How is a wooden corner made on a four-sided machine. Price for a four-sided milling machine. Pros and cons of equipment
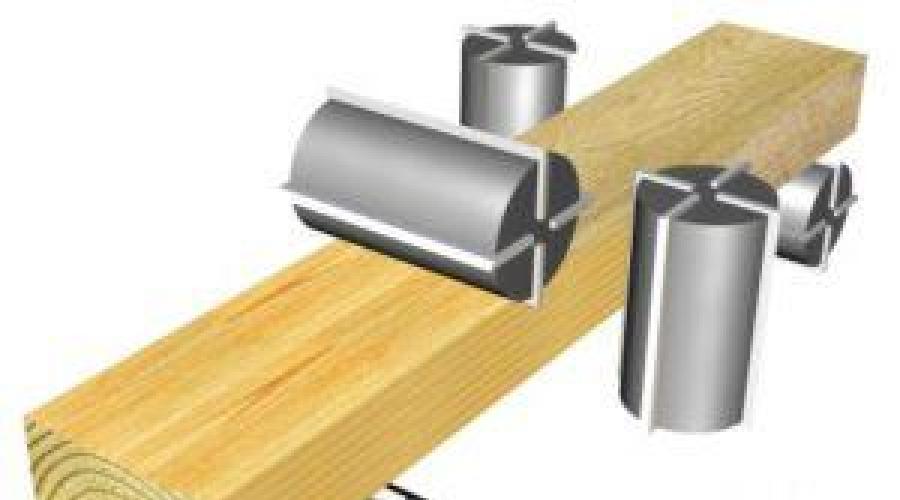
Read also
Lining as finishing material has been used for the past few decades, due to the presence of a huge number of undeniable advantages of this material. Among all the advantages, it should be noted the relatively low cost, as well as the ability to independently create this finishing material using special equipment - a 4-sided machine. There are quite a few models of such woodworking equipment, each with its own advantages and disadvantages. However, all industrial versions can be characterized by high cost. They are not suitable for domestic use. That is why many craftsmen decide to create with their own hands. Let's consider all the features of this work.
Why create a homemade four-sided machine?
There are several advantages of a home-made version of the machine:
- significant reduction in the cost of the finished material. If you use a homemade milling machine on wood, the cost of the resulting material is significantly reduced. To carry out finishing work on a site or in a private house, you can use a homemade lining, since it will be insignificantly inferior in quality to the one sold in the store;
- you can create additional income. Lining is needed by many, since this material is universal in use. Therefore, you should not think that after finishing the house, a homemade 4-sided woodworking machine is no longer needed;
- you can control the quality of the products with high precision. At the same time, changes can be made quickly and inexpensively. The advantage of a home-made design is that all parameters of its operation can be adjusted within a certain range if necessary;
- it is possible to use a four-sided machine that processes a workpiece from solid wood on 4 sides, it is possible to solve other problems, for example, it can be used to produce a bar.
The above points determine that many decide to independently create a four-sided machine that processes the workpiece on 4 sides.
Principle of operation
Considering the principle of operation of a typical machine that processes a workpiece on 4 sides, we note that it removes material over the entire width of the workpiece in one or more passes. The device carries out grinding from above and below, but at the same time it still forms the required profile on the sides. In this case, the formed side profile can be a groove, a thorn of various shapes. The type of profile obtained depends on the choice of the master.
Often, the body is rigidly attached to the base, which effectively dampens vibration, which significantly improves the quality of processing. However, there are also portable versions that are lightweight and dimensions... They can be used for installation in a garage or other room.
- an element configured for the correct feed of the workpiece;
- knot, which is represented by cutters with planing elements.
It is important to note that with poor quality of the mechanism feeding the workpiece, processing will be carried out at a low level of accuracy. Therefore, when making a homemade version, it is important to pay attention to this element of the woodworking machine.
When considering the cutting zone where the cutters are located, it is important to pay attention to their rotational speed. For high-quality processing, the rotational speed in the range from 4500 to 5000 rpm is characteristic. For domestic use, you can create a structure that will have a lower rate of rotation of the cutting tool.
Creating a homemade machine
A four-sided industrial machine is too expensive for many. Moreover, in some cases, it is simply not advisable to install it. That is why the solution is to create a homemade woodworking machine that can simultaneously remove material from 4 sides.
In order to create a four-sided woodworking machine with your own hands, you will need the following equipment and accessories:

As a rule, your four-sided machine is made depending on the installation conditions and processing characteristics. To carry out the work of preparing and assembling the necessary parts, you should acquire the following tools:
- Welding machine. The woodworking four-sided machine consists of a large number of metal elements. An example is the frame, which is made from corners and pipes. Please note that it is not recommended to use an ordinary threaded connection in this case, as there is a possibility of strong vibration. All elements of the structure under consideration must be rigidly connected to each other.
- A drill is used to create holes. In order to be able to adjust the height of the table, the holes for the adjusting bolts are created.
- The grinder is simply an indispensable tool when working with metal.
- If you provide for independent turning of pulleys and rollers, then you will need a four-sided lathe. You can order the manufacture of new parts, but it is cheaper to find suitable ones from various disassembled devices.
Manufacturing instructions are standard, depending on different working conditions, it can take from several days to months.
On the Stankoff.RU website you can buy four-sided woodworking machines from leading manufacturers: Beaver, Griggio, Logosol, Woodtec, ZMM Stomana and other Russian, Chinese, Taiwanese manufacturers. More than 123 models of 4-sided machines are available and on order at the best prices. Only great deals with detailed descriptions and photo. Check the prices with the managers.
4-sided machines. Benefits of using
In furniture production, natural wood is often used to create high-quality products. The processing of boards, bars is carried out using special four-sided machines, presented in our catalog.
The system allows you to obtain a high-quality part based on a wooden blank in one pass without additional processing. Modern four-sided woodworking machines offered by our company can withstand considerable loads. Thanks to the special design, all manipulations are carried out in the inner chamber of the machine. It does not vibrate when working. The maximum and minimum size of a part depends on the characteristics of a particular model.
The feeding belt is equipped with special lower and upper rollers, along which the workpiece moves, and side clamping strips that fix the board or timber.
The range of application of such equipment is wide:
- woodworking enterprises;
- furniture manufacture;
- production of wooden blanks for construction;
- production of molded products.
Using a four-sided machine, you can significantly speed up the production process, make it rational, efficient, cost-effective. Perfect planing quality is ensured by modern, multifunctional spindles. 4-spindle and 5-spindle machines are in demand.
Each of the four sides of the wood can be handled differently. Maximum depth planing depends on the specific model of equipment. Powerful motors keep the system running smoothly. The possibility of pushing the workpiece out during machining is excluded. The machine does not vibrate when machining massive large parts, thanks to the solid cast iron bed, which can withstand impressive loads.
All machines are offered as standard. The consumer can order additional options depending on specific needs.
Where to buy a four-sided machine
To buy a four-sided machine, you need to contact a reliable supplier of high quality equipment. The range of units is wide. It is advisable to use the recommendations of experts to make an informed choice. Additionally, delivery, assembly, commissioning services are provided. If necessary, you can purchase spare parts, additional components, which are offered in a wide range by the supplier.
Units of leading manufacturers have been in operation for a long time and are distinguished by a high degree of reliability and safety. When choosing four-sided machines, it is worth paying attention to such criteria as the maximum and minimum dimensions of the workpiece, the thickness of the removed layer, the depth of processing, the number of spindles.
Leasing services are offered. The client receives the equipment for temporary use with the possibility of subsequent redemption at the residual value. Many consumers are interested in such offers. Such services are different from equipment rental. Potential clients can learn more about all the possibilities by consulting the company's manager. It is possible to establish furniture and woodworking production by cooperating with leading suppliers of the appropriate equipment.
The processing of wooden blanks from four sides at once in one pass is carried out with four-sided woodworking machines. As a result of processing on such equipment, a wooden building blank is obtained, having a given geometry, the desired profile and the required surface quality. The main products of the four-sided apparatuses are wood blanks in the form of a floorboard, lining, timber and block-house, platband.
When buying such a device, you must definitely focus on the main specifications four-sided machines:
- interval between feeds of workpieces;
- the largest transverse dimensions of the supplied workpiece;
- number of working spindles;
- the total weight of the equipment;
- total power characteristics of the equipment.
According to the number of spindles, four-sided machine tools are divided into five-spindle machines and six-spindle machines. Sometimes there are devices of a four-spindle design and vice versa, multi-spindle.
Four-sided machine models
Domestic industry and foreign manufacturers supply Russian market a large number of four-sided machines with a wide variety of performance characteristics. These machines can perform work, both in semi-automatic mode, and follow the program entered into the CNC unit.
Among the large number of items of this machine park, the four-sided Beaver machines, which have been supplied to Russia since 2003, stand out. The series of these German machine tools contains from four to eight spindle heads. This design is the best suited for solving various problems in woodworking. They can perform both the calibration of wood products and the shaping of large cross-section timber for building houses. Moreover, the processing speed of such products reaches 60 meters per minute.
The area of application of Bauer machines are various workshops and enterprises of the carpentry and construction profile, where panels and glued beams are produced, molded products of various types for housing construction of a standard type, as well as woodworking in furniture production.
Products obtained on such equipment in one pass are very diverse. It all depends on the settings of the machine and the entered workpiece program.
The design features of the machines include excellent dynamic balancing of the work of the spindles, which are made of steel that has passed heat treatment... These main parts of the machines first undergo precision machining and then meticulous control. As a result, all parts and assemblies of the machine are of impeccable quality. In addition, before being installed on the machine, each spindle undergoes many hours of running-in on a special stand. The spindle mechanism is based on high precision bearings that do not require any maintenance during operation.
The Biewer 416 four-sided woodworking machine has excellent characteristics and operational parameters. It is used for profiling and surface machining of workpieces in one pass from four sides at once. The result of this work is a product of ideal geometry with a given surface finish.
Beaver 416 specifications:
- transverse dimensions of the workpiece to be processed 100x160 mm;
- number of working spindles - 4 pcs .;
- working feed of the workpiece during processing - up to 25 m / min;
- power consumed from the electrical network - 22 kW;
- machine weight - 2780 kg.
The working and feeding tables are heat treated, resulting in the highest metal strength. The surface of the tables is covered with a thick layer of chrome, due to which the wear resistance of these parts is very high. Also, as a result of polishing these surfaces, the workpieces easily slide over them, without spending much effort on feeding into the processing zone.
The bed is machined on high-precision Japanese CNC equipment. Many parts that affect the vibration resistance of the device during operation are made using ultra-precision casting technology.
Weinig machine
The diagram shows the basic structure of a four-sided machine
The German four-sided machine Weinig is used for profiling a wooden part from four sides at once. The processing of the wood stock takes place simultaneously with its profiling. Since everything is done in one technological operation, such equipment significantly reduces the time spent on processing one product, thereby increasing the efficiency of workers.
The advantage of the Weinig four-side planer over similar devices:
- the highest purity of processing the wood surface of the part;
- very high productivity;
- accuracy of product compliance with specified geometric parameters;
- ease of installation of equipment at the production site.
Weinig machine tools are used both in small-scale business and in the production of piece wood moldings. The impeccable cleanliness of the surface treatment allows the equipment to be used for the production of products from any wood species.
S-25 series machines
Special attention should be paid to the four-sided machine C-25, which is designed for the manufacture of high quality molded wood products. These are, first of all, floorboards, lining, planed beams, plinths and platbands. The source material for obtaining these products is edged board or timber. The productivity of the S-25 allows you to get up to 2 cubic meters of high-quality products per hour.
With continuous feeding, the product is processed immediately from four sides in a large size range. The device has a box-shaped frame made of cast iron, and on it are installed calipers with workpiece clamping rollers and a feed mechanism. This four-sided planer has steel table pads for positioning the wood during processing. The feeding mechanism is equipped with a variator, which allows smoothly changing the feeding speed in the range from 10 to 45 m / min.
Features of the C-25 device:
- below the drive hazel-grouse;
- high precision of all spindle units;
- the presence of feed rollers along the entire length of the workpiece;
- high feed rate of the workpiece;
- ease of setup and changeover of the machine.
Domestic equipment S-25 is widely used both as a four-sided lathe for lining and as a four-sided lathe for timber.
The four-sided machine C-26 differs from its analogue C25 in its higher productivity, increased up to 40 m / min and increased power, which makes it possible to remove the wood layer of the workpiece with a thickness of up to 10 mm in one pass. The operation of the apparatus is allowed by unskilled personnel, since its design is very simple and reliable. In addition, the use of low-quality workpieces is allowed for processing. An important feature of such equipment is the ability to operate it in an unsuitable room, sometimes directly under a canopy from rain and snow.
Sometimes good option for an entrepreneur is to buy a used four-sided wood machine model C-26. Even with a long operating time, this equipment allows you to get high quality products. The main bearing assemblies of domestic configuration can be easily restored, since all spare parts can be easily found on the equipment market. Usually the most consumable items are the planer knives, which many woodworking equipment suppliers offer in abundance.
Four-sided milling machines
The element of choice for equipment for the manufacture of molded wood products is the four-sided milling machine SKM M-412. It is used for four-sided processing of wood blanks with milling cutters. In this case, it is possible to create a product profile of a small depth. The main application of these devices is furniture production, the manufacture of various wooden stairs. Such equipment is usually used where high precision quality parameters are not required for products.
The price of the SCM four-sided woodworking machine is currently 1 million 76 thousand rubles.
Features of the design of the four-sided longitudinal milling machine SCM:
- separate electric motor for each work spindle;
- digital provision of positioning accuracy;
- high speed of working bodies;
- compact arrangement of units and mechanisms;
- adjustable feed of the workpiece.
Thanks to the centralized control panel, the device is very convenient and easy to use. Each of the spindles is controlled separately. Milling cutters for a four-sided machine are easy to buy by going to the websites of suppliers of woodworking equipment and accessories.
In addition to the four-sided equipment listed and described in the article, entrepreneurs use C-16 machines, Start machines and Griggio equipment. Any of these types of technical support can be purchased both new and used.
When choosing which four-sided machine to buy, you need to decide exactly on the range of future products and on the performance of work. And already, proceeding from this, dwell on some separate model. If the project requires low productivity and small transverse dimensions of the workpieces being processed, then a four-sided mini-machine may be more suitable, which will cost much less and will take up a rather modest place on the production site.
The four-sided woodworking machine is a specialized equipment that is used for the profiling of natural timber. His samples are indispensable machines in woodworking enterprises, they are also currently used in the furniture and construction industries.
It is with their help that today some types of parquet are produced, as well as moldings, door furniture. Let's take a closer look at the four-sided machine.
1 Technical features of the equipment
The four-sided woodworking machine works on the milling principle. In the four-sided machine, the chuck feeds the required element for processing, which is then trimmed with special milling cutters on four sides and pulled out back with perfectly smooth surfaces.
1.1 How to choose a machine for yourself?
When buying a 4-sided milling machine from options 4015, 26, 13, 160, 15, 51 and others, you need to pay attention to the following design aspects:
- Power. Here, the rule is that the higher the better, it is not necessary. Some models may have low power, but the quality of the processing makes this indispensable at home. But samples with a high given parameter should be considered mainly as professional equipment.
- The type of CNC provided by the PFC. The best option for today is eta. But if this type of CNC is not personally convenient for you, you can choose an alternative option. Fortunately, PFS produces four-roll models of all types of CNC.
- Bed design. It is desirable that the four-roll samples have a single piece. This is improves the quality of their balancing and overall reliability.
- The cost and quality of components. Remember, you will have to change the knives from time to time, as well as other consumables. It is desirable that they are affordable for you.
Also, in all models, regardless of the PFC and the type of CNC, you need to pay attention to functionality. The general advice here is - don't go after very complex versions. Four-roll models with a minimal but streamlined set of options often perform better.
Especially at the moment, attention should be paid to those who take the product for home use.
2 Popular four-sided roll forming machines
Today the four-sided planer is presented on the market in a large number of samples from various PFCs. The most popular among them, worthy of your attention, are the following models:
- four-sided milling machine mid 1. One of the most popular types for the production of profiled timber. Does not require special installation conditions, has a simple CNC, reliable chuck. In one feed, the material can remove up to 5 mm from the bar. Designed for processing parts with a length of 1 meter;
- model c26 2H. Another option for processing a profile bar, thanks to the efforts of the PFS, has a universal chuck. C26 2H makes it possible to work with samples from 63 cm. C 26 has an average power, thanks to which it can be used for homework, and for large-scale furniture production. Like other roll bars 26 or 13, it is extremely easy to use;
- four-sided milling machine c20 4b is a model of turning equipment designed for processing both coniferous and deciduous trees. Like the c26, 13, 15 model, it has a fairly high processing speed, a universal chuck, which means that it can also be used in woodworking enterprises. And like c26 2H, it guarantees high quality of production, regardless of the specified processing parameters;
- version c16 1a. A type of turning equipment for home and factory woodworking. The advantages of this option include the maximum ease of control of the c16 1a sample, its reliability, as well as a wide enough range of applications, which provides a universal cartridge, as in models 26, 13, 160, 15. The maximum workpiece volume for it will be 160 x 80 mm. C16 1a will be especially convenient for beginners;
- Hold MB 4015 is one of the most reliable pieces of equipment with a solid frame. Milling Hold is intended for workshop processing;
- Beaver 520 is one of the most modern versions of the equipment. Has, like Hold, high quality software... Compact but powerful enough. Recommended for industrial use.
2.2 Do-it-yourself four-sided machine
Of course, for many private farms wishing to start the production of lumber, a four-sided machine, for example, Hold MB 4015, with 26, c16, 13 and other models, from the manufacturer is a rather expensive purchase.
The question arises - is it possible to make such equipment with your own hands. In fact, there is such a possibility. In order to make a homemade milling machine, you need to purchase a set of cutters (it is advisable not to save money here, since it is the quality of these components that determines the level of wood processing by an already finished structure).
Next, you will need to assemble the body, the supply line of the type that is installed on the factory models. The cartridge can even be made from a regular profile. Structurally, the cartridge in home and factory models, including 4015, 26, 13, 160, 15, 51, does not differ.
It is also better to take the engine ready-made, and not do it yourself. You can purchase a unit of the required power from similar equipment, replace flexible parts and gears on it, and install it for operation. Next, you will need to make a homemade control unit, taking into account the number of operating modes.
If this is your first time taking up this case, stop at simple scheme, which will only work on and off.
Gather homemade machine milling can be done according to the general scheme for such products, for example, used in versions 4015, 26, 13, 160, 15, 51. At the end of the work, be sure to make sure that the fasteners are reliable, especially the cutters themselves.
Only after you are convinced that the homemade analogue of the factory equipment is working properly, you can start processing wood with it.
Do not forget only about safety rules. Those who choose a homemade option need to pay special attention to them.
Four-sided woodworking machines allow you to deal with the jointing of blanks with a fairly high quality. It is the boards that are most often processed. Modifications on the market different types... First of all, the separation of devices is carried out according to the position of the support.
Also, machines are available with two or three guides. Their racks can be wooden or metal. In order to learn more about this type of machine, specific modifications should be considered.
3 kW modification
A 3 kW machine is quite simple to assemble. In this case, the engine is taken of the collector type. However, before installing it, it is important to do the assembly of the bed. However, some experts recommend using metal supports are more reliable.
After fixing the bed, you need to start assembling the caliper. For this, a steady rest with a rotating flywheel is selected. The cutter in this case must be used of a short length. After fixing the caliper, the steady rest is attached. In order for the workpiece to be securely fixed, a plate is installed. At the end of the work, it remains only to put the control unit to start the collector motor.
Assembling the 5 kW model
Four-sided 5 kW woodworking machines must be made with rigid beds. To do this, the width of the stop must be at least 2.2 cm. In this case, the slab is used with a small width. However, the bed is installed with additional support. Flywheels are used to adjust the caliper.
There are also modifications with roller devices. However, making them yourself is rather difficult. In this case, it is more expedient to use a drive shaft. The engine must be installed at the bottom of the structure. You should also provide space for the control unit. To protect the caliper, experts recommend the use of casings. If you wish, you can make a shield. The cutter is installed on the machine last.
10 kW devices
Woodworking machines four-sided 10 W are common. In order to assemble the device, it is necessary to make a frame with four supports. It is also important to choose a wide slab for the rack. In this case, it is more expedient to install the support above the stops. To fix the stand you need to use
Many experts also recommend using screws to improve grip. The guides in the device are attached behind the caliper. Ultimately, it should not touch the center plate. You can always trim the guides if necessary. To fix the protective shield, you will have to use a welding machine. it is more expedient to select with CNC. They are quite expensive. At the end of the work, all that remains is to fix the cutter.
Top caliper device
To make a four-sided one, you first need to tackle the rack. In this case, the legs can be made from metal profiles. Many experts recommend against using steel sheets. Directly the working plate is selected from cast iron. In order to fix the stand, a metal corner should be welded. It should be located at the edge of the bed.
In this case, it is important to calculate the distance to the cutter. The protective plate is installed last. Many people recommend attaching additional screws to secure the caliper. The flange must be away from the caliper. After fixing the steady rest, the handwheels are installed. They are required to set up the cutter. At the end of the work, the motor is installed together with the control unit.
Bottom caliper model
A homemade four-sided woodworking machine with a lower support position is large. However, such models can handle long boards. In this case, the motors are installed of an asynchronous type with a power of 5 kW or more. CNC blocks are used to control the machining process. Racks in devices are often made of steel corners. Modifications with are rare. In order to make a model yourself, you need to choose a high-quality slab.
Many experts recommend choosing a short length. It should weigh no more than 15 kg. Then there will be no strong pressure on the racks. The caliper in this case is installed next to the pin. The guides are directly attached in a horizontal position. To prevent the cutter from rubbing against the working area, a steady rest is used. In many modifications, it is used of a cam type.
Modification on a movable plate
It is rather difficult to independently manufacture four-sided woodworking machines with movable plates. In this case, a roller mechanism is selected that is able to withstand heavy load... The bed must be made at least 30 cm wide.
The side supports can be fixed on metal corners. In order for the roller mechanism to be stationary, a pulley is used. In this case, the caliper must be installed after the motor. CNC devices are very rare. Most often, conventional control units are used. The steady rest is used directly of the cam type. After fixing it, the cutter is installed.
Double quill model
The model with two quills allows you to process boards of large width. To make a four-sided woodworking machine (photo shown below) with your own hands, you need a long plate. In this case, it is more expedient to make the racks from metal corners. Metal corners are also used to fix the plate. The caliper must be installed over the quill.
The flywheels in this case will be on the sides of the bed. The steady rest is attached before installing the motor. Screws are used to fix it. Legs are usually made of metal corners. Many motor experts advise using a commutator type. Its rated power must be at least 5 kW. The control unit is fitted as standard with a contact type.
Machines on two guides
It is quite easy to assemble machines on two guides. In this case, the support can be installed under the work plate. The motor is allowed to use low power. It is more expedient to select a steady rest with a through drive. The handwheels are installed directly on the side of the steady rest. Many experts advise soldering the work plate to the bed. In this case, the cutter is adjusted with screws. The motor must be installed from the caliper side. The control unit can be used with CNC.
Model SCH-1
The four-sided woodworking machine SCH-1 is very popular. In this case, the guides are installed near the steady. The bed has a low height. The flywheels are located on the side of the caliper. If we talk about parameters, then the motor is used at 5.5 watts. The limiting frequency of the model is 55 Hz. The cutter is capable of making more than 2 thousand revolutions per minute. The quill for the model is provided with
Handwheels are used to adjust the cutter. The stand in the device is installed at 45 cm. The base plate of the model is used without stops. Directly the control unit is located next to the motor. There is a lining under the bezel. A holder is used to fix the workpiece. These four-sided woodworking machines (Borovichi, Russia) are on the market in the region of 230 thousand rubles.