Аустенитные нержавеющие стали их свойства и применение. Аустенит - это что такое? Фазовые превращения в аустенитных нержавеющих сталях
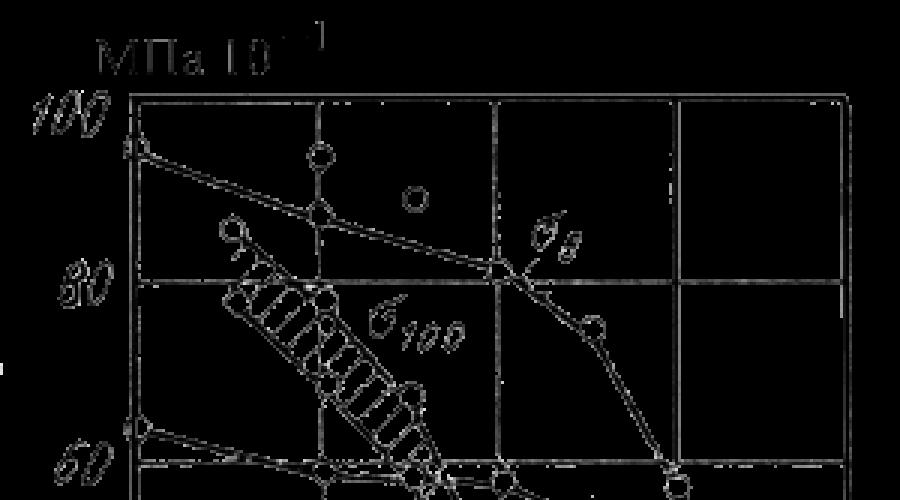
Читайте также
Аустенитые стали (см. табл. 1,2) применяют для изготовления деталей газовых турбин, клапанов двигателей, баков, труб и других деталей, работающих при температурах 500-700°С. Жаропрочные стали легированы хромом, никелем и являются одновременно коррозионностойкими.
Аустенитные стали подразделяют на неупрочняемые при термической обработке (нестареющие) и упрочняемые при термической обработке (стареющие) аустенитные стали.
К нестареющим аустенитным жаропрочным сталям относят стали типа 12Х18Н9Т, 12Х18Н10Т, 12Х18Н12Т.
Стареющие аустенитные стали обычно являются более сложнолегированными, например: 37Х12Н8Г8МФ5 (ЭИ481), 45Х14Н14В2М (ЭИ69) и т. п.
По способу упрочнения их подразделяют на аустенитные стали с карбидным упрочнением и аустенитные стали с интерметаллидным упрочнением.
В не упрочняемых аустенитных сталях хром вводится для придания ей коррозионной стойкости (на поверхности образуется плотная окисная пленка Cr O ), никель для получения аустенитной структуры, титан – для предотвращения межкристаллитной коррозии, которая нарушает связь между зернами и делает сталь непригодной к эксплуатации. Если в сталях нет титана (или ниобия), то в ней образуются карбиды хрома, которые при нагреве закаленной стали до 500-700°С выделяются по границам зерен, и устойчивость стали против коррозии падает. При введений титана образуются карбиды титана TiC, что исключает выделение карбидов хрома и возникновение межкристаллитной коррозии. Термическая обработка сталей заключается в нагреве до температур 1050-1100°С с последующим охлаждением в воде. Структура после закалки состоит из зерен аустенита с наличием двойников и небольшого количества карбидов TiC. Используется сталь для деталей выхлопных систем, труб, а также полуфабрикатов в виде листа и сортовой стали. Температура окалинообразования 850°С. Длительная жаропрочность стали при 600°С и выдержке 100000 ч составляет 110 МПа.
Химический состав сталей аустенитного класса с карбидным упрочнением 37Х12Н8Г8МФВ, 45Х14Н14В2М приведен в табл. 1.
Хром и молибден повышают температуру рекристаллизации и, следовательно, жаропрочность стали благодаря образованию карбидов и предохраняют сталь от окисления. Никель, расширяя -область, вводится для получения аустенитной структуры. Марганец применяется в качестве аустенитообразующего, для частичной замены никеля и увеличения устойчивости аустенита.
Ниобий и титан являются очень эффективными карбидообразователями. Содержание ниобия обычно небольшое (0,1-0,2%). Титан и ниобий используют для связывания углерода, как и в хромоникелевых нержавеющих сталях, во избежание межкристаллитной коррозии, а также для получения природного мелкого зерна.
Длительная жаропрочность при температуре испытаний 600°С и выдержке в течение 100 ч составляет 400 МПа. Структура стали после закалки с 1140°С в воде состоит из крупных зерен аустенита и небольшого количества карбидов: VС, NbC. Монокарбиды выделяются чаще всего по границам зерен в виде крупных включений неправильной формы.
Аустенитная сталь с карбидным упрочнителем 45Х14Н14В2М имеет в структуре от 2-2,6% вольфрама. Вольфрам так же, как титан и ниобий, в нержавеющих сталях предотвращает интерметаллидную коррозию. Поведение остальных элементов аналогично предыдущей стали. Структура стали после отжига при 820°С состоит из мелких зерен аустенита и большого количества карбидов. Температура закалки стали составляет 1175°С. Чем выше температура закалки, тем сталь становится более жаропрочной, но менее пластичной и вязкой. Это, по-видимому, объясняется более полным растворением карбидов в аустените, большей его устойчивостью, а также крупнозернистой структурой. После закалки в воде структура стали состоит из крупных зерен аустенита и небольшого количества карбидов. В авиадвигателестроении сталь применяется для изготовления выхлопных клапанов поршневых двигателей, лопаток компрессора последних ступеней реактивных двигателей, деталей трубопроводов.
Жаропрочные стали с интерметаллидным упрочнителем (10Х11Н20Т3Р, 10Х11Н23Т3МР) (см.табл. 1,2). Для повышения жаропрочности их легируют хромом, молибденом, вольфрамом с добавками алюминия, титана или ниобия и тантала. Титан и алюминий образуют основную упрочняющую g¢-фазу (Ni Ti или Ni TiAl). Молибден легирует твердый раствор, повышая энергию межатомной связи. Бор упрочняет границы зерен аустенита. Упрочняющая термообработка этих сталей состоит из закалки и старения (см. табл. 2). Стали используются для изготовления камер сгорания, дисков и лопаток турбин, а также сварных конструкций, работающих при температурах до 700°С.
Аустенитные стали отличаются большой пластичностью, хорошо свариваются, однако по сравнению с перлитными сталями труднее обрабатываются давлением и резанием.
Жаропрочные сплавы на железоникелевой основе (ХН35ВТ, ХН35ВТЮ и др.) дополнительно легированы хромом, титаном, вольфрамом, алюминием, бором; упрочняются закалкой и старением. Их применяют для изготовления турбинных лопаток и дисков, колец соплового аппарата и других деталей, работающих при температурах до 750°С.
Аустенитные стали имеют ряд особых преимуществ и могут применяться в рабочих средах, отличающихся значительной агрессивностью. Без таких сплавов не обойтись в энергетическом машиностроении, на предприятиях нефтяной и химической промышленности.
Аустенитные стали - это стали с высоким уровнем легирования, при кристаллизации образуется однофазная система, характеризуемая кристаллической гранецентрированной решеткой. Такой тип решеток не меняется даже под воздействием очень низких температур (около 200 градусов Цельсия). В отдельных случаях имеется еще одна фаза (объем в сплаве не превышает 10 процентов). Тогда решетка получится объемноцентрированной.
Описание и характеристики
Стали разделяют на две группы относительно состава их основы и содержания легирующих элементов, таких как никель и хром:
- Композиции, в основе которых содержится железо: никель 7%, хром 15%; общее количество добавок - до 55%;
- Никелевые и железоникелевые композиции. В первой группе содержание никеля начинается от 55% и больше, а во второй - от 65 и больше процентов железа и никеля в соотношении 1:5.
Благодаря никелю можно добиться повышенной пластичности, жаропрочности и технологичности стали, а с помощью хрома - придать требуемую коррозийность и жаростойкость. А добавление других легирующих компонентов позволит получать сплавы с уникальными свойствами. Компоненты подбирают в соответствии со служебным предназначением сплавов.
Для легирования преимущественно используют:
- Ферритизаторы, стабилизирующие структуру аустенитов: ванадий, вольфрам, титан, кремний, ниобий, молибден.
- Аустенизаторы, представленные азотом, углеродом и марганцем.
Все перечисленные компоненты расположены не только в избыточных фазах, но и в твердом растворе из стали.
Сплавы, устойчивые к коррозии и перепадам температур
Широкий спектр добавок позволяет создать особые стали, которые будут применены для изготовления компонентов конструкций и будут работать в криогенных, высокотемпературных и коррозионных условиях. Поэтому составы разделяют на три типа:
- Жаропрочные и жаростойкие.
- Стойкие к коррозии.
- Устойчивы к воздействию низких температур.
Жаростойкие сплавы не разрушаются под влиянием химикатов в агрессивных средах, могут использоваться при температуре до +1150 градусов. Из них изготавливают:
- Элементы газопроводов;
- Арматуру для печей;
- Нагревательные компоненты.
Жаропрочные марки на протяжении длительного времени могут оказывать сопротивление нагрузкам в условиях повышенных температур, не теряя высоких механических характеристик. При легировании используются молибден и вольфрам (на каждое дополнение может отводиться до 7%). Для измельчения зерен в небольших количествах применяется бор.
Аустенитные нержавеющие стали (стойкие к коррозии) характеризуются незначительным содержанием углерода (не более 0,12%), никеля (8−30%), хрома (до 18%). Проводится термическая обработка (отпуск, закалка, отжиг). Она важна для изделий из нержавейки, ведь дает возможность хорошо держаться в самых разных агрессивных средах - кислотных, газовых, щелочных, жидкометаллических при температуре 20 градусов и выше.
У хладостойких аустенитных композициях содержится 8−25% никеля и 17−25% хрома. Применяют в криогенных агрегатах, но стоимость производства существенно возрастает, потому используются очень ограниченно.
Свойства термической обработки
Жаростойкие и жаропрочные марки могут подвергаться разным типам тепловой обработки, чтобы нарастить полезные свойства и модифицировать уже имеющуюся структуру зерен. Речь идет о числе и принципе распределения дисперсных фаз, величине блоков и собственно зерен и тому подобное.
Отжиг такой стали помогает уменьшить твердость сплава (иногда это важно при эксплуатации), а также устранить излишнюю хрупкость. В процессе обработки металл нагревается до 1200 градусов на протяжении 30−150 минут, потом его необходимо как можно быстрее охладить. Сплавы со значительным количеством легирующих элементов, как правило, охлаждаются в маслах или на открытом воздухе, а более простые - в обычной воде.
Нередко проводится двойная закалка. Сначала выполняют первую нормализацию составов при температуре 1200 градусов, затем следует вторая нормализация при 1100 градусах, что позволяет значительно увеличить пластические и жаропрочные показатели.
Добиться повышения жаропрочности и механической прочности можно в процессе двойной термической обработки (закалка и старение). До эксплуатации проводится искусственное старение всех жаропрочных сплавов (то есть выполняется их дисперсионное твердение).
Существующие аустенитные высоколегированные стали и сплавы различают по содержанию основных легирующих элементов – хрома и никеля и по составу основы сплава. Высоколегированными аустенитными сталями считают сплавы на основе железа, легированные различными элементами в количестве до 55%, в которых содержание основных легирующих элементов – хрома и никеля обычно не выше 15 и 7% соответственно. К аустенитным сплавам относят железоникелевые сплавы с содержанием железа и никеля более 65% при отношении никеля к железу 1:1,5 и никелевые сплавы с содержанием никеля не менее 55%.
Аустенитные стали и сплавы классифицируют
- по системе легирования,
- структурному классу,
- свойствам
- и служебному назначению.
Высоколегированные стали и сплавы являются важнейшими материалами, широко применяемыми в химическом, нефтяном, энергетическом машиностроении и других отраслях промышленности для изготовления конструкций, работающих в широком диапазоне температур. Благодаря высоким механическим свойствам при отрицательных температурах высоколегированные стали и сплавы применяют в ряде случаев и как хладостойкие. Соответствующий подбор легирующих элементов определяет свойства и основное служебное назначение этих сталей и сплавов (табл. 1 – 3).
Характерным отличием коррозионно-стойких сталей является пониженное содержание углерода (не более 0,12%). При соответствующем легировании и термической обработке стали обладают высокой коррозионной стойкостью при 20°С и повышенной температуре как в газовой среде, так и в водных растворах кислот, щелочей и в жидкометаллических средах.
К жаропрочным относятся стали и сплавы, обладающие высокими механическими свойствами при повышенных температурах и способностью выдерживать нагрузки при нагреве в течение длительного времени. Для придания этих свойств стали и сплавы легируют элементами-упрочнителями – молибденом и вольфрамом (до 7% каждого). Важной легирующей присадкой, вводимой в некоторые стали и сплавы, является бор, способствующий измельчению зерна.
Жаростойкие стали и сплавы обладают стойкостью против химического разрушения поверхности в газовых средах при температурах до 1100 – 1150°С. Обычно их используют для слабонагруженных деталей (нагревательные элементы, печная арматура, газопроводные системы и т. д.). Высокая окалиностойкость этих сталей и сплавов достигается легированием алюминием (до 2,5%) и кремнием, способствующими созданию прочных и плотных окислов на поверхности деталей, предохраняющих металл от контакта с газовой средой.
По системе легирования аустенитные стали делятся на два основных типа: хромоникелевые и хромомарганцевые. Существуют также хромоникельмолибденовые и хромоникельмарганцевые стали.
В зависимости от основной структуры, получаемой при охлаждении на воздухе, различают следующие классы аустенитных сталей: аустенитно-мартенситные, аустенитно-ферритные, аустенитные.
Сплавы на железоникелевой (при содержании никеля более 30%) и никелевой основах по структуре являются стабильноаустенитными и не имеют структурных превращений при охлаждении на воздухе. В настоящее время находят применение также аустенитно-боридные Х15Н15М2БР1 (ЭП380), Х25Н20С2Р1 (ЭП532), ХН77СР1 (ЭП615) и высокохромистые аустенитные ХН35ВЮ (ЭП568), ХН50 (ЭП668) стали и сплавы, основная структура которых содержит аустенит и боридную или хромоникелевую эвтектические фазы соответственно.
После соответствующей термической обработки высоколегированные стали и сплавы обладают высокими прочностными и пластическими свойствами (табл. 4). В отличие от углеродистых эти стали при закалке приобретают повышенные пластические свойства. Структуры высоколегированных сталей разнообразны и зависят не только от их состава, но и от режимов термической обработки, степени пластической деформации и других факторов.
Положение фазовых областей на диаграммах состояния определено в основном в виде псевдобинарных разрезов систем железо – хром – никель или железо–хром–марганец (рис. 1). Железохромоникелевые сплавы непосредственно после затвердевания имеют твердые растворы видов α и γ и гетерогенную область смешанных твердых растворов α + γ . Устойчивость аустенита определяется близостью состава к границе α - и γ -области. Неустойчивость может проявляться при нагреве до умеренных температур и последующем охлаждении, когда фиксированная быстрым охлаждением аустенитная структура частично переходит в мартенситную. Увеличение содержания никеля в этих сплавах способствует понижению температуры γ → α (М) -превращения (рис. 2).
Рис. 1. Вертикальные разрезы диаграмм состояния железо–хром–никель (а) и железо–хром–марганец (б)
Рис. 2. Изменения температуры мартенситного превращения железохромоникелевых сплавов в зависимости от легирования
Неустойчивость проявляется при холодной деформации, когда стали типа 18-8 в зависимости от степени деформации изменяют свои магнитные и механические свойства (рис. 3). Кроме того, неустойчивость аустенитных сталей может вызываться выделением карбидов из твердого раствора при изменении температуры, сопровождающимся изменением концентрации углерода и хрома. Это вызывает нарушение равновесного состояния и превращение аустенита в феррит и мартенсит преимущественно по границам зерен, где наблюдается наибольшее обеднение хромом и углеродом твердого раствора.
Рис. 3. Изменение механических свойств хромоникелевой стали (18% Cr, 8% Ni, 0,17% С) в зависимости от степени холодной деформации (обжатия)
В тройной системе железохромомарганцовистых сплавов после затвердевания образуется непрерывный ряд твердых растворов с γ -решеткой и в процессе дальнейшего охлаждения в зависимости от состава сплава происходят различные аллотропические превращения. Марганец относится к элементам, расширяющим γ - область, и в этом отношении аналогичен никелю. При достаточной концентрации марганца (>15%) и хрома (<15%) сталь может иметь однофазную аустенитную структуру. Сопоставление фазовых диаграмм систем железо – хром – никель и железо – хром – марганец при высоких температурах и 20°С показывает, что аустенитная фаза в системе с никелем имеет значигельно большую площадь.
При кристаллизации хромоникелевых сталей из расплава начинают вначале выпадать кристаллы хромоникелевого феррита, имеющего решетку δ-железа (рис. 4). По мере охлаждения в δ-феррите образуются кристаллы хромоникелевого аустенита, имеющего решетку γ -железа, и сталь приобретает аустенитную структуру. Углерод в аустенитно-ферритной и аустенитной сталях при температурах выше лини SE находится в твердом растворе и в виде фаз внедрения. Медленное охлаждение стали ниже линии SE приводит к выделению углерода из твердого раствора в виде химического соединения – карбидов хрома типа Cr 23 C 6 располагающихся преимущественно по границам зерен. Дальнейшее охлаждение ниже линии SK способствует выпадению по границам зерен вторичного феррита. Таким образом, сталь при медленном охлаждении до 20°С имеет устенитную структуру со вторичными карбидами и ферритом.
Рис. 4. Псевдобинарная диаграмма состояния в зависимости от содержания углерода для сплава 18% Cr, 8% Ni, 74% Fe
При быстром охлаждении (закалке) распад твердого раствора не успевает произойти, и аустенит фиксируется в пересыщенном и неустойчивом состояниях.
Количество выпавших карбидов хрома зависит не только от скорости охлаждения, но и от количества углерода в стали. При его содержании менее 0,02 – 0,03%, т. е. ниже предела его растворимости в аустените, весь углерод остается в твердом растворе. В некоторых композициях аустенитных сталей ускоренное охлаждение может привести к фиксации в структуре первичного δ-феррита, предупреждающего горячие трещины.
Изменение в стали содержания легирующих элементов влияет на положение фазовых областей. Хром, титан, ниобий, молибден, вольфрам, кремний, ванадий, являясь ферритизаторами, способствуют появлению в структуре стали ферритной составляющей. Никель, углерод, марганец и азот сохраняют аустенитную структуру. Однако основными легирующими элементами в рассматриваемых сталях являются хром и никель. В зависимости от их соотношения стали иногда разделяют на стали с малым (%Ni/%Cr)≤1 и большим (%Ni/%Cr)>1 запасом аустенитности.
В аустенитных хромоникелевых сталях, легированных титаном и ниобием, образуются не только карбиды хрома, но и карбиды титана и ниобия. При содержании титана Ti > [(%C–0,02)*5] или ниобия Nb > (%С*10) весь свободный углерод (выше предела его растворимости в аустените) может выделиться в виде карбидов титана или ниобия, а аустенитная сталь становится не склонной к межкристаллитной коррозии. Выпадение карбидов повышает прочностные и понижает пластические свойства сталей. Это свойство карбидов используют для карбидного упрочнения жаропрочных сталей, проводимого в комплексе с интерметаллидным упрочнением частицами Ni 3 Ti; Ni 3 (Al, Ti), Fe 2 W, (N, Fe) 2 Ti и др. К интерметаллидным соединениям относят и σ-фазу, которая образуется в хромоникелевых сталях при длительном нагреве или медленном охлаждении при температурах ниже 900 – 950°С. Она обладает ограниченной растворимостью в α - и γ -твердых растворах и, выделяясь преимущественно по границам зерен, упрочняет сплав и одновременно резко снижает пластические свойства и ударную вязкость металла. Повышенные концентрации в стали хрома (16–25%) и элементов-ферритизаторов (молибдена, кремния и др.) способствуют образованию σ-фазы при 700 – 850°С. Выделение этой фазы происходит преимущественно с образованием промежуточной фазы феррита (γ →α→ σ ) или преобразования δ-феррита (δ→ σ ). Однако возможно ее выделение и непосредственно из твердого раствора (γ → σ ).
В хромомарганцовистых сталях с высоким содержанием хрома и марганца при замедленном охлаждении также наблюдается выделение σ -фазы. Углерод в хромомарганцовистых и хромомарганцевоникелевых сталях приводит к дисперсионному твердению сталей после соответствующей термической обработки, особенно при совместном легировании с карбидообразующими элементами (ванадием, ниобием и вольфрамом).
Упрочнение аустенитно-боридных сталей происходит в основном за счет образования боридов железа, хрома, ниобия, углерода, молибдена и вольфрама. В соответствии с этими процессами аустенитные стали подразделяют в зависимости от вида упрочнения на карбидные, боридные и с интерметаллидным упрочнением. Однако в большинстве случаев в связи с содержанием в сталях и сплавах большого количества различных легирующих элементов их упрочнение происходит за счет комплексного влияния дисперсных фаз и интерметаллидных включений.
Таблица 1. Состав некоторых коррозионно-стойких аустенитных сталей и сплавов, %
Таблица 2. Состав некоторых жаропрочных аустенитных сталей и сплавов, %
Таблица 3. Состав некоторых жаростойких аустенитных сталей и сплавов, %
Таблица 4. Типовые механические свойства некоторых марок высоколегированных аустенитных и аустенитно-ферритных сталей и сплавов
Аустенит — это твердый однофазный раствор углерода до 2 % в y-Fe. Главная его особенность заключается в последовательности, в которой располагаются атомы, т. е. в строении кристаллической решетки. Она бывает 2 типов:
- ОЦК a-железо (объемно - центрированная - по одному атому располагается в 8-ми вершинах куба и 1 в центре).
- ГЦК y-железо (гране-центрированная по одному атому находится в 8-ми вершинах куба и по одному находятся на каждой из 8-ми граней, всего 16 атомов).
Простыми словами: аустенит — это структура или состояние металла, определяющая его технические характеристики, которые получить в другом состоянии невозможно, т.к. меняя строение, металл изменяет и свойства. Без аустенита невозможна такая технология как закалка, которая является самой распространенной, дешевой, технически доступной, а в некоторых случаях и единственной технологией упрочнения металла.
Свойства аустенитных сталей и где их используют
Само состояние железа в Y-фазе (аустенит) уникально, благодаря ему металл является жаропрочным (+850 ºC), холодостойким (-100 ºC и ниже t), способен обеспечивать коррозионную и электрохимическая стойкость и другие важнейшие свойства, без которых были бы немыслимы многие технологические процессы в:
- нефтеперерабатывающей и химической отраслях;
- медицине;
- космическом и авиастроении;
- электротехнике.
Жаропрочность — свойство стали не менять своих технических свойств при критических температурах с течением времени. Разрушение происходит при неспособности металла противостоять дислокационной ползучести, т. е. смещению атомов на молекулярном уровне. Постепенно происходит разупрочнение, и процесс старения металла начинает происходить все быстрее. Это происходит с течением времени при низких или высоких температурах. Так вот, насколько этот процесс растянется во времени — это и есть способность металла к жаропрочности.
Коррозионная стойкость — способность металла противостоять разрушению (дислокационной ползучести) не только с течением времени и при криогенных и высоких температурах, но еще и в агрессивных средах, т. е. при взаимодействии с веществами активно вступающих в реакцию с одним или несколькими компонентных элементов. Разделяют 2 типа коррозии:
- химическая — окисление металла в таких средах, как газовая, водная, воздушная;
- электрохимическая — растворение металла в кислотных средах, имеющих положительно или отрицательно заряженные ионы. При разности потенциалов между металлом и электролитом, происходит неизбежная поляризация, приводящая к частичному взаимодействию двух веществ.
Холодостойкость — способность сохранять структуру при криогенных температурах с течением длительного времени. Из-за искажения кристаллической решетки структура стали холодостойкой способна принимать строение присущее обычным малолегированным сталям, но уже при очень низких температурах. Но этим сталям присущ один недостаток — иметь полноценные свойства они могут только при минусовых температурных значениях, t - ≥ 0 для них недопустимы.
Методы получения аустенита
Аустенит — это структура металла, которая в малолегированных марках возникает в диапазоне температур 550-743 ºC. Как можно сохранить эту структуру и, соответственно, свойства за границами этих t? — Ответ: методом легирования. При наполнении решетки аустенита атомами других элементов, образуются структурные искажения, а процесс восстановления ОЦК-решетки (естественное строение при нормальных температурах) сдвигается на сотни градусов.
Как эти свойства проявляются и в каком состоянии, зависит от добавочных т. е. легирующих элементов и термической обработки детали, которую она может дополнительно получать. Причем влияют не только элементы, но их соотношение, так аустенитная сталь подразделяется на:
- хромомарганцевую и хромникельмарганцевую (07Х21Г7AН5, 10X14AГ15, 10X14Г14H4T);
- хромоникелевую (08Х18Н12Б, 03Х18Н11, 08X18H10T, 06X18Н11, 12X18H10T, 08X18H10;
- высококремнистую (02Х8Н22С6, 15Х18Н12C4Т10);
- хромоникельмолибденовую (03Х21Н21М4ГБ, 08Х17Н15М3Т, 08X17Н13M2T, 03X16H15M3, 10Х17Н13М3Т).
Химические элементы и их влияние на аустенит
Пособников у аустенита немного, использоваться они могут как совместно, так и частично, в зависимости от того какие свойства нужно получить:
- Хром — при его содержании более 13 % на поверхности образует оксидную пленку, толщиной 2-3 атома, которая исключает коррозию. В аустените хром находится свободном состоянии, при условии минимального содержания углерода, так как тот сразу образует карбид Cr 23 C 6 , что приводит к сегрегации хрома и обедняет большие участки матрицы, делая ее доступной для окисления, сам карбид Cr 23 C 6 способствует межкристаллитной коррозии аустенита.
- Углерод (максимальное его значение не более 10 %). Углерод в аустените находится в соединенном состоянии, основная его задача — образование карбидов, которые обладают предельной прочностью.
- Никель — основной элемент, который стабилизирует желаемую структуру. Достаточно содержание 9-12 %, чтобы перевести сталь в аустенитный класс. Измельчает и сдерживает рост зерна, что обеспечивает высокую пластичность;
- Азот заменяет атомы углерода, присутствие которых в сталях электрохимически стойких снижено до 0,02 %;
- Бор — уже в тысячных процентах увеличивает пластичность, в аустените, измельчая его зерно;
- Кремний и марганец не указываются как основные легирующие элементы в маркировке, но они являются основными или обязательными легирующими элементами аустенита, которые придают прочность и стабилизируют структуру.
- Титан и ниобий — при температуре выше 700 °С карбид хрома распадается и образуется стойкий TiC и NiC, который не вызывает межкристаллитную коррозию, но их использование не всегда оправданно холодостойких сталях, т.к. оно повышает границу распада аустенита.
Термическая обработка
Аустенит подвергают обработке только по необходимости. Основные операции это высокотемпературный отжиг (1100-1200 °С в течение 0,5-2,5 часа) при котором устраняется хрупкость. Далее закалка с охлаждением в масле или на воздухе.
Аустенитную сталь, легированную алюминием, подвергают двойной закалке и двойной нормализации:
- при t 1200 °С;
- при t 1100 °C.
Механическая окончательная обработка проводится до закалки, но после отжига.
Изделия из аустнитных сталей
Полуфабрикаты, в которых поставляется сталь, представляет собой:
- Листы, толщиной 4-50 мм с гарантированным химическим составом и механическими свойствами.
- Поковки. Ввиду сложной обработки этих сталей методом сварки, изготовление некоторых деталей представляет собой получение практически готовых изделий уже на этапе литья. Это роторы, диски, турбины, трубы двигателей.
Методы соединения аустенита:
- Припой - очень сильно ограничивает использование металла при t более 250 °С;
- Сваривание - возможно в защитной атмосфере (газовой, флюсовой), при последующей термической обработке.
- Механическое соединение - болты и другие крепежные элементы, изготовленные из аналогичного материала.
Аустенитные стали одни из самых дорогих технических сталей, использование которых ограничивается узкой специализацией оборудования.
9.1. СОСТАВ И СВОЙСТВА СТАЛЕЙ
Высоколегированные аустенитные стали имеют повышенное содержание основных легирующих элементов - хрома и никеля (обычно не ниже 16 и 7 % соответственно), придающих им соответствующую структуру и необходимые свойства (табл. 9.1). Для сокращения высоколегированные стали можно обозначать в соответствии с содержанием основных легирующих элементов цифрами, например 18-8, 25-20 и др. Первая цифра обозначает содержание хрома, вторая - никеля.
Никель - дефицитный и дорогой легирующий элемент и поэтому в тех случаях, когда условия работы конструкции позволяют, используют стали с пониженным его содержанием или безникелевые хромистые стали. В сплавах на железоникелевой основе содержание никеля еще выше, чем в хромоникелевых сталях. В никелевых сплавах никель служит основой, а железо - легирующей присадкой. Эти сплавы благодаря своим свойствам находят применение в ответственных конструкциях, работающих в сложных и специфических условиях.
Высоколегированные стали и сплавы по сравнению с менее легированными обладают высокой хладостойкостью, жаропрочностью, коррозионной стойкостью и жаростойкостью. Эти важнейшие материалы для химического, нефтяного, энергетического машиностроения и ряда других отраслей промышленности используют при изготовлении конструкций, работающих в широком диапазоне температур: от отрицательных до положительных. Несмотря на общие высокие свойства высоколегированных сталей, соответствующий подбор состава легирования определяет их основное служебное назначение. В соответствии с этим их можно разделить на три группы: коррозионно-стойкие, жаропрочные и жаростойкие (окалиностойкие). Благодаря их высоким механическим свойствам при отрицательных температурах высоколегированные стали и сплавы применяют в ряде случаев и как хладостойкие.
9.1. Состав некоторых марок высоколегированных аустенитных и
аустенитно-ферритных сталей и сплавов по ГОСТ 5632-72 (в ред. 1989 г.),
применяемых для изготовления сварных конструкции, %
Коррозионно-стойкие стали при соответствующем легировании и термообработке обладают высокой коррозионной стойкостью при комнатных и повышенных до 800 °С температурах как в атмосферной и газовой среде, так и в чистых и водных растворах кислот и щелочей, жидко-металлических средах и т.д. Характерное отличие этих сталей - пониженное содержание углерода, обычно не превышающее 0,12 %, оказывающее решающее влияние на стойкость их к межкристаллитной коррозии (МКК). Благодаря этим свойствам их используют при изготовлении трубопроводов и аппаратов для химической и нефтяной промышленности.
Жаропрочные стали и сплавы обладают высокими механическими свойствами при повышенных температурах и способностью сохранять их в данных условиях в течение длительного времени. Для придания этих свойств сталям и сплавам их обычно легируют элементами-упрочни-телями молибденом и вольфрамом (до 7 % каждого). Важной легирующей присадкой, вводимой в некоторые стали и сплавы, является бор. В ряде случаев к этим металлам предъявляется требование и высокой жаростойкости.
Одна из основных областей применения этих сталей - энергетическое машиностроение (трубопроводы, детали и корпуса газовых и паровых турбин и т.д.), где рабочие температуры достигают 750 °С и выше. Жаростойкие стали и сплавы обладают стойкостью против химического разрушения поверхности в газовых средах при температурах до 1100 ... 1150 °С. Обычно их используют для деталей слабонагруженных (нагревательные элементы, печная арматура, газопроводные системы и т.д.). Высокая окалиностойкость этих сталей и сплавов достигается легированием их алюминием (до 2,5 %) и вольфрамом (до 7 %). Эти легирующие элементы и кремний способствуют созданию прочных и плотных оксидов на поверхности деталей, предохраняющих металл от непосредственного контакта с газовой средой.
После соответствующей термообработки высоколегированные стали и сплавы обладают высокими прочностными и пластическими свойствами (табл. 9.2). В отличие от углеродистых при закалке эти стали приобретают повышенные пластические свойства. Структуры высоколегированных сталей очень разнообразны и зависят в основном от их химического состава, т.е. содержания основных элементов: хрома (ферритизатора) и никеля (аустенитизатора). На структуру влияет также содержание и других легирующих элементов-ферритизаторов (Si, Mo, Ti, Al, Nb, W, V) и аустенитизаторов (С, Co, Ni, Cu, Nb, B).
СОСТАВ И СВОЙСТВА СТАЛЕЙ
9.2. Механические свойства некоторых марок
высоколегированных аустенитных и аустенитно-ферритных сталей и сплавов
ТЕХНОЛОГИЯ СВАРКИ АУСТЕНИТНЫХ СТАЛЕЙ
Для приближенного определения характера структуры обычно пользуются диаграммой Шеффлера, предварительно подсчитав эквивалентные содержания никеля и хрома. На структуру этих сталей оказывает влияние также термообработка, пластическая деформация и другие факторы. Поэтому положение фазовых областей на диаграммах состояния определено в виде псевдобинарных разрезов тройных систем, обычно Fe-Cr-Ni с углеродом.
Рассмотрим фазовые области для одной из таких систем (штриховая линия на рис. 9.1) при содержании 0,05 % С. При очень медленном охлаждении и затвердевании (точка / на линии ликвидус) из расплава вначале начинают выпадать кристаллы хромоникелевого феррита, имеющего решетку 6-железа, а по мере охлаждения - и кристаллы хромоникелевого аустенита, имеющего решетку γ-железа. После затвердевания всего расплава (температура ниже точки 2 на линии солидус) сталь имеет аусте-нитно-ферритную структуру. При дальнейшем охлаждении в точке 3 происходит превращение δ → γ , и сталь приобретает аустенитную структуру.
Рис. 9.1. Псевдобинарная диаграмма состояния в зависимости от содержания углерода для сплава 18 % Сг, 8 % Ni, 74 % Fe
СОСТАВ И СВОЙСТВА СТАЛЕЙ
Углерод в аустенитно-ферритной и аустенитной сталях при температурах выше линии SE (выше точки 4) находится в твердом растворе в виде фаз внедрения. Медленное охлаждение стали ниже точки 4 приводит к выделению углерода из твердого раствора в виде химического соединения - карбидов хрома типа Сr 23 С 6 , располагающихся преимущественно по границам зерен. Дальнейшее охлаждение ниже точки 5 способствует выпадению по границам зерен вторичного феррита. Таким образом, сталь при медленном охлаждении при комнатной температуре имеет аустенитную структуру со вторичными карбидами и ферритом.
В зависимости от скорости охлаждения с температур, лежащих выше линии SE, углерод частично или полностью выделяется из твердого раствора в виде карбидов. Этот процесс оказывает решающее влияние на свойства сталей. При быстром охлаждении (закалке) распад твердого раствора не успевает произойти, и аустенит фиксируется в пересыщенном и неустойчивом состоянии. Количество выпавших карбидов хрома, помимо скорости охлаждения, зависит и от количества углерода в стали. При его содержании менее 0,02 ... 0,03 %, т.е. ниже предела его растворимости в аустените, весь углерод остается в твердом растворе.
Ускоренное охлаждение стали в некоторых композициях ау-стенитных сталей может привести к фиксации в их структуре первичного 5-феррита, в некоторых случаях необходимого с точки зрения предупреждения горячих трещин. Холодная деформация, в том числе и наклеп закаленной стали, в которой аустенит зафиксирован в неустойчивом состоянии, способствует превращению γ → α. Феррит, располагаясь тонкими прослойками по границам аустенитных зерен, блокирует плоскости скольжения и упрочняет сталь (рис. 9.2). Упрочнение стали тем выше, чем ниже температура деформации. Обычно тонколистовые хромонике-левые стали в состоянии поставки имеют повышенные прочностные и пониженные пластические свойства. Это объясняется их повышенной деформацией при прокатке и пониженной температурой окончания прокатки.
Если сталь, в которой не произошло выпадения карбидов и углерод зафиксирован в твердом растворе, медленно нагревать, подвижность атомов увеличивается. В соответствии с этим увеличивается и способность их к диффузии и восстановлению равновесия в твердом растворе, в котором аустенит зафиксирован в перенасыщенном и неустойчивом состоянии, что приводит к образованию и выделению карбидов из перенасыщенного твердого раствора. Этот процесс начинается при температуре 400 ... 500 °С, но вследствие малой скорости диффузии идет медленно с образованием карбидов преимущественно по границам зерен.
ТЕХНОЛОГИЯ СВАРКИ АУСТЕНИТНЫХ СТАЛЕЙ
Рис. 9.2. Изменение механических свойств
хромоникелевой стали (18 % Сг; 8 % Ni; 0,17 % С)
в зависимости от степени холодной деформации (обжатия)
Вследствие того что скорость диффузии хрома значительно ниже, чем углерода, связываемый в карбид хром извлекается из ближайших к границе областей зерна, т.е. происходит местное обеднение твердого раствора хромом. При работе в коррозионной среде эти участки зерна растворяются, что приводит к нарушению связи между отдельными зернами. Этот процесс называется межкристаллитной коррозией (МКК).
При температурах 600 ... 700 °С скорость диффузии более высокая и образование карбидов идет быстрее, в большем количестве и более крупных. При температуре 800 ... 900 °С карбиды образуются еще быстрее и коагулируют. Ввиду достаточно высокой скорости диффузии хром, связываемый в карбид, извлекается из более глубоких областей зерна, и местное обеднение границ зерна хромом уменьшается. При температурах выше 900 °С (выше температур линии SE) наряду с коагуляцией карбидов начинается обратный процесс их растворения с переходом углерода в твердый раствор и образованием однородной массы аустенита. Быстрое охлаждение этой стали (закалка) опять фиксирует структуру аустенита в
СОСТАВ И СВОЙСТВА СТАЛЕЙ
перенасыщенном и неустойчивом состоянии с углеродом, находящимся в твердом растворе. Как видно из рис. 9.1, температура закалки для получения подобной структуры (линия SE) тем выше, чем больше содержание углерода в стали. Подобная термообработка называется закалкой на гомогенный твердый раствор (аустенитизация) и для сталей типа 18-8 проводится с температур 1050 ... 1100 °С.
Межкристаллитная коррозия вызывается местным обеднением хромом металла зерна возле границы, вследствие более низкой скорости диффузии хрома по сравнению с углеродом, при температурах ниже 900 °С. Однако если сталь при этих температурах выдерживать достаточно длительное время, несмотря на малую скорость диффузии хрома, его концентрация по объему зерна (периферийная и центральная) будет выравниваться и склонность стали к МКК уменьшится. Такая термообработка называется стабилизирующим отжигом. Его проводят обычно при температуре 850 ... 900 СС в течение 2 ... 3 ч.
В целом зависимость МКК от времени и температуры можно представить схемой на рис. 9.3. Левая ветвь схемы (кривая /) показывает тем-пературно-временные условия появления в швах склонности к МКК. При температурах до 650 °С скорость образования карбидов хрома возрастает при небольшой скорости диффузии хрома. В результате время выдержки металла при рассматриваемой температуре до появления МКК сокращается и при температуре 650 °С (t кр) может достигать нескольких минут.
Рис. 9.3. Зависимость появления склонности к МКК металла швов на аустенитной стали" от температуры и времени
ТЕХНОЛОГИЯ СВАРКИ АУСТЕНИТНЫХ СТАЛЕЙ
Повышение температуры, увеличивая скорость диффузии хрома, уменьшает местное обеднение границ зерен хромом и склонность швов к МКК. Выдержка стали в рассматриваемом интервале температур в течение?им и более, приводя к диффузионному выравниванию содержания хрома по объему зерна, способствует приобретению металлом повторной стойкости к МКК (кривая 2). Уменьшение в стали содержания углерода, легирование ее более сильными, чем хром, карбидообразователями (титан, ниобий и др.) сдвигает вправо кривую / начала появления склонности металла к МКК. Процессы, протекающие при образовании карбидов, влияют не только на появление такой склонности, но и сильно изменяют механические свойства сталей при комнатных и высоких температурах.
Изменение в стали содержания легирующих элементов влияет на положение фазовых областей. Основными легирующими элементами в рассматриваемых сталях служат хром и никель. В зависимости от их соотношения стали иногда разделяют на стали с малым (% Ni / % Сг ≤ 1) и большим запасом аустенитности (% Ni / % Сг > 1).
Титан, ниобий, вольфрам и ванадий - карбидообразователи. Поэтому в стали могут образовываться не только карбиды хрома, но и карбиды этих элементов (TiC, NbC, VC). При определенных содержаниях весь свободный, выше предела его растворимости (0,02 %), углерод может выделиться не в виде карбидов хрома, а в виде карбидов титана или ниобия. Выпадение карбидов повышает прочностные и понижает пластические свойства сталей.
Упрочнение, связанное с выделением карбидов, зависит от степени дисперсности - оно увеличивается с уменьшением размеров карбидов. Это свойство карбидов используют для дисперсионного упрочнения жаропрочных сталей, проводимого обычно в комплексе с интерметаллид-ным упрочнением [упрочняющие частицы-интерметаллиды Ni 3 Ti, Ni 3 (Al, Ti), Fe 2 W и др.]. К интерметаллидным соединениям относят и а-фазу, которая образуется в хромоникелевых сталях при длительном нагреве или медленном охлаждении при температурах ниже 900 ... 950 °С. Она обладает ограниченной растворимостью в α- и γ-твердых растворах и, выделяясь преимущественно по границам зерен, резко снижает пластические свойства и ударную вязкость металла.
Повышенные концентрации в стали хрома (16 ... 25 %) и элементов, способствующих образованию феррита (молибдена, кремния и др.), вы-
зывают образование при температурах 700 ... 850 °С а-фазы. Выделение этой фазы происходит преимущественно с образованием промежуточной фазы феррита (γ → α → σ) или преобразованием 5-феррита (δ → σ). Однако возможно ее выделение и непосредственно из твердого раствора (γ → σ). Холодная деформация, приводя к появлению дополнительных плоскостей сдвига, увеличивает количество выделившейся σ-фазы. Выделение σ-фазы резко снижает служебные характеристики жаропрочных и жаростойких сталей.
9.2. ОСНОВНЫЕ СВЕДЕНИЯ О СВАРИВАЕМОСТИ
Свариваемость рассматриваемых сталей и сплавов затрудняется многокомпонентностью их легирования и разнообразием условий эксплуатации сварных конструкций (коррозионная стойкость, жаростойкость или жаропрочность). Общей сложностью сварки является предупреждение образования в шве и околошовной зоне кристаллизационных горячих трещин, имеющих межкристаллитный характер, наблюдаемых в виде мельчайших микронадрывов и трещин. Горячие трещины могут возникнуть и при термообработке или работе конструкции при повышенных температурах. Образование горячих трещин наиболее характерно для крупнозернистой структуры металла шва, особенно выраженной в многослойных швах, когда кристаллы последующего слоя продолжают кристаллы предыдущего слоя.
Концентрационное и термическое переохлаждение способствует развитию дендритной или микроскопической ликвации. В аустенитных швах направленность столбчатых кристаллов выражена наиболее четко. Повышенное сечение и поэтому малая поверхность столбчатых кристаллов способствуют образованию межкристаллитных прослоек повышенной толщины, что и увеличивает вероятность образования горячих трещин. Применение методов, способствующих измельчению кристаллов и дезориентации структуры, утоныыая межкристаллитные прослойки, несколько повышает стойкость швов против горячих трещин.
Один из таких методов - получение швов, имеющих в структуре некоторое количество первичного δ-феррита. Положительное действие феррита в аустенитно-ферритных швах на предупреждение образования в них горячих трещин связано с характером процесса первичной кристал-
ТЕХНОЛОГИЯ СВАРКИ АУСТЕНИТНЫХ СТАЛЕЙ
лизации металла сварочной ванны. Одновременное выпадение из жидкой фазы кристаллов аустенита и первичного δ-феррита приводит к измельчению и дезориентации структуры, т.е. уменьшению сечения столбчатых кристаллов и утонению межкристаллитных прослоек, разделенных участками первичного δ-феррита. В результате вероятность образования горячих трещин по местам расположения прослоек уменьшается.
Элементы, способствующие ферритизации металла, оказывают и обессеривающее действие на сварочную ванну, уменьшая количество легкоплавкой сульфидной эвтектики. Благоприятное действие δ-феррита может быть объяснено и большей растворимостью в нем примесей, уменьшающей их ликвацию. Получение аустенитно-ферритных швов достигается их дополнительным легированием ферритообразующими элементами, такими как хром, кремний, алюминий, молибден и др. В изделиях, работающих как коррозионно-стойкие при температурах до 400 °С, допускается содержание феррита до 20 ... 25 %. В швах на жаропрочных и жаростойких сталях, работающих при более высоких температурах, возможно образование σ-фазы с соответствующим ухудшением служебных характеристик шва. С целью предупреждения сигматизации швов количество δ-феррита в швах на жаропрочных и жаростойких сталях ограничивают 4 ... 5 %.
В сталях с большим запасом аустенитности получение швов с аустенитно-ферритной структурой затруднено необходимостью легирования их повышенным количеством ферритизаторов. Возможность предотвращения в швах на них, а также на аустенитно-ферритных сталях горячих трещин достигается ограничением содержания в швах вредных (фосфора, серы) и ликвирующих примесей, образующих легкоплавкие эвтектики, располагающиеся на завершающейся стадии кристаллизации по границам столбчатых кристаллов. Это достигается применением сварочных материалов, минимально засоренных вредными и ликвирующими элементами, например электродных проволок, изготовленных из сталей вакуумной выплавки, электрошлакового переплава и т.д. Ограничивается также проплавление основного металла.
В некоторых случаях повышение стойкости швов против горячих трещин, наоборот, достигается повышением ликвирующих примесей до концентраций, обеспечивающих получение при завершении кристаллизации сплошной пленки легкоплавкой эвтектики на поверхности кри-
ОСНОВНЫЕ СВЕДЕНИЯ О СВАРИВАЕМОСТИ
сталлита. Это может быть достигнуто легированием стали бором (0,3 ... 1,5 %). Повышенная литейная усадка и значительные растягивающие напряжения, действующие при затвердевании на сварочную ванну, также способствуют образованию горячих трещин. Снижение действия силового фактора (ограничение силы тока, заполнение разделки валиками небольшого сечения, рациональная конструкция соединения и др.) способствует предупреждению горячих трещин.
Помимо сложности получения на аустенитных высоколегированных сталях и сплавах швов без горячих трещин имеются и другие трудности, обусловленные спецификой их использования. К сварным соединениям на жаропрочных сталях предъявляется требование сохранения в течение длительного времени высоких механических свойств при повышенных температурах. Большие скорости охлаждения металла шва при сварке приводят к фиксации неравновесных по отношению к рабочим температурам структур. Во время эксплуатации при температурах выше 350 °С в результате диффузионных процессов в стали появляются новые структурные составляющие, приводящие обычно к снижению пластических свойств металла шва.
Термическое старение при температурах 350 ... 500 °С может привести к появлению 475°-ной хрупкости. Выдержка аустенитно-ферритных швов при температуре 500 ... 650 °С приводит к старению в основном за счет выпадения карбидов. Одновременно идет процесс образования σ-фазы. Легирование сталей титаном и ниобием приводит к дисперсионному упрочнению стали за счет образования их прочных карбидов. Являясь ферритизаторами, титан и ниобий, способствуя образованию в шве ферритной составляющей, увеличивают количество σ-фазы в металле. Выдержки при температуре 700 ... 850 °С значительно интенсифицируют образование σ-фазы с соответствующим охрупчиванием металла при более низких температурах и снижением предела ползучести при высоких температурах. При этих температурах возрастает роль и интер-металлидного упрочнения за счет образования, в частности, интерметал-лидных фаз железа с титаном и ниобием.
В чисто аустенитных швах в процессах теплового старения ведущее место занимают процессы карбидного и интерметаллидного упрочнения. Одно из эффективных средств уменьшения склонности сварных соединений жаростойких и жаропрочных сталей к охрупчиванию в результате
ТЕХНОЛОГИЯ СВАРКИ АУСТЕНИТНЫХ СТАЛЕЙ
выпадения карбидов - снижение в основном металле и металле шва содержания углерода. Наклеп, способствуя увеличению в шве содержания ферритной фазы, усиливает возможность их охрупчивания.
Ввиду высокого коэффициента теплового расширения суммарная внутренняя пластическая деформация металла шва и околошовной зоны при сварке высоколегированных сталей выше, чем в низколегированных сталях. В результате при сварке многослойных швов (многократная пластическая деформация), жестких соединений и т.п. околошовная зона и нижние слои металла шва могут заметно упрочняться. Самонаклеп также увеличивает количество ферритной фазы, а значит, и вероятность охрупчивания (сигматизации) швов.
В зоне термического влияния некоторых жаропрочных аусте-нитных сталей под действием термического цикла сварки снижаются пластические и прочностные свойства, что может повести к образованию в этой зоне трещин. Подобные изменения свойств основного металла вызываются развитием диффузионных процессов, приводящих к повышенной концентрации в металле околошовной зоны элементов (углерода, кислорода и др.), которые совместно с вредными примесями могут образовывать легкоплавкие эвтектики. При длительной эксплуатации в этой зоне могут выделяться мелкодисперсные карбиды и интерметаллиды, коагуляция которых приводит также к охрупчиванию металла. При сварке этих сталей для предупреждения образования горячих трещин в шве часто получают металл шва, по составу отличающийся от основного и имеющий двухфазную структуру.
В процессе высокотемпературной эксплуатации происходит карбидное и интерметаллидное упрочнение металла шва и соответствующее снижение его пластических свойств, что приводит к локализации в околошовной зоне деформаций и образованию в ней трещин. Этому способствует и высокий уровень остаточных сварочных напряжении в сумме с рабочими напряжениями. Предотвращение подобных локальных разрушений достигается термообработкой - аустенитизацией при температуре 1050 ... 1100 °С для снятия остаточных сварочных напряжений и самонаклепа и придания сварному соединению более однородных свойств. В ряде случаев аустенитизация сопровождается последующим стабилизирующим отжигом при температуре 750 ... 800 °С для получения относительно стабильных структур за счет выпадения карбидной и интерме-таллидной фаз.
ОСНОВНЫЕ СВЕДЕНИЯ О СВАРИВАЕМОСТИ
При сварке высокопрочных сталей в околошовной зоне возможно образование холодных трещин. Поэтому до сварки рекомендуется их аустенитизация для получения высоких пластических свойств металла, а после сварки - упрочняющая термообработка. Подбор химического состава металла шва, получение в нем благоприятных структур за счет выбора режима сварки и термообработки, снижение уровня остаточных напряжений за счет уменьшения жесткости сварных соединений или термообработки - основные пути предотвращения охрупчивания сварных соединений и образования в них холодных трещин. Предварительный или сопутствующий подогрев до температуры 350 ... 450 °С служит этой же цели.
При сварке жаростойких сталей под воздействием температуры в металле швов могут наблюдаться такие же структурные изменения, как и при сварке жаропрочных сталей. Высокая коррозионная стойкость жаростойких сталей в газовых средах при повышенных температурах определяется возможностью образования и сохранения на их поверхности прочных и плотных пленок оксидов. Это достигается легированием их хромом, кремнием, алюминием. Поэтому во многих случаях необходимая жаростойкость сварного соединения достигается максимальным приближением состава шва к составу основного металла. Во многих случаях к сварным соединениям жаростойких сталей предъявляется требование стойкости к газовой межкристаллитной коррозии.
Большинство жаростойких сталей и сплавов имеет большой запас аустенитности и поэтому при нафеве и охлаждении при сварке фазовых превращений не претерпевает, кроме карбидного и интерметаллидного дисперсионного твердения. При сварке этих сталей возможно образование холодных трещин в шве и околошовной зоне, предупреждение которых в ряде случаев может быть достигнуто предварительным подофевом сталей до температуры 250 ... 550 °С.
Высоколегированные аустенитные стали и сплавы наиболее часто используют как коррозионно-стойкие. Основное требование, которое в этом случае предъявляется к сварным соединениям, - стойкость к различным видам коррозии. Межкристаллитная коррозия может развиваться в металле шва и основном металле у линии сплавления (ножевая коррозия) или на некотором удалении от шва (рис. 9.4). Механизм развития этих видов коррозии одинаков. Однако причины возникновения названных видов межкристаллитной коррозии различны.
ТЕХНОЛОГИЯ СВАРКИ АУСТЕНИТНЫХ СТАЛЕЙ
Рис. 9.4. Схемы межкристаллитной коррозии сварных соединений аустенитных сталей:
а - в основном металле; б - в металле шва; в - ножевая коррозия
Межкристаллитная коррозия в металле шва (см. рис. 9.4, б) возникает в результате выделения под действием термического цикла сварки из аустенита карбидов хрома, приводящего к местному обеднению границ зерен хромом. Основная причина этого - повышенное содержание в металле шва углерода и отсутствие или недостаточное содержание титана или ниобия. Неблагоприятный термический цикл сварки - длительное пребывание металла шва в интервале критических температур (t > t кр, рис. 9.3) приводит к появлению склонности к межкристаллитной коррозии шва. Шов может потерять стойкость против межкристаллитной коррозии в результате воздействия критических температур при эксплуатации изделия. Аустенитно-ферритные швы с дезориентированной структурой имеют и повышенную стойкость против ММК по сравнению с ау-стенитными.
Увеличение протяженности границ зерен за счет их измельчения увеличивает поверхности, на которых выделяются карбиды. Выделяющиеся карбиды более дисперсны, и местное обеднение объема зерна хромом происходит на меньшую глубину. Кроме того, процессы диффузии в феррите протекают значительно быстрее, и выравнивание концентрации хрома в обедненных участках и центральных участках зерна происходит достаточно быстро.
Межкристаллитная коррозия основного металла на некотором удалении от шва (см. рис. 9.4, а) вызывается также действием термического цикла сварки в той части основного металла, где находилась изотерма критических температур.
Предупреждение склонности стали и швов к ММК достигается: снижением содержания углерода до пределов его растворимости в аусте-ните (до 0,02 ... 0,03 %), легированием более энергичными, чем хром, карбидообразующими элементами (стабилизация титаном, ниобием, тан-
ОСОБЕННОСТИ ТЕХНОЛОГИИ И ТЕХНИКИ СВАРКИ 359
талом, ванадием и др.); аустенитизацией (закалкой) с температур 1050 ... 1100 °С, однако при повторном нагреве в интервале критических температур (500 ... 800 °С) сталь повторно приобретает склонность к межкристаллитной коррозии; стабилизирующим отжигом при температуре 850 ... 900 °С в течение 2 ... 3 ч; созданием аустенитно-ферритной структуры с содержанием феррита до 20 ... 25 % путем дополнительного легирования хромом, кремнием, молибденом, алюминием и др. Однако такое высокое содержание в структуре феррита может понизить стойкость металла к общей коррозии. Эти же меры способствуют и предупреждению ножевой коррозии.
Ножевая коррозия имеет сосредоточенный характер (см. рис. 9.4, в) и поражает основной металл. Этот вид коррозии развивается в сталях, стабилизированных титаном и ниобием, обычно в участках, которые нагревались до температур выше 1250 °С. При этом карбиды титана и ниобия растворяются в аустените. Повторное тепловое воздействие на этот металл критических температур 500 ... 800 °С (например, при многослойной сварке) приведет к сохранению титана и ниобия в твердом растворе и выделению карбидов хрома.
Общая коррозия представляет собой растворение металла в коррозионной среде и может развиваться преимущественно в металле шва, различных участках зоны термического влияния или преимущественно в основном металле. В некоторых случаях она может развиться равномерно в основном металле и сварном соединении.
Наблюдается еще один вид коррозионного разрушения - коррозионное растрескивание, возникающее под совместным действием растягивающих напряжений и агрессивной среды. Разрушение развивается как межкристаллитное, так и транскристаллитное. Снижение уровня остаточных сварочных напряжений - одна из основных мер борьбы с этим видом коррозионного разрушения.
9.3. ОСОБЕННОСТИ ТЕХНОЛОГИИ И ТЕХНИКИ СВАРКИ
Высоколегированные аустенитные стали и сплавы обладают комплексом положительных свойств. Поэтому одну и ту же марку стали иногда можно использовать для изготовления изделий различного назначения, например коррозионно-стойких, хладостойких, жаропрочных и т.д. В связи с этим и требования к свойствам сварных соединений будут раз-
ТЕХНОЛОГИЯ СВАРКИ АУСТЕНИТНЫХ СТАЛЕЙ
личными. Это определит и различную технологию сварки (сварочные материалы, режимы сварки, необходимость последующей термообработки и т.д.), направленную на получение сварного соединения с необходимыми свойствами, определяемыми составом металла шва и его структурой.
Характерные для высоколегированных сталей теплофизические свойства определяют некоторые особенности их сварки. Пониженный коэффициент теплопроводности при равных остальных условиях значительно изменяет распределение температур в шве и околошовной зоне (рис. 9.5). В результате одинаковые изотермы в высоколегированных сталях более развиты, чем в углеродистых. Это увеличивает глубину проплавления основного металла, а с учетом повышенного коэффициента теплового расширения возрастает и коробление изделий.
Поэтому для уменьшения коробления изделий из высоколегированных сталей следует применять способы и режимы сварки, характеризующиеся максимальной концентрацией тепловой энергии. Примерно в 5 раз более высокое, чем у углеродистых сталей, удельное электросопротивление обусловливает больший разогрев сварочной проволоки в вылете электрода или металлического стержня электрода для ручной дуговой сварки. При автоматической и полуавтоматической дуговой сварке следует уменьшать вылет электрода и повышать скорость его подачи. При ручной дуговой сварке уменьшают длину электродов и допустимую плотность сварочного тока.
Одна из основных трудностей при сварке рассматриваемых сталей и сплавов - предупреждение образования в швах и околошовной зоне горячих трещин. Предупреждение образования этих дефектов достигается:
Рис. 9.5. Температурные поля при одинаковой погонной энергии
и толщине металла при сварке углеродистой (а)
и высоколегированной (б) сталей
ОСОБЕННОСТИ ТЕХНОЛОГИИ И ТЕХНИКИ СВАРКИ 361
1) ограничением (особенно при сварке аустенитных сталей) в основном и наплавленном металлах содержания вредных (серы, фосфора) и ликвирующих (свинца, олова, висмута) примесей, а также газов - кислорода и водорода. Для этого следует применять режимы, уменьшающие долю основного металла в шве, и использовать стали и сварочные материалы с минимальным содержанием названных примесей. Техника сварки должна обеспечивать минимальное насыщение металла шва газами. Этому способствует применение для сварки постоянного тока обратной полярности. При ручной сварке покрытыми электродами следует поддерживать короткую дугу и сварку вести без поперечных колебаний. При сварке в защитных газах, предупреждая подсос воздуха, следует поддерживать коротким вылет электрода и выбирать оптимальными скорость сварки и расход защитных газов. Необходимо также принимать меры к удалению влаги из флюса и покрытия электродов, обеспечивая их необходимую прокалку. Это уменьшит также вероятность образования пор, вызываемых водородом;
2) получением такого химического состава металла шва, который обеспечил бы в нем двухфазную структуру. Для жаропрочных и жаростойких сталей с малым запасом аустенитности и содержанием никеля до 15 % это достигается получением аустенитно-ферритной структуры с 3 ... 5 % феррита. Большее количество феррита может привести к значительному высокотемпературному охрупчиванию швов ввиду их сигмати-зации. Стремление получить аустенитно-ферритную структуру швов на глубокоаустенитных сталях, содержащих более 15 % Ni, потребует повышенного их легирования ферритообразующими элементами, что приведет к снижению пластических свойств шва и охрупчиванию ввиду появления хрупких эвтектик, а иногда и σ-фазы.
Поэтому в швах стремятся получить аустенитную структуру с мелкодисперсными карбидами и интерметаллидами. Благоприятно и легирование швов повышенным количеством молибдена, марганца и вольфрама, подавляющих процесс образования горячих трещин. Количество феррита в структуре швов на коррозионно-стойких сталях может быть повышено до 15 ... 25 %. Высоколегированные стали содержат в качестве легирующих присадок алюминий, кремний, титан, ниобий, хром и другие элементы, обладающие большим сродством к кислороду, чем железо. Поэтому при наличии в зоне сварки окислительной атмосферы возможен их значительный угар, что может привести к уменьшению содержания
ТЕХНОЛОГИЯ СВАРКИ АУСТЕНИТНЫХ СТАЛЕЙ
или к полному исчезновению в структуре шва ферритной и карбидной фаз, особенно в металле с небольшим избытком ферритизаторов.
Для сварки рекомендуется использовать неокислительные низкокремнистые, высокоосновные флюсы (фторидные) и покрытия электродов (фтористокальциевые). Сварка короткой дугой и предупреждение подсоса воздуха служит этой же цели. Азот - сильный аустенитизатор, способствует измельчению структуры за счет увеличения центров кристаллизации в виде тугоплавких нитридов. Поэтому азотизация металла шва способствует повышению их стойкости против горячих трещин.
Высокоосновные флюсы и шлаки, рафинируя металл шва и иногда модифицируя его структуру, повышают стойкость против горячих трещин. Механизированные способы сварки, обеспечивая равномерное про-плавление основного металла по длине шва и постоянство термического цикла сварки, позволяют получить и более стабильные структуры на всей длине сварного соединения;
3) применением технологических приемов, направленных на изменение формы сварочной ванны и направления роста кристаллов аустени-та. Действие растягивающих сил, перпендикулярное направлению роста столбчатых кристаллов, увеличивает вероятность образования горячих трещин (рис. 9.6). При механизированных способах сварки тонкими электродными проволоками поперечные колебания электрода, изменяя схему кристаллизации металла шва, позволяют уменьшить его склонность к горячим трещинам;