What brick is better for facing at home - ceramic or silicate. Ceramic or silicate brick: Compare two material
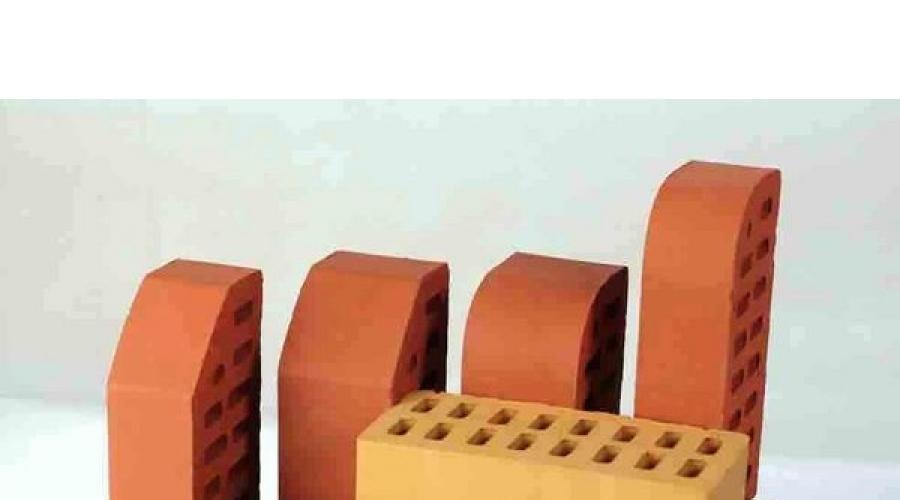
Humanity has always shown to show creative abilities. The items created with their own hands became proud of the author. Some specialize in small products, others on large-scale construction sites. The latter, creating homes, are forced to solve complex tasks associated with the choice. Because you can create anything if you own sufficient information on this issue.
During the construction of the building, it is necessary not to delay the issue with the materials used. Including Their characteristics and tasks for which they are intended. The most popular now are the following types of bricks:
- Ceramic, which is made of clay by firing.
- White, which is made from lime and quartz sand by sintering at high temperature.
To choose bricks consciously, you must first determine the requirements for them:
- Location of the object.
- Required class moisture protection.
- What pressure must withstand.
- Planned construction work costs.
- Basic data and aesthetics.
In size, bricks can be divided into 3 classes: Single, one-time and double. The sizes of the base in them are 250 to 120 mm. And the height equals 65, 88 and 138 mm, respectively.
Calculate material consumption according to the following scheme. Input parameter will be The thickness of the seams, it takes equal to 10 mm. As a result of simple computing, we have that one masonry cubometer contains 395 single, 302 thickened and 200 double bricks. The duration of work and the spent solution has a dependence on the magnitude of the brick: large stones perform the masonry more profitable.
Ceramic and can be divided into groups according to their intended purpose:
Facing brick applies to perform finishing finishing of street masonry. It must meet very stringent requirements. The surface of its very smooth, the geometry is ideal, and the dimensions correspond to the standard to a millimeter.
An ordinary brick is used to build the array of walls.
There are other types of bricks on sale, which are highly specialized. Fireproof and chimney bricks are ideal for masonry furnaces and pipes, because it is easily withstanding large temperatures. Clinker bricks can be brought to garden tracks and lining the base.
Ceramic and silicate stones have differences for the following characteristics. Freezing and pressure resistance - key stone characteristics. The strength of the brick has a fairly accurate gradation and begins with M50. The number that stands after the literator indicates the load on the brick, which can withstand 1 square centimeter of its surface.
If the planned building will have no more than 3 floors, then you can limit the choice of stone with a density M100-125. More dense bricks are used as a material for building greater floors.
Frostability resistance in brick has its gradation. It begins with F15. The number makes it clear how many times the brick can be freezed and defrosting so that it began to lose the declared physical characteristics.
Ceramic and silicate brick may have cavities and be without them. Full-tempered should not have cavities, or their number should not be more than 13% of the volume. He is able to withstand large loads and high humidity. Even the interior partitions in the bathroom and the toilet are better to perform this type of stone.
The advantages of bricks with cavities are obvious: it has a low thermal conductivity and low weight. Thanks to this, the walls in the house can be made less thickness, which reduces pressure on the base.
Ceramic and silicate stones have a different area, shape and number of cavities. It is recommended to choose stones whose cavities are thin, narrow and long. This Council has very serious grounds. When laying in the hole, the masonry mixture falls, it reduces thermal properties. And with the specified parameters in the cavity, the minimum amount of cement mortar will fall.
Silicate brick is usually done without cavities, possessing a density of 1800-1900 kg per cubic meter. You can find such a brick having holes (from 15 to 30%) that are not passing through the thickness of the brick. Its density will be equal to 1500-1550 kg per cubic meter.
The percentage of cavities in ceramic can reach 55% at a density of 1500-1550 kg per cubic meter. Consider that if a silicate brick will be chosen to complete the house, it will provide an increased load on the base.
There is a demand for consumers to ceramic bricks with pores, having increased heat conservation efficiency. When it is made in a mixture of clay include lightweight materials (sawdust, straw, etc.). In the firing process, they burn, leaving in their place a small cavity. There are many such pores and they strongly increase the ability of the stone to absorb sounds.
Keep in mind that single stone is solely full, and thickened can be in two versions as well. The latter is practically not full.
Screwing moisture and freezing resistance
Silicate brick has its drawbacks that limit the places in which it can be used. It is unacceptable to apply for the construction of the foundation, basement and basement. It is impossible to lay the walls of wet rooms out of it.
He has a very high self-humidity (from 16 to 18%), as well as a percentage of water absorption (from 10 to 13%). Stone with voids has great indicators than without them. Ceramic brick absorbs only 6 to 13% water. And the clinker is even less from 2 to 3%.
Silicate brick is not suitable for masonry furnaces, fireplaces and chimneys. For this purpose, only ceramic bricks without cavities are used. This is due to the fact that white brick Starts to collapse already at 800 degrees.
Ceramic brick, which is designed for cladding is able to dry very quickly after wetting. This characteristic explains the resistance to biological destruction.
With moisture absorption, resistance to negative temperatures and the life of the product are closely connected. This is especially true of the facade cladding. For its construction, stones are used with a large significance of frost resistance. Silicate brick has an indicator F25-35, in exceptional cases to F50. Ceramic brick has the value of the F50 coefficient. The clinker can also have F100.
Thermal conductivity and ability to skip steam
If the conversation came about the facing material, then warmly depends on the ability to absorb moisture specificationsand products. Squeezing masonry entails a strong decrease in thermal insulation capacity.
Comparing the thermal conductivity coefficients of bricks of different composition, You can make a simple conclusion: the red brick building will be the warmer of its own analogue of white.
An additional bonus owners of the house of ceramic brick is its naturalness. It is able to breathe and skip steam.
conclusions
After analyzes and calculations, it is worth choosing the material that is better suited for a particular case. Ceramic brick has a greater value than a silicate one and a half times.
Choosing a brick as a construction material is definitely correct solution. Houses of brick stand no one hundred years. Brick due to the peculiarities of production is an eco-friendly and harmless material, moreover, possessing unique characteristics, such as high strength, frost resistance, moisture resistance and thermal conductivity. A variety of brick species can confuse any buyer. What brick choose: silicate or ceramic for the construction of the cottage? To begin with, let's try to figure out what their significant difference is.
Ceramic brick.
Ceramic bricks are made of clay and sand by firing when high temperaturesoh. This is an oldest production technology. Clay pick one of the species with greater moisture degree or less. Brick made of clay, humidity 17-30% gets additional advantages in the form of an opportunity to use it in rooms with high humidity.
During production, the following types are obtained: full, hollow, facing, chamotte and clinker. Hollow ceramic brick due to production technology forms air cavities. Cavities can be seen in the form of round, oval rectangular or other shape of the holes. Thanks to this, such a brick is characterized by the best pike and heat-insulation. Also, such bricks are much smaller. It is used both as the construction of carriers and as the construction of undesiable walls. It should be noted that its price is an order of magnitude below the full-scale analogue. At the same time, you can at all doubt that all other characteristics will remain unchanged: moisture resistance, strength and frost resistance also remain at a high level.
Full-time ceramic brick is highlighted by special strength and is used in the construction of bearing walls, chimneys, buildings of buildings. It is already much more severe than its hollow conifer.
Chamotted ceramic brick found its application in the construction of furnaces and fireplaces. It is able to withstand the temperature differences, and also has high refractoriness. Such a brick is laying out exactly in those places where it will be in close proximity to fire: it can withstand temperatures up to 1600 degrees Celsius. Chamotte brick refers to ceramic bricks by the fact that in its composition special fire-clay and powder shame. Such a brick turns out a pleasant sandy or golden color. And the strength is one of the best: it is very difficult to cut, saw or handle.
Clinker ceramic brick is obtained from refractory clay varieties at very high temperatures. Its feature is the greatest strength of all kinds of bricks and durability. Externally, it looks dense without cracks and emptiness. But in price, it is very different from other types of bricks, so that its use is advisable, only in some places for hardening, for example in the construction of the base.
Facing ceramic brick make both hollow and full-length. Also, it can be different. For its laying, colored mixes often use. The main feature of such brick is its high frost resistance and low water absorption, as high demands apply to facing brick.
Ceramic brick can be of different colors from yellow, apricot to bright red, burgundy. It is not necessary to scare that the color does not coincide with the usual understanding of the type of brick, this does not mean that impurities were used in its production. This is due to the fact that when it obtained it uses the clay of different varieties and from different areas of production. Clay color and gives a characteristic color of brick.
In addition to these types of ceramic brick, you should pay attention to the technical characteristics suitable for both silicate and ceramic bricks. This strength (is expressed in the MARK M, is measured in maintaining the load of kg per sq. Cm), frost resistance (MPZ, F, is tested by a cyclic method), thermal conductivity, noise insulation, moisture absorption. Based on the technical characteristics and types of bricks, it becomes clear that on one house you may need various types of bricks. Most importantly, choosing a brick for one element, pick it up from the same batch, as depending on the clay, its composition, color and firing, you will receive a batch of one shade. Otherwise, you will have a long time to look for the missing missing brick.
Based on the stated characteristics and production technology of various types of ceramic brick, we advise you to choose the following types for individual items:
For foundation - high-strength, frost-resistant, and, the main thing that does not absorb moisture, i.e., a full ceramic brick or clinker brick.
For base - full ceramic brick
For furnaces, fireplaces - chamotte brick, refractory and durable.
For the facade - facing or clinker brick
Ceramic hollow and full-length is suitable for the walls.
Silicate brick.
Silicate brick is made by an autoclave method from a mixture of sand, lime, water and some other additives. Silicate brick is also produced by hollow and full-length. Hollowly as in the case of ceramic hollow brick wins in thermal insulation qualities in full-scale, and also has a smaller weight. All technical characteristics are also applicable to the choice of silicate brick, such as strength, frost resistance, heat and noise-insulation (which is an order of magnitude higher than that of ceramic bricks) and water resistance. Also a certain plus, in favor of selecting silicate bricks will be more low price. So why is a silicate brick not number 1 in the list of the best building materials?
Frost resistance and resistance to temperature differences in ceramic bricks are much higher than that of silicate. That is why it, for example, is not used in the construction of furnaces and fireplaces. Also, low moisture resistance does not allow the use of silicate brick for the construction of foundations. However, as some specialists noted, there is an erroneous opinion that silicate bricks have very low moisture resistance. All other things being equal, a drop of moisture on a ceramic brick is absorbed far faster than on silicate. However, it will not cause any constructive changes on the first. And with constant humidity, silicate brick can lose its strength characteristics and start crumbled. It is also not recommended to use it in the construction of foundations and due to non-resistance to aggressive media: such as groundwater, salt.
The thermal conductivity of silicate brick is almost 2 times higher than that of ceramic, which forces the thicker walls. Despite the fact that silicate brick has a rather presentable view, as well as a large variation of shades, the use of it as a facing facade may not be the most the best option. The fact is that silicate brick is characterized by high hygroscopicity, so it easily absorbs all atmospheric precipitates, which can significantly worsen the color of the facade over time.
Thus, applying everything above, we can conclude that when building a brick house, you will need different types Brick. What is silicate, that ceramic brick is distinguished by environmental friendliness, durability and durability. The choice of one or another type for construction is determined by the objectives and characteristics of the facility under construction. That is why it is impossible to say that it is better: silicate or ceramic brick. Each has its advantages and disadvantages, and the choice is determined by the appointment of the material.
With the current diversity of constructive materials offered today by manufacturers for low-rise construction, a person is not easy to decide on the choice, since the mass of issues arises. The consumer must have detailed information.
What a brick: ceramic or silicate, more profitable for construction from a financial point of view; What walls will be better to maintain heat; How does the laying on the atmospheric moisture and temperature differences react? Video in this article, called: "Silicate and ceramic brick: comparison," will give answers to many of them, and will help our readers to make the right choice.
Lime-colored brick
Fast turning and slow lime hardening, served a barrier for a long time for its use in the production of artificial stone than by and large and is any brick. Nevertheless, at the end of the XIX century, the technology of autoclave processing of lime and sand mixtures was created, of which, with high pressure and simultaneous heating, moisture-resistant, and very durable stones were obtained.
The thing is that at one hundred percent humidity, and the temperature from +170 degrees and above, silicon dioxide contained in the sand enters the chemical reaction with lime. As a result, a fundamentally new substance is formed, which is called calcium hydrosilicate, very close by characteristics to cement.
Therefore, such technologies are used today not only in the production of bricks, but also for the manufacture of concrete and large-format wall articles. Concretes using calcium hydrosilicate as binder, require less, compared to cement options, consumption. Hence the lower price, which is the undoubted advantage of this raw material.
Manufacture
The brick lime-sand, which we are all accustomed to call silicate, more than 90% consists of sand. Lime in it is only 5-8%, and about the same amount of water.
It is quenched after the scene compounds - depending on the method used, in drums or silos. Then, the mass is supplied for additional moisturizing to the agitator, after which it is sent to the press.
So:
- For pressing silicate brick, pressure is required up to 200 kg / cm2. The raw is molded, stacked on the trolley, and is directed to hardening in an autoclave, which is a twenty-meter cylinder with hermetic covers. As the temperature increases, the calcium hydrosilicate formation reaction is accelerated, and flows at least 8 hours.
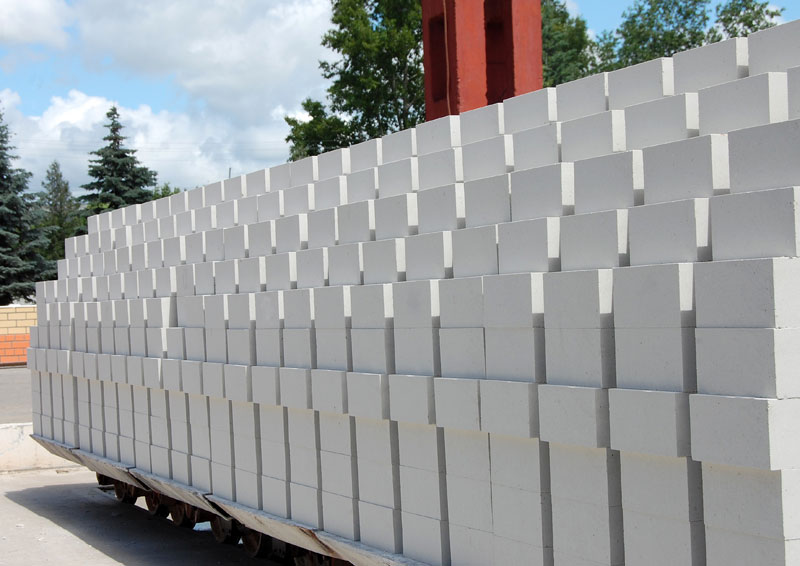
- To accelerate hardening, pairs are served in the autoclave, and under rising and periodically declining pressure, the products are kept still in the pasty, during which the raw brick turns into a very durable stone. As for the shape and sizes, there is no difference here - silicate or ceramic brick.
Brick dimensions Standard: Length 250 mm, width 120 mm. In height, there may be options: single, corresponds to 65 mm; 48 mm half; and double 138 mm.
The only one, ceramic bricks still have the format "Euro": 250 * 85 * 65 mm, which appeared not so long ago, but is envisaged by the standard updated in 2007. The lowest brand of silicate brick - M75, the highest - M300, and their seven.
We analyze the dignity and disadvantages
Apply lime-sandy bricks for the same goals as the clay brick - but still, for him there are some limitations.
Note! Silicate materials It is not recommended to use for the construction of foundations, outlined walls of basements and the basement of buildings, since the strength of the stone is reduced in a humidified state. Do not use this brick and for masonry furnaces, since during prolonged heating its structure is destroyed.
- In other cases, silicate brick can be used without any restrictions, since in many indicators it is practically not inferior to his ceramic fellow. By the way, there are two more types of silicate brick, where slag or ash is used as a filler instead of sand. These are very cheap raw materials, actually being the waste of production.
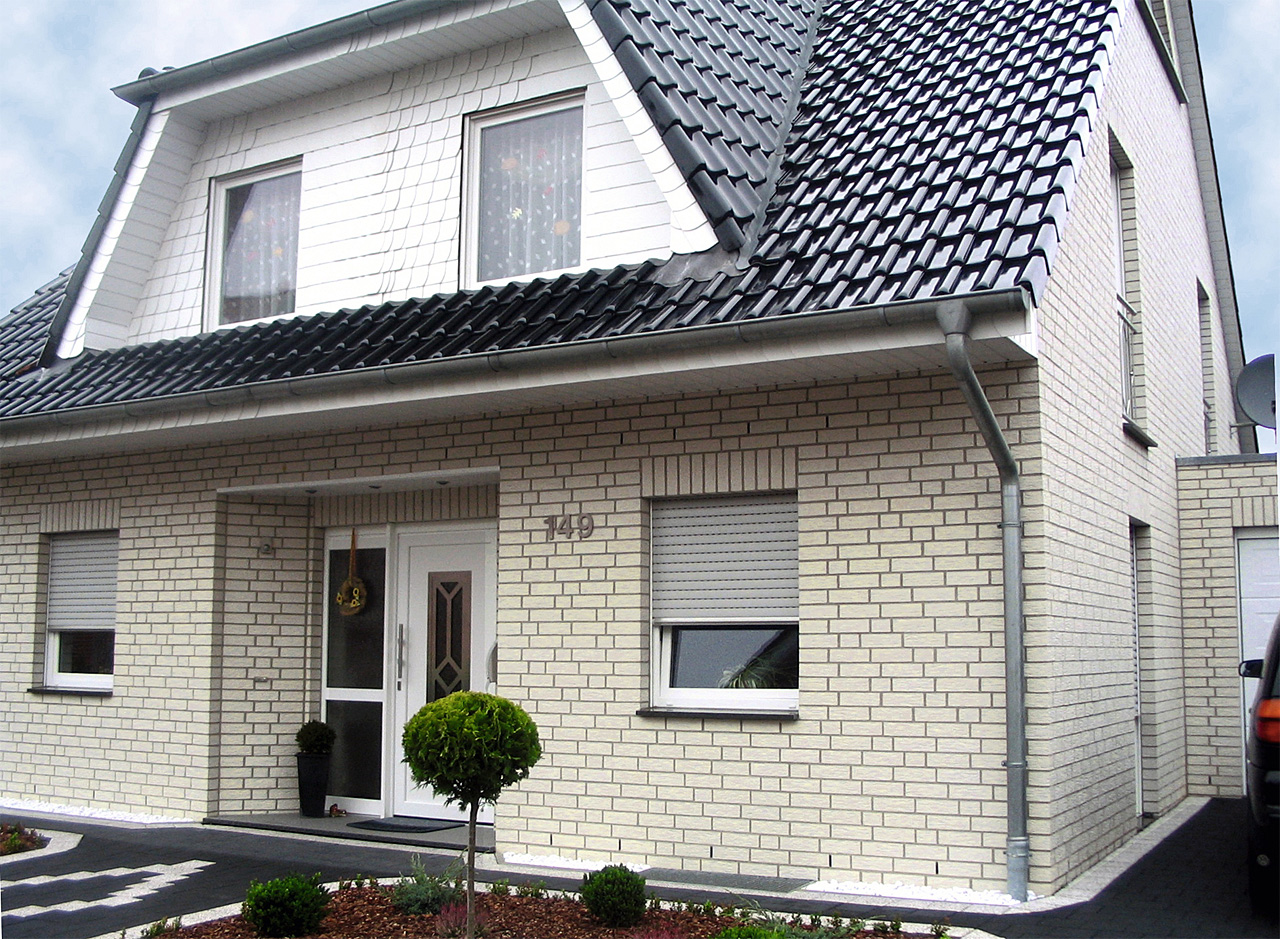
- The manufacture of ash and slag brick is most beneficial from an economic point of view. The production technologies are used the same, only this brick on the format is more (250 * 120 * 140 mm). According to the characteristics, he is not inferior to the brick lime-sandy, and is manufactured according to the same standards. But how to compete ceramic, silicate brick on heat engineering indicators, you will be easier to see in the comparative table.
Take as the basis of the most popular in private construction, a single full-time version of the M125 brand:
- Now, when there are specific numbers before your eyes, it will be easier to see the difference in the indicators - and we comment on them. The thermal conductivity of silicate, ceramic brick - if both, and the other full, is different. The fact that this indicator is closer to zero, the better the masonry keeps heat.
- Alas, no full-length brick can boast of high thermal insulation properties, and it is worse in this regard only reinforced concrete. W. hollow Bricks These characteristics are much better, but it is inferior to a full-scale brick, called ordinary, for strength.
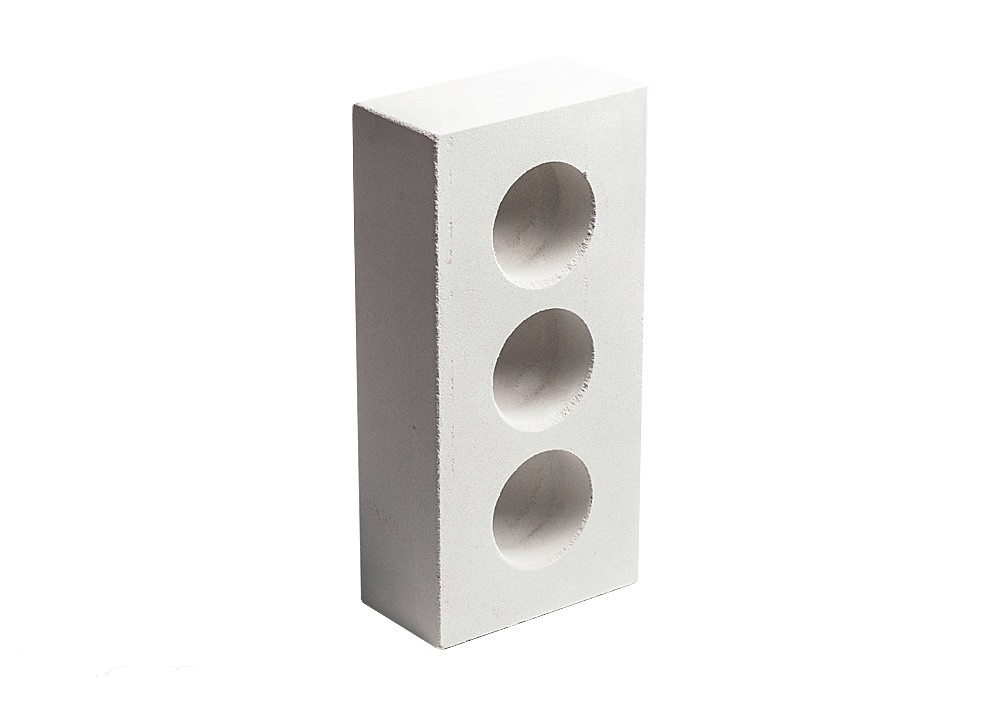
- To achieve a golden middle, carrying walls are brought from ordinary bricks, and we are lined with a void, laying the insulation between two walls. By the way, the hollow brick is not only ceramic, but also silicate.
- The difference consists only in the fact that the last emptiness does not come through that we are visible in the photo. The clay brick most often has through vertical or horizontal emptiness, and is called slot. Strength and frost resistance in clay and silicate full-scale brick is the same.
But density, and accordingly, the weight of the silicate brick, a little more. This fact can be attributed to negative qualities, since the foundation under such a masonry should be more powerful.
But these costs are fully compensated by the lower cost of the brick itself. Only now, the higher water absorption is not compensated by anything, therefore, silicate bricks have restrictions in use.
A little about ceramic brick
So, we continue to argue on the topic: "What is better, ceramic brick, or silicate?". In general, in Russian intelligent dictionaries, the word "brick" is interpreted as "hit from clay, and burned bar".
Consequently, everything that is not done from clay is not suitable for the definition of brick. In essence, silicate brick is a solid stone, only like a brick in shape, as well as some physico-technical characteristics.
So:
- Despite some similarities, these two materials produce different standards, and there is a fairly clear boundary between them. Silicate brick today is made not only for simple masonry, but also offered decorative options: Colored, embossed. And, nevertheless, it cannot be compared to the assortment with the brick ceramic.
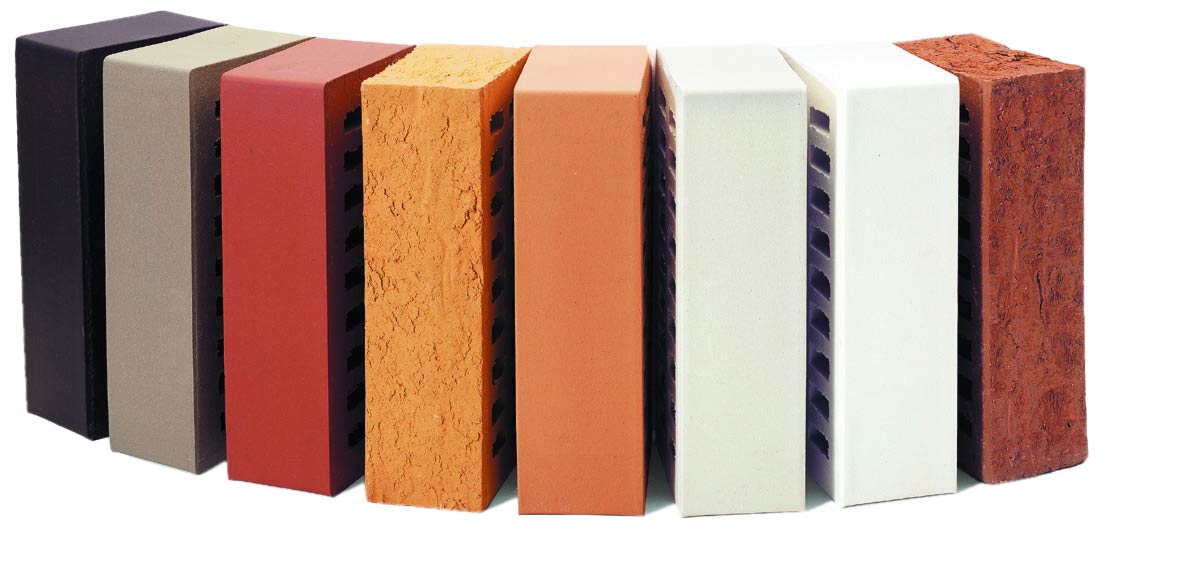
Varieties of clay bricks
In addition to the ordinary and hollow brick, there are still decorative options that are called facing, or facial bricks. There is a mass of variations: this is the widest color gamut; and surfaces treated in such ways as genuing, glazing, mechanical apposition. W. decorative bricksBy the way, enlarged at least two faces.
- There is also a shaped brick, with which you can bind the columns, round out the outer angle, it is beautifully arranged window openings, form a bonding tide, or lay out the arched jumper. Perhaps such complex designs will not always be done with their own hands. But if there is a desire, then the necessary instruction, which will help in work, will certainly be found.
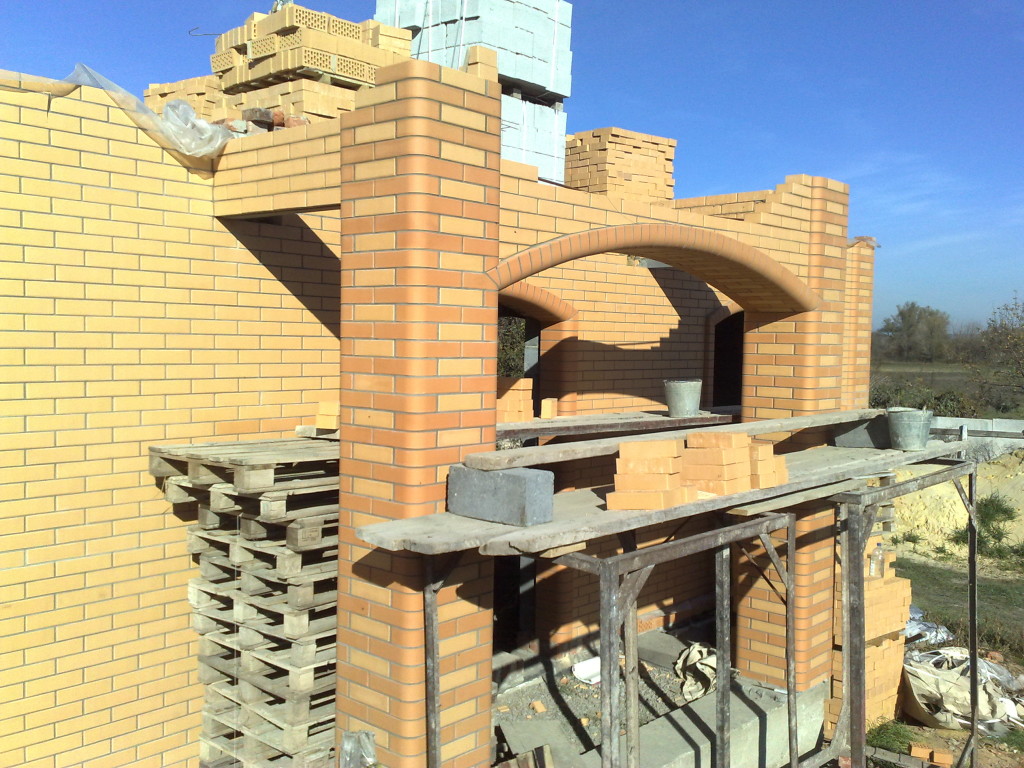
- Another argument that speaks in favor of ceramic brick is that it is not afraid of elevated temperatures. For this reason, it is precisely it is used to build furnaces, fireplaces and chimneys. Usually the part that directly contacts the fire, lay out from fireproof bricksmanufactured from chammed clay.
But for the facing of the outer surfaces of the furnace or fireplace, adjacent wall, as well as grude ovens, uses clinker, or ordinary ceramic - including the shaped brick.
Heat engineering and other properties
Of all the above, it is quite understandable that the ordinary brick is used to masonry the outer walls and partitions, and the facial serves as a decorative frame of the wall from the working brick. If we talk about the heat engineering properties, then according to this indicator, this material is conditionally divided into three categories.
So:
- The first group includes options with high thermal insulation characteristics. It is a slit brick and ceramic blocks with a density of less than 1400 kg / m3. Their use allows you to reduce the thickness of the walls - if you compare it with a thickness of a masonry from full-scale brick.
- The second option is indicated as conditionally effective. This is a hollow facing brick, with a density in the range of 1410-1600 kg / m3, which only improves the characteristics of the main structure. Well, to the third, ineffective category, the ordinary brick belongs, the density of which exceeds 1610kg / m3.
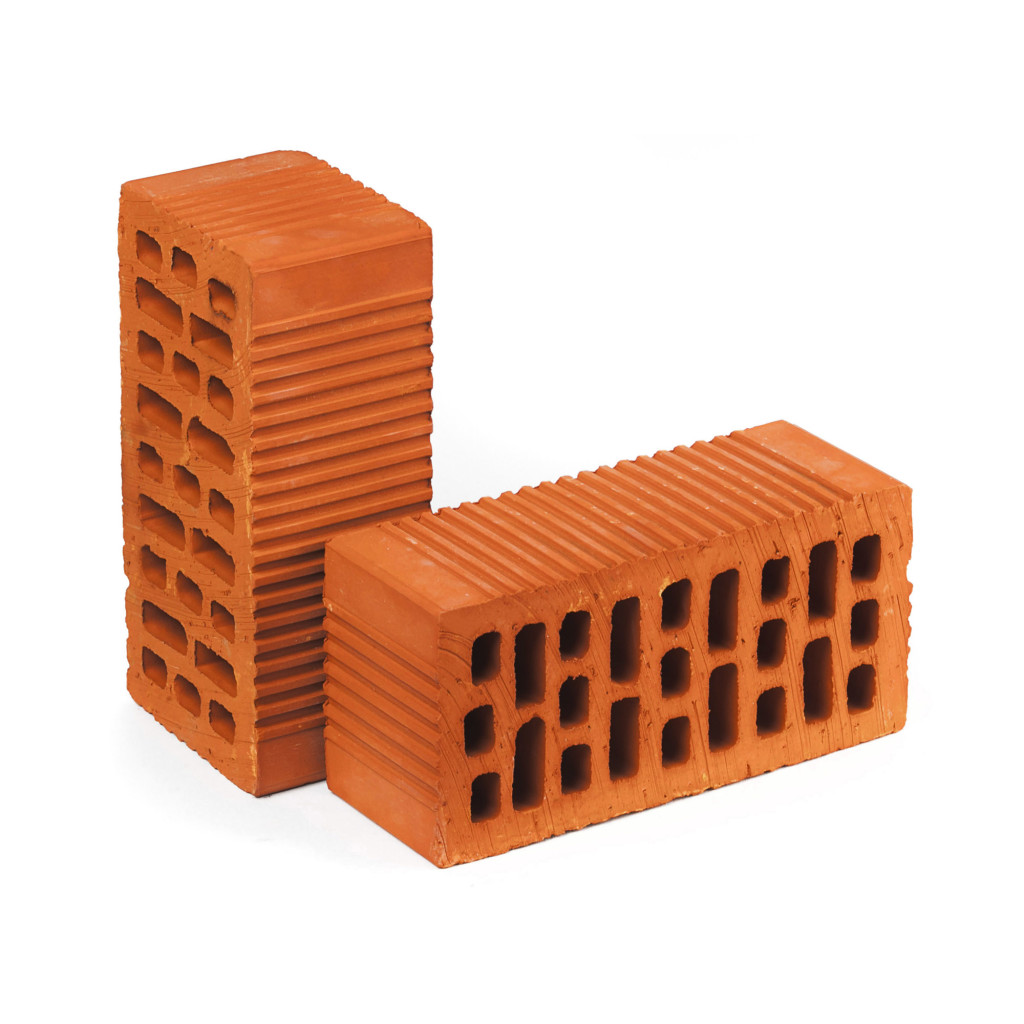
Effective brick: features
In the photo from above, you see the representative of the first group - it is a thickened (one-hour) slotted brick M-125 brand. Its density average is 1210 kg / m3, and the thermal conductivity coefficient corresponds to only 0.36 W / (M * K).
Comparing these indicators with a sign in which we led the characteristics of full-scale bricks of the same brand, we immediately see a difference that does not doubt that this option was not for nothing called effective.
- Its heat engineering properties are twice as much as full brick. Slital brick is also called workers, because it can be used for the main masonry of the walls. Although of course, such a masonry cannot compete in strength with masonry from full-scale brick. If you, for example, you need to build a foundation, then any of the hollow material of speech and can not be.
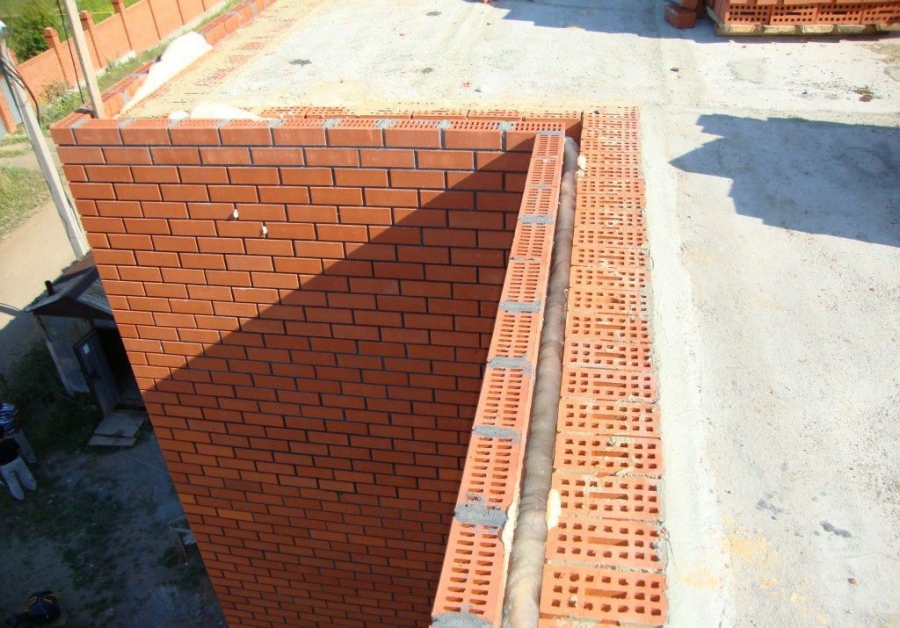
- For the construction of multi-storey buildings, the effective brick is also not used, since the load is too large. The only one can lay out the walls of the upper floors from it, or fill out the spills of frame buildings. But there the entire load is carried by the framework, and the task of the filling material is precisely in ensuring proper thermal insulation.
- But for the walls of low-rise buildings - this is exactly what you need. The use of hollow ceramic bricks and blocks, made it possible to perfectly solve the problem of thermal insulation walls of buildings. As a result, it caused a decrease in the cost of their operation, and, without prejudice, the quality of the structures.
- In addition, the cost of the object is reduced, because thanks to a smaller weight of the enclosing structures, it becomes below the load, and, accordingly, the costs of the foundation. And this is not all the advantages of the slotted brick. Thanks to the profile existing on the side of the sides, the joints between bricks are obtained almost hermetic, and the solution consumption is significantly reduced.
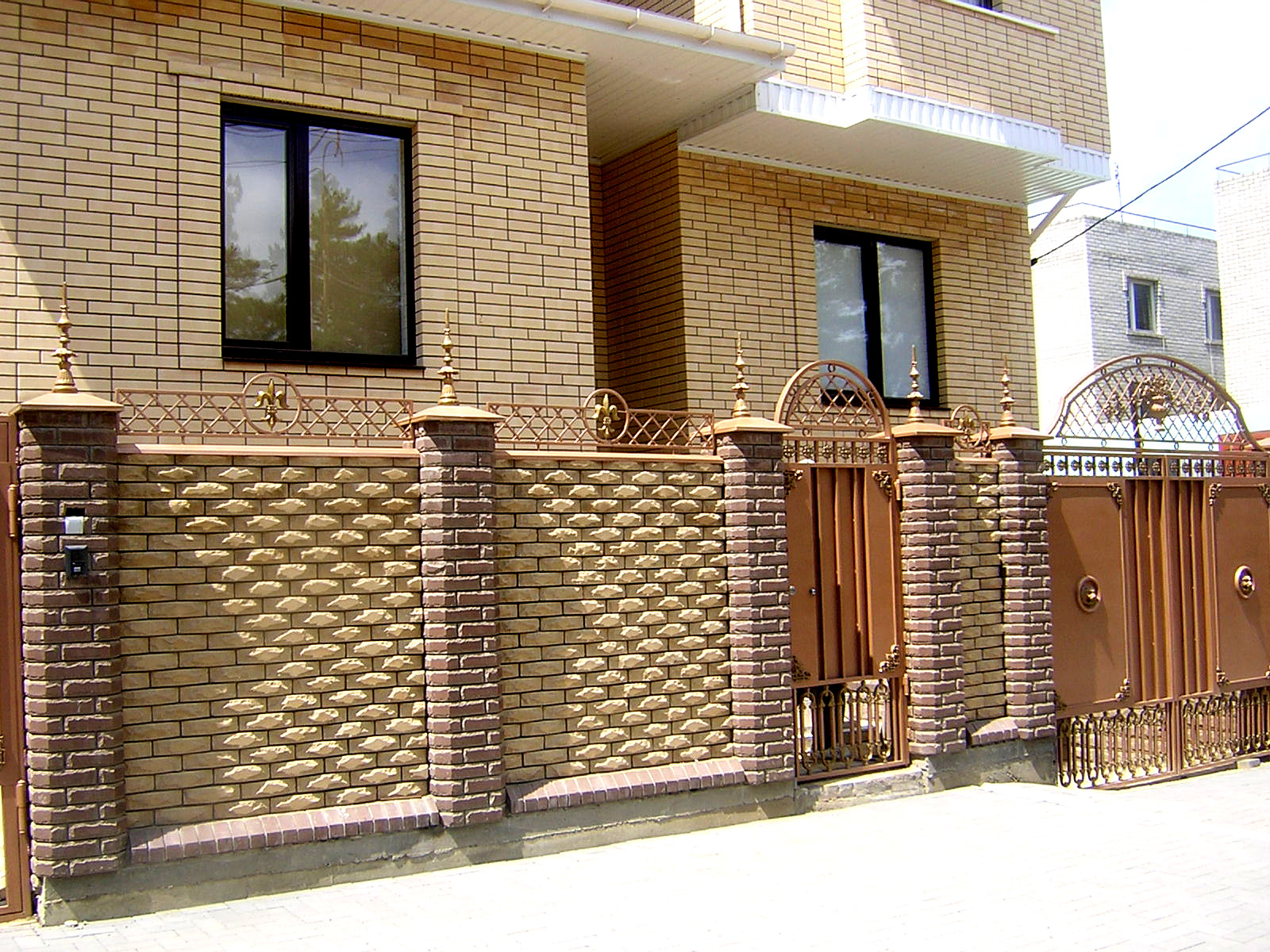
The time consideration of the construction of walls is reduced, since instead of multiple masonry, the porous brick or the block is stacked in one row. With all these advantages, the price of a single slotted brick does not exceed the cost of the usual full-scale.
All the above confirms the undoubted advantages of this material, turns into direct economic benefits. Isn't this goal that is first of all any customer?
Walls of any building need protection against bad weather, harmful effects of heat and frost, mechanical effects. The role of such protection performs outdoor facing. And since in our country it is most often made of bricks, a challdorm question arises: what facing brick is better to use for this?
Regardless of which the house itself is built, it can be bred by brick. The laying technology will be slightly different depending on the material of the main walls, but it does not affect the choice of bricks.
The differences of ordinary and facing bricks
Made of one raw material, facing and ordinary construction brick Have a lot of differences.
- The structure is unlike full-scale ordinary artificial stone, facial is done hollow, with several cavities. They make it easier, simplifying the transportation and work of builders, and also increase heat insulating properties Facing.
- Frost resistance and moisture resistance facial brick above. This is important because he has to withstand a constant negative impact. external environment.
- Appearance. Color, shape, surface texture facing bricks Maybe anyone. This allows you to implement any exterior solutions, harmoniously entering the structure into the surrounding landscape.
- The price of such a brick is higher. The cost of facing works is higher compared to the usual masonry, as they require care, accuracy and creative approach. But if they are produced qualitatively, the owner of the house for decades will not have to take care of the repair or reconstruction of the facade.
For reference. It is worth noting that the silicate building brick, unlike ceramic, has a smooth and smooth surface, so houses that are fully built from it do not need additional decorative finish.
If the outer walls are two- or three-layer structures with thermal insulation layers of foam or mineral wool, it disappears the need and in the additional insulation of facades.
Comparative analysis of silicate and ceramic facing brick
Basic requirements for external finishing materials - These are high performance and attractive design. Let's see what bricks have these parameters better.
Performance features
Compare the parameters on which the durability of the brick facade and its thermal insulation properties depends.
- Water absorption. At silicate stone it is higher than ceramic and reaches 13-15%. Products from burned clay are more resistant to moisture, and some species, for example, differ in very low water absorption (2-3%).
- Frost resistance. For the climate, most of our country is one of the main indicators. It depends on water absorption directly, as it shows how many freezing and defrosting cycles saturated with moisture material can withstand without loss of strength. And the more moisture in it, the larger loads it is experiencing. At silicate brick, frost resistance is 25-35 cycles, and in ceramic at least 50.
For reference. The most frost-resistant is a clinker brick, in which this indicator is 100 cycles.
- Heat insulating properties Also directly depend on the water absorption of the material. The presence of moisture in it sharply reduces the ability of the brick to hold heat, and in our climate, where rain and wet snow - the manual is normal, it is not worth neglected.
It is precisely because of the high water absorption of silicate brick in real operating conditions loses its thermal insulation properties very sharply. What you can not say about ceramics: it is distinguished by fairly stable indicators of thermal conductivity.
- Soundproofing. It should be recognized that due to the greater density of silicate stone, it is better coping with an insulation of air noise penetrating the room from the street. However, the noise absorption of ceramics is not much lower.
- Fire resistance. Perhaps this is not the most basic parameter for which it is worth assessing the advantages of facing material, and, nevertheless, in a fire, a silicate brick will start to collapse after 2 hours, and ceramic will withstand fire 4-6 hours.
- Ecology. If the production is followed by instructions and requirements for the composition of raw materials, then neither in red, nor in white brick does not contain substances harmful to health. Both are produced from natural natural materials: First of clay, and the second of sand and lime.
- Parp permeability. This indicator is often called breathable ability, and the clay products it is better. Insufficient vapor permeability of silicate brick requires an air gap device between the bearing wall and cladding, and for this you need to make a wider foundation.
There is no need to specify that all of the above items speak in favor of traditional ceramic bricks. Although the significantly lower cost of silicate may be decisive for many.
Designer opportunities
We all want to live not only in warm and kindly, but also in a beautiful house. And the ideas about the beauty of each of their own. Therefore, you have to pay attention to the external data of the facing material.
Choosing, which brick is better to bind the house, you need to relate an exterior decoration with its architectural style, with its surrounding scenery. Although you can enroll on the contrary: to be unrecognizable to change the appearance of your home. Assortment of brick products will easily allow this.
In this regard, ceramic and silicate brick is difficult to compare. And the one and the other can have a variety of shades, a smooth or textured surface, imitate natural stone etc. But still ceramic products They look more natural and natural.
The dimensions of those and other materials make it easy to combine them in the masonry, creating rather original and interesting solutions.
Conclusion
A huge range of facing bricks in the modern market makes breaking his head over what to choose. But if you clearly decide on the requirements that you prevent appearance and qualitative characteristics facades, the task is simplified.
In the video presented in this article you will find additional information on this topic. She will help you make the right choice.
Now there have been many materials intended for the construction of buildings, houses and other buildings. However, such a proven material, like a brick, is still in demand for the construction of walls and cladding of various surfaces. Many beginner builders do not understand, in what cases it is better to use silicate brick, and where ceramics are suitable.
The purpose of this article will be a comparison of silicate and ceramic bricks, the study of features and areas of these materials.
Technical parameters of bricks
To find out which brick is better and how silicate is different from ceramic bricks, the main characteristics of materials should be studied.
Preparation method
The composition of two types of bricks and methods of their manufacture are fundamentally different:
- Ceramic brick consists of clay, which is molded, dried and burned in the furnaces.
- The composition of silicate brick includes 90% of quartz sand, 10% of oversized lime, water, as well as some additives. Weight formulate and exposed pressure and steam in the autoclave.
Strength
The difference between ceramic bricks from silicate consists in their strength, which characterizes the ability of the block to withstand a certain weight per 1 square centimeter. Silicata has a strength equal to 150-200 kg / cm 2, and clay is 50-200 kg / cm 2. This is clearly observed the superiority of the lime-sandy block. It is from such a material that build structures above 1st floor.
Density and weight
Full-time silicate has a density of 1600-2000 kg / m 3 and greater weight. Red brick density is 1,400-2000 kg / m 3. The hollow lime-sand unit has a void of 15-30%, and its density is 1400 to 1600. The hollow block of ceramics has a voidness of 40-55% at a density of 1200-1400. As you can see, silicate exceeds clay according to these indicators.
By weight, full bricks are about the same, but the weight of the hollow silicate slightly exceeds the weight of the clay analogue.
Fire resistance
Choosing blocks for the construction of structures in contact with open flame (fireplaces, ovens, mangals), many wonder: what is better, ceramic or silicate brick? The answer is unequivocal. It is recommended to use a ceramic option that successfully resists high temperatures within 6 hours. But its silicate analogue is destroyed at a temperature of 600 degrees, and only 3 hours can withstand open fire.
There is a type of ceramic brick - chamotte block. It is made of chammed clay, therefore he has an increased degree of fire resistance. It is used to masonry the furnaces in the furnaces and fireplaces.
Thermal conductivity
From what kind of brick apply, silicate or ceramic depends on the heat in your home. In silicate brick, the thermal conductivity coefficient is 0.4-0.7 W / m * to. If the material is not new, the coefficient can reach 0.95. Ceramic brick has less thermal conductivity, at the level of 0.34-0.57 W / m * to. Consequently, the walls from it will give less heat, and the house will be more comfortable.
Important! Hollow blocks significantly reduce thermal conductivity, at the same time reducing the load on the foundation.
Frost resistance
This indicator determines the number of cycles of freezing and thawing, during which the material does not lose its properties. Denotes the letter F. At silicate it is 15-35, and improved varieties have an indicator 50. Ceramics F50 is the norm, and some species are characterized by large values. So, the clinker has F100.
Soundproofing
Silicat is superior to the degree of noise absorption ceramics. This indicator is 50-51 dB, while ceramics it is equal to 45-46 dB. Construction of white blocks interior partitions leads to a tangible increase in the level of noise protection.
Water absorption
Silicate material has an indicator of water absorption of 12%. Quartz sand, which is included in its composition, has a crystal structure. He quickly drinks moisture, but also quickly and gives her air. But the layered structure of ceramics makes it difficult to penetrate water between the layers. However, hitting there, the burnt clay will dry for a long time. This is especially dangerous during frosts, because of which the block can be broken. In ceramics, this indicator is 6-14%. The durability of silicate is connected with this.
Price category
The cost is also an important parameter when choosing a material. Silicat almost doubled in the price of red brick, if you focus on the volume.
Advantages and disadvantages of ceramics
pros
- Universality. Apply for masonry of the main walls, partitions, as well as for cladding walls and facades.
- It has fire resistance and resistance to moisture.
- It is made of environmentally friendly raw materials.
- Inert to aggressive environments.
- Large selection of shades and degrees of voidness.
Minuses
- It is not recommended to build construction more than 1st floor due to insufficient strength.
- The appearance of salt sediments on the surface is possible.
- High price.
Advantages and disadvantages of silicate
pros
- Environmental purity.
- High strength, giving the opportunity to build high houses.
- High degree of sound insulation.
- Acceptable cost.
Minuses
- Exposure to moisture. Not applied in wet rooms.
- Increased thermal conductivity.
- Restriction on refractory.
- Limited selection of colors.
Practical application of materials
When it is worth the choice, silicate brick or ceramic brick to use, you need to focus on the specific type of work performed.
Silicate brick
It is recommended to use it for the construction of the above-ground parts of the buildings, including large floors. Silicate brick behaves perfectly on the walls, additionally providing increased soundproofing of the building. Good masonry and the use of high-quality solution is the key to the durability of walls and internal partitions.
Sand-lime blocks should not be used below the soil level. It is not recommended to use blocks for the construction of baths, wells, basements, shower, basement floors and other buildings with high humidity. If such buildings have already been erected, it is desirable to process the surface with moisture-proof composition, causing it in dry weather when the material is dry.
It is impossible to lay out the silicate of the furnace and fireplaces, since the exposure to high temperatures leads to the rapid destruction of the blocks.
If the site is observed in the appearance of groundwater, it is necessary to prevent them from entering the surface of the masonry. The fact is that sulfur salts contained in groundwater can destroy silicate in the process of contact with it.
Ceramic brick
The material behaves well as the basis for walls, having a reduced degree of thermal conductivity. Fireplaces, mangals, stoves, chimneys are built from red bricks. Material can be used for finishing. Especially attractive looks like clinker in this plan. Blocks fold drain pits, wells, basements, basement floors.
You should not build a red brick wall above the first floor. Possessing not too high strength, blocks will be exposed to increased weight loads.
Knowledge of the features and basic characteristics of the facing and ceramic blocks allows you to avoid mistakes in the construction of houses, hozpostroops, baths and other buildings. And you can correctly apply these materials for cladding at home using their strengths.