Crushed stone for construction works GOST 8267 93. Crushed stone and gravel from dense rocks
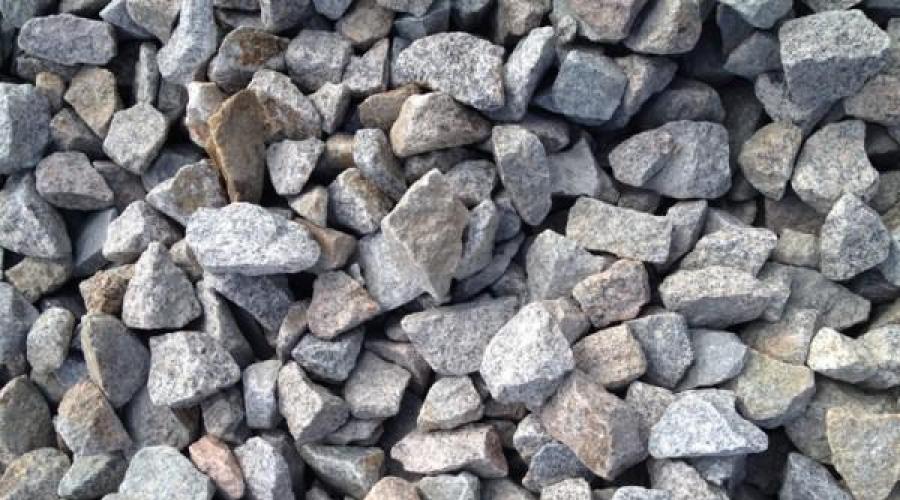
Crushed stone construction materialwhich is actively used when performing the most different construction workoh. Without it, it is not necessary to do with the erection of roads, the production of concrete, sinking and planning of the territories.
But before purchasing the presented product, it is very important to understand what characteristics it possesses, as well as what types of rubble are used to implement certain construction work.
It has an extensive classification, the fundamental factor in which the origin of the material is.
What brand of concrete is needed for belt Fundament And what are the proportions in it rubble you can learn from this
Distinguish such types of the presented product:
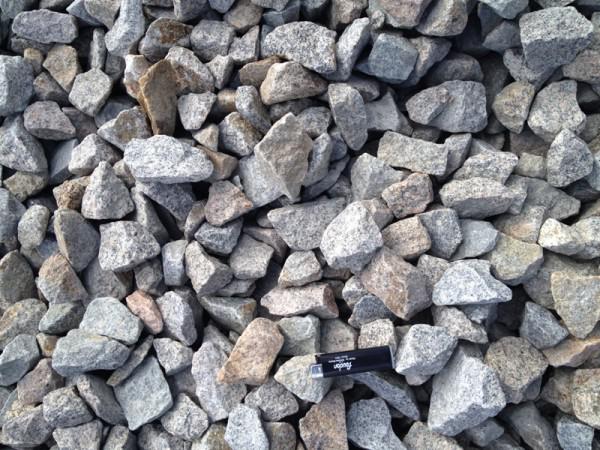
Fractions
Divided into such fractions:
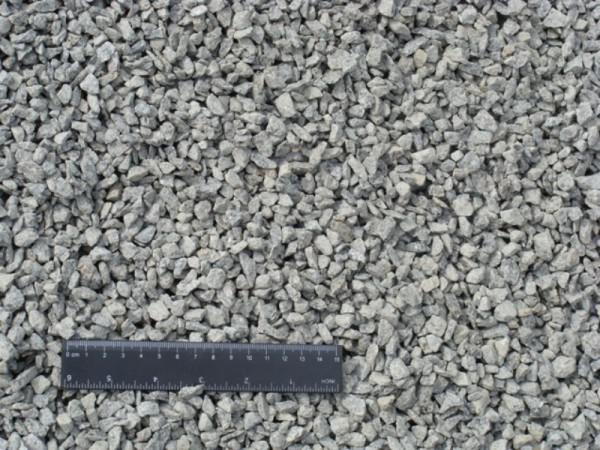
Which components are made heavy fine-grained concrete and with which proportion of rubble can be found from this
At the request of the customer, crushed stone can receive other fractions, as well as in the form of a mixture standard sizes. It is the sizes of grains that influence the scope of the finished product. For example, medium and finely used in the production of concrete and asphalt concrete compositions. The product with a large fraction was widespread during the construction of roads.
Cost
For the formation of the price, the fundamental factors are the appearance of this product. The maximum cost is the granite material. Its price of 1 m3 will be approximately 1900 rubles. Crushed limestone origin will cost you 1400 rubles.
What are the features of rubble with a fraction 40 70, you can learn from this
Crushed stone is a unique building material for its qualities. He got widespread in the field of construction, because it is characterized by such qualities as durability, frost resistance, eco-friendly safety. Before buying this product, it is necessary to clearly decide for what purposes you are going to apply it, as well as what fraction.
Crushed stone and gravel from dense mountain breeds For construction work
Technical conditions
GOST 8267-93
(With amendments of December 10, 1997, December 4, 2000, June 3, 2002)
Date of introduction January 1, 1995
Instead of GOST 8267-82, GOST 8268-82,
GOST 10260-82, GOST 23254-78, GOST 26873-86
1 area of \u200b\u200buse
This standard applies to crushed stone and gravel from rocks with an average grain density from 2.0 to 3.0 g / cm3, used as aggregates for heavy concrete, as well as for road and other types of construction work.
The standard does not apply to crushed stone and gravel for the ballast layer of the railway track and decorative crushed stone.
The requirements set out in paragraphs 4.2-4.9, sections 5 and 6 are mandatory.
By changing N 2, approved by the Resolution of the Russian State Building of the Russian Federation of December 4, 2000, N 115, in Section 2 of this GOST Amended, entered into force from April 1, 2001
See Section Section in the previous editorial board
2. Regulatory references
This standard uses links to the following standards:
GOST 3344-83 Crushed stone and sand slag for road construction. Technical conditions.
GOST 8269.0-97 "Crushed stone and gravel from dense rocks and waste industrial production for construction work. Methods of physical and mechanical testing."
GOST 30108-94 Building materials and products. Determination of the specific effective activity of natural radionuclides.
GOST 8269.1-97 "Crushed stone and gravel from dense rocks and waste industrial production for construction work. Chemical analysis methods."
3. Definitions
This standard applies the following terms.
Mountain crushed stone - Inorganic grainy bulk material with grains of sv. 5 mm, obtained by crushing rocks, gravel and boulders, minorly produced reverend and accommodating rocks or substandard waste of mining enterprises for the processing of ores (black, colored and rare metallurgical industries) and non-metallic minerals of other industries and subsequent rushing products of crushing.
Mountain Gravel - Inorganic grainy bulk material with grains of sv. 5 mm obtained by harsh natural gravel-sand mixtures.
4. Technical requirements
4.1 Crushed stone and gravel should be made in accordance with the requirements of this standard for technological documentation approved by the manufacturer.
A change in N 3, approved by the Resolution of the Gosstroita of the Russian Federation of June 3, 2002, N 32, amendments made in action from July 1, 2002 were made to paragraph 4.2 of this GOST.
4.2 Main parameters and sizes
4.2.1 Crushed stone and gravel produced in the form of the following main fractions: from 5 (3) to 10 mm; sv. 10 to 15 mm; sv. 10 to 20 mm; sv. 15 to 20 mm; sv. 20 to 40 mm; sv. 40 to 80 (70) mm and a mixture of fractions from 5 (3) to 20 mm.
In coordination of the manufacturer with the consumer, crushed stone and gravel in the form of other mixtures composed of individual fractions, as well as fractions from 80 (70) to 120 mm, sv. 120 to 150 mm.
4.2.2 Full residues on control sints in harassment of rubble and gravel fractions from 5 (3) to 10 mm; sv. 10 to 15 mm; sv. 10 to 20 mm, sv. 15 to 20 mm; sv. 20 to 40 mm, sv. 40 to 80 (70) mm and a mixture of fractions from 5 (3) to 20 mm should correspond to those specified in Table 1, where D and D are the smallest and largest rated grain sizes.
Table 1
Notes
1. For rubble and gravel of fractions from 5 (3) to 10 mm and the mixture of fractions from 5 (3) to 20 mm are used additionally: lower sieve 2.5 mm (1.25); The full residue on which should be from 95 to 100%.
2. In coordination of the manufacturer with the consumer, it is allowed to produce crushed stone and gravel with a full residue on the sieve 0.5 (d + d) from 30 to 80% by weight.
4.2.3 For rubble and gravel fractions of St. 80 (70) to 120 mm and sv. 120 to 150 mm, as well as for a mixture of fractions produced by coordination of the manufacturer with a consumer, full residues on the control sines with a diameter D, D, 1,25D must be satisfied with the specified in Table 1, and the ratio of fractions in the mixtures is established by coordinating the manufacturer with the consumer in accordance with Regulatory documents on the use of these mixtures for construction work.
4.2.4 Excluded from July 1, 2002
See the text of clause 4.2.4
4.3.1 Crushed stone from gravel should contain crushed grains in an amount of at least 80% by weight. It is allowed to coordinate the manufacturer with the consumer, the production of rubble from gravel with the content of crushed grains of at least 60%.
By a change in N 3, approved by the Resolution of the State Assembly of the Russian Federation of June 3, 2002 N 32, Clause 4.3.2 of this GOST introduced amended from July 1, 2002.
See the text of the point in the previous edition
4.3.2 The shape of grains of rubble and gravel is characterized by the grain content of a plate (lamb) and a needle-shaped form.
The crushed stone, depending on the content of plate and needle-shaped grains, is divided into five groups that must match the specified in Table 2.
table 2
Note - In terms of the coordination of the manufacturer with the consumer, the production of rubble from the erupted rocks containing SV is allowed. 50%, but not more than 65% of the grains of the plate (lamb) and the needle form.
4.3.3 Gravel should not contain grains with a plate and needle form more than 35% by weight.
4.4 Strength
4.4.1 The strength of rubble and gravel is characterized by a brand determined by the crushed ground drum (gravel) during compression (crushing) in the cylinder.
Crushed stone and gravel, intended for the construction of highways, characterize the abrasion brand in the shelf drum.
4.4.2 Marks for crushed stone sweatshirts from sedimentary and metamorphic rocks must comply with the requirements specified in Table 3, and the rubble stamps from the erupted rocks in Table 4.
Table 3.
Stamp on the scrambledness of rubble from sedimentary and metamorphic breeds | Mass loss when testing rubble,% | |
---|---|---|
in dry condition | in saturated water | |
1200 | Up to 11 included. | Up to 11 included. |
1000 | St. 11 to 13 | St. 11 to 13 |
800 | St. 13 to 15 | St. 13 to 15 |
600 | St. 15 to 19 | St. 15 to 20 |
400 | St. 19 to 24 | St. 24 to 28 |
300 | St. 24 to 28 | St. 28 to 28 |
200 | St. 28 to 35 | St. 38 to 54 |
Table 4.
It is allowed to determine the brand of rubble from sedimentary and metamorphic rocks both in dry and in saturated water.
In case of incoming grades for fracture, the strength is evaluated according to the results of the test in saturated water.
Stamps on the crushed stone of gravel and gravel must comply with the requirements specified in Table 5.
Table 5.
4.4.3 The abrasion brands of rubble and gravel must comply with the requirements specified in Table 6.
Table 6.
Table 7.
4.6 frost resistance
4.6.1 Frost resistance of rubble and gravel characterize the number of cycles of freezing and thawing, in which the percentage losses by weight of rubble and gravel do not exceed the set values.
It is allowed to evaluate the frost resistance of rubble and gravel by the number of saturation cycles in sodium sulfate and drying solution. In case of incomprehension of brands, frost resistance is assessed by freezing and thawing test.
4.6.2 Crushed stone and frost resistance gravel are divided into the following stamps: F15; F25; F50; F100; F150; F200; F300; F400.
Frost resistance indicators of rubble and gravel when testing freezing and thawing or saturation in sodium sulfate solution and drying must match the specified in Table 8.
Table 8.
Type of test | Mark for frost resistance rubble and gravel | |||||||
---|---|---|---|---|---|---|---|---|
F15 | F25 | F50 | F100 | F150 | F200 | F300 | F400 | |
Freezing-thawing: | ||||||||
number of cycles | 15 | 25 | 50 | 100 | 150 | 200 | 300 | 400 |
10 | 10 | 5 | 5 | 5 | 5 | 5 | 5 | |
Saturation in sodium sulfate solution - Drying: | ||||||||
number of cycles | 3 | 5 | 10 | 10 | 15 | 15 | 15 | 15 |
loss of mass after testing,%, no more | 10 | 10 | 10 | 5 | 5 | 3 | 2 | 1 |
4.8 Availability of harmful components and impurities
4.8.1 Crushed stone from the minimal reverence and accommodating breeds and substandard waste of mining enterprises for the processing of ores (black, non-ferrous and rare metallic industry) and non-metallic minerals of other industries should be resistant against all types of decays.
Table 9.
Note - It is allowed in crushed stone grades of 800 and higher from the erupted, metamorphic and sedimentary rocks, an increase in 1% of the content of dust particles under the following conditions:
- if the geological exploration of the field establishes the absence of clay and merghelistic inclusions and interlayers in the initial rock;
- Upon presentation by the enterprise, the manufacturer's conclusion of a specialized laboratory on the absence of clay minerals in particles of less than 0.05 mm.
Table 10.
The stability of the rubble structure against all types of decays must comply with the requirements specified in Table 11.
Table 11.
4.8.2 Crushed stone and gravel must be resistant to exposure ambient. Crushed stone and gravel, intended for use as aggregates for concrete, should have resistance to chemical exposure to cement alkalis.
The resistance of rubble and gravel is determined by the mineral-petrographic composition of the initial rock and the content of harmful components and impurities that reduce the durability of concrete and corrosive reinforcement reinforcement and structures.
The list of harmful components and their maximum allowable content is given in Appendix A.
A change in N 2, approved by the Resolution of the Gosstroya of the Russian Federation of December 4, 2000, N 115, amendments made in action from April 1, 2001 were made to clause 4.9 of this GOST
See the text of the point in the previous edition
4.9 In the production of rubble and gravel, their radiation-hygienic assessment should be carried out, according to the results of which the scope is established. Crushed stone and gravel depending on the values \u200b\u200bof the total specific effective activity of natural radionuclides A_Eff * (1) Apply:
- with and eff up to 370 BK / kg - in newly under construction of residential and public buildings;
- With the effect of sv. 370 to 740 BC / kg - for road construction within the territory settlements and prosecution zones, as well as during the construction of industrial buildings and structures;
- With the effect of sv. 740 to 1500 BC / kg - in road construction outside the settlements.
If necessary, in national norms operating in the state, the value of the specific effective activity of natural radionuclides can be changed within the limits of the norms mentioned above.
4.10 Crushed stone and gravel should not contain foreign clogging impurities.
4.11 Security established by the standard values \u200b\u200bof the quality indicators of rubble and gravel on grain composition (grain content of less than the smallest nominal size D and the greatest nominal size D) and the content of dust and clay particles should be at least 95%.
5. Rules of acceptance
5.1 Crushed stone and gravel should be accepted by the technical control of the manufacturer.
5.2 Acceptance and supply of rubble and gravel produce parties. The party is considered the amount of rubble (gravel) of one fraction (mixtures of fractions), established in the contract for the supply and at the same time shipped by one consumer in one railway composition or one vessel. When shipping by automotive parties, the amount of rubble (gravel) of one fraction (fraction mixtures) is considered to be shipped to one consumer during the day.
5.3 To verify compliance with the quality of rubble (gravel), the requirements of this standard carry out acceptance control and periodic tests.
Acceptance control at the manufacturing company is carried out daily by testing the combined sample of rubble (gravel) selected from each technological line. At acceptance control, determine:
- grain composition;
- the content of dust and clay particles;
- The content of grains of weak rocks.
By change N 2, approved by the Resolution of the Gosstroita of the Russian Federation of December 4, 2000 N 115, to paragraph 5.4. This GOST has made changes enacted from April 1, 2001.
See the text of the point in the previous edition
5.4 at periodic tests determine:
- once in 10 days - the content of grains of a plate and needle shape and the content of crushed grains in the crushed stone from the gravel and the content of the free fiber of asbestos in crushed parts of asbestos-containing rocks;
- once a quarter - strength and bulk density, stability of the structure against decays;
- Once a year - frost resistance and class of rubble (gravel) on the meaning of the specific effective activity of natural radionuclides, as well as at the request of consumers, the content of harmful components and impurities.
The value of the specific effective activity of natural radionuclides is determined, and the class of rubble and gravel is installed in specialized laboratories on certified gamma spectrometric installations or in the radiation metric laboratories of supervisory organs.
In the absence of data from geological exploration on radiation-hygienic assessment of the field and imprisonment of gravel and gravel, the manufacturer conducts a preliminary assessment of the developed areas of rocks directly in the career or rubble (gravel) in the warehouse of finished products in accordance with GOST 30108.
The strength, frost resistance of rubble and gravel, as well as the stability of the rubble structure against all types of decays, determine in each case a change in the properties of the feedstock (rock, albeit-mined rocks and waste industrial production).
In the absence of data from geological intelligence on the content of harmful components and impurities, the company conducts in specialized or accredited laboratories and testing centers by definition in products of reaction-capable rocks, the content of weak grains and impurities of the metal in crushed parts of black and non-ferrous metallurgy slags, slag and electrical insulating activity Properties of rubble for ballast layer of the railway track.
A change in N 2, approved by the Resolution of the Russian Federation of December 4, 2000 N 115, paragraph 5.5. This GOST has made changes enacted from April 1, 2001.
See the text of the point in the previous edition
5.5 The selection and preparation of samples of rubble (gravel) for quality control at the manufacturing company is carried out in accordance with the requirements of GOST 8269.0, GOST 8269.1.
Control points for preliminary estimates of rocks and class of rubble and gravel are chosen according to GOST 30108.
5.6 Consumer with a control check for the compliance of rubble (gravel) with the requirements of this standard should apply the sampling procedure in paragraph 5.7-5.10.
By change N 2, approved by the Resolution of the Russian Federation of December 4, 2000 N 115, paragraph 5.7. This GOST has made changes enacted from April 1, 2001.
See the text of the point in the previous edition
5.7 The number of point samples taken by the consumer to control the quality of rubble (gravel) in each batch depending on the volume of the party must be at least:
up to 350 m³ ...................................... 10
sv. 350 to 700 m³ ............................... 15
sv. 700 m³ ........................................ 20
From point samples form a combined trial, which characterizes the controlled batch. Averaging, reduction and preparation of the test to the test is carried out according to GOST 8269.0, GOST 8269.1.
5.8 To control the quality of rubble and gravel supplied by rail, point samples are taken from the unloading of cars from the rubble stream (gravel) on the belt conveyors used to transport it to the consumer warehouse. With the unloading of each distinguished car, five point samples are taken at equal intervals. The number of wagons is determined, taking into account the preparation of the required number of point samples on 5.8. Wagons are chosen by instructions. If the party consists of one car, with discharge, five point samples are taken from which the combined sample is obtained.
If the conveyor transportation is not used when unloading wagons, then the point samples are taken directly from the wagons. For this, the surface of the rubble (gravel) in the car is aligned and at the point of selection, the holes are torn off by a depth of 0.2-0.4 m. The selection points must be located in the center and in four corners of the car, while the distance from the side of the carrot to the sampling points should Being at least 0.5 m. From the holes of the sample, rubble is selected by the scoop, moving it from the bottom up along the wall of the well.
5.9 To control the quality of rubble (gravel) supplied by water transport, point samples are selected during the unloading of ships.
In the case of applied when the belt conveyors are unloading, the point samples are taken at equal time intervals from the rubble stream (gravel) on the conveyors. When the vessels are unloading, the spot samples are selected by a scoop at equal intervals of time as unloading directly from the newly formed surface of rubble (gravel) in the vessel, and not from the wells.
5.10 To control the quality of rubble (gravel), shipped by road, point samples are selected during car unloading.
In the case of applied during the discharge of rubble (gravel) of the tape conveyors, point samples are taken from the rubble stream on the conveyors. When unloading each car, select one point sample. The number of cars takes into account the preparation of the required number of point samples by 5.7. Cars are chosen by instructions of the consumer.
If the party consists of less than ten cars, then rubble samples are taken from each car.
If the conveyor transport during the unloading of cars does not apply, the point samples are selected directly from cars. For this, the surface of the crushed stone (gravel) in the car is aligned, in the center of the body, they take off the hole with a depth of 0.2-0.4 m. From the hole, the sample of rubble (gravel) is selected by a scoop, moving it upwards along the wells.
5.11 The amount of rubble supplied (gravel) is determined by volume or mass. Screwdow (gravel) is measured in cars and cars. Crushed stone (gravel), shipped in cars or cars, weigh on rail or car scales. The mass of rubble (gravel) shipped in the courts is determined by the sediment of the vessel. The amount of rubble (gravel) from units of mass in a unit of volume is recalculated by the value of the bulk density of rubble (gravel), determined by its humidity during the shipment.
The volume of rubble (gravel) supplied in the car or car is determined by its measurement, the resulting volume is multiplied by the seal coefficient (gravel) when transporting it, which depends on the loading method, transportation range, grain composition. The maximum permissible value of humidity and the coefficient of the seal, which should not exceed 1.10, are established in the contract for the supply.
5.13 The results of acceptance control and periodic tests lead in a quality document indicating:
- the name of the manufacturer and its address;
- the number and date of issuing a document;
- the name and address of the consumer;
- party number and number of rubble (gravel);
- Room of the car or the number of the vessel and the number of the overhead;
- grain composition of rubble (gravel);
- the content of grains of a plate (lamb) and a needle form;
- the content of crushed grains in crushed it from gravel;
- Clay content in lumps;
- brand rubble (gravel) for strength (swelling);
- the content of grains of weak rocks;
- frost resistance rubble (gravel);
- bulk density rubble (gravel);
- specific activity of natural radionuclides of rubble (gravel);
- stability of the structure of rubble against decays;
- the content of harmful components and impurities;
- Designation of this standard.
In addition, at the request of the consumer, the document indicates the mineral and petrographic characteristic of gravel and rock, from which rubble, as well as true and middle density, porosity, voidness and water absorption.
6. Monitoring methods
A change in N 2, approved by the Resolution of the Gosstroita of the Russian Federation of December 4, 2000 N 115, paragraph 6.1. This GOST has made changes enacted from April 1, 2001.
See the text of the point in the previous edition
6.1 Tests of rubble and gravel are carried out according to GOST 8269.0, GOST 8269.1.
When determining the grain composition of rubble and gravel, it is allowed to use a sieve with holes 70 mm before equipping enterprises with sieves with holes 80 mm.
A change in N 2, approved by the Resolution of the Gosstroita of the Russian Federation of December 4, 2000 N 115, paragraph 6.2. This GOST has made changes enacted from April 1, 2001.
See the text of the point in the previous edition
6.2 Stability of the structure of rubble against all types of decays is determined according to GOST 8269.0.
6.3 The specific effective activity of natural radionuclides in crushed stone and gravel is determined by the gamma spectrometric method according to GOST 30108.
6.4 The provision of the standard contents established by the standard grain grain and grain grain size of less smallest nominal size D and the greatest nominal size D and the content of dust and clay particles are characterized by the ratio of the number of replaceable samples, which are the quality indicators of which exceed the normative values, to the total number of replacement samples selected and Tested for one block.
7. Transportation and storage
7.1 Crushed stone and gravel transport in bulk in vehicles of any kind according to the existing rules for the carriage of goods and the technical conditions of loading and fastening of goods approved by the Ministry of Railways, the rules of cargo transportation by road and water transport.
When transporting rubble and gravel railway cars should be loaded taking into account the full use of their carrying capacity.
7.2 Crushed stone and gravel stored separately according to fractions and mixtures of fractions under conditions that protect them from clogging and pollution.
Appendix A.
(mandatory)
Content of harmful components and impurities
1. To the main components that reduce the strength and durability of concrete include inclusions:
- clay minerals (montmorillonite, kaolinitis, etc.);
- mica and hydroellud and other layered silicates;
- asbestos;
- organic substances (coal, lignite, combustible shale, humus acids, etc.);
- minerals unstable to weathering processes (chlorite, zeolite, apatite, nepheline, phosphorite).
2. The main components causing the deterioration in the quality of the surface and the internal corrosion of concrete include inclusions:
- breeds and minerals containing amorphous species of silicon dioxide (chalcedony, opal, etc.);
- sulfur-containing breeds and minerals (pyrite, marcasit, pyrrhotite and other sulphides, as well as plaster, anhydrite and other sulfates);
- breeds and minerals containing oxides and iron hydroxides (magnetite, gentite, etc.);
- micro, hydroellud and other layered silicates.
3. To the main components causing corrosion of reinforcement in concrete include inclusions:
- halogen-containing minerals (pyrite, marcasit, pyrrhotite and other sulphides, plaster, anhydrite and other sulfates).
4. Crushed stone and gravel are used in concrete without restrictions, if the content of breeds and minerals attributable to harmful components, not more than:
- 50 mmol / l of amorphous species of silicon dioxide soluble in alkalis;
- 1.5% by weight of sulfates (gypsum, anhydrite) and sulphides, except for pyrite (marcasit, pyrrhotite, gypsum, anhydrite, etc.) in terms of SO 3;
- 4% by weight of pyrite;
- 15% in terms of layered silicates, if mica, hydroslides, chlorites and others are breeding minerals;
- 0.1% by weight of halide compounds (Galit, Sylvin, etc., including water-soluble chlorides) in terms of chlorine ion;
- 0.25% by weight of the free fibers of asbestos;
- 1.0% by weight of coal and wood residues;
- 10% in terms of each of the listed breeding minerals (magnetite, gheetite, hematite, etc., apatite, nepheline, phosphorite) or their sum in the amount of no more than 15%.
Appendix B.
(information)
A change in N 2, approved by the Resolution of the Gosstroita of the Russian Federation of December 4, 2000 N 115, an application b of this GOST is excluded
Preface
1. Developed by the Institute of Vnipperromyrius with the participation of Vnikodezbeton, Niizba, Somponia Russian Federation
Made by Gosstroke Russia
2. Adopted by the Interstate Scientific and Technical Commission for Standardization and Technical Registration in Construction (MNTKS) November 10, 1993
3. Instead of GOST 8267-82, GOST 8268-82, GOST 10260-82, GOST 23254-78, GOST 26873-86 4. Entered into force on January 1, 1995 as the State Standard Raspanic Federation by a decree of the Gosstroy of Russia on June 17, 1994 № 18-43
5. Reprint. October 1996
Change No. 1 has been made, adopted by the Interstate Scientific and Technical Commission for Standardization, Technical Registration and Certification in Construction (MNTKS) 10.12.97 Entered into force 01.04.98 and published in IUS No. 5 1998
1 area of \u200b\u200buse
This standard applies to crushed stone and gravel from rocks with an average grain density from 2.0 to 3.0 g / cm3, used as aggregates for heavy concrete, as well as for road and other types of construction work.
The standard does not apply to crushed stone and gravel for the ballast layer of the railway track and decorative crushed stone.
The requirements set out in paragraphs 4.2-4.9, sections 5 and 6 are mandatory.
Technical conditions
GOST 8269-87 Crushed stone from natural stone, gravel and gravel crushed stone for construction work.
Test methods
GOST 30108-94 Building materials and products. Determination of the specific effective activity of natural radionuclides.
3 Definitions
This standard applies the following terms.
Crushed stone from rocks - inorganic grainy bulk material with grains of sv. 5 mm, obtained by crushing rocks, gravel and boulders, minorly produced reverend and accommodating rocks or substandard waste of mining enterprises for the processing of ores (black, colored and rare metallurgical industries) and non-metallic minerals of other industries and subsequent rushing products of crushing.
Gravel from rocks - inorganic grainy bulk material with grains of sv. 5 mm, obtained by harsh natural gravel and sand mixtures.
4 Technical requirements
4.1 Crushed stone and gravel should be manufactured in accordance with the requirements of this standard for technological documentation approved by the manufacturer.
4.2. Main parameters and sizes
4.2.1 Crushed stone and gravel produced in the form of the following main fractions: from 5 (3) to 10 mm; sv. 10 to 20 mm; sv. 20 to 40 mm; sv. 40 to 80 (70) mm and a mixture of fractions from 5 (3) to 20 mm. In coordination of the manufacturer with the consumer produced crushed stone and gravel in the form of fractions from 10 to 15 mm; sv. 15 to 20 mm; sv. 80 (70) to 120 mm and sv. 120 to 150 mm, as well as mixtures of fractions from 5 (3) to 15 mm; sv. 5 (3) to 40 mm; sv. 20 to 80 (70) mm.
4.2.2 Full residues on control sints in harassment of rubble and gravel fractions from 5 (3) to 10 mm, sv. 10 to 20 mm, sv. 20 to 40 mm, sv. 40 to 80 (70) mm and a mixture of fractions from 5 (3) to 20 mm and from 5 to 15 mm should correspond to those specified in Table 1, wherees - the smallest and largest rated grain sizes.
Table 1.
4.2.3 For rubble and gravel fractions of St. 80 (70) to 120 mm and sv. 120 to 150 mm, as well as for a mixture of fractions from 5 (3) to 40 mm and st. 20 to 80 (70) mm Full residues on control sines with a diameter should satisfy specified in Table 1, and the ratio of fractions in the mixtures is established by coordinating the manufacturer with the consumer in accordance with the regulatory documents for the use of these mixtures for construction work. 4.2.4. Full residues on control sints when rushing rubble and gravel fractions from 10 to 15 mm and sv. 15 to 20 mm should be:
from 85 to 100% | |||||||
4.3.1 Crushed stone from gravel should contain crushed grains in an amount of at least 80% by weight. It is allowed to coordinate the manufacturer with the consumer, the production of rubble from gravel with the content of crushed grains of at least 60%.
4.3.2 The shape of grains of rubble and gravel is characterized by the grain content of a plate (lamb) and a needle-shaped form.
The crushed stone, depending on the grain content of a plate and needle form, is divided into four groups that must match the specified in Table 2.
Table 2.
In percentage by weight
4.3.3 Gravel should not contain grains with a plate and needle form more than 35% by weight.4.4 Strength
4.4.1 The strength of rubble and gravel is characterized by a brand determined by the crushed ground drum (gravel) during compression (crushing) in the cylinder.
Crushed stone and gravel, intended for the construction of highways, characterize the abrasion brand in the shelf drum.
4.4.2 Marks for crushed stone sweatshirts from sedimentary and metamorphic rocks must comply with the requirements specified in Table 3, and the rubble stamps from the erupted rocks in Table 4.
Table 3.
Table 4.
It is allowed to determine the brand of rubble from sedimentary and metamorphic rocks both in dry and in saturated water.In case of incoming grades for fracture, the strength is evaluated according to the results of the test in saturated water.
Stamps on the crushed stone of gravel and gravel must comply with the requirements specified in Table 5.
Table 5.
4.4.3 The abrasion brands of rubble and gravel must comply with the requirements specified in Table 6.
Table 6.
Table 7.
4.6 frost resistance4.6.1 Frost resistance of rubble and gravel characterize the number of cycles of freezing and thawing, in which the percentage losses by weight of rubble and gravel do not exceed the set values.
It is allowed to evaluate the frost resistance of rubble and gravel by the number of saturation cycles in sodium sulfate and drying solution. In case of incomprehension of brands, frost resistance is assessed by freezing and thawing test.
4.6.2 Crushed stone and frost resistance gravel are divided into the following stamps: F15; F25; F50; F100; F150; F200; F300; F400.
The frost resistance indicators of rubble and gravel when testing freezing and thawing or saturation in sodium sulfate solution and drying should correspond to the specified in Table. eight.
Table 8.
Type of test | Mark for frost resistance rubble and gravel |
|||||||
Freezing-thawing: number of cycles | ||||||||
Saturation in sodium sulfate solution - Drying: number of cycles | ||||||||
Mass loss after testing,%, no more: |
Table 9.
In percentage by weight
View of rock and brand for crushed stone and gravel | |
Crushed stone from erupted and metamorphic brands: | |
from 600 to 800 included. | |
Crushed stone grades: | |
from 600 to 1200 included. | |
Crushed stone from gravel and boulders and gravel brands: | |
NOTE - It is allowed in crushed steel grades of 800 and above from the erupted, metamorphic and sedimentary rocks, an increase in 1% of dust particles under the following conditions: - if the geological exploration of the field establishes the absence of clay and merghelistic inclusions and interlayers in the initial rock; - Upon presentation by the enterprise, the manufacturer's conclusion of a specialized laboratory on the absence of clay minerals in particles of less than 0.05 mm. |
Table 10.
In percentage by weight
4.8 Availability of harmful components and impurities
4.8.1 Crushed stone from the minimal enclose-in enclosing rocks and substandard waste of mining enterprises for the processing of ores (black, non-ferrous and rare metallurgical industries) and non-metallic minerals of other industries should be resistant against all types of decays.
The stability of the rubble structure against all types of decays must comply with the requirements specified in Table 11.
Table 11.
4.8.2 Crushed stone and gravel should be resistant to environmental impact. Crushed stone and gravel, intended for use as aggregates for concrete, should have resistance to chemical exposure to cement alkalis.
The resistance of rubble and gravel is determined by the mineral-petrographic composition of the initial rock and the content of harmful components and impurities that reduce the durability of concrete and corrosive reinforcement reinforcement and structures.
The list of harmful components and their maximum allowable content is given in Appendix A.
4.9 In the production of rubble and gravel, their radiation-hygienic assessment should be carried out, according to the results of which the scope is established. Crushed stone and gravel depending on the values \u200b\u200bof the total specific effectively activity of natural radionuclides: - at up to 370 BC / kg - in newly under construction of residential and public buildings;
- With sv. 370 to 740 BC / kg - for road construction within the territory
settlements and prosecution zones, as well as during the construction of industrial buildings and structures;
with sv. 740 to 2800 BC / kg - in road construction outside settlements.
(Modified edition, change No. 1).
4.10 Crushed stone and gravel should not contain foreign clogging impurities.
4.11 The security established by the standard values \u200b\u200bof the quality indicators of rubble and gravel in grain composition (grain content of less than the smallest nominal size and the greatest nominal size) and the content of dust and clay particles should be at least 95%.
5 Rules acceptance
5.1 Crushed stone and gravel should be accepted by the technical control of the manufacturer.
5.2 Acceptance and supply of rubble and gravel produce parties. The party is considered the amount of rubble (gravel) of one fraction (mixtures of fractions), established in the contract for the supply and at the same time shipped by one consumer in one railway composition or one vessel. When shipping by automotive parties, the amount of rubble (gravel) of one fraction (fraction mixtures) is considered to be shipped to one consumer during the day.
5.3 To verify compliance with the quality of rubble (gravel), the requirements of this standard carry out acceptance control and periodic tests.
Acceptance control at the manufacturing company is carried out daily by testing the combined sample of rubble (gravel) selected from each technological line. At acceptance control, determine:
- grain composition;
- The content of dust and clay particles;, br\u003e
- The content of grains of weak rocks.
5.4 During periodic tests, it is determined by: - \u200b\u200bonce in 10 days - the content of grains of the plate and needle shape and the content of crushed grains in the crushed stone of gravel;
- once a quarter - strength and bulk density, stability of the structure against decays;
- Once a year - frost resistance and class of rubble (gravel) on the meaning of the specific activity of natural radionuclides.
The value of the specific effective activity of natural radionuclides is determined, and the class of rubble and gravel is installed in specialized laboratories on certified gamma spectrometric installations or in the radiation metric laboratories of supervisory organs.
In the absence of data from geological exploration on radiation-hygienic assessment of the field and imprisonment of gravel and gravel, the manufacturer conducts a preliminary assessment of the developed areas of rocks directly in the career or rubble (gravel) in the warehouse of finished products in accordance with GOST 30108.
The strength, frost resistance of rubble and gravel, as well as the stability of the rubble structure against all types of decays, is determined in each case a change in the properties of the developed rock.
5.5 Selection and preparation of samples of rubble (gravel) for quality control at the manufacturing company is carried out in accordance with the requirements of GOST 8269.
Control points for preliminary estimates of rocks and class of rubble and gravel are chosen according to GOST 30108.
5.6 Consumer with a control check for the compliance of rubble (gravel) with the requirements of this standard should be applied in PP. 5.7-5.10 Sampling procedure.
5.7 The number of point samples taken by the consumer to control the quality of rubble (gravel) in each batch depending on the volume of the party must be at least:
up to 350 m. . . . . . . . . . 10
sv. 350 to 700 m. . . . . . . .
15
"700 m.........
20
From point samples form a combined trial, which characterizes the controlled batch. Averaging, reduction and preparation of the test to the test is carried out according to GOST 8269.
5.8 To control the quality of rubble and gravel supplied by rail, point samples are taken from the unloading of cars from the rubble stream (gravel) on the belt conveyors used to transport it to the consumer warehouse. With the unloading of each distinguished car, five point samples are taken at equal intervals. The number of wagons is determined, taking into account the preparation of the required number of point samples according to paragraph 5.8. Wagons are chosen by instructions. If the party consists of one car, with discharge, five point samples are taken from which the combined sample is obtained.
If the conveyor transportation is not used when unloading wagons, then the point samples are taken directly from the wagons. For this, the surface of the rubble (gravel) in the car is aligned and at the point of selection, the holes are torn off by a depth of 0.2-0.4 m. The selection points must be located in the center and in four corners of the car, while the distance from the side of the carrot to the sampling points should Being at least 0.5 m. From the holes of the sample, rubble is selected by the scoop, moving it from the bottom up along the wall of the well.
5.9 To control the quality of rubble (gravel) supplied by water transport, point samples are selected during the unloading of ships.
In the case of applied when the belt conveyors are unloading, the point samples are taken at equal time intervals from the rubble stream (gravel) on the conveyors. When the vessels are unloading, the spot samples are selected by a scoop at equal intervals of time as unloading directly from the newly formed surface of rubble (gravel) in the vessel, and not from the wells.
5.10 To control the quality of rubble (gravel), shipped by road, point samples are selected during car unloading.
In the case of applied during the discharge of rubble (gravel) of the tape conveyors, point samples are taken from the rubble stream on the conveyors. When unloading each car, select one point sample. The number of cars takes into account the preparation of the required number of point samples on 5.7. Cars are chosen by instructions of the consumer. If the party consists of less than ten cars, then rubble samples are taken from each car.
If the conveyor transport during the unloading of cars does not apply, the point samples are selected directly from cars. For this, the surface of the crushed stone (gravel) in the car is aligned, in the center of the body, they take off the hole with a depth of 0.2-0.4 m. From the hole, the sample of rubble (gravel) is selected by a scoop, moving it upwards along the wells.
5.11 The amount of rubble supplied (gravel) is determined by volume or mass. Screwdow (gravel) is measured in cars and cars.
Crushed stone (gravel), shipped in cars or cars, weigh on rail or car scales. The mass of rubble (gravel) shipped in the courts is determined by the sediment of the vessel. The amount of rubble (gravel) from units of mass in a unit of volume is recalculated by the value of the bulk density of rubble (gravel), determined by its humidity during the shipment.
The volume of rubble (gravel) supplied in the car or car is determined by its measurement, the resulting volume is multiplied by the seal coefficient (gravel) when transporting it, which depends on the loading method, transportation range, grain composition. The maximum permissible value of humidity and the coefficient of the seal, which should not exceed 1.10, are established in the contract for the supply.
5.13 The results of acceptance control and periodic tests lead in a quality document indicating:
- the name of the manufacturer and its address;
- the number and date of issuing a document;
- the name and address of the consumer;
- party number and number of rubble (gravel);
- Room of the car or the number of the vessel and the number of the overhead;
- grain composition of rubble (gravel);
- the content of grains of a plate (lamb) and a needle form;
- the content of crushed grains in crushed it from gravel;
- Clay content in lumps;
- brand rubble (gravel) for strength (swelling);
- the content of grains of weak rocks;
- Frost resistance of rubble (gravel);, br\u003e - bulk density of rubble (gravel);
- specific activity of natural radionuclides of rubble (gravel);
- stability of the structure of rubble against decays;
- the content of harmful components and impurities;
- Designation of this standard.
In addition, at the request of the consumer, the document indicates the mineral-petrographic characteristic of gravel and rock, from which rubble, as well as true and medium density, porosity, voidness and water absorption.
6 Monitoring methods
6.1 Tests of rubble and gravel are carried out according to GOST 8269.
When determining the grain composition of rubble and gravel, it is allowed to use a sieve with holes 70 mm before equipping enterprises with sieves with holes 80 mm.
6.2 Stability structure against all types of decays is determined according to GOST 3344. 6.3 The specific effective activity of natural radionuclides in crushed stone and gravel is determined by the gamma spectrometric method according to GOST 30108.
6.4 Provision established by the standard value of the contents in crushed stone and grain grain size less than the smallest nominal size and the greatest nominal size and content of dust and clay particles are characterized by the ratio of the number of replacement samples, which are the quality indicators exceeding the normative values, to the total number of replaceable samples selected and tested in For one block.
7 Transportation and storage
7.1 Crushed stone and gravel transport in bulk in vehicles of any kind according to the existing rules for the carriage of goods and the technical conditions of loading and fastening of goods approved
Ministry of Railways, the rules for transportation of goods by road and water transport. When transporting rubble and gravel railway cars should be loaded taking into account the full use of their carrying capacity.
7.2 Crushed stone and gravel stored separately according to fractions and mixtures of fractions under conditions that protect them from clogging and pollution.
Appendix A.
(mandatory)
1 To the main components that reduce the strength and durability of concrete include inclusions:
- clay minerals (montmorillonite, kaolinitis, etc.);
- mica and hydroellud and other layered silicates;
- asbestos;
- organic substances (coal, lignite, combustible shale, humus acids, etc.);
- minerals unstable to weathering processes (chlorite, zeolite, apatite, nepheline, phosphorite).
2 To the main components causing deterioration in the quality of the surface and the internal corrosion of concrete include inclusions:
- breeds and minerals containing amorphous species of silicon dioxide (chalcedony, opal, etc.);
- sulfur-containing breeds and minerals (pyrite, marcasit, pyrrhotite and other sulphides, as well as plaster, anhydrite and other sulfates);
- breeds and minerals containing oxides and iron hydroxides (magnetite, gentite, etc.);
- micro, hydroellud and other layered silicates.
3 The main components causing corrosion of reinforcement in concrete include inclusions: - halogen-containing minerals (pyrite, marcasit, pyrrhotite and other sulfides, gypsum, anhydrite and other sulfates).
4 Crushed stone and gravel are used in concrete without restrictions, if the content of breeds and minerals attributable to harmful components, not more than:
- 50 mmol / l of amorphous species of silicon dioxide soluble in alkalis;
- 1.5% by weight of sulfates (gypsum, anhydrite) and sulphides, except for pyrite (marcippet, pyrrhotite, gypsum, anhydrite, etc.) in terms of SO;
- 4% by weight of pyrite;
- 15% in terms of layered silicates, if mica, hydroslides, chlorites and others are breeding minerals;
- 0.1% by weight of halide compounds (Galit, Sylvin, etc., including water-soluble chlorides) in terms of chlorine ion;
- 0.25% by weight of the free fibers of asbestos;
- 1.0% by weight of coal and wood residues;
- 10% in terms of each of the listed breeding minerals (magnetite, gheetite, hematite, etc., apatite, nepheline, phosphorite) or their sum in the amount of no more than 15%.
GOST 8267-93 - get by crushing natural granite.
In the careers, the granite is a solid monolithic rock, which is first exploded, then the harvesters resulting from explosion will be crushed in a special crushing machine, after which they get granite crusp . Further Granite crusp Sail, separating on the fraction. The smaller the fraction granite rubble (that is, the more work on crushing), the crushes is more expensive.
Same crushed stone granitis mining in a career by sieving the breed. IN granite rubblewe normalize the content of grains of plate (lamb) and needle forms. The grains of lamellar and needle forms include such grains, thickness or width of which are less than three times or more.
The grade of the strength of the granite rubble from 1200 to1400.
Granite is a solid rock of the grain structure.
Granite breed - characteristic of the top of the continental earth crust, formed throughout the entire geological history of our planet, the most common mountain rock on Earth. In other words, this is a magma's emission on the surface of the Earth, which has cooled and hardened.
Granite consists of well-formed crystals polespota, quartz, mica, etc. It is influenced by the composition of field spatts and mica. Depending on their compositions, granite can be red, pink or gray. Based on these colors, the granite crushed stone may have many shades.
In the form of grains crushed stone granitis They are divided into three groups (grain content of plate and needle forms to% by weight): Cuboid up to 15, improved from 15 to 25, the usual from 25 to 35 a mixture of cubic grains gives the most dense packaging.
Availability B. granite rubble The grains of lamellar and needle forms leads to an increase in the interzraine emptiness in the mixture. Cuboid grains have greater durability than grains with lamellar and needle forms.
Fractions of granite rubble.
Granite explorer 0-5 mm. and granite crumb 2-5 mm. Most It is used as an antgollectual agent, in the production of concrete products and in decorative purposes.
3-10 mm. and 5-10 mm. Small fraction of granite rubble . It goes to the production of concrete and designs from it, as well as applied to decorative purposes. A rather deficient fraction is brought mainly under the order.
5-20 mm. Small fraction of granite rubble . It goes to the production of concrete, designs from it and on foundation work. The most consumed fraction of rubble.
20-40 mm. The average fraction of granite rubble . It goes to the production of concrete, structures from it and on foundation work, also used during drainage work.
40-70 mm. Large fraction of granite rubble . It goes to the production of concrete, massive structures from it and on working with a large volume of concrete.
100 mm. This fraction is called Granite Booth. Pretty deficient fraction of rubble and bring it to Moscow to order in large volume. Granite boot is used in decorative purposes, for decoration of pools, ponds, river coast, drainage.
Price crushed stone granita
Granite crushed stone is high demand due to its excellent performance characteristics.
Granite crushed stone is obtained during the crushing of various rocks. It is the most popular and indispensable material in construction. Such material has high strength during operation and ease during processing. Crushed stone is also valued thanks to its frost resistance.
Price crushed stone granita It is established depending on the quality of its fraction. Most often, the smallest fraction is estimated more expensive. It takes a lot of time on its production and more work is spent.
There are several fractions of granite rubble. The main are: 5-10 mm, 5-20 mm, as well as 10-15 mm. Crushed stone fraction 5-20 is used in the process of laying bridge structures, road coatings, foundations and is the most sought-after.
This material has many advantages. It interacts well with various adhesive substances. Buy granite crusp High quality and necessary faction can be in our online store. This material is in demand, because it has an attractive appearance. In addition, crushed stone does not require additional processing. It is also possible to use it in the most different areas Activities and for different purposes.
If there is a problem with independent export of material, our company can offer delivery. Price with shipping crushed stone granite Calculated individually.
Granite crusp
Granite crusp features excellent stability properties and technical characteristicsTherefore, its applications are constantly expanding. The main indicator of rubble is the size of the fractions, based on what, and the area of \u200b\u200buse is determined.
The above products are in high demand in the construction market today, therefore, the sales volumes of rubble are increasing every year.
Sale of rubble is carried out with the needs of each buyer, and crushed with delivery - This is one of mutually beneficial services, thanks to which, the customer receives this product in a timely manner to the object specified in the contract.
Crushed stone shipped, both wholesalers and according to a one-time order for individual needs. The quality of delivery of rubble and the low cost of this service ensure an increase in the customer base every year. For regular customers there is a flexible system of discounts.
In the company's catalog, you can familiarize yourself with the terms of the order and the implementation of this material, because rubble, the price of which is 100% compliance with its quality, is in demand in construction and other areas of production. We have proven themselves with reliable and proven partners, so buy crushed stone in our company and get the goods without delay - this best offer For those who draw their individual sites or large construction objects.