б70; легким травлением в ванне с едким натром 45-55 г/л и фтористым натром 45-55 г/л при температуре 60-70° С в течение 10-15 мин для снятия плакированного слоя; промывкой в теплой и холодной водах и осветлением в азотной кислоте с последующей промывкой и сушкой. Для нержавеющих и титановых сплавов подготовку деталей производят путем протравливания для снятия окалины в ванне с плавиковой (50-60 г/л) и азотной (150-160 г/л) кислотами или в ванне с электроподогревом до 450-460° С в едком натре и азотнокислом натрии (20%) с последующей промывкой и сущкой, обезжириванием и легким травлением с повторной промывкой и сушкой.
2. Нанесение защитных покрытий на места обрабатываемой детали, не подлежащие травлению. Его производят путем установки специальных накладок, химически стойких шаблонов прилипающего типа или, наиболее часто, нанесением лакокрасочных покрытий, в качестве которых обычно используют перхлорвиниловые лаки и эмали, полиамидные лаки и материалы на основе не опреновых каучуков. Так, для алюминиевых сплавов рекомендуется эмаль ПХВ510В, растворитель РС1 ТУ МХП184852 и эмаль ХВ16 ТУ МХПК-51257, растворитель Р5 ТУ МХП219150, для титановых сплавов - клей АК20, разбавитель РВД. Для лучшего сцепления этих покрытий с металлом иногда предварительно производят анодирование поверхности. Нанесение лакокрасочных покрытий осуществляют кистями или пульверизаторами с предварительной защитой мест травления шаблонами или путем погружения в ванну; в последнем случае на высушенной защитной пленке производят разметку контура, затем его прорезку и удаление.
3. Химическое растворение производят в ваннах с соблюдением температурного режима. Химическое фрезерование алюминиевых и магниевых сплавов производят в растворах едких щелочей; сталей, титана, специальных жаропрочных и нержавеющих сплавов - в растворах сильных минеральных кислот.
4. Очистка после травления деталей из алюминиевых сплавов с эмалевым защитным покрытием производится промывкой в проточной воде при температуре 50+70° С, отмачиванием защитного покрытия в более горячей проточной воде при температуре
70-90° С и последующим снятием защитного покрытия ножами вручную или мягкими щетками в.растворе этилацетата с бензином (2:1). Затем производят осветление или легкое травление и сушку.
Качество поверхности после химического фрезерования определяется исходной шероховатостью поверхности заготовки и режимами травления; обычно она на 1-2 класса ниже чистоты исходной поверхности. После травления все имевшиеся ранее на заготовке дефекты. (риски, царапины, неровности) сохраняют свою глубину, но уширяются, приобретая большую плавность; чем больше глубина травления, тем сильнее проявляются эти изменения. На качество поверхности влияют также способ получения заготовок и их термообработка; прокатанный материал дает лучшую поверхность по сравнению со штампованным или прессованным. Большая шероховатость поверхности с резко выраженными неровностями получается на литых заготовках.
На шероховатость поверхности оказывают влияние структура материала, размер зерен и их ориентация. Закаленные алюминиевые листы, подвергнутые старению, имеют более высокий класс чистоты поверхности. Если структура крупнозернистая (например, металл отожжен), то окончательно обработанная поверхность будет с большими шероховатостями, неровной, бугристой. Наиболее пригодной для химической обработки следует считать мелкозернистую структуру. Заготовки из углеродистой стали лучше обрабатывать химическим фрезерованием перед закалкой, так как в случае наводороживания при травлении последующий нагрев способствует удалению водорода. Однако тонкостенные стальные детали желательно закаливать перед химической обработкой, так как последующая термическая обработка может вызвать их деформацию. Обработанная химическим фрезерованием поверхность всегда несколько разрыхлена вследствие растравливания, и поэтому этот метод Значительно снижает усталостные характеристики детали. Учитывая это, для деталей, работающих в условиях циклических нагрузок, необходимо после химического фрезерования проводить полирование.
Точность химического фрезерования ±0,05 мм по. глубине и не менее +0,08 мм по контуру; радиус закругления стенки выреза получается равным глубине. Химическое фрезерование обычно производят на глубину 4-6 мм и реже до 12 мм; при большей глубине фрезерования резко ухудшается качество поверхности и точность обработки. Минимальная окончательная толщина листа после травления может составлять 0,05 мм, поэтому химическим фрезерованием можно обрабатывать детали с очень тонкими перемычками без коробления, проводить обработку- на конус путем постепенного погружения детали в раствор. При необходимости травления с двух сторон нужно либо располагать заготовку вертикально так, чтобы дать возможность выделяющемуся газу свободно подниматься с поверхности, либо травить в два приема - 1 сначала с одной стороны, а потом с другой. Второй способ предпочтительнее, так как при вертикальном расположении заготовки верхние кромки вырезов обрабатываются хуже из-за попадающих туда пузырьков газа. При изготовлении глубоких вырезов следует применять специальные меры (например, вибрации) по удалению с обрабатываемой поверхности газа, который препятствует осуществлению нормального процесса. Контроль глубины, травления в процессе обработки осуществляют погружением Одновременно с заготовкой контрольных образцов, непосредственным контролем размеров толщиномерами типа индикаторной скобы или электронными, а также посредством автоматического весового контроля.
Производительность химического фрезерования определяется скоростью удаления материала по глубине. Скорость травления возрастает с повышением температуры раствора примерно на 50-60% на каждые 10° С, а также зависит от вида раствора, его концентрации и чистоты. Перемешивание раствора в процессе травления можно производить сжатым воздухом. Процесс травления определяется экзотермической реакцией, поэтому подача сжатого воздуха несколько его охлаждает, однако в основном постоянство температуры обеспечивается помещением в ванну водяных змеевиков.
Травление методом погружения имеет ряд недостатков - использование ручного труда, частичный пробой защитных пленок на необрабатываемых поверхностях. При обработке ряда деталей более перспективен струйный метод травления, при котором подача щелочи осуществляется форсунками.
Средством повышения производительности химического фрезерования является использование ультразвуковых колебаний с частотой 15-40 кгц; в этом случае производительность обработки увеличивается в 1,52,5 раза - до 10 мм/ч. Процесс химической обработки также значительно ускоряется под воздействием инфракрасного излучения направленного действия. В этих условиях отпадает необходимость в нанесении защитных покрытий, так как сильному нагреву подвергается металл по заданному контуру нагрева, остальные участки, будучи холодными, практически не растворяются.
Время травления устанавливают опытным путем на контрольных образцах. Протравленные заготовки вынимают из травильной машины, промывают в холодной воде и для удаления эмульсии, краски и клея БФ4 обрабатывают при температуре 60-80° С в растворе, содержащем 200 г/л каустической соды. Готовые детали тщательно промывают и сушат в потоке воздуха.
Улучшение условий черновой обработки заготовок резанием путем предварительного удаления корки травлением является другим примером растворяющего действия реактива. Перед травлением заготовки с целью удаления окалины подвергают обдувке песком. Травление титановых сплавов производят в реактиве, состоящем из 16% азотной и 5% фтористоводородной кислот и 79% воды. По данным зарубежной литературы, для этой цели применяют травление в соляных ваннах с последующей промывкой в воде и затем повторным травлением в кислотных травителях для окончательной очистки поверхности.
Химическое воздействие технологической среды находит применение и для улучшения процессов обычного резания; все более широкое применение находят методы обработки материалов, основанные на сочетании химического и механического воздействий. Примерами уже освоенных методов является химико-механический способ шлифования твердых сплавов, химическое полирование и др.