Способ модификации поверхностного слоя металлических изделий. Способ модификации поверхности Метод модификации свойств поверхности изделия
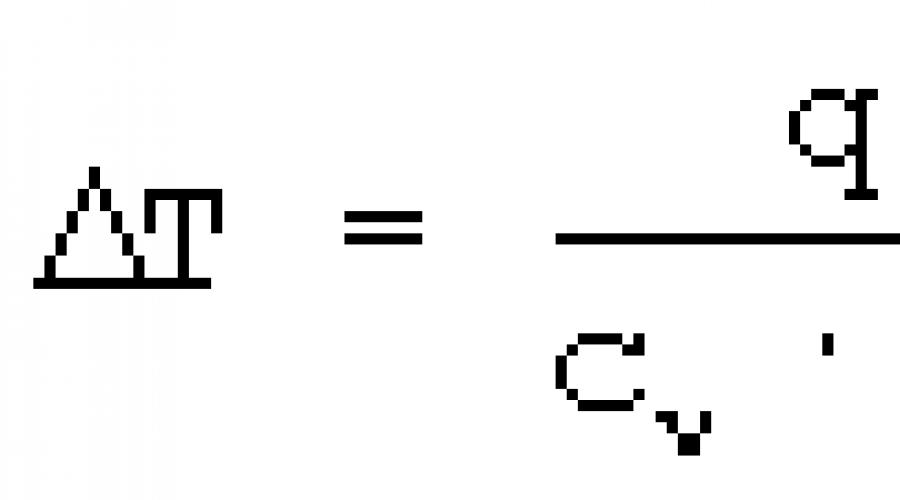
Читайте также
Под физико-химическим модифицированием понимают целенаправленное изменение свойств поверхности в результате технологического внешнего воздействия. При этом имеется в виду изменение структуры материала в тонких поверхностных слоях вследствие физического воздействия (ионными и электронными пучками, низкотемпературной и высокотемпературной плазмы, электрического разряда и др.) или химического воздействия, приводящего к образованию на поверхности слоев химических соединений на основе базового материала (химическое, электрохимическое и термическое оксидирование, фосфатирование, сульфидирование, плазменное нитрирование и т.д.).
Очевидно, что отсутствует выраженная классификационная граница между процессами физико-химического модифицирования и поверхностного упрочнения.
Среди множества способов физико-химического модифицирования наиболее перспективными представляются ионная имплантация, анодирование, в частности импульсное (обработка в электролитной плазме), лазерное упрочнение.
Ионная имплантация является сравнительно новым способом физико-химического модифицирования, основанным на внедрении ускоренных ионов легирующих элементов в поверхностный слой.
|
Рис. 19.12. Схема установки для ионной имплантации с линейным ускорителем (а) и З D-имплантаиии (б):
1 - источник ионов; 2 - система вытягивания ионов; 3 - сепаратор; 4 - фокусирующие магниты; 5 - линейный ускоритель; 6 - электростатическая отклоняющая система; 7 - поток ионов; 8 - упрочняемые детали
Имплантируемые ионы имеют малую глубину проникновения, однако их влияние распространяется намного дальше от поверхности.
Можно выделить следующие особенности ионной имплантации:
Возможность формирования на поверхности сплавов, которые нельзя получить в обычных условиях из-за ограниченной растворимости или диффузии компонентов. В ряде случаев равновесные пределы растворимости превышены на несколько порядков;
Легирование не связано с диффузионными процессами, за исключением модифицирования материалов ионной имплантации при большой плотности тока, когда наблюдается радиационно-стимулированная диффузия компонентов;
Процесс протекает при низких температурах (менее 150 °С), без изменения механических свойств материала. Метод позволяет обрабатывать термочувствительные материалы;
Отсутствует заметное изменение размеров деталей после имплантации;
Модифицированные поверхности не требуют дальнейшей финишной обработки;
Процесс хорошо контролируется и воспроизводится;
Экологическая чистота процессов;
Упрочняются только открытые поверхности, непосредственно находящиеся под воздействием облучения ионами;
Малая глубина модифицированного слоя;
Относительно высокая стоимость оборудования.
Установка для имплантации ионным лучом содержит источник ионов, систему «вытягивания» ионов 2, сепаратор ионов 3, магнитные фокусирующие линзы 4, линейный ускоритель 5, электростатическую отклоняющую систему б. На практике используются различные по конструкции источники ионов непрерывного и импульсного действия, генерирующие ионы газов (от водорода до криптона) и металлов (с горячим и холодным катодом, магнетронный, диаплазмотрон и др.). Выходящие из источника ионы неоднородны по составу. Для отделения посторонних ионов используется магнитный масс-сепаратор, который отклоняет от основной оси ионы, имеющие другую массу и заряд. «Очищенный» ионный луч фокусируется и ускоряется в линейном ускорителе. Сканирование ионного луча по поверхности упрочняемой детали производится отклоняющей системой 6 .
Для обеспечения равномерности упрочнения деталь вращается и поворачивается относительно луча.
Ионная имплантация ионами плазмы - иногда ее называют ЗБ-имплантация - выполняется в вакуумных камерах, где тлеющим или дуговым разрядом создают ионизированную среду, а на деталь подается импульсное высокое напряжение, обеспечивающее ускорение ионов в направлении бомбардируемых поверхностей. Высокоэнергетический ионный поток может формироваться непосредственно в процессе горения импульсного самостоятельного разряда между заземленной вакуумной камерой и изделием, являющимся катодом.
Ионы, ускоренные в поле прикатодного падения малой толщины, эффективно модифицируют поверхность изделия, которое может иметь сложную объемную форму. Падающие ионы генерируют электронный пучок с поверхности изделия, который, взаимодействуя с плазмой, обеспечивает самоподдержание разряда. Этот метод имеет определенные преимущества перед лучевыми методами за счет простоты и относительно низкой цены реализации технологических процессов. Он может сочетаться с другими ионно-плазменными методами обработки, такими, как магнетронное, вакуумно-дуговое и плазменно-термическое напыление, ионное азотирование и др.
При высокоэнергетической ионной имплантации для упрочнения металлов и сплавов, керамик, полимеров используются ионы газов с энергией до 100 кэВ.
Обработка высокоэнергетическими ионами азота эффективно повышает стойкость режущего и штампового инструмента, усталостную прочность деталей.
Имплантация атомов внедрения (азот, углерод и бор) способствует повышению износостойкости и сопротивления усталости сталей. Эти элементы обладают свойством сегрегации к дислокациям даже при комнатной температуре, что блокирует их движение и упрочняет поверхностный слой, а это в свою очередь препятствует развитию усталостных трещин.
При ионной имплантации никеля бором усталостная прочность увеличивается более чем на 100 %.
Увеличение усталостной прочности обусловлено не действием остаточных напряжений сжатия, возникающих при ионной имплантации, как считалось раньше, а торможением развития усталостных трещин вследствие снижения подвижности дислокаций.
Для повышения антифрикционных свойств может выполняться имплантация ионов молибдена и двойного количества ионов серы. Совместная имплантация может стать новым методом формирования антифрикционных и других специальных легированных слоев.
Имплантируя титан, получают на поверхности аморфную фазу Ti-C-Fe, что приводит к снижению трения и износа.
Ионная имплантация широко используется для повышения коррозионной стойкости стальных деталей. С этой целью имплантируют ионы.
Локальная термическая обработка осуществляет модифицирование структуры поверхностного слоя. При этом обеспечиваются такие температурно-временные режимы и результаты упрочнения, которые сложно или невозможно получить традиционными способами термической обработки, а именно:
Высокие скорости нагрева и охлаждения (скорости нагрева достигают величин 10 4 ... 10 8 К/с, а скорости охлаждения - 10 3 ... 10 4 К/с в зависимости от времени воздействия и энергии излучения, а также от режимов работы лазера). Такие режимы нагрева и охлаждения приводят к неравновесному протеканию фазовых превращений, к смещению критических точек А с и А, образованию пересыщенных твердых растворов с мелкодисперсными структурами вплоть до аморфных. В результате формируется слой с повышенной твердостью (превышает на 15 ... 20 % твердость после закалки существующими способами), с хорошим сопротивлением износу и схватыванию при трении;
Возможность упрочнения поверхностей в труднодоступных местах (полости, углубления), куда луч лазера может быть введен с помощью оптических устройств;
Использование лазера позволяет резко уменьшить глубину закаленного слоя и эффективно управлять его величиной.
Лазерное закаливание используется для упрочнения режущего и мерительного инструмента, рабочих кромок матриц и пуансонов на глубину до 0,15 мм (импульсное излучение) и до 1,5 мм (непрерывное излучение). На инструментальных сталях твердость составляет 63 ... 67 HRC. Шероховатость обрабатываемой поверхности при этом не изменяется.
Установлено, что использование лазерного излучения в качестве источника нагрева при термопластическом упрочнении никелевых сплавов позволяет получать в поверхностном слое остаточные напряжения сжатия величиной до 10 ГПа.
При лазерной термической обработке можно создать условия избирательного испарения выступов неровностей, которые приводят к снижению шероховатости поверхности.
Лазерная наплавка является одним из наиболее перспективных способов восстановления ответственных деталей ГТД, в частности лопаток турбин и компрессоров. Ее основными достоинствами являются возможность устранения небольших дефектов без разогрева примыкающей к дефекту поверхности и отсутствие поводок при наплавке.
Лазерную наплавку производят в камерах с защитной атмосферой или с поддувом инертного газа. В качестве присадочных материалов используют проволоку, фольгу или порошковые материалы.
Лазерная наплавка порошковыми металлическими сплавами при минимальном термическом воздействии позволяет повысить в несколько раз работоспособность деталей в тяжелых температурных, эрозионных и других условиях эксплуатации.
Изобретение относится к области химико-физической обработки поверхностного слоя металлических изделий из титана и его сплавов с целью изменения их поверхностных свойств. Способ включает физико-химическую обработку поверхности изделий и алитирование, при этом физико-химическую обработку поверхности изделий производят электрохимическим полированием в электролите следующего состава: хлорная кислота - 1 часть; уксусная кислота - 9 частей, при температуре 30-35°С, плотности тока 2 А/дм 2 , напряжении 60 В, в течение 3 мин. Технический результат: активизация взаимодействия поверхности металлических изделий к контактирующим средам и веществам, высокая окалиностойкость и коррозионностойкость, высокие антифрикционные свойства. 1 табл.
Изобретение относится к области химико-физической обработки поверхностного слоя металлических изделий из титана и его сплавов с целью изменения их поверхностных свойств.
Поверхностные явления - выражение особых свойств поверхностных слоев, т.е. тонких слоев вещества на границе соприкосновения тел (сред, фаз). Эти свойства обусловлены избытком свободной энергии поверхностного слоя, особенностями его структуры и состава. Молекулярная природа и свойства поверхности могут коренным образом изменяться в результате образования поверхностных мономолекулярных слоев или фазовых (полимолекулярных) пленок. Любое "модифицирование" поверхностного (межфазного) слоя обычно приводит к усилению или ослаблению молекулярного взаимодействия между контактирующими фазами (лиофильность и лиофобность). Лиофильность означает хорошее (часто полное) смачивание, малое межфазное натяжение, устойчивость поверхностей к взаимному слипанию. Лиофобность - противоположное понятие.
При контакте двух твердых тел или твердого тела с жидкой и газовой средами свойства поверхности определяют условия таких явлений, как адгезия, смачивание, трение. Физические или химические превращения в поверхностных слоях сильно влияют на характер и скорость гетерогенных процессов - коррозионных, каталитических, мембранных и др. Поверхностные явления в значительной мере определяют пути получения и долговечность важнейших строительных и конструкционных материалов, в частности, производимых в металлургии.
Смачивание (лиофильность) является необходимым условием при поверхностном насыщении титана алюминием и другими элементами (диффузионное насыщение металлами). Изделие, поверхность которого обогащена этими элементами, приобретает ценные свойства, к числу которых относятся высокая окалиностойкость, коррозионностойкость, повышенная износостойкость, твердость и свариваемость.
Несмачиваемость (лиофобность) незащищенного металла повышает его стойкость к агрессивным средам.
В патенте (патент РФ 2232648, МПК B 05 D 5/08, публ. 2004.07.20) указывается, что свойства поверхностей проявляются по-разному. Обусловлено это тем, что поверхности изготавливают из самых разных материалов, и они имеют в большинстве случаев различную структуру. В частности, наиболее лиофобными свойствами обладают металлы, выбранные из группы, включающей бериллий, магний, скандий, титан, ванадий, хром, марганец, железо, кобальт, никель, медь, цинк, галлий, иттрий, цирконий, ниобий, молибден, технеций, рутений, рений, палладий, серебро, кадмий, индий, олово, лантан, церий, празеодим, неодим, самарий, европий, гадолиний, тербий, диспрозий, гольмий, эрбий, тулий, иттербий, лютеций, гафний, тантал, вольфрам, рений, осмий, иридий, платину, золото, таллий, свинец, висмут, прежде всего титан, алюминий, магний и никель либо соответствующий сплав названных металлов.
Большое влияние на поверхностные свойства оказывают карбидные и оксидные пленки. Особенно плотные пленки карбида и оксида наблюдаются у химически активных металлов, например титана и циркония.
Известен способ изменения поверхностных свойств сплавов на основе титана (У.Цвингер, «Титан и его сплавы», перевод с немецкого, Москва, «Металлургия», 1979 г., стр.326), в котором автор утверждает, что «оксидный слой, всегда существующий на поверхности титана, чаще всего не смачивается металлами. При повышенных температурах в расплавах смачивание происходит в случаях предварительного отжига титана в вакууме, когда образуется безоксидная поверхность. При изгибах таких образцов образуются трещины».
Недостатком данного способа подготовки поверхности к металлизации является сложно и трудно осуществимый механизм обработки многотонных слитков, слябов, крупногабаритных заготовок. Кроме того, в способе не учитывается влияние на ту же смачиваемость поверхности другого элемента внедрения - углерода. Установлено (Курапов В.Н., Трубин А.Н., Курапова Л.А., Савельев В.В. «Изучение особенностей распределения углерода в титановых сплавах методом радиоактивных индикаторов (РАИ), Сборник «Металловедение и обработка титановых и жаропрочных сплавов». Москва, 1991 г.; В.В.Тетюхин, В.Н.Курапов, А.Н.Трубин, Л.А.Курапова, «Исследование слитков и полуфабрикатов титановых сплавов с применением метода радиоактивных индикаторов (РАИ)» Научно-технический журнал «Титан», № 1(11), 2002 г.), что при нагреве сплавов углерод транспортируется к поверхностным слоям из нижележащих объемов, но не покидает кристаллическую решетку титана, в отличии от стали, где при высокотемпературном нагреве углерод образует летучее соединение по формуле:
C (Тв) +O2 (газ) СO2 (газ) .
Следовательно, в отличие от стали, где происходит обезуглероживание поверхности, в титане происходит лишь его перераспределение в поверхностных слоях. Также установлено, что подобное перераспределение углерода в поверхностных слоях заготовок и изделий происходит при резании металла, что является следствием его локального нагрева и деформации. Это перераспределение наблюдается при различных видах резания, включая обработку зубилом и напильником, даже при самых «мягких» режимах, например точении.
В отличие от перераспределения углерода в поверхностных слоях при высокотемпературном нагреве, которое видно на фотопленке невооруженным взглядом, в случае резания металла перераспределение наблюдается при увеличении. Это перераспределение в самом поверхностном слое более хаотично. В глубине металла выявляются эквивалентные механическим и тепловым нагрузкам, возникающие при обработке материала, волнообразные кривые перераспределения углерода в поверхностном слое, что делает совершенно нестабильным физико-химические свойства поверхности после резания. Эта нестабильность, как показано выше, не устраняется вакуумным отжигом.
Известен способ очистки поверхности кремния (Патент РФ № 1814439, публ. 1995.02.27, МПК H 01 L 21/306). Сущность изобретения: кремниевые пластины обрабатывают в жидкостном травителе. Образовавшийся окисный слой и поверхность кремния удаляют при комнатной температуре травлением в дифториде ксенона. При этом достигается высокая степень обезуглероживания поверхности. Затем пластины кремния без соприкосновения с атмосферой переносят в вакуумную камеру и удаляют адсорбированные на поверхности фториды нагревом и выдержкой при 600°С в сверхвысоком вакууме. Для перекристаллизации амортизированного слоя на поверхности кремния может быть проведен отжиг при более высокой температуре.
Данный способ дорогостоящий и может быть использован при обработке деталей малых геометрических размеров.
Известен способ поверхностной химико-термической модификации узлов трения (Патент РФ № 2044104, публ. 20.09.1995 г., МПК С 23 С 8/40). Способ включает взаимодействие с реакционной жидкостью с последующей термообработкой.
К недостаткам данного способа относится то, что он используется для повышения износостойкости конструкционных материалов, а в качестве модификатора поверхности используется фторированный углерод, отличающийся высокой лиофобностью, поверхность практически не смачивается.
Известен способ горячего алюминирования изделий из титана и его сплавов (SU 160068, опубл. 14.01.1964) - прототип, при котором изделия подвергают травлению растворами серной (35-65%) или соляной (30-37%) кислоты при температуре 50-70°С продолжительностью 30-40 мин или при комнатной температуре в течение 2-3 ч с получением на них гидридной пленки вместо оксидной, после чего изделия погружают в расплавленный алюминий при температуре 800-850°С.
Недостатком данного способа является свойства гидридной пленки, имеющей хрупкую, пористую природу, с большим количеством микротрещин и полостей, которые могут проникать на глубину 0,2-0,3 мм, образуя между основным металлом и покрытием участки с пористой структурой. Кроме того, в процессе контактирования расплавленного алюминия с гидридами титана происходит их разложение с выделением водорода, что предопределяет образование в алюминиевом покрытии пор. Сочетание этих факторов резко снижает стойкость полученного покрытия.
Задачей предлагаемого изобретения является повышение лиофильности поверхностного слоя заготовок и изделий из сплавов на основе титана за счет удаления поверхностного слоя, содержащего оксиды и карбиды, без использования механической обработки и отжига.
Техническим результатом, достигаемым при осуществлении изобретения, является активизация взаимодействия поверхности металлических изделий к контактирующим средам и веществам, что придает им качественно новые свойства - высокую окалиностойкость и коррозионностойкость, высокие антифрикционные свойства.
Указанный технический результат достигается тем, что в способе модификации поверхностного слоя изделий из титана и его сплавов, включающей физико-химическую обработку поверхности изделий и алитирование, физико-химическую обработку поверхности изделий производят электрохимическим полированием в электролите следующего состава: хлорная кислота - 1 часть; уксусная кислота - 9 частей, при температуре 30-35°С, плотности тока 2 А/дм 2 , напряжении 60 В, в течение 3 мин.
При электрохимической обработке под действием электрического тока в электролите происходит растворение материала анода (поверхностного слоя изделия), причем быстрее всего растворяются выступающие части поверхности, что приводит к ее выравниванию. При этом материал, в т.ч. оксидная или карбидная пленка, снимается со всей поверхности, в отличие от механического полирования, где снимаются только наиболее выступающие части. Электролитическое полирование позволяет получить поверхности весьма малой шероховатости. Важное отличие от механического полирования - отсутствие каких-либо изменений в структуре обрабатываемого материала, что не вызывает перераспределения углерода по толщине изделия и очаговую концентрацию его на поверхности.
Происходит полное удаление поверхностного слоя, содержащего оксиды и карбиды, и поверхность изделий, изготовленных из химически активных металлов, приобретает высокую лиофильность, позволяющую проводить высококачественную химико-термическую обработку поверхностного слоя, например алитирование.
Предлагаемый способ опробован при алитировании образцов титанового сплава ВТ8 в расплаве алюминия марки А85 в течение 4-х часов при температуре 850°С. Было изготовлено по четыре образца с различными способами подготовки поверхности, и были получены следующие результаты (табл.):
Табл. | ||
№ | Способ подготовки поверхности | Качество алитирования |
1 | Тонкое точение | Отсутствие налипания алюминия на поверхности. |
2 | Механическое полирование | Очаговое налипание (тонким слоем приблизительно на 42-57% поверхности). |
3 | Электрохимическое полирование в электролите следующего состава: хлорная кислота - 1 часть, уксусная кислота - 9 частей. При температуре электролита - 30-35°С, плотности тока - 2 А/дм 2 , напряжении - 60 B, в течение 3 мин. | Налипание алюминия по всей поверхности.* |
*Локальное определение алюминия в плоскости, перпендикулярной оси образца, показало:
а) его равномерное по окружности проникновение вглубь образца,
б) выявило диффузионную зону обогащения алюминием титанового образца,
в) обнаружило на поверхности образца зону растворяемого в алюминии титана.
Таким образом, устранение поверхностного слоя, обогащающегося углеродом (из глубины металла) и кислородом из атмосферы после любой механической обработки заготовок и деталей из титана и его сплавов электрополированием, является простым и надежным способом активизации взаимодействия контактирующих металлов при металлизации. Изобретение позволяет при незначительных материальных и трудовых затратах перевести лиофобную поверхность в лиофильную. Активизация поверхности позволяет, например, улучшить сцепление при диффузионном легировании поверхности с металлом, увеличить скорость диффузии атомов внедряемого металла в кристаллическую решетку заготовок и изделий, что придает их поверхностям качественно новые эксплуатационные качества, в частности:
Высокую окалиностойкость и коррозионностойкость - покрытие из алюминия снижает скорость окисления титановых сплавов при температуре 800-900°С в 30-100 раз. Это происходит в результате образования на поверхности покрытия слоя -Al 2 O 3 (Э.М.Лазарев и др., Окисление титановых сплавов, М., Наука, 1985 г., стр.119);
Высокие антифрикционные свойства, т.к. коэффициент трения алюминия значительно ниже, чем у титановых сплавов.
ФОРМУЛА ИЗОБРЕТЕНИЯ
Способ модификации поверхностного слоя изделий из титана и его сплавов, включающий физико-химическую обработку поверхности изделий и алитирование, отличающийся тем, что физико-химическую обработку поверхности изделий производят электрохимическим полированием в электролите следующего состава: хлорная кислота - 1 часть; уксусная кислота - 9 частей, при температуре 30-35°С, плотности тока 2 А/дм 2 , напряжении 60 В в течение 3 мин.
Владельцы патента RU 2265075:
Изобретение относится к области металлургии, а именно к способам обработки поверхностей токопроводящих материалов. Предложен способ модификации поверхности токопроводящих тел путем ее разогрева переменным электрическим током, при этом для модификации поверхности используют импульсы тока длительностью 20-100 нс и с амплитудой, обеспечивающей глубину оплавления поверхности 1-10 мкм. Технический результат - разработка способа модификации поверхности токопроводящих тел для повышения эксплуатационных характеристик металлов и сплавов и управления требуемыми свойствами, такими как твердость, износостойкость, усталость и коррозионная стойкость. 3 ил.
Изобретение относится к области обработки электропроводящих материалов путем нагрева электрическим полем.
Уровень техники
Многие физико-механические свойства материалов сильно зависят от состояния поверхности. Например, твердость, усталость, износ, коррозионная прочность и трещиностойкость существенно улучшаются при уменьшении размера зерна и аморфизации поверхностного слоя. Известно большое количество способов воздействия на поверхность с целью ее упрочнения. К числу таких способов относятся плакирование и нанесение различных покрытий, лазерная и механическая обработка (например, пескоструйная), ионная имплантация и так далее . Методами быстрой закалки из расплава получаются аморфные и нанокристаллические материалы определенных химических составов. Критическая скорость охлаждения, требуемая для аморфизации, и температура стеклования зависят от природы химического состава расплава. Обычные скорости закалки для аморфизующихся систем составляют 10 5 -10 7 К/сек и достигаются в методах спиннингования расплава - охлаждение струи на массивном вращающемся блоке, прокатки расплава между холодными валками, распыление струи расплава газовыми потоками (газовая атомизация).
Такими способами получают либо порошки или чешуйки с характерными размерами 1-100 нм, либо тонкие ленты толщиной 10-100 мкм . Для аморфизации чистых металлов требуются чрезвычайно высокие скорости охлаждения -10 12 -10 14 К/сек , которые недостижимы при современных схемах быстрой закалки . Более медленные скорости закалки 10 2 -10 4 - К/сек применяют для получения так называемых массивных металлических стекол с характерными размерами порядка нескольких милиметров в сечении . Такие стекла получают из расплавов с широкой областью переохлаждения, наличие или отсутствие которой определяется химическим составом сплава. Малые размеры, высокая стоимость и ограниченность аморфизующихся составов при скоростной закалке ограничивают области применения аморфных сплавов. Достоинства поверхностной обработки готовых изделий очевидны. Так, например, метод ионной имплантации используется для аморфизации поверхностного слоя бомбардировкой ионами высоких энергий (например, бомбардировка никеля ионами P + при комнатной температуре - доза 10 17 ион/см 2 , энергия ионов 40 кэВ - приводит к образованию аморфной фазы в поверхностном слое ).
Хорошо известен метод лазерной аморфизации поверхности, который использует мощный импульсный лазерный луч, сканирующий по поверхности и оплавляющий небольшие участки поверхностного слоя, которые после прекращения действия лазерного излучения быстро затвердевают благодаря интенсивному отводу тепла в массивную подложку . Для более эффективной аморфизации в состав обрабатываемого материала вводят аморфообразующие элементы. Технологическими недостатками лазерной аморфизации являются сложность оборудования, высокая стоимость и относительно невысокая скорость обработки больших поверхностей. К металлургическим недостаткам данного способа следует отнести высокие внутренние напряжения, формируемые на границе аморфизованного слоя и кристаллической матрицы, и, главное, высокая макро- и микронеоднородность структуры, обусловленная сканированием лазерного пучка по обрабатываемой поверхности.
Другим способом термической обработки как всего объема, так и поверхностных слоев материала, выбранным в качестве прототипа, является индукционный нагрев - нагрев токопроводящих тел путем возбуждения в них электрических токов переменным электромагнитным полем. Для создания последнего используются токи низкой (50 Гц), средней (до 10 кГц) и высокой (свыше 10 кГц) частоты. Применяется для плавления металлов, поверхностной закалки деталей и т.д.
Привлекательность индукционного нагрева в промышленности связана, прежде всего, с технологической простотой, высокой производительностью, высокой точностью поддержания режима термической обработки, высокой степенью экологичности, легкостью встраивания в автоматизированные технологические линии. В настоящее время разработано и изготавливается индукционное нагревательное оборудование для разнообразного применения в промышленности:
Для объемной и поверхностной термообработки металлических изделий с целью закалки, нормализации, улучшения, отжига, отпуска, химико-термической обработки;
Для нагрева металлических заготовок перед пластической деформацией;
Для нагрева поверхностей металлических изделий для специальных целей.
Мощность современных установок индукционного нагрева металла составляет десятки - сотни кВт, рабочие частоты - единицы кГц - единицы - МГц.
Сущность изобретения
Сущность изобретения состоит в использовании мощных коротких электрических импульсов для модификации поверхности электропроводящих объектов.
1. повышения эксплуатационных характеристик металлов и сплавов;
2. управления требуемыми свойствами, такими как твердость, износостойкость, усталость, коррозионная стойкость;
3. снижения себестоимости продукции;
предлагается способ модификации структуры поверхности путем формирования аморфных, нано- и микрокристаллических поверхностных слоев. В отличие от прототипа мы предлагаем использовать мощный одиночный импульс тока, приводящий к требуемому разогреву поверхности (скин-слоя).
Скин-эффект состоит в локализации высокочастотного электрического тока в тонком приповерхностном слое проводника . Толщина скин-слоя δ оценивается как:
где ω - частота переменного тока, μ - магнитная проницаемость и σ - проводимость проводника. При протекании импульса тока длительностью t 0 плотностью j по проводнику с удельным сопротивлением ρ=1/σ выделяется теплота q:
Эта теплота расходуется на увеличение внутренней энергии, а следовательно, и температуры поверхностного скин-слоя, поскольку длительность импульса короткая и изменениями структуры и оттоком тепла через внешнюю поверхность можно пренебречь. Приращение температуры ΔT за малый интервал времени t 0 пропорционально количеству теплоты q:
где c v - удельная теплоемкость и ρ m - плотность проводящего слоя.
Для оценок будем полагать, что форма импульса тока длительности t 0 близка к полупериоду синусоидальной функции с частотой ω. Тогда можно полагать:
Пусть ток I протекает по цилиндрическому образцу радиуса R 0 . Тогда площадь сечения S скин-слоя толщиной δ составит величину:
Тогда можно найти связь полного тока I и плотности тока j:
Подставляя (1, 2, 4-6) в (3), получаем оценку зависимости величины разогрева поверхности от амплитуды тока I и радиуса образца R 0:
Подставляя (4) в (1), получаем выражения для определения требуемой длительности электрического импульса для модификации поверхностного слоя толщиной δ:
Из (7) можно найти амплитуду тока, необходимую для разогрева поверхности образца радиуса R 0 на величину ΔT:
Таким образом, выражения (8, 9) позволяют оценить параметры импульса тока, необходимого для прогрева до температуры ΔT поверхностного слоя толщиной δ.
Время остывания t f поверхностного слоя определяется диффузией тепла внутрь образца и зависит от его толщины (δ) и коэффициента температуропроводности α.
где λ - коэффициент теплопроводности.
Важнейшей характеристикой обработки поверхности, определяющей, в частности, возникновение аморфного поверхностного слоя, является скорость ее охлаждения T:
Используя (8, 10), получаем:
Таким образом, как следует из полученных выражений, для достижения температуры плавления скин-слоя и получения высокой скорости его охлаждения требуются короткие, мощные импульсы тока. Оценки показывают, что для обработки образцов диаметром порядка миллиметров и получения скорости охлаждения порядка 10 10 К/с требуются импульсы тока амплитудой порядка 100 кА и длительностью в десятки наносекунд.
Требуемая структура и толщина модифицированного слоя могут регулироваться путем контроля величины перегрева расплава или температуры поверхностного слоя в случае, если плавление поверхности не являются желательными, и скорости охлаждения, которые, в свою очередь, определяются амплитудой, длительностью приложенного импульса тока и начальной температурой образца. Следовательно, предлагаемый способ реализует достоинства поверхностной термической обработки и скоростной закалки.
Реализация заявляемого способа зависит от технических возможностей получения коротких импульсов тока большой амплитуды. Основная проблема состоит в обеспечении высокой скорости вывода энергии из генератора в нагрузку. В настоящее время для лучших конденсаторов с энергоемкостью ˜10 4 Дж это время составляет ˜300 нс . Время вывода энергии из батареи определяется как параметрами самих конденсаторов, так и нагрузкой. Добавление внешней нагрузки приводит к неизбежному возрастанию индуктивности системы и увеличению времени вывода энергии до ˜1 мкс.
В настоящее время наибольшие скорости вывода энергии получают в двухкаскадных генераторах, включающих в себя первичный генератор импульса тока (ГИН) и систему увеличения мощности (СУМ). ГИН обычно представляет собой батарею импульсных конденсаторов, включаемых по той или иной схеме (например, схеме Маркса ) и запитываемых от источника высокого напряжения. Система увеличения мощности предназначена для существенного (в 10-100 раз) увеличения плотности энергии, поступающей с ГИНа для получения на нагрузке импульса тока длительностью ˜(10-100) нс. Существует два типа СУМ - на основе промежуточного емкостного накопителя или с использованием индуктивного накопителя . Плотность энергии в индуктивных накопителях в десятки раз выше, чем в емкостных. Однако они требуют использования сильноточных быстродействующих размыкателей тока, переключающих генератор на нагрузку, что представляет собой серьезную научно-техническую проблему.
Более просты в реализации СУМы на основе одиночной (или двойной) формирующей линии коаксиального типа, заполненных глицерином (относительная диэлектрическая проницаемость ε=44) или деионизованной водой (ε=81). В этих средах можно на время заряда получить достаточно высокое значение напряженности электрического поля, а следовательно (с учетом достаточно большого значения высокочастотной диэлектрической проницаемости ε), и высокую плотность энергии, что обеспечивает получение короткого и мощного электрического импульса.
Целью изобретения является модификации поверхности электропроводящих объектов.
Поставленная цель достигается тем, что в способе модификации токопроводящих тел путем возбуждения в них электрического тока переменным электромагнитным полем новым является то, что для модификации поверхности используются мощные одиночные импульсы тока наносекундного диапазона длительности.
Ввиду того что из уровня техники неизвестны способы модификации поверхности, основанные на использовании наносекундных мощных импульсов тока, оно соответствует критерию "новизна".
Ввиду того что заявляемое изобретение очевидным образом не следует из аналогов и прототипа, оно соответствует критерию "изобретательский уровень".
Как будет показано ниже, ввиду высокого расчетного значения скорости охлаждения и ожидаемой сравнительно низкой удельной стоимости, область промышленного применения заявляемого изобретения может быть весьма широкой. Соответственно заявляемое изобретение соответствует критерию "промышленная применимость".
Перечень фигур чертежей
На фиг.1 представлены результаты расчета прохождения импульса тока амплитудой 240 кА и длительностью 40 нс по медному цилиндрическому образцу диаметром 1 мм. Представлены графики зависимостей от времени силы тока - I, текущего через образец, температуры поверхности образца - Т, радиуса фазового перехода (плавления) - R m и скорости изменения температуры с момента плавления - dT/dt.
На фиг.2 показана микрофотография поверхности медного циллиндрического образца длиной 10 мм и диаметром 0,8 мм, обработанного импульсом тока по заявляемому способу. Изображение поверхности получено в сканирующем электронном микроскопе Hitachi S-3500.
На фиг.3 показаны микрофотографии одного и того же участка поверхности циллиндрического образца нитинола (NuTi) диаметром 1,0 мм, обработанного импульсом тока по заявляемому способу. На фиг.3a показана поверхность образца в исходном состоянии. а на фиг.3b - после обработки. изображение поверхности получено в сканирующем электронном микроскопе Hitachi S-3500.
Сведения, подтверждающие возможность осуществления изобретения.
Для поверхностной модификации металлов могут быть использованы генераторы импульсов токов (ГИТ) наносекундной 20...100 нс длительности и амплитудой тока ˜100 кА. Как правило, такие генераторы выполнены на основе одиночной (двойной) формирующих линий (ФЛ) коаксиального типа, заполненных глицерином или деионизованной водой. Применение данных линий в конструкциях ГИТ обусловлено следующими факторами :
1. Длительность импульса тока определяется электрической длиной ФЛ и легко может меняться за счет использования либо дополнительных отрезков ФЛ, либо ФЛ различной электрической длины.
2. Время нарастания импульса тока в генераторе существенно зависит от индуктивности разрядного контура, в основном определяемой закорачивающим разрядником и, в значительной мере, высотой последнего. При установке в линию многоканального закорачивающего разрядника с током через каждый канал ˜10 кА взамен одноканального можно уменьшить длительность фронта импульса тока.
3. В случае электрического пробоя в линии жидкий диэлектрик не теряет своих электропрочностных свойств и может быть использован в дальнейшем.
В качестве примера реализации приведем результаты расчетов, выполненных для медного цилиндра диаметром 1 мм, начальная температура Т 0 =300 К. Параметры импульса тока выбирались таким образом, чтобы обеспечить глубину оплавления ˜1÷10 мкм.
Получено, что для медного образца при амплитуде импульса тока I=240 кА и его длительности t 0 =40 нс толщина проплавленного слоя составила 9 мкм. Процесс разогрева длился ˜0,1 мкс, процесс остывания ˜1 мкс. Максимальный разогрев достиг 1953 К (при температуре плавления и испарения меди соответственно 1356 К и 2868 К). Максимальная скорость охлаждения составила величину T=1,8·10 11 К/с.
Результаты расчетов подтверждаются экспериментально, как показано на фиг.2 для медного образца диаметром 0,8 мм, и на фиг.3 для образца из нитилона диаметром 1 мм, которые были обработаны по заявляемому методу. Плавление поверхностного слоя очевидно.
Таким образом, на основе заявляемого способа возможна разработка промышленных установок, обеспечивающих термическую обработку поверхности изделий.
Источники информации
1. Surface Engineering, Euromat-99, Vol. 11, ed. H.Dimigen, Willey-VCH, Germany (2000) 539 р.
2. В.П.Алехин, В.А.Хоник, Структура и физические закономерности деформации аморфных сплавов. М.: Металлургия, 1992, 248с.
3. А.И.Манохин, Б.С.Митин, В.А.Васильев, А.В.Ревякин, Аморфные сплавы. М.: Металлургия, 1992, 160с.
4. E.M.Breinan, Phys.Today V.29 (1976) рр.45-51.
5. A.Inoue, Bulk Amorphous Alloys, Practical Characteristics and Applications, Trans.Tech.Pub., Swizerland(1999) 146p.
7. I.R.Pashby, S.Bames and B.G.Bryden, Surface hardening of steel using a high power diode laser. Journal of Materials Processing Technology, 139 (2003) pp.585-588.
8. G.W.Stachowiak and A.W.Batchelor, Surface hardening and deposition of coatings on metals by a mobile source of localized electrical resistive heating. Journal of Materials Processing Technology, 57 (1996) pp.288-297.
Способ модификации поверхности металлов относится к технологии финишной обработки поверхности металлических деталей и может найти применение в машиностроении, металлургии и т.д. Способ заключается в том, что проводят микролегирование поверхностного слоя магнитно-абразивной обработкой при скорости магнитно-абразивного резания не менее 500 м/мин, напряженности магнитного поля в рабочем зазоре между полюсами 0,4-0,7 Тл и величине этого зазора 2-5 мм. Магнитно-абразивную обработку поверхностного слоя металла проводят порошками, содержащими карбиды переходных металлов IV-VI групп Периодической системы. Способ позволяет в одной операции совместить механическую очистку и выглаживание поверхности с микролегированием поверхностного слоя переходными металлами, улучшающими коррозионную стойкость металлов. При обработке по предложенному способу в поверхностном слое всегда создаются сжимающие напряжения, улучшающие защитные свойства образующейся на нем оксидной пленки. 1 з.п. ф-лы.
Изобретение относится к технологии финишной обработки поверхности металлических деталей и может найти применение в машиностроении, металлургии и т. д. Известен способ лазерной обработки поверхности металлов, который заключается в расплавлении предварительно нанесенного различными способами слоя, необходимого для микролегирования элемента под действием лазерного излучения большой мощности, образования пересыщенного раствора элемента покрытия и металла подложки и последующего быстрого его затвердевания (De Damboronea J. Surface and Coat. Technol. - 1998. - 100-101, N1-3. С. 372-377). По другому методу после напыления тонкой пленки поверхность металла облучается пучком ионов высокой энергии. В процессе ионного перемешивания часть атомов распыляется, а другая внедряется в материал подложки, тем самым изменяя ее состав и структуру (Onate J.I., Alonso F., Garia A. Thin Solid Films - 1998.- 317, N1-2. С. 471-476). Наиболее близким по технической сущности является способ плазменной обработки металлов (заявка ЕР 0908535 ЕПВ, МПК 6 С 23 G 5/00, Н 01 J 37/34; - N97203/36.3), заключающийся в бомбардировке плазмой и положительными ионами поверхности металла. Описанный способ позволяет проводить травление, окисление металла, а также формировать пленки других продуктов взаимодействия с металлом подложки. Недостатком плазменной технологии является сложность необходимой для осуществления описанных способов аппаратуры - вакуумной установки с магнетронной системой формирования плазмы, которая требует высоковольтных источников тока большой мощности. Кроме того, при оплавлении поверхностного слоя металла вблизи модифицированного слоя возникают растягивающие напряжения, которые в случае нержавеющих сталей приводят к уменьшению усталостной прочности. В дополнение к этому перед обработкой необходимо проводить предварительную очистку поверхности обрабатываемого металла. Задачей предлагаемого изобретения является устранение этих недостатков. Поставленная задача решается тем, что по предлагаемому способу модификация поверхности включает микролегирование поверхностного слоя с помощью магнитно-абразивной обработки (МАО) металла в условиях, способствующих локальному повышению температуры в зоне обработки, а именно повышение магнитной индукции до 0,4-0,7 Тл, уменьшение ширины рабочего зазора между магнитными полюсами до 2-5 мм, повышение линейной скорости обработки до величины не менее 500 м/мин и отказ от применения смазывающе-охлаждающей жидкости (СОЖ). Одновременно в результате однородного режущего воздействия "щетки" из абразива в обработанном поверхностном слое металла возникают напряжения, которые в отличие от других видов абразивного шлифования и полирования жестко закрепленным абразивным зерном всегда являются сжимающими. Для осуществления модификации поверхности в состав абразива помимо всегда присутствующей ферромагнитной матрицы должны входить элементы, перенос которых в поверхностный слой при обработке металла способствует улучшению механических, химических и коррозионных свойств материала в целом. Для большинства конструкционных металлов благоприятным является микролегирование переходными металлами IV-VI группы Периодической системы с размером частиц от 5 до 630 мкм. Среди известных соединений переходных металлов наилучшим сочетанием химических и механических свойств обладают карбиды. Изобретение иллюстрируется следующими примерами: Пример 1. Трубки из сплава Zr - 1%Nb обрабатывают на установке МАО по а.с. X" 1216907 с помощью магнитно-абразивного порошка, содержащего дробленый колотый чугун (ДЧК) с фракцией 630-315 мкм без СОЖ. В отличие от обычного режима МАО по предлагаемому способу величину рабочего зазора уменьшают до 2 мм, а линейную скорость вращения магнитных полюсов повышают до 500 м/мин. Магнитная индукция в рабочем зазоре не меняется и составляет 0,4 Тл. Поверхность металла после МАО в таком режиме в отличие от обычной серебристо-матовой выглядит слегка загорелой. Уровень поверхностных микронапряжений повышается до 138,5 МПа по сравнению с исходным - 32,5 МПа. Толщина наклепанного слоя составляет не более 10 мкм, так как после фиксированного стравливания этого слоя микронапряжения снижаются до уровня исходного металла. С помощью лазерного микроанализатора в поверхностном слое металла после МАО обнаруживается повышение содержания железа от 17 до 27 мкг/см 2 . Образующийся модифицированный поверхностный слой заметно изменяет электрохимические и коррозионные свойства металла. При анодном оксидировании циркония после МАО возникает значительный инкубационный период, понижается скорость формовки оксидной пленки и повышается ее электронная проводимость. При коррозионных испытаниях в воде при 350 o С через 5000 час привес составляет 32,6 мг/дм 2 , сравнимый с привесом 35,3 мг/дм 2 для образцов после обычного травления во фтористоводородной ванне. На различия в способах обработки указывает только внешний вид коррозионной оксидной пленки: темная матовая после МАО и черная блестящая после травления. Пример 2 Пластины из сплава Zr - 2,5%Nb обрабатывают с помощью магнитно-абразивного порошка, содержащего 20% карбида титана и 9% кремния, с фракцией 630-315 мкм по следующему режиму: магнитная индукция в зазоре - 0,4 Тл, линейная скорость вращения магнитных полюсов - 500 м/мин; при длительности обработки 2 мин толщину зазора для различных образцов меняют от 5 до 2 мм. С уменьшением величины зазора поверхность пластины после обработки выглядит слегка загорелой. Величина электролитической емкости поверхности составляет 1,1 мкФ/см 2 вместо 8-10 мкФ/см 2 , типичной для поверхности сплава после электрополировки, что указывает на образование поверхностного слоя диэлектрической фазы. Содержание титана в поверхностном слое линейно повышается с уменьшением толщины зазора, что положительно сказывается на коррозионном поведении сплава. Пример 3 Пластины из сплава Zr - 1%Nb обрабатывают с помощью магнитно-абразивного порошка, содержащего 15% карбида тантала и 9% кремния, с фракцией 630-315 мкм по следующему режиму: магнитная индукция в зазоре - 0,7 Тл, линейная скорость вращения магнитных полюсов - 500 м/мин. При толщине зазора 2 мм за 1 мин обработки на поверхности металла образуется слой темно-желтого цвета, электролитическая емкость которого (1,0 мкФ/см 2) указывает на хорошие диэлектрические свойства. За 500 час испытаний в воде при 350 o С на поверхности сплава образуется темная матовая пленка с хорошими защитными свойствами. Пример 4 Пластины сплава Zr - 1%Nb обрабатывают с помощью магнитно-абразивного порошка, содержащего 5% карбида вольфрама и 5% карбида молибдена, с фракцией 315-250 мкм, по следующему режиму: магнитная индукция в зазоре - 0,7 Тл, линейная скорость вращения магнитных полюсов - 500 м/мин. При толщине зазора 2 мм за 1 мин обработки на поверхности сплава образуется слой темно-синего цвета, электролитическая емкость которого (1,5 мкФ/см 2) указывает на хорошие диэлектрические свойства. За 500 час испытаний в воде при 350 o С на поверхности сплава образуется темная матовая пленка с хорошими защитными свойствами. Как видно из приведенных примеров, при обработке поверхности металлов по предложенному способу в зоне обработки возникает короткоживущая "трибоплазма", в результате действия которой на поверхности возникают соединения, включающие элементы абразива, металла подложки и окружающей атмосферы, происходит микролегирование поверхностного слоя. В отличие от известных плазменных технологий для осуществления предложенного способа не требуется сложной вакуумной установки и высоковольтного источника тока. Применение обычной магнитно-абразивной оснастки позволяет в одной операции совместить механическую очистку и выглаживание поверхности с микролегированием поверхностного слоя переходными металлами, улучшающими коррозионное поведение металлов. При обработке по предложенному способу в поверхностном слое всегда создаются сжимающие напряжения, улучшающие защитные свойства образующейся на нем оксидной пленки.
Формула изобретения
1. Способ модификации поверхности металлов, заключающийся в микролегировании поверхностного слоя атомами металлов и окружающей атмосферы, отличающийся тем, что микролегирование поверхностного слоя проводят магнитно-абразивной обработкой металла при скорости магнитно-абразивного резания не менее 500 м/мин, напряженности магнитного поля в рабочем зазоре между полюсами 0,4-0,7 Тл и величине этого зазора 2-5 мм. 2. Способ по п. 1, отличающийся тем, что магнитно-абразивную обработку поверхности металлов проводят порошками, содержащими карбиды переходных металлов IV-VI групп периодической системы с размером частиц от 50 до 630 мкм.
Похожие патенты:
Изобретение относится к способам обработки поверхностей узлов трения и может быть использовано в различных отраслях машиностроения и на транспорте при ремонте и профилактике механического износа различного оборудования