The correct proportions of concrete. Choice of brand of concrete
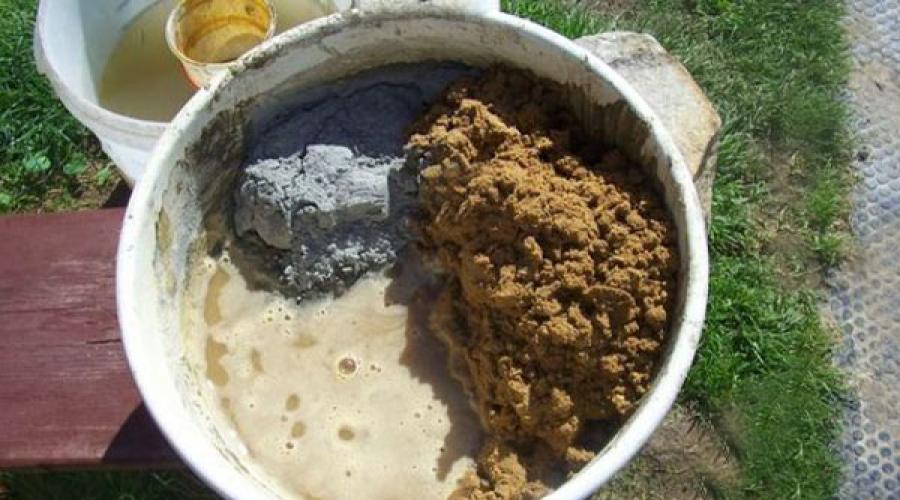
Read also
Concrete preparation is a very important construction process. The strength of future structures and their performance characteristics depend on the correctness of its implementation and the use of all components in the right proportions. Next, we will talk about right choice components and what proportions of concrete are best used when making concrete yourself.
The main components of the concrete solution
To obtain a high-quality concrete solution, it is necessary to choose the appropriate components for its manufacture, which are determined by the requirements for the strength of the future foundation. We’ll talk about how to prepare a solution for certain tasks a little later, but now let’s figure out what components can be in the solution:
- Cement of a certain marking.
- Sand.
- Various admixtures or plasticizers.
- Stone filler.
- Water.
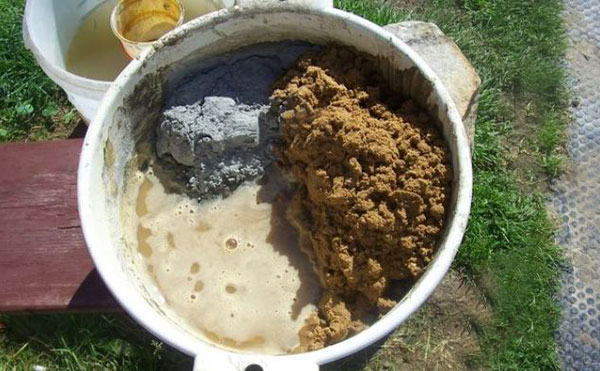
The choice of concrete elements must be treated responsibly and take into account their features.
Cement
Cement is the main ingredient concrete mix, which is a binder for all elements. When choosing its brand, it is necessary to determine the level of load that will act on its surface, as well as the impact of external destructive factors.
The load force per 1 cm² is indicated on the label immediately after the letter M. For example, to prepare the main foundation of structures that are erected during private construction, specialists in construction industry recommend using concrete M500. This means that 1 cm² can withstand a load of 500 kg on its surface. It is also allowed to use the M400 brand, but such a base will be less durable. For work inside structures, concrete with weaker strength indicators (M300, etc.) is used.
Some rules for choosing cement:
- It should be dry and loose. Do not buy cement of dubious origin, which is lumpy or obviously damp.
- The packaging must be marked. Without it, you may be sold a composition of fake content that does not meet the declared characteristics, which will lead to backfire(from the crackling of the walls to the destruction of the building, due to the destruction of the foundation).
- Pay attention to the numbers after the letter D. The digital equivalent is equal to the percentage of impurities present in the cement. For example, if M300-D40 is written on the package, this means that up to 40% of additional substances are in the binder. For personal use, it is better to purchase options with a value after the letter D, ranging from 0 to 20. This will allow you to get the highest quality solution.
There is one more small rule - buy cement for a certain period before the start construction works(about 14 days). He needs time to "rest".
Sand
Sand is a component used as a filler for the space formed between coarse concrete particles. Such filling is used to obtain concrete of the highest strength.
Features of his choice:
- The cleaner it is, the better. The same strength of all particles, which cannot be said about sand with the remains of vegetation or earth, improves the quality of the foundation.
- For the manufacture of the mixture, sand is selected, the dimensions of the elements of which are about 2-5 mm. If they differ in size, it should not exceed 2 mm.
- If possible, use sand extracted from the bottom of the rivers. Its quality indicators are optimal for use in construction purposes.
To obtain a concrete structure with maximum strength, instead of ordinary sand, artificial sand is used - a stone that has been crushed to a small fraction.
impurities
The preparation of the solution sometimes implies the presence of additional components:
- plasticizer. Makes the mixture more fluid or viscous.
- reinforcing substances. Slightly increase the tensile strength of concrete.
- Lime. When adding this component, the solution becomes more pliable for laying and leveling.
- Additives. They can change the characteristics of concrete, allowing it to set in wet conditions or when exposed to critical temperatures.
To use impurities in the manufacture of high-quality concrete, you need to clearly know the proportions and all the subtleties of their use, so if the work is done independently, it is better to refuse them.
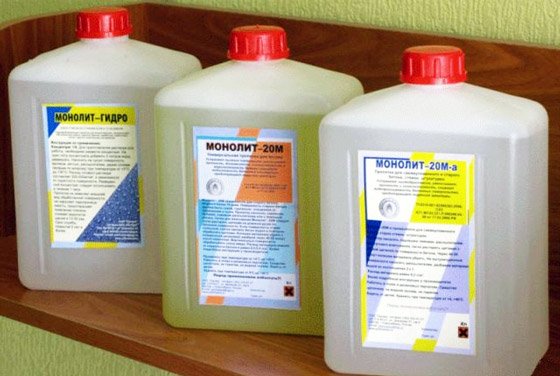
Filler
Key points when choosing crushed stone or gravel:
- The material should be as free from impurities as possible.
- The high surface roughness of the elements improves the strength characteristics of concrete (there will be better adhesion of the elements).
- In the case of a filler, the greater the difference in particle size fractions, the better.
If the filler is stored on the soil, do not use its bottom layer. Along with it, dirt or earth can get into the solution.
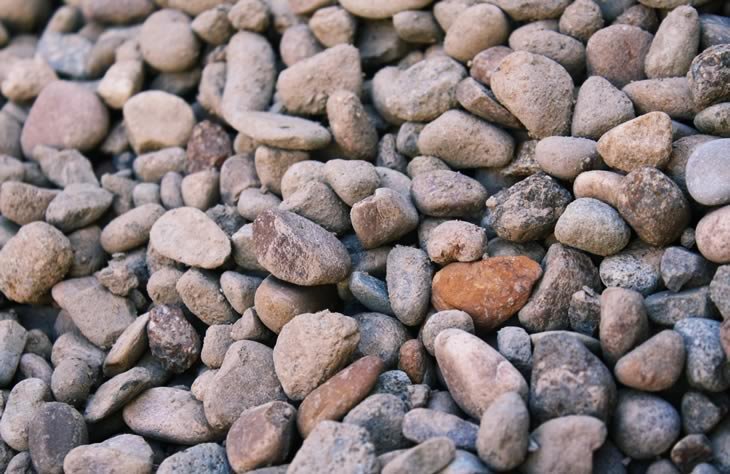
Water
The statement that for concrete there is no difference what kind of water is used is obviously erroneous. If its composition contains components that violate the structure of the elements of the concrete mixture, then it is better to refuse it. The list of such waters includes river or lake.
Important! If the water is drinkable, it is ideal for making concrete mix.
The correct proportions of concrete
The ratio of the components used to each other affects the strength of the final substance. The required level of strength depends on the goals: you need to build the foundation of a building, a small structure, an alley, etc. For example, the foundation for a house should contain the required amount of crushed stone or gravel of a large fraction, and in the simplest form of a solution, there may be no gravel at all ( only cement and sand).
The proportion that has gained the greatest distribution implies a consistent increase in the number of components in geometric progression: 1 part of concrete, 3 - sand, 6 - aggregate. Water should be present from 0.5 to 1 part. Its quantity depends only on the required consistency, which the solution should be obtained.
Such ratios are rather conditional - they do not take into account the sizes of the fractions of the components, as well as their characteristics. Therefore, without exact calculations, a rather unexpected result can turn out.
How to calculate the amount of concrete?
Let us give an example of calculus using a specific example. We need to make 10 cubic meters of the mixture. We use the following components:
- 1 part of cement M500.
- Water 2 parts.
- Aggregate. 4 parts. We will use crushed stone as a filler.
It turns out that you need to make 10 cubes from 7 parts. Each piece will be equal to 1.42 cubes (10 / 7). To find out the volume of each element, you need to multiply the number of its parts by the resulting value. For example, the placeholder will be 4 parts: 4 x 1.42 = 5.68 cubes.
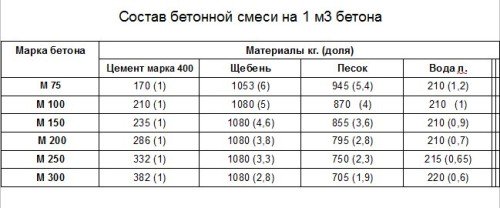
Attention! It is believed that the optimal amount of water used should be equal to half of the cement used.
Preparing concrete is a fairly simple construction process that you can do yourself. But it is important to accurately calculate the proportions, and use only high-quality materials for manufacturing. An inattentive attitude or errors in the preparation of the mixture can lead to subsequent deformation of the building frame, caused by the destruction of the foundation.
What are the proportions for concrete updated: December 14, 2015 by: crunch0
To prepare a concrete mixture, it is important to know its proportions. The ratio of the main components of concrete - cement, sand, crushed stone and water determine its type and intended use. Basically, concrete is cement with multiple fillers. The main fillers are sand and crushed stone, less often - gravel, expanded clay, stone chips. Sometimes a plasticizer is introduced into the mixture - a special additive.
Which cement to choose
For concrete, it is important to choose the appropriate type of cement. Cement is selected based on the requirements for concrete in terms of frost resistance, strength, resistance to impact chemical substances, permeability. It is necessary to take into account the design features and manufacturing methods reinforced concrete structures.Choice of brand of cement depending on the required concrete grade for compressive strength:
Concrete grade | Grade of cement |
100 | 300 |
150 | 300 |
200 | 400 |
250 | 400-500 |
300 | 500 |
400 | 400-600 |
500 | 600 |
600 | 600 |
For example, using the most common cement grade M-400, concrete grade M-250 is obtained.
The grade of the required cement depends on the quality and quantity of sand and gravel used in the composition of concrete.
To obtain a good result, it is advisable to take a filler of different sizes for concrete. A large number of voids will increase the consumption of cement, and, accordingly, the cost, since cement is the most expensive component of the concrete mixture. Fillers of different sizes will reduce the number of voids.
The thickness of the concrete pavement for the foundation when laying by hand should be 3 times the size of the maximum size filler. To calculate the volume of voids, you need to fill a 10 liter bucket with filler and pour water into it to the brim. If the water flow is 3.5 liters, then 35% of the total volume is left to fill the voids with cement.
What rubble will be useful
Limestone has medium strength, but low frost resistance. The resulting types of concrete - up to M-350.
- Crushed stone - strength 800-1000, obtained types of concrete - up to M-450. Enough strength and frost resistance for private construction.
- Granite - strength 1000-1400, the resulting types of concrete - from M-450 and above. The most durable, frost-resistant, for road construction.
Why additives are needed Various additives are sometimes added to concrete, but before that you need to decide what indicators they will improve. Basically, they are needed in order to make concrete more ductile and easy to lay. There are additives that increase the strength of the concrete pavement and regulate the degree of adhesion and setting of the mixture, those that increase frost resistance and reduce moisture absorption. When using additives, carefully read the instructions for use. The amount of water required is reduced when special additives are used. Add water in small portions. Some plasticizers are incompatible with others. Standard concrete mix proportions
Direct selection of proportions
To choose the proportions of the concrete mix, you need to analyze several points:
- How will the concrete mix be placed? If manually, then it should be plastic. With a mechanized laying method, a mixture of a higher density is required. When adding water, do not forget to add cement. Plasticity is not determined by the amount of water, its excessive amount will lead to a loss of structural strength, which, when exposed to loads or adverse conditions, can lead to destruction. This is especially critical when building a foundation.
- what will it be used for
- What quality components will be included in its composition.
As such a universal recipe for cooking various brands there is no concrete. Due to the fact that the components are different in quality, you can only roughly indicate the proportions of the concrete mix different brands.Some standard concrete mix ratio is 3:1 or 4:1 sand to cement, depending on the quality of the aggregates and designated purpose concrete, the desired ratio is determined empirically. The strength of concrete directly depends on the correct ratio of water and cement.
The usual concrete mixture is diluted in the following ratio: 1: 2: 4: 1/2 cement, sand, crushed stone, water, respectively.
For example, to obtain 1 m3 of concrete, you will need:
- 330 kg of cement
- 180 liters of water
- 1250 kg of crushed stone
- 600 kg of sand
The specified amount of water may vary slightly. Hard water is added less than the specified amount, soft - more. Cement without fillers hardens but does not required strength due to cracks and gives a lot of shrinkage. In addition, fillers further reduce the cost of concrete, since the price of cement is higher compared to sand and crushed stone. Sand is better to take large clean river without clay.
The proportions of the concrete mixture to obtain 1 cubic meter of concrete:
- Cement M-400 - 492 kg
- Water - 205 l
- PGS (sand-gravel mixture) - 661 kg
- Crushed stone - 1000 kg
- Cement M-300 - 384 kg
- Water - 205 l
- PGS (sand-gravel mixture) - 698 kg
- Crushed stone - 1055 kg
- Cement M-200 - 287 kg
- Water - 185 l
- PGS (sand-gravel mixture) - 751 kg
- Crushed stone - 1135 kg
- Cement M-100 - 206 kg,
- Water - 185 l
- PGS (sand-gravel mixture) - 780 kg
- Crushed stone - 1177 kg
In the manufacture of concrete mortar at home, it is more convenient to measure the components of concrete in liters or buckets, rather than kilograms. It is useful to know that there are 38 liters of cement in a 50 kg bag.
If the work needs to be done urgently and there is no time for experiments, buy a ready-made dry mix indicating the required amount of water on the package. So you can quickly and efficiently complete necessary work without too much trouble.
Concrete is an amazing material. It is used not only for the construction of the foundation of buildings, but also for the installation of walls and roofs. But the scope of its application is not limited to this. Concrete can also be used to produce piece items, for example paving slabs, balusters, vases and even countertops for living rooms and kitchens.
To date, there are many ways to prepare concrete, and this allows you to build this material almost to a level equivalent to such natural materials like granite or marble. Although, according to its external data, it is not particularly aesthetic like natural stones, you can say with confidence what it is made of.
If you decide to abandon the purchase of concrete, and decide to make it yourself, then you need to observe the exact proportions of the mixed materials. Only in this case, your finished mixture will have high strength and durability.
Concrete preparation, proportions
The whole process of preparing concrete is quite simple, although there are a number of special points that must be taken into account that will determine its quality and suitability in the future. Depending on the purpose of the application, the method of its preparation will also change.
There are two main options for making concrete with your own hands: In the first case, mix all the ingredients in a dry form, and then just pour water.
In the second case, you pour cement, aggregate and sand into the poured water. With dry kneading, all materials seem to be distributed evenly, however, after adding water and manual mixing, there is no exact guarantee that the entire volume obtained will get wet quickly and efficiently. As a result, it turns out that a dry layer remains at the bottom, and as a result, this will lead to a violation of proportions. If you mix the solution thoroughly and for a very long time, then a long time will pass, and as a result, the solution will begin to set, and this will directly affect its strength. When adding all the components of the solution to water, the cement will be kneaded for a long time and will not be able to adhere well enough to the filler. The second option is slightly better than the first when mixing concrete in small quantities.
The most well-known proportions of concrete are 1:3:6 parts of cement, aggregate and sand, as well as 0.5-1 part of water, depending on the required fluidity of the solution. Adhering to these proportions, a concrete solution that is not very convenient for mixing may turn out.
When adding proportions, a bucket or other container is taken and filled (high-quality tamping is not needed) with sand, aggregate and cement in turn and weighed. By elementary calculations, convert all buckets into a percentage of each other.
When mixing all proportions of concrete in the best possible way will use special concrete mixers. Only thanks to such machines, it is possible to mix the components of the concrete mixture quickly and with sufficient quality and deliver them to the place of consumption before the mixture thickens. Of course, you can use the old manual method, but it is not particularly suitable for large volumes of the mixture. With this method of kneading, it is not possible to control the entire process and add ingredients according to the desired recipe.
The composition of concrete is a mixture of a solution of cement and filler. The main ingredients are: cement, sand, filler (crushed stone, gravel, pebbles, slag, etc.). Recently, however, modern technologies involve special additives - plasticizers. Their goal is to give concrete unique properties.
The main and main characteristic of concrete is strength (expressed in mega pascals).
Concrete is usually divided into grades according to its strength. According to state standards in the CIS countries, concrete classes are marked as B7.5 - B80. The number in the brand name means pressure in MPa.
The most common type of concrete is a mixture of cement and coarse sand. The concrete is coming for the substrate under the main foundation. Typically, such concrete is made directly at the bottom of the formwork under the main foundation. When mixing the mixture, a small amount of water must be added so that the solution acquires a density similar to that of wet soil. The strength of this concrete is low, but it perfectly protects the main foundation from subsidence and abundant moisture. To obtain the most durable concrete, it is necessary to use a variety of crushed stone with different fractions from 2 to 35 mm.
The quality of concrete will depend on the purity of all its components. Therefore, before proceeding with the preparation of the solution, it is worth considering each incoming component separately.
Cement - as the main component of concrete
Cement- this is the main and main ingredient of the concrete mix, which binds all the components together. Most often used for the preparation of concrete - Portland cement (perfect for working at low temperatures). It is distinguished by a high content of calcium silicates (about 80%), which is why the adhesion and bonding of materials improves.
Depending on the task, other types of cement have also been widely used.
Today, cement grade 500 is used for construction. You can also use the M400, only this will directly affect the durability and strength of the same foundation. To work in warm or hot weather ideal option will use Portland slag cement. In the standard marking of cement, in addition to indicating strength, it is customary to indicate third-party impurities (letter "D").
For example, concrete grade M500-D0 or M500-D20 is concrete with impurities from 0 to 20%.
When buying cement, it must be dry and free-flowing. Under unfavorable conditions, cement quickly picks up moisture from the air and loses its basic qualities. Therefore, it is recommended to buy the required amount of cement a maximum of 2 weeks before its use or directly a couple of days before.
When buying, be sure to check the integrity of the packaging and the presence of markings.
Auxiliary components of concrete - Sand
To prepare concrete with your own hands, you will also need sand. Sand suitable for mixing concrete must necessarily have a fraction of 1.5 to 5 mm, the ideal option would be a uniform size (1-2 mm). When choosing sand, it should not contain various impurities. Construction debris, plant residues, as well as various foreign inclusions that decay and rot over time, will drastically reduce the quality and strength of concrete. To clean the sand, it is passed through a special sieve with small cells.
Ideal for making concrete with your own hands river sand, although it is more expensive than ravine, it has the right grain size.
For places where there are stone quarries nearby, artificial heavy sand is used as an option. When it is washed and sieved, the size of its grains will be somewhat better than even river sand. But when using it, the concrete mixture will turn out to be much heavier, and this is important if it is used for screeding over interfloor floors.
Main aggregates: crushed stone and gravel
The strength of concrete directly depends on the filling with gravel or crushed stone. However, expanded clay is often used. It is quite strong yet lightweight.
When preparing a mixture, the size of gravel and crushed stone should not exceed 35 mm, larger pieces are most often used in production, but this is rare.
As with river sand, it is desirable that crushed stone or gravel contain as little foreign matter, dust or clay sediments as possible on its surface. It should be noted that the greater the roughness on the faces of the particles, the better the adhesion will be. For independent mixing of concrete proportions, an aggregate is selected, the particles of which have several sizes, or they are mixed coarse gravel with small or medium. This is done to ensure that the particles fit snugly together and prevent the formation of large voids. In the worst case, all voids will be filled with mortar, and this may affect both the quality of concrete and the consumption of the mortar itself.
The choice of water in the preparation of concrete mix
When preparing a concrete mix, the key and important point is the choice of water. Of course, there is no question of using any specific water. However, it must be free of any impurities (acids, alkalis) and must be clean. It is unacceptable to use river and lake water, in which there are numerous foreign inclusions. The main rule when choosing water for mortar: the water we drink is also ideal for making good and durable concrete. By following this rule, you can calculate the strength and durability of your concrete without damage or destruction.
Auxiliary additives for concrete and lime
When repairing and building, craftsmen add a little slaked lime to the concrete. This is done in order to make the solution more “convenient” for masonry. This makes it a little easier to level the surface of the concrete screed or the desired section of the porch, outlet. To resort to the addition of lime or not, the master decides, depending on the required composition. Currently, it is customary to use ready-made slaked lime, which is sold in special hardware stores and is called fluff.
Special additives - plasticizers
Modern technologies make it possible to give a concrete solution greater fluidity or viscosity due to special additives - plasticizers. It is they who change the properties of the solution in the right direction. The use of plasticizers can increase or decrease the amount of water used to prepare the concrete mix. As a rule, plasticizers are not used for pouring the foundation, however, they can help if the reinforcement is compacted or the foundation is sufficient. complex shape. However, more fluid concrete will fill in all the voids and branches formed much faster and better, and this will improve the result and speed up the whole process.
Concrete mortar is an essential component in the construction of foundations, and the durability of the entire structure depends on its quality. It is not always possible to order a ready mix, and therefore it is desirable to know how to make concrete with your own hands. Here it is important not only to observe the proportions, but to choose the right components, otherwise the strength of the solution will not be high enough.
Strength
Concrete mortar is a mixture of cement, sand, filler and water in certain proportions, which vary depending on the purpose of the concrete and the brand of cement. If necessary, plasticizers are added to the solution. The most important characteristic of concrete is its compressive strength, which is measured in MPa (mega pascals). It is according to this indicator that concrete is divided into classes. But the brand of concrete indicates the amount of cement in the mortar.
Concrete class | Average strength of this class, kg s / sq. cm | The nearest brand of concrete |
---|---|---|
AT 5 | 65 | M 75 |
At 7.5 | 98 | M 100 |
AT 10 | 131 | M 150 |
At 12.5 | 164 | M 150 |
At 15 | 196 | M 200 |
IN 20 | 262 | M 250 |
At 25 | 327 | M 350 |
At 30 | 393 | M 400 |
At 35 | 458 | M 450 |
At 40 | 524 | M 550 |
At 45 | 589 | M 600 |
At 50 | 655 | M 600 |
At 55 | 720 | M 700 |
At 60 | 786 | M 800 |
Concrete grade M100 and M150 (B7.5 and B12.5) is most often used as a layer under the main foundation, for the manufacture of screeds, concreting paths. Concrete M200-M350 is most in demand: it is used in the construction of foundations, for the manufacture of screeds, concrete stairs, blind areas. Solutions of higher grades are used mainly in industrial construction.
Plastic
An important characteristic of concrete is its ductility. The more plastic the solution, the better it fills the formwork structure. With low concrete mobility, unfilled areas remain in the screed or foundation, which leads to the gradual destruction of the concrete slab. For standard structures, concrete with plasticity P-2 or P-3 is used; for formwork of complex shape and in hard-to-reach places, it is recommended to use mortar P-4 and higher.
Waterproof and frost resistant
Water resistance depends on the amount and brand of cement in the solution. The higher the grade, the more resistant the concrete to moisture. Frost resistance of concrete is achieved by adding plasticizers to the composition. It should be noted that such solutions set very quickly; if it is incorrect to calculate the amount of the mixture or use it at a low temperature, the concrete will turn into a monolithic block right in the tank.
Concrete components
Cement performs a binding function for all other components of the concrete solution and the strength of the concrete itself directly depends on its quality. In private construction, cement grades M400 and M500 are most in demand. When buying cement, you should be aware that it loses its qualities during prolonged or improper storage. Within a month after manufacture, the binding properties of cement are reduced by 10%, after six months - by 50%, after a year it is not recommended to use it at all. But even fresh cement will become unusable if dampness pulls, so it must be stored in a dry place.
Sand is the second most important component of the concrete solution. In rare cases, it is replaced with slag, while standard concrete is always mixed with sand. It is best to use coarse-grained river sand without various impurities. If only ordinary fine sand is available, it should not contain clay, earth or silt, which reduce the adhesion of the mortar with the filler. Before kneading, the sand must be sieved to remove all excess.
Aggregate
The best aggregate for concrete mortar is crushed stone with sizes from 5 to 35 mm. Often crushed stone is replaced with gravel, a little less often with expanded clay. It is very important that the surface of the aggregate be rough, then its adhesion to the cement will be as strong as possible. To compact the mixture, you need to take aggregate different factions. Like sand, the aggregate must be clean, so it should be poured onto a prepared and compacted area or onto a spread tarp.
Additives
To give concrete frost resistance, water tightness and other useful properties plasticizers are used. They provide the setting of the solution at low temperatures, increase its plasticity or, conversely, impart viscosity. They should be used only if it is really necessary, and you should strictly follow the instructions for their use and observe the proportions.
If a thin screed or a screed on an unstable basis is required, reinforcing fibers are mixed into the concrete solution. They are made of polyvinyl chloride and polypropylene, their strength is small, but they perfectly avoid concrete cracking. In standard foundations and screeds, reinforcing substances are not needed.
Solution proportions
To make high-quality concrete yourself, you need to know in what proportions to mix the components. Most often, the ratio of cement, sand and crushed stone is used as 1:3:6; At the same time, they take half as much water as total weight dry ingredients. It is recommended to add water not all at once, but in several portions, so it is easier to control the density of the solution. The moisture content of the sand also matters - the higher it is, the less water is required. You need to measure all the components in one container, for example, a bucket. When using containers of different volumes, it will not be possible to achieve the desired proportions.
When mixing, the purpose of the solution should be taken into account. For the substrate under the screed, lean concrete is made without the addition of crushed stone, crushed stone of medium and fine fractions is used for concreting the paths and the blind area, for the foundation for the house, medium-fraction crushed stone and high-quality cement. The table will help you find out the exact proportions of concrete of different grades.
Manual way of mixing concrete
Mixing the concrete solution is carried out manually or in a concrete mixer. If you need to fill a large area, the first method is not suitable, as it will take too much time and physical effort. If you need a little solution, it is more convenient to knead it with your hands.
Step 1. Preparation
To prepare the solution, you will need a low wide container, for example, a large metal trough, a pick-up shovel, a bucket and an ordinary hoe.
Step 2: Dry Mixing
A bucket of cement is poured into the container, then 3 buckets of sifted sand and 5 buckets of crushed stone. Dry ingredients are thoroughly mixed with a hoe. The proportions may be different, depending on the required brand of solution.
Step 3: Adding Water
If all the ingredients are mixed evenly, you can add water. First, 7-8 liters are poured out and the contents are intensively stirred with a hoe. This process will require effort, but you need to stir very well. It is advisable to lift the bottom layer and run the hoe around the corners where dry lumps may remain. If the solution is very thick and reaches for the hoe, you need to add a little water. Properly prepared concrete slowly slides off the shovel, does not delaminate.
There is another option for kneading: first, water is poured into the container, then cement is poured. For 2 buckets of water you need 2 buckets of cement. Thoroughly mix the cement with water and add 4 buckets of sand. Mix well again until smooth. Crushed stone is poured last in the amount of 8 buckets and mixed again. Which method is better, there is no unequivocal opinion, so you should try both and determine for yourself the most optimal one.
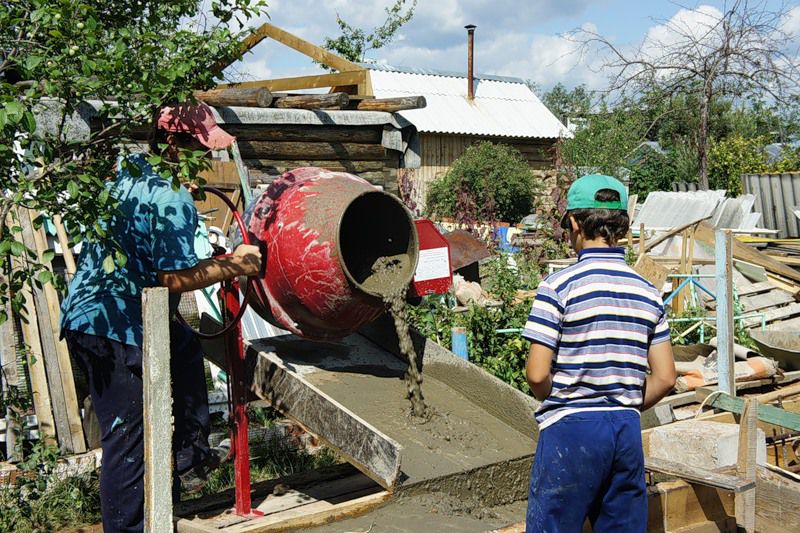
If the resulting concrete is too thick, a little cement is added to the remaining water, mixed well and poured into a concrete mixer. It is not recommended to stir the solution for more than 10 minutes, otherwise the cement will begin to set. Ready concrete is poured immediately onto the site or into a wheelbarrow if the concrete mixer is at a distance. It is advisable to pour out the entire solution at once, but if this does not work out, part of the mass is left in the included concrete mixer. It should be used as soon as possible.
Video - How to make concrete with your own hands