Glavni trendovi u razvoju industrijske organske sinteze. Savremeni trendovi u razvoju industrije petrohemijske sinteze i efikasnost korišćenja alternativnih izvora ugljikovodičnih sirovina Alternativne organske sirovine i nafta
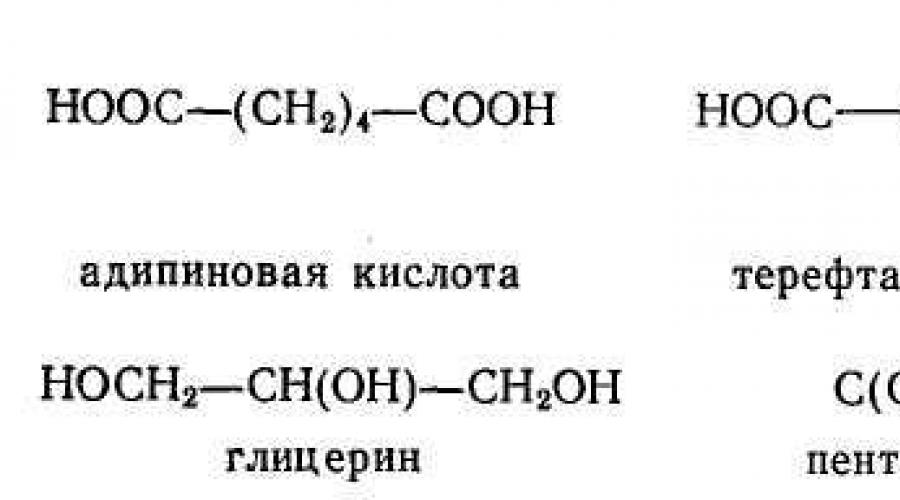
Proizvode ove industrije karakterizira široka raznolikost strukture, svojstava i primjena. To su razni ugljovodonici, derivati hlora i fluora, alkoholi i fenoli, etri, aldehidi i ketoni, karboksilne kiseline i njihovi derivati (esteri, anhidridi, nitrili itd.), amini i nitro jedinjenja, supstance koje sadrže sumpor i fosfor itd. po svojoj namjeni, svi su podijeljeni u dvije grupe: međuproizvodi za sintezu drugih supstanci u istoj ili drugim granama organske tehnologije i proizvodi za ciljanu upotrebu u različitim sektorima nacionalne privrede.
intermedijarni proizvodi. Mnoge supstance koje se gotovo ne koriste u nacionalnoj ekonomiji proizvode se uglavnom da bi se na njihovoj osnovi sintetizovale druga vredna jedinjenja. To su intermedijarni proizvodi organske sinteze. Dakle, najveći dio 1,2-dikloroetana se proizvodi za naknadnu preradu u vinil hlorid, etilen oksid da bi se dobio monoetilen glikol.
Uloga, obim proizvodnje i asortiman međuproizvoda su veoma veliki, jer se sinteza organskih jedinjenja odvija kroz niz međufaza.
Monomeri i polazni materijali za polimerne materijale. Njihova proizvodnja zauzima jedno od najvažnijih mesta u glavnoj organskoj i petrohemijskoj sintezi, obezbeđujući industriju sirovinama. plastike, sintetička guma, sintetički lakovi, ljepila, filmski materijali, vlakna.
Svi sintetički polimeri dobivaju se dvije glavne metode - polimerizacijom i polikondenzacijom. Prva od ovih reakcija zahtijeva monomere, odnosno tvari koje se mogu međusobno kombinirati pod utjecajem topline, svjetlosti, zračenja ili katalizatora bez izolacije bilo kakvih spojeva male molekularne težine i daju duge polimerne lance s istim elementarnim jedinicama kao u originalnom monomeru: polimerizacija etilena .
Od monomera izdvajamo monoolefine (etilen, propilen, izobuten), diene (butadien-1,3 i izopren koji je osnova za proizvodnju gume) i stiren.
U polikondenzaciji, polazni materijali moraju imati najmanje dvije funkcionalne grupe koje mogu međusobno reagirati. Dakle, u formiranju poliestera, hidroksi i karboksi grupe međusobno djeluju:
Početni materijali za procese polikondenzacije pripadaju raznim di- i polifunkcionalnim spojevima. To su fozgen COC1 2, dikarboksilne kiseline, njihovi anhidridi i kiseli hloridi, kao i niz polikarboksilnih kiselina i njihovih anhidrida, glikoli i poliglikoli, diamin:
U reakcijama polimerizacije i polikondenzacije, čistoća reagensa je vrlo važna. Nečistoće sadržane u njima mogu inhibirati reakciju ili prekinuti rast molekulskog lanca tokom polimerizacije, narušiti željeni omjer polaznih supstanci tokom polikondenzacije, što dovodi do polimera s preniskom molekulskom težinom i smanjenih tehničkih performansi. S tim u vezi, postavljaju se vrlo visoki zahtjevi za proizvode osnovne organske i petrohemijske sinteze, a čistoća monomera često mora odgovarati sadržaju glavne supstance od 99,8-99,9% ili više (izobutilen polimerizacijske čistoće).
Plastifikatori i druga pomoćna sredstva zapolimernih materijala. U proizvodnji sintetičkih polimera i proizvoda od njih, uz monomere i polazne materijale, važnu ulogu imaju plastifikatori i druge pomoćne tvari koje doprinose procesu sinteze ili poboljšavaju tehnička svojstva dobivenih polimera i proizvoda.
Plastifikatori (ili omekšivači) su tvari koje se dodaju nekim polimerima u količini do 30-40% radi poboljšanja njihovih plastičnih, elastičnih svojstava. To je neophodno, prije svega, u preradi polimera presovanjem, valjanjem i drugim metodama, za koje polimeri moraju biti dovoljno tečni. Jedna od najvažnijih grupa plastifikatora su esteri visokog ključanja, kao što su dibutil i dioktil ftalati, neki estri viših alkohola sa dikarboksilnim kiselinama ili viših karboksilnih kiselina sa dihidričnim alkoholima, alkilaromatski ugljovodonici, niži poliolefini itd.
Stabilizatori su tvari koje povećavaju otpornost polimera i gume na oksidativno starenje. Alkilfenoli, aromatični diamini se koriste kao stabilizatori.
Sintetički surfaktanti i deterdženti. Površinski aktivna svojstva pojavljuju se u organskim supstancama koje sadrže hidrofobnu grupu u molekuli i, zajedno s njom, hidrofilnu (polarnu) grupu sposobnu za otapanje u vodi. U običnom sapunu - natrijum soli stearinske ili palmitinske kiseline RCOONa, ulogu ovih grupa obavljaju dugi ugljikovodični lanac, odnosno karboksilatna grupa.
S obzirom na ovu strukturnu osobinu, površinski aktivna supstanca (surfaktant) se koncentriše na međufaznu granicu, orijentišući svoju hidrofobnu grupu na komponentu ulja i masti u sistemu, a hidrofilnu grupu na vodu. Kao rezultat toga, površinski napon je značajno smanjen, što doprinosi dobrom vlaženju materijala i prijenosu zagađivača u vodu. Surfaktanti također imaju svojstva emulgiranja i disperzije, sposobnost stvaranja pjene.
Surfaktanti i deterdženti posebno se koriste u svakodnevnom životu za pranje tkanina i proizvoda od njih i čišćenje raznih predmeta. U tekstilnoj industriji koriste se za obradu tkanina prije bojenja, u mašinstvu i obradi metala - pri rezanju metala, za čišćenje dijelova od ulja i mehaničkih nečistoća, u industriji parfema - kao komponente toaletnog sapuna i kozmetike. U hemijskoj tehnologiji služe kao emulgatori u heterofaznim reakcijama (posebno u emulzijskoj polimerizaciji).
Surfaktanti i deterdženti dijele se na ionske i nejonske, a razlikuju se po prisutnosti ili odsutnosti grupa sposobnih za disocijaciju u vodenim otopinama. Jonske supstance su, zauzvrat, anjonske i kationske, kod kojih su površinski aktivna svojstva određena anjonom ili kationom nastalim tokom disocijacije.
Anionske tvari uključuju najvažnije industrijske deterdžente, uključujući sapune - obične i dobivene od sintetičkih masnih kiselina (aktivni dio molekule je RCOO ~ grupa). Takvi surfaktanti imaju alkalnu reakciju i doprinose razaranju tkiva, daju nerastvorljive soli sa magnezijevim i kalcijevim solima, što smanjuje njihova svojstva pranja u tvrdoj vodi, a aktivni su samo u značajnoj koncentraciji u vodi. Ovi nedostaci su uglavnom odsutni u modernim sintetičkim anjonskim supstancama, od kojih su većina natrijeve soli organskih sulfonskih kiselina i kiseli estri sumporne kiseline. To uključuje alkil arenesulfonate RC 6 H4SO 2 ONa, alkil sulfonate RSO 2 ONa i alkil sulfate ROSO 2 ONa sa C 12 -C 18 alkil grupama.
Kationski deterdženti su od relativno malog praktičnog značaja. Najčešće su to soli amina ili kvaternarnih amonijum baza, kao što je alkilbenziltrimetilamonijumova so + C1-
Poslednjih godina sve se više koriste nejonski deterdženti. Sintetiziraju se iz etilen oksida i raznih organskih spojeva - alkilfenola, karboksilnih kiselina, alkohola, amina i drugih tvari s aktivnim atomima vodika. Hidrofilna svojstva im daje oksietilni lanac, na primjer R (OCH 2 CH 2) n OH.
Budući da površinski aktivne tvari nakon upotrebe završavaju u otpadnim vodama, važan zahtjev je visok stepen njihove biorazgradivosti, odnosno sposobnost oksidacije u bezopasne tvari pod utjecajem mikroorganizama koji se nalaze u prirodnim vodnim tijelima. Ovo nameće određena ograničenja na strukturu ugljikovodičnih ostataka uključenih u surfaktant, koji ne bi trebali biti razgranati.
Sintetička goriva, ulja za podmazivanje i njihovi aditivi. Mnogi proizvodi osnovne organske i petrohemijske sinteze važni su u drumskom saobraćaju, vazduhoplovstvu, raketnoj tehnici i drugim oblastima. Tu spadaju sintetička motorna i raketna goriva, ulja za podmazivanje, aditivi koji poboljšavaju svojstva goriva i ulja, antifrizi koji sprečavaju smrzavanje rashladnih tečnosti, kočionih i hidrauličnih tečnosti.
Kao visokooktanske komponente motornih goriva koriste se izoparafini, izopropilbenzen C 6 H 5 CH (CH 3) 2, terc-butil metil etar (CH 3) sCOCH 3 itd.
Sintetička ulja za podmazivanje pripadaju nekoliko grupa organskih spojeva, od kojih su najznačajniji: sintetički ugljovodonici (niži polimeri olefina i alkilovani aromatični ugljovodonici); estri dvobaznih karboksilnih kiselina i viših monohidroksilnih alkohola, kao i viših monokarboksilnih kiselina i polihidričnih alkohola.
Različiti aditivi se koriste za poboljšanje performansi goriva i ulja i njihovu stabilnost skladištenja. Antioksidativni aditivi u gorivima i uljima za podmazivanje, kao i u polimerima (na primjer, alkilirani fenoli) usporavaju lančane reakcije autooksidacije. Ostali aditivi snižavaju tačku tečenja ulja (depresivi), poboljšavaju njihova svojstva viskoznosti (aditivi za viskoznost), sprečavaju koroziju metala (inhibitori korozije) itd.
Rastvarači i ekstrakti. Štaviše, sintetički rastvarači bi trebali biti jeftini, lako dostupni i malo toksični. Njihova tačka ključanja ne smije biti preniska da bi se izbjegli preveliki gubici, i ne smije biti previsoka da bi se povratila destilacijom. U nizu slučajeva bilo je moguće sintetizirati otapala sa smanjenom opasnošću od požara, pa čak i potpuno nezapaljiva.
Trenutno se rastvarači i ekstrakti koriste vrlo široko: za odvajanje aromatičnih ugljovodonika iz proizvoda prerade nafte, u procesima azeotropne i ekstraktivne destilacije, za ekstrakciju masti i ulja iz prirodnih supstanci. U hemijskoj industriji često se koriste, na primjer, za pročišćavanje i rekristalizaciju, kao apsorbenti za plinove i pare (acetilen i hlapljive tvari koje se prenose plinovima), u sintezi polimera (posebno u industriji boja i lakova). U mašinstvu i obradi metala otapala se koriste za odmašćivanje i čišćenje delova. U poljoprivredi su otapala potrebna pri upotrebi pesticida.
Sintetički rastvarači i ekstraktanti mogu pripadati različitim grupama organskih jedinjenja. To su benzen, hlorni derivati ugljovodonika (tetrahlorometan, dihlorometan, tri- i tetrahloretilen), alkoholi (etanol, propanol, butanoli, pentanoli), celosolvi, etri (dietil, diizopropil i viši), ketoni (aceton, etil-etil, etil-etil, metil keton), estri (etil-, butil- i pentilacetat), kao i dimetilformamid HCON (CH 3) 2, dimetil sulfoksid (CH 3) 2 SO, itd.
Pesticidi i hemikalije za zaštitu bilja. Pesticidi (ili pesticidi) su tvari koje imaju toksična svojstva u odnosu na različite žive organizme – od bakterija i gljivica do biljaka i štetnih životinja. Značajan dio pesticida koristi se u poljoprivredi kao hemikalije za zaštitu bilja; osim toga, koriste se u svakodnevnom životu, za suzbijanje širenja bolesti i epidemija, za uništavanje štetočina u skladištima, u skladištima brodova, u stambenim zgradama itd. Upotreba pesticida u poljoprivredi omogućava izbjegavanje mnogih bolesti ratarskih i hortikulturnih usjeva i značajno smanjuju gubitke usjeva. U tom smislu, hemijska sredstva za zaštitu bilja postala su ništa manje važan faktor u povećanju prinosa od hemijskih đubriva.
SIROVINE ZA PETROHEMIJSKU SINTEZU I NJENU PRIPREMU Sirovine za petrohemijsku sintezu
iz "Osnove tehnologije petrohemijske sinteze"
Razvoj petrohemijske industrije povezan je sa upotrebom niskomolekularnih olefina - etilena, propilena, izobutilena i n-butilena kao sirovina. Kasnije su hemijski obrađeni amileni, a zatim metan, etan, propan, butan i pentan. Velika važnost nabaviti industrijske sinteze na bazi acetilena, čiji je pouzdan izvor metan.Trenutno se tečni naftni ugljovodonici takođe široko koriste za petrohemijsku sintezu. Iz godine u godinu povećava se potrošnja benzena, toluena, ksilena i naftalena za sintezu deterdženata, sintetičkih vlakana, pesticida itd. Čvrsti parafini se u velikoj mjeri koriste u oksidacijskim procesima kako bi se dobile sintetičke masne kiseline i alkoholi. , kao i meki (tečni) parafini. Parafini se također koriste za sulfoksidaciju i sulfokloraciju. Prilikom krekiranja čvrstih parafina dobijaju se α-olefini iz kojih se proizvode sekundarni alkil sulfati – deterdženti.
Među naftnim ugljovodonicima posebno mjesto zauzima cikloheksan, koji se koristi kao intermedijer i kao otapalo u proizvodnji sintetičkih vlakana i plastike. Upotreba cikloheksana u ove svrhe potaknula je povećanje njegove proizvodnje.
Prilikom razvoja plinskih polja, prirodni plinovi su ciljni proizvod. Prirodni gas se sastoji uglavnom od metana i nekih drugih ugljovodoničnih gasova, kao i primesa inertnih i retkih gasova (videti tabelu 0.2). Gasovi se proizvode i iz gasno-kondenzatnih polja - dubokih plinskih polja sa visokim pritiskom u rezervoaru. Nakon smanjenja tlaka, takvi plinovi oslobađaju kondenzat - tekuće ugljovodonike, koji ključaju do 300 ° C i više, koji se također mogu koristiti kao kemijske sirovine. Na primjer, Karadaški kondenzat ima n. k.57°S, sadrži frakcije do 100°S-14%, do 150°S -40%, do 200°C -57% i k. do 340°s. Gas Karadag sadrži do 168 g kondenzata po 1 L1 gasa, gasovi Saratovskog gasnog kondenzatnog polja sadrže 45 g kondenzata po 1 m3.
Moguća je hemijska prerada i koksovanje gasova koji sadrže do 2,5% olefina. Proizvodni plinovi i plinovi za preradu škriljaca mogu se koristiti u procesima koji koriste vodonik ili za sinteze na bazi ugljičnog monoksida i vodonika, ovi plinovi sadrže do 63% vodonika, 15% ugljičnog monoksida, 12% metana i malu količinu (0,5%) olefina .
Petrohemijska sinteza ima niz mogućnosti za hemijske transformacije ugljovodonika. Hemijskoj preradi se podvrgavaju pojedinačni ugljovodonici ili uske frakcije, koji se izoluju iz prirodnih i pratećih gasova, gasova prerade nafte, iz tečnih proizvoda termičkih katalitičkih procesa za preradu naftnih sirovina. U nastavku se razmatraju glavne transformacije pojedinačnih ugljovodonika.
Met je sastavni dio povezanih, prirodnih i umjetnih plinova. Trenutno su razvijene i uvedene u industriju različite metode njegove hemijske obrade. Jedan od obećavajućih procesa je oksidacija metana sa stvaranjem formaldehida, metanola i acetaldehida.
Piroliza i dehidrogenacija metana mogu proizvesti acetilen, čađu i vodonik. Prilikom konverzije metana parom ili parom i kiseonikom dobija se sintezni gas (CO-L -LHg) - sirovina koja se koristi za dalju organsku sintezu, kao i odvojeno čisti ugljen monoksid i vodonik koji se koriste za hidrogenaciju i amonijak. procesi sinteze. Amonijak se koristi za sintezu uree, koja je vrijedan proizvod za proizvodnju plastike i efikasno đubrivo.
Kada se metan hloriše u industrijskoj skali, dobijaju se metil hlorid, metilen hlorid, hloroform i ugljen-tetrahlorid. Kada se metan nitrira, nastaje nitrometan, koji se koristi kao otapalo u proizvodnji raznih lakova.
Šema glavnih pravaca prerade metana prikazana je na sl. I.I.
Prilikom pirolize etana nastaje etilen kao sirovina za sintezu etilen oksida, etil alkohola, polietilena, stirena i drugih proizvoda (slika I. 2). Prilikom oksidativne pirolize nastaje acetilen, pri hloriranju se dobija etil hlorid koji se koristi za proizvodnju tetraetil olova, alkohola, plastike, a tokom nitracije - nitroetana i nitrometana, koji se široko koriste kao rastvarači.
Propan. Kada se propan oksidira, dobijaju se acetaldehid, formaldehid, sirćetna kiselina i aceton. Pirolizom propana nastaju etilen i propilen. Zajedno sa metanom i etanom, propan se takođe može koristiti za proizvodnju acetilena (vidi sliku I. 2). Kada se propan nitrira, dobijaju se nitrometan, nitroetan i nitro propan. Proizvodi za kloriranje propana još nemaju industrijsku vrijednost.
GORIVO. Prilikom dehidrogenacije izobutana nastaje izobutilen - sirovina za proizvodnju butil gume, poliizobutilena, polimernog benzina.Osim toga, izobutan je široko rasprostranjeno sredstvo za alkilaciju.
Etilen. Etilen se u najvećim količinama koristi u petrohemijskim sintezama. Od njega se dobijaju etil alkohol, etilen oksid, polietilen, stiren, dihloretan i drugi proizvodi. Najveći dio etilena u narednim godinama će se prerađivati u polietilen (Sl. I. 4).
propilen. Propilen služi kao sirovina za sintezu polipropilena, izopropil alkohola, izopropilbenzena, na osnovu kojeg se dobijaju fenol i aceton, glicerina i epihlorohidrina, prolilen tetramera za deterdžente, metilstirena, propilen oksida, akroleina i drugih proizvoda (amil alkohol Slika I. 5). U posljednje vrijeme industrijska sinteza akrilonitrila iz propilena i amonijaka dobija na značaju. Proizvodnja izopropilbenzena se povećava iz godine u godinu i nastaviće da raste, jer se na njegovoj osnovi dobija najjeftiniji fenol, za kojim je potražnja veoma velika.
Proizvodi na bazi propilena, uključujući polipropilen, mogu se proizvoditi u rafinerijama koje imaju velike resurse propilena u obliku propan-propilenske frakcije.
Butileni. Butileni igraju veoma važnu ulogu u petrohemijskoj industriji, uglavnom se koriste za sintezu kaučuka. Najpopularnije sirovine za proizvodnju sintetičkih kaučuka su butilen-1 i butilen-2 - međuproizvodi nastali tokom proizvodnje butadiena. Kopolimerizacijom izoprena i izobutilena nastaje posebna vrsta sintetičkog kaučuka - butil kaučuka.
Na bazi butilena butan-butilenske frakcije kreking gasova vrši se industrijska proizvodnja alkilata, visokooktanskog aditiva motornom gorivu. U industrijskim razmjerima proizvode se poliizobutileni male i velike molekulske mase, koji se koriste kao zgušnjivači za naftna maziva ulja i u druge svrhe. Butileni se takođe koriste za industrijsku proizvodnju sekundarnih i tercijarnih butil alkohola i drugih proizvoda (Sl. I. 6).
Acetilen. Acetilen služi kao sirovina za sintezu velikog broja petrokemijskih proizvoda. Rastuća potražnja za acetilenom iz godine u godinu zahtijevala je razvoj novih ekonomičnih metoda za njegovu proizvodnju. Trenutno je industrija ovladala metodom za proizvodnju acetilena iz prirodnog gasa - termičkom oksidativnom pirolizom metana, odnosno cijepanjem metana spaljivanjem dijela plina kisikom koji se dovodi u proces.
Glavna sirovina ugljikovodika za petrokemijske sinteze su mješavine plinovitih, tekućih i čvrstih ugljovodonika.
prirodni gasovi sastoje se uglavnom od metana i drugih zasićenih ugljovodonika; sadrže i inertne plinove (azot, ugljični dioksid) i rijetke plinove (argon, ksenon). Prirodni gasovi se proizvode tokom razvoja gasnih i kondenzatnih polja.
Povezani naftni gasovi dobijen kao nusproizvod ekstrakcije ulja. Ovi gasovi se rastvaraju u ležištu nafte i oslobađaju se tokom proizvodnje usled smanjenja pritiska. Povezani naftni plin sastoji se od zasićenih ugljovodonika od metana do pentana i obično sadrži nešto inertnih gasova; Povezani gasovi nekih polja sadrže i slobodni vodonik sulfid. Po pravilu, prateći naftni gasovi sadrže značajne količine ugljovodoničnih komponenti - etana, propana i butana, koji su vrijedne sirovine za petrohemiju.
Rafinerijski gasovinastaje u procesima krekiranja, koksovanja, reforminga; uzimaju se i iz postrojenja za stabilizaciju ulja i direktnu destilaciju. U zavisnosti od prirode ovih procesa, sastav nastalih gasova varira u širokom opsegu. Na primjer, plinovi katalitičkog reforminga sadrže do 60% vodonika; ostatak su zasićeni ugljovodonici. Plinovi krekinga i koksiranja sastoje se od zasićenih i nezasićenih ugljovodonika.
Gasovi za stabilizaciju nafteodlikuju se visokim sadržajem propana, butana, pentana i izopentana, što ih čini vrijednom sirovinom za proizvodnju butadiena i izoprena.
Benzini prokuhati u rasponu od 30-120 0 S; sadrže butan, pentan, izopentan, kao i C 6 i C 7 ugljovodonike normalne strukture i izo strukture.
Gasni kondenzatiključanje u rasponu 40-360 0 C. Sadrže 15-30% aromatični ugljovodonici; 25-40% naftena i 20-60% parafina (u zavisnosti od polja).
Tečni destilati i naftni derivati, koji nastaju tokom različitih procesa prerade nafte, koriste se i kao sirovina u petrohemijskim procesima, tačnije, kao izvor za izolaciju određenih grupa ugljovodonika. Dakle, aromatični ugljovodonici se izoluju iz proizvoda katalitičkog reforminga, olefini iz proizvoda termičkog i katalitičkog krekinga, a parafini iz proizvoda deparafinisanja dizel goriva.
Ugljovodonici izolirani iz ugljikovodičnih sirovina su od velike praktične važnosti. Na primjer, prirodni plin metan se koristi kao gorivo i sirovina za proizvodnju vodika, acetilena, amonijaka i metanola. Etan služi kao sirovina za procese pirolize za proizvodnju etilena; gasni kondenzati - sirovine za proizvodnju butadiena, izoprena, aromatičnih ugljovodonika.
v Zahtjevi za ugljikovodične sirovine
Sirovine ugljovodonika za petrohemijske procese obično su podložne mnogo strožijim zahtevima od sirovina za procese rafinacije nafte.
Reakcije koje se koriste u petrohemijskoj sintezi, uglavnom katalitičke ili radikalne lančane, a visoka selektivnost katalizatora neophodna za dobijanje traženih proizvoda, potpuno su neprihvatljive. neželjene reakcije itd. Zbog toga je potreban visok stepen čistoće sirovine. Dakle, za proizvodnju etil alkohola direktnom hidratacijom etilena potrebno je 97-98% etilena, praktično bez vodonik sulfida (do 0,002% H 2 S). Za proizvodnju HDPE-a je potrebno 99,99% etilena, potpuno bez acetilena.
Pažljivo prečišćavanje etilena od sumporovodika u proizvodnji etil alkohola je neophodno jer destilacioni uređaj za odvajanje nastalog alkohola iz reakcione smeše brzo korodira i pokvari. Iz istog razloga, etilen ne bi trebao sadržavati acetilen.
Prilikom oksidacije tekućih i čvrstih parafina u alkohole i kiseline, neophodno je da sirovina sadrži minimalni iznos(do 0,5%) naftenskih i aromatičnih ugljovodonika koji inhibiraju oksidaciju. Ništa manje važno je i odsustvo fenola, azotnih i sumpornih spojeva koji prekidaju oksidacijski lanac. S tim u vezi, zahtjevi za sadržajem sumpora u aromatičnim ugljovodonicima su strogi (ne više od 0,02%) i njegov dozvoljeni sadržaj se stalno smanjuje.
U nekim slučajevima potrebno je pročistiti ugljikovodične sirovine od izomera i homologa iste kemijske prirode. Dakle, ako parafini sadrže izostrukturne ugljikovodike, proizvodi naknadne oksidacije sadrže povećan iznos kiseline male molekularne mase, kao i izokiseline izuzetno neprijatnog mirisa.
Dodavanje diena u olefine dovodi do razvoja smole tokom izomerizacije i alkilacije.
Za ugljikovodične sirovine treba postojati ograničenja u pogledu sadržaja ugljičnih oksida, amonijaka i vlage.
Sve navedeno ukazuje na potrebu pažljivog pripremanja ugljikovodičnih sirovina.
v Značenje pre-trening ugljovodonične sirovine za preradu
Ugljovodonične sirovine moraju ispunjavati visoke zahteve određene specifičnostima daljih hemijskih transformacija ugljovodonika. Jedan od glavnih zahtjeva za sirovinu ugljikovodika je minimalni sadržaj ili potpuno odsustvo tvari različite kemijske prirode. Neophodna je pažljiva priprema ugljikovodičnih sirovina za preradu kako bi se izbjegla korozija procesne opreme; produženi vijek trajanja katalizatora; isključeno je začepljenje cjevovoda i njihov protok; smanjila se količina nusproizvoda, povećao prinos ciljnog proizvoda i poboljšao njegov kvalitet.
.
budžet savezne države obrazovne ustanove
više obrazovanje
"Kazanski nacionalni istraživački tehnološki univerzitet"
(FGBOU VO "KNRTU")
Katedra "Tehnologija osnovne organske i petrohemijske sinteze"
apstraktno
u disciplini "Hemija i tehnologija osnovne organske i petrohemijske sinteze"
na temu "Butadien"
Završeno:
magistar odsjeka za TOONS,
grupa 417-M11
Ishmukhametova L.A.
Kazan 2017
Uvod…………………………………………………………………………………….…3
Svojstva………………………………………………………………………4
Primjena u UNOC industriji…………………………………4
Industrijske metode sinteze……………………………………………5
Izgledi za proizvodnju i primjenu u Rusiji…………………….11
Izgledi za proizvodnju i primjenu u inostranstvu…………………..12
Tehnološka šema dehidrogenacije butana i butena…………...13
Uvod
Butadien-1,3 (divinil) CH 2 = CH-CH = CH 2 - bezbojni plin s karakterističnim neugodnim mirisom s temp. bale 268,59 K.
Butadien - tipični dienski ugljovodonik sa konjugovanim dvostrukim vezama, lako se polimerizuje i kopolimerizuje sa stirenom, nitrilima ili estrima akrilne ili metakrilne kiseline, vinil i metil vinil piridini, vinil i viniliden hloridi, izobutilen, izobutilen itd. je glavni monomer koristi se u modernoj industrijskoj proizvodnji sintetičkih kaučuka. Proizvodnja velike većine sintetičkih guma opće namjene temelji se na butadienu: stereoregular 1,4,- cis-butadien, butadien-stiren, butadien-metilstiren, određeni broj sintetičkih guma posebne namjene- butadien-nitril, butadien-metilvinilpiridin i dr. Osim u proizvodnji sintetičkih kaučuka, butadien se u industrijskom obimu koristi za proizvodnju sintetičkih smola, adiponitrila (u proizvodnji poliamida) i sebacinske kiseline.
Svojstva
Butadien-1,3 (divinil) C4 H6 je bezbojni gas u normalnim uslovima, kondenzuje se u tečnost na 268,7 K (-4,3°C), sa tačkom ključanja od -4,4°C, tačkom topljenja 108,9° C i gustinom u tečnom stanju od 0,645 t/m3 (na 0°C). Ne otapajmo u vodi, loše ćemo se rastvoriti u alkoholima, dobro je - u benzenu, dietil eteru, hloroformu; formira azeotropne smjese s nekim rastvaračima. Kritična temperatura butadiena je 152°C. Sa vazduhom butadien stvara eksplozivne smeše sa granicama zapaljivosti od 2,0 i 11,5% vol. Tačka paljenja butadiena je -40°C, temperatura samozapaljenja je 420°C.
Butadien se lako polimerizira:
nC 4 H 6 → [-CH 2 -CH \u003d CH-CH 2 -] n
Polimerizaciju pokreću peroksidi koji nastaju kada butadien dođe u kontakt sa vazduhom. Toplotni efekat polimerizacije zavisi od temperature i kreće se od 72,8 do 125,6 kJ/mol. Kao posljedica toga, butadien se skladišti u prisustvu inhibitora, na primjer p-oksidifenilamina ili p-tert-butilpirokatehola, koji se uklanjaju ispiranjem natrijum hidroksidom prije polimerizacije. Radikalna lančana kopolimerizacija butadiena sa stirenom, a-metilstirenom ili akrilonitrilom proizvodi kopolimere čije makromolekule sadrže nasumično naizmjenične jedinice polaznih materijala.
Butadien u visokim koncentracijama ima narkotički učinak; u malim koncentracijama iritira respiratorni trakt i sluzokožu očiju. MPC je 100 mg/m3.
Aplikacija
Butadien je glavni monomer koji se koristi u modernoj industrijskoj proizvodnji sintetičkih kaučuka. Proizvodnja velike većine sintetičkih guma opšte namjene zasniva se na butadienu: stereoregularni 1,4-cis-butadien, stiren-butadien, butadien-metilstiren, niz sintetičkih guma specijalne namjene - nitril butadien, butadien-metilvinil itd. Osim za proizvodnju sintetičkih kaučuka, butadien se u industrijskom obimu koristi za proizvodnju sintetičkih smola, adiponitrila (u proizvodnji poliamida) i sebacinske kiseline.
Metode industrijske sinteze
Divinil je prvi nabavio francuski hemičar J.B. Cavant 1862. pirolizom fuzelnog ulja.
Njegova prva industrijska proizvodnja u SSSR-u organizirana je po Lebedev metodi od etil alkohola. Ova metoda je katalitička konverzija etil alkohola. Otvoren je 1931. godine. Lebedevova metoda bila je osnova za industrijsku sintezu divinila u našoj zemlji. Međutim, trenutno ovu metodu nije u širokoj upotrebi.
1949. W. Reppe je otkrio metodu za dobijanje butadiena-1,3 interakcijom acetilena sa formaldehidom. Od 1940. godine počele su studije o metodi dobijanja divinila katalitičkom dehidrogenacijom n-butana i n-butilena N.D. Zelinsky i A.A. Baladina, kasnije uspješno uveden u praksu.
Jednostepena dehidrogenacija n-butana savladana je od 1947. godine. Godine 1980. izgrađeno je postrojenje u Permu za odvajanje butana i pentana od pratećih naftnih gasova. Ova instalacija omogućava dobijanje 50% divinila iz naftnih sirovina.
Metoda S.V. Lebedev
2C 2 H 5 OH → C 4 H 6 + H 2 + 2H 2 O - 84,8 kJ
Iz jednadžbe se može vidjeti da je ukupna reakcija kombinacija kondenzacije, dehidrogenacije i dehidracije. Ove zahtjeve ispunjava polifunkcionalni oksidni katalizator koji je predložio Lebedev, koji osigurava reakciju dobijanja divinila u jednoj fazi sa tehnički prihvatljivim prinosom.
Konverzija etanola sastoji se od sljedećih reakcija:
Dehidrogenacija alkohola u acetaldehid:
CH 3 CH 2 OH → CH 3 CHO + H 2
Kondenzacija acetaldehida u aldolm praćena eliminacijom vode i stvaranjem krotonaldehida:
2CH 3 CHO → CH 3 CH(OH)CH 2 CHO →CH 3 CH \u003d CHCHO + H 2 O
Redukcija karbonilne grupe krotonaldehida upotrebom molekule etanola kao hidrogenirajućeg agensa (potonji se pretvara u acetaldehid):
CH 3 CH \u003d CHCHO + C 2 H 5 OH → CH 3 CH \u003d CHCH 2 OH + CH 2 CHO
Dehidracija krotil alkohola, praćena stvaranjem konjugovanog sistema dvostrukih veza:
CH 3 CH \u003d CHCH 2 OH →CH 2 \u003d CH-CH = CH 2 + H 2 O
Konverzija alkohola u butadien se odvija na 360-380°C na fiksnom oksidnom katalizatoru. Kako nastaju nusproizvodi organska jedinjenja različite klase: ugljovodonici, alkoholi, etri, aldehidi itd.
Teorijski prinos butadiena je 58,7%, međutim, zbog pojave nuspojava, obično je nešto manji, ali ostaje blizu teoretskog. Glavni nedostatak procesa je niska selektivnost. Prednost metode je komparativna jednostavnost dizajna hardvera tehnološki proces. Trenutno je ovaj proces u velikoj mjeri izgubio industrijski značaj.
Sinteza butadiena po Reppe metodi.
Zatim se na 260-270 0 C u prisustvu vodene pare i natrijum fosfata (katalizatora) na koksu ili grudvastom grafitu, voda ponovo odvaja od tetrahidrofurana; rezultat je butadien. Takođe se može dobiti direktno odvajanjem dva molekula vode iz 1,4-butilen glikola u prisustvu fosfatnog katalizatora, ali dolazi do nuspojava i prinosi su lošiji nego kod dvofaznog procesa.
Industrijske metode za dobijanje butadiena iz butana ili butena-1.
Dehidrogenacija n-butana u butadien-1,3 je reverzibilni heterogeni katalitički proces koji se odvija apsorpcijom topline kroz fazu formiranja izomera butilena prema shemi:
Industrija koristi različite tehnološke mogućnosti za dobijanje butadiena dehidrogenacijom C 4 ugljovodonika. Primijenjeni procesi se uslovno mogu podijeliti u sljedeće grupe: dehidrogenacija butana u butene, dehidrogenacija butena; jednostepena i dvostepena dehidrogenacija butana u butadien. Karakteristična karakteristika reakcija dehidrogenacije sa stvaranjem olefina je ograničenje stepena konverzije ravnotežnim uslovima. Reakcije dehidrogenacije su uvijek endotermne i stoga se ravnoteža prema stvaranju nezasićenih ugljovodonika mora pomjerati s povećanjem temperature. Stepen konverzije ugljovodonika raste sa povećanjem temperature i smanjenjem pritiska. U praksi, na temperaturama iznad 773-823 K, čak i u odsustvu katalizatora, zasićeni ugljovodonici prolaze kroz izomerizaciju, krekiranje itd. Stoga se proces dehidrogenacije butana odvija na temperaturama do 923-973 K, tj. at niže temperature od termodinamičkih optimalnih. Upotreba katalizatora omogućava postizanje visoke brzine procesa na relativno niskoj temperaturi, kada doprinos sporednih reakcija još nije značajan. Zbog reverzibilnosti reakcija dehidrogenacije-hidrogenacije i, posljedično, sposobnosti katalizatora da ubrzaju reverzibilne reakcije u oba smjera, ove reakcije kataliziraju isti spojevi. Tokom dehidrogenacije, zbog uklanjanja vodonika, uvijek dolazi do povećanja zapremine gasa, a smanjenje pritiska pogoduje povećanju stepena konverzije. Zbog toga se procesi dehidrogenacije izvode pri pritisku bliskom atmosferskom, au nekim slučajevima proces se odvija u vakuumu. Ponekad je, umjesto vakuuma, poželjno razrijediti reakcionu masu plinom koji je inertan u uvjetima reakcije, ili parom, što također dovodi do smanjenja parcijalnih pritisaka reagensa i povećanja ravnoteže. stepen konverzije. Smanjenje parcijalnog tlaka također omogućava snižavanje temperature reakcije i na taj način smanjuje stvaranje nusproizvoda. Važan parametar u izvođenju reakcije dehidrogenacije je vrijeme kontakta reakcione smjese sa katalizatorom.
Radi na katalitičkoj dehidrogenaciji n-butana u dvostepenoj verziji:
n-butan → n-buten → butadien su nastali u SAD 1920-ih. U Sovjetskom Savezu fundamentalna istraživanja u ovoj oblasti sproveo je S.V. Lebedev, N.I. Shuikin, A.A. Balandin, B.A. Kazanski i drugi.
Dehidrogenacija butana u butadien u jednom koraku
C 4 H 10 ↔ C 4 H 6 + 2H 2 + ∆H, ∆H= 247 kJ
Ima očigledne prednosti pre dvostepenog procesa zbog odsustva potrebe za odvajanjem gasnih mešavina nakon svake faze i nižih troškova energije i kapitala.
Rice. 2 - Zavisnost sastava ravnotežne smjese tokom dehidrogenacije butana u butene i butadien od temperature i pritiska. Pune linije - 0,1 MPa, isprekidane linije - 0,01 MPa.
1 - butan; 2 - buteni; 3 - butadien
Termodinamički proračuni pokazuju da se ravnotežni prinos diena značajno povećava s porastom temperature i sa smanjenjem parcijalnog pritiska alkana. Pošto je povećanje temperature povezano sa gubitkom selektivnosti reakcije, jednostepena proizvodnja diena iz alkana je izvedena u uslovima vakuum dehidrogenacije. U jednostepenom procesu dehidrogenacije koriste se aluminijum-hrom katalizatori koji sadrže 18-30% hrom-oksida. Goodry (SAD) je prva kompanija koja je implementirala proces dobijanja butadiena iz butana u jednoj fazi (slično procesu dobijanja izoprena iz izopentana). U prisustvu aluminijum-hrom katalizatora dolazi do bočnih transformacija butana, butena i butadiena. Upotreba aluminijum-hrom katalizatora eliminiše upotrebu pare kao razblaživača.
Proces u dva koraka
divinil iz butilena, dehidrogenacija butana u butilen na promoviranom katalizatoru od krom-oksida na bazi glinice odvija se prema reakciji:
C 4 H 10 ↔ C 4 H 8 + H 2; ΔN= 131 kJ.
U industrijskim reaktorima se javljaju i nuspojave: reverzna reakcija hidrogenacije butilena, kreking butana i butilena, izomerizacija butana i butilena i reakcije stvaranja ugljika. U sovjetskim industrijskim postrojenjima za dehidrogenaciju butana koriste se sistemi sa fluidiziranim slojem finozrnastog aluminij-kromnog katalizatora razreda K-5. U procesu dehidrogenacije butana, katalizator se prekriva naslagama ugljika i mijenja svoj hemijski sastav. U ovom slučaju, aktivnost katalizatora naglo opada. U svrhu reaktivacije, katalizator se kontinuirano izvlači iz reaktora i kalcinira u struji zraka u regeneratoru s fluidiziranim slojem. U ovom slučaju, ugljični spojevi izgaraju, a niži oksidi kroma se oksidiraju u Cr 2 O 3. Dehidrogenacija butilena u divinil se odvija na krom-kalcij-fosfatnom katalizatoru prema reakciji:
C 4 H 8 ↔ C 4 H 6 + H 2, ΔH = 119 kJ.
Butadien se razgrađuje na povišenim temperaturama, stoga je, kako bi se održala dovoljno visoka selektivnost butadiena, u praksi potrebno pribjeći smanjenju parcijalnog tlaka reakcionih plinova zbog upotrebe pregrijane vodene pare ili vakuuma. Optimalna temperatura sirovine na ulazu u reaktor je 860-910K. Dvofazni proces omogućava stvaranje optimalnih uslova za njegov protok u svakoj fazi, osiguravajući maksimalan prinos proizvoda i selektivnost. Aparati sa fluidizovanim slojem se široko koriste za prvu fazu. Ovakvi uređaji imaju niz prednosti u odnosu na uređaje kod kojih je katalizator fiksiran na nekoliko ploča: 1) izotermni sloj koji se postiže aktivnim mešanjem; 2) fluidnost sloja, koja omogućava transport koksovanog katalizatora od reaktora do regeneratora i nazad; 3) visoka međufazna izmjenjivačka površina, što rezultira visokim prijenosom topline i prijenosa mase; 4) nizak hidraulički otpor sloja, koji obezbeđuje smanjenje troškova energije i povećava brzinu procesa. Dakle, u dizajnu CS reaktora uočavaju se sve zakonitosti izvođenja heterogenih katalitičkih reakcija. Procesi dehidrogenacije i regeneracije izvode se u različitim uređajima istog dizajna. Za razliku od prve, druga faza se odvija u adijabatskim reaktorima sa fiksnim slojem katalizatora. Toplina potrebna za reakciju se dovodi pregrijanom parom pomiješanom sa sirovinom. Prednost ovih uređaja je jednostavnost dizajna, nedostaci su neravnomjerna raspodjela temperature u sloju, visok hidraulički otpor uređaja, pogoršanje performansi reaktora kako se katalizator koksuje, učestalost rada uređaja, naizmjenično rade u režimu dehidrogenacije, zatim u režimu regeneracije. Etapa se izvodi na više visoke temperature i smanjeni parcijalni pritisak, koji se postiže razblaživanjem butena vodenom parom. Temperatura za različite vrste katalizator se kreće od 580 do 677, razrijeđen parom u omjeru 20:1. Kontaktno hlađenje gasa (gašenje) se vrši ubrizgavanjem vodenog kondenzata, dalje hlađenje gasa se odvija u kotlu otpadne toplote, zatim se gas šalje u skruber na pranje i dalje na separaciju. Izlaz butadiena iz mase originalnog butena je 20-35%. Selektivnost se kreće od 73 do 94%. Prednosti jednofaznog procesa dehidrogenacije n-butana u butadien-1,3 su: značajne smanjena potrošnja procesne pare; korištenje topline regeneracije katalizatora i reakcije dehidrogenacije u adijabatskom režimu i, kao rezultat, jednostavnost dizajna reaktora i odsutnost složene opreme za izmjenu topline; isključenje druge faze dehidrogenacije i operacija separacije butan-butilenske frakcije. Zbog toga se relativno nizak prinos butadiena-1,3 (12-14%) i stepen konverzije n-butana (koji ne prelazi 0,2) kompenziraju nižim kapitalnim troškovima i energetskim intenzitetom proizvodnje i kao rezultat , niža nego kod dvostepene metode, cijena butadiena-1,3. Shodno tome, nakon analize navedenog, može se vidjeti da je metoda dvostepene dehidrogenacije butana energetski intenzivna i zahtijeva složenu tehnološku shemu. Za industrijsku implementaciju to je neisplativo, jer će biti potrebni značajni troškovi energije. Stoga je postojala potreba da se pronađe alternativni metod dehidrogenacije. Pokazalo se da se ovaj proces može odvijati i po jednostepenoj shemi, iako termodinamika procesa postavlja jasnu granicu za prinos ciljnog proizvoda. Ali s povećanjem temperature i smanjenjem tlaka, prema ovoj shemi mogu se postići dobri rezultati. U ovom članku, kao rješenje problema, razmatra se metoda dehidrogenacije pod vakuumom koju je u SAD izumila kompanija Goodry. Kako se pokazalo, ova metoda ima niz prednosti i daje dobar prinos proizvoda. Da bi se povećao prinos ciljnih proizvoda, povećala selektivnost i smanjili troškovi materijala, potrebno je provesti daljnja istraživanja utjecaja dubine vakuuma na dehidrogenaciju butana i butilena.
Izgledi za proizvodnju i upotrebu butadiena u Rusiji
Glavni pravac potrošnje butadiena u Rusiji je proizvodnja gume razne marke(divinilstiren, butadiennitril, polibutadien, itd.); mala količina butadiena se koristi u proizvodnji akrilonitril butadien stiren plastike (ABS plastike), divinilstiren termoplastičnih elastomera i lateksa. Gotovo svaki veći proizvođač ima vlastitu sirovinsku bazu baziranu na frakcioniranju.
Procesi razvijeni za dobivanje butadiena kao ciljnog proizvoda su dehidrogenacija butana ili butena, kao i odvajanje butadiena iz C 4 frakcije kreking plinova (BDF). Glavni proizvođači butadiena metodom izolacije ciljnog proizvoda su OAO Nizhnekamskneftekhim, OAO Omsky Kauchuk, OOO Togliattikauchuk i ZAO Kauchuk (Sterlitamak).
Metoda dehidrogenacije butana uvedena je u dva preduzeća u Rusiji - u OAO Tobolsk Petrochemical Company i OOO NKNKh-Divinyl. Implementirana tehnologija, uprkos svojoj istorijskoj zrelosti, izuzetno je tražena Rusko tržište. To je zbog dva glavna faktora: stabilnog trenda rasta proizvodnje tečnih plinova - sirovinske baze, i pozitivnog trenda rasta proizvodnje sintetičkih kaučuka - potrošača butadiena. Dakle, NKNKh-Divinyl nije samo proizvođač jednog od ključnih monomera u petrohemijskoj seriji "tečnih gasova" - gume, već i značajan potrošač (do 175 hiljada tona godišnje) normalnog butana. Osim toga, tehnološki kapaciteti jedinica CGFU, koje su dio Nizhnekamskneftekhima, omogućavaju odvajanje ciljne vrste sirovine (normalnog butana) od tehničkih frakcija butana itd.
U 2007. godini u Rusiji je proizvedeno 404,1 hiljada tona butadiena: 54% metodom jednostepene dehidrogenacije n-butana, 46% ekstrakcijom iz frakcije pirolize. U 2009. godini proizvedeno je 409,7 hiljada tona, au 2011. godini, zbog povećanja kapaciteta, skoro sva ruska preduzeća uspela su da dostignu vrednost od 483,9 hiljada tona/g butadiena. Ali čak i sa takvom proizvodnjom, godišnji nedostatak butadiena u 2012. iznosio je oko 200 hiljada tona godišnje, što je uticalo na proizvodnju svih vrsta proizvoda koji sadrže butadien. U uslovima trenutne sirovinske krize u industriji butadiena, cene butadiena su porasle više od 2 puta. Prodajna cijena butadiena - 1,3 proizvedenog u OJSC Tobolsk-Neftekhim od marta 2012. iznosila je najmanje 100 hiljada rubalja / tona. Drugi ruski proizvođači nisu imali komercijalnu proizvodnju butadiena, sav proizvod koji su dobili potrošili su na vlastitu potrošnju.
Izgledi za proizvodnju i upotrebu butadiena u inostranstvu.
U inostranstvu se široko koriste procesi za dobijanje butadiena iz n-butanske i/ili butan-butilenske frakcije, i izoprena - iz izopentanske i/ili izopentanizoamilenske frakcije, što je proces katalitičke dehidrogenacije ugljovodonika - proces "Katadien" kompanije za razvoj " Air Products and Chemicals" (SAD). Modifikacije Catadien procesa izvršio je ABB Lummus Crest (SAD).
Najveće kapacitete u 2003. godini (hiljadu tona godišnje) imale su sljedeće zemlje: SAD - 2592, Japan - 1012, Kina - 768, sjeverna koreja- 724, Njemačka - 505, Francuska - 420. Najveća fabrika butadiena na svijetu je preduzeće Huntsman kompanije u Hjustonu (SAD) - 544 hiljade tona godišnje. Očekuje se da će tokom 2001-2006 više od 580 hiljada tona novih kapaciteta biće pušteno u rad u severoistočnoj Aziji.
Tehnološka shema dehidrogenacije butana i butena
Prečišćena frakcija butana iz separatora 9 ulazi u isparivač 10. Pare ugljovodonika se prvo pregrevaju u pregrejačima 8 do 275 0 C, a zatim u cevnoj peći 2 - do 530 - 550 0 C. Iz peći se pregrevaju pare butana pod pritiskom. 1,5 atm se šalje u reaktor 7 sa fluidiziranim slojem katalizatora. Dehidrogenacija se vrši na 580 C. Da bi se postigla ova temperatura, katalizator zagrejan na 640 - 650°C kontinuirano se dovodi u reaktor iz regeneratora 6. Temperatura u reakcionoj zoni se kontroliše promjenom omjera cirkulacije katalizatora (obično je cirkulacijski omjer u rasponu od 14-20). Dakle, u ovom procesu, katalizator je i rashladno sredstvo. Kontaktni gasovi iz reaktora, nakon što su prošli pregrejače 8 i isparivače 10, ispiru se vodom u skruberu 11 i hlade. U separatoru 13 kontaktni gas se odvaja od teških ugljovodonika i šalje na separaciju.
Istrošeni katalizator na izlazu sa dna reaktora tretira se dušikom kako bi se desorbirali ugljovodonici. Fino zrnati katalizator se šalje u regenerator kroz pneumatsku transportnu cijev uz pomoć zraka b. U regeneratoru, naslage ugljenika na površini katalizatora se sagorevaju kiseonikom vazduha u fluidizovanom sloju. Međutim, toplota koja se oslobađa tokom sagorevanja naslaga ugljenika nije dovoljna da se katalizator zagreje na potrebnu temperaturu (≈650°C). Zbog toga se gorivi gas uvodi u regenerator kroz mlaznice, pri čijem sagorevanju se oslobađa dodatna toplota.
Regenerirani katalizator prolazi kroz desorber, gdje se pročišćava butanom kako bi se uklonio adsorbirani kisik i dodatno smanjio heksavalentni kisik.
hroma do trovalentnog. U ove svrhe troše od 3 do 5% butana koji se isporučuje u proces; butan iz desorbera se koristi kao gorivo koje se dovodi u regenerator za sagorevanje. Fizička toplina izduvnih plinova iz regeneratora koristi se u kotlu otpadne topline 5 za proizvodnju pare. Prašina katalizatora, zahvaćena gasovima iz regeneratora, vlaži se u aparatu 4 i taloži se u elektrofilteru 3.
Spisak korišćene literature
I.P. Mukhlenov, Kataliza u fluidizovanom sloju - L.: Hemija, 1917.
AA. Nazarov, D.F. Yulbarisov, S.I. Ponikarov, Priprema butadiena dehidrogenacijom butana i butadiena
A.P. Pisarenko, Z.Ya. Khavin, Kurs organske hemije. - M.: Viša škola, 1968.
S.K. Ogorodnikov, Priručnik petrohemičara. U dva toma. T. 2. - L.: Hemija, 1978. - 592 str.
A. Riche, Osnove tehnologije organskih supstanci. - M.: Državna naučna i tehnička izdavačka kuća hemijske literature , 1959.
A.G. Liakumovič, R.A. Akhmedyanova, T.M. Bogačeva, K.V. Golovanova, Sadašnje stanje industrije butadiena - 1.3 i proizvoda na bazi njega. Problemi i izgledi. 2012