Sickness do it yourself drawings. Wooden machine with their own hands. Assembly and applying turning fixture. Universal machine from electric drills. Accessories for templates
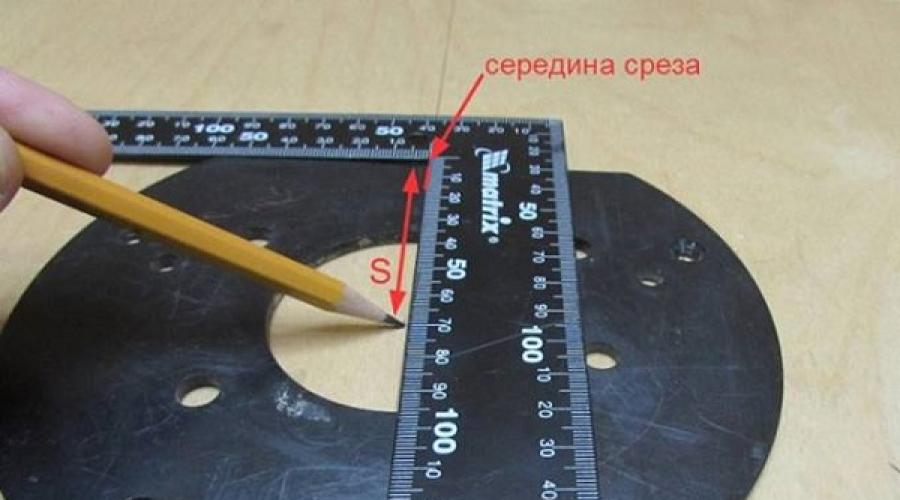
The use of various devices for a manual milling is significantly expanding the capabilities of this unit, and also improves comfort and safety when working with it. There are already ready-made models of devices intended for use in a pair with a milling mill, but, as a rule, they are expensive. Therefore, many masters prefer to make devices for this aggregate with their own hands.
If you fix a manual milling machine with a special way under the table, you will get a universal carpentry machine that allows you to produce accurate and fast processing of long and short wood blanks. To make a table for a milling hand, you first need to prepare the necessary parts for the assembly of the entire design. The figure below shows the cutting card, on which all the details of the future milling table are located. They are cut with a circular or format-cutting machine.
The device can be made from plywood, LDSP or MDF.On the map of the cutting indicated the thickness of the material is 19 mm, but this is not a prerequisite. The table can also be collected from plates with a thickness of 16 or 18 mm. Of course, for the manufacture of table tops it is better to use laminated or plastic sheet materials that will allow you to easily slide the billet on the surface.
It should also be considered that this homemade table is intended. for installation on goats. If you need a desktop option, then the kings (5) need to do much wider than 150 mm. Their width should be slightly greater than the height of the device so that it can accommodate under the table top.
If the details of the table are filled out of plywood or MDF, their ends should be polished. The ends of the details made from LDSP will need to be covered with a melamine edge using an ordinary iron.
Making countertops
The milling of the milling table can be done both using the mounting plank, and without it. Training countertops for direct fastening It occurs to it as follows.

Fastening an aggregate using a mounting plate
When installing the apparatus on the main plate, its thickness significantly reduces the departure of the cutter. Therefore, to install an aggregate on thick countertops, it is customary to use more subtle mounting plates made of durable materials (steel, duralumin, polycarbonate, getyinaks or glassstolite). The plate is manufactured as follows.

Improvement of the stop
Parallel stop can be finalized that the setting of the milling table occurred more conveniently and quickly: for this you need to embed with C-shaped guides in the worktop. The profile can be made of aluminum. For the insert, a direct groove milling mill is used. The profile is stacked in the prepared groove and fastened with screws.
Next, you should choose a bolt with a hex hats of this size so that it can be included in the C-shaped profile and not turn it into it. Drill 2 holes at the base of the parallel stop corresponding to the diameter of the bolt.
It should also be embedded with a C-shaped profile and to the front strip of the stop for fixing various clamps and protective housings on it.
The stop is screwed to the tabletop with the help of nut-bars.
On the back of the stop can be made camera for connecting a vacuum cleaner. To do this, it is enough to cut the square from plywood, drill a hole in it under the nozzle of the vacuum cleaner and fasten the resulting lid to the skins.
Also, you can add safety flap, Made of MDF or LDSP and a small rectangle of plexiglas. For sampling, the grooves can be used a jigs or a milling mill with a mold installed.
To have the ability to handle small parts, it is necessary to make clamps and fitness from plywood or MDF.
It is manufactured on a circular with a pitch between the cuts of 2 mm.
If desired, you can make milling table with tool boxes.
Making table base
If it is required from a manual milling mill to make a stationary machine, then without the manufacture of a solid base can not do. Below is a cutting card with details deposited on it that will be required to assemble the base of the table. The dimensions of the parts will need to be corrected if the sheet material is different than the thickness.
All desktop parts for manual milling are collected using confirmates. For the convenience of moving the table to his bottom, you can attach rollers. If you expand this table slightly and attach a disk hand saw in his free part, it will turn out universal table for milling and circular.
In order for the machine to occupy less space, it can be made on the principle of table books with countertops descending from both sides.
Homemade Milling Devices
For expansion functionality This unit is on sale there are enough expensive devices. But the owners of the milling products in order to save funds are trying to produce various adolescents with their own hands that work is not worse than factory.
A simple clipped for a milling mill is made of two pieces of plywood and pairs of furniture telescopic guides. The milling mill is installed on a platform having a hole for the tool. The playground is attached to the workbench at an angle (for more convenient positioning of the equipment in height), as shown in the photo below.
So, the nipseral device is manufactured in the following order.
- Cut from plywood 2 platforms of the same sizes. The size of the adaptation can be any.
- Place the two telescopic guides parallel to each other and screw them along the edges of the first site and screw them with screws.
- For more accurate positioning of the guides, you can fasten the two equal to the length of the plank between them.
- It is necessary to put forward the retaliatory planks and put the second area in the second place with the first. Parameters on the second platform of the point through the bar, then spend the line through them.
- Remove the response planks from the guides by clicking on the plastic "mustache" located on their reverse side.
- Put the checkpoint on the platform to the site so that the line passes through the center of the holes for fasteners, and screw them with screws.
- Gently align 2 guides and push them (you must hear click). If you insert the part with a breakdown, you will break the telescopes, and balls will be hurt.
- Between the vertical focus with the aggregate and the mobile table must be to withstand a certain distance.This is done in order for when lowering the cutter, it does not hurt the table. Since in this case the maximum cutter departure will be about 25 mm, then you can temporarily lay between the table and the stubborn bar of the same width, that is, 25 mm. Planck allows you to place the design parallel to the vertical
.
- At the next stage, holding the device, drill 2 holes for the seasons. They will allow you to quickly position the clicks on the workbench. When the holes are ready, insert a couple of shots in them. Now you can remove the bar, laid between the focus and the device.
- Now that the mobile table is fixed, on the upper platform it is necessary to install the vertical stop, as shown in the following figure. For stiffness, the focus is maintained by two jams.
- When all elements of the clicks are fixed, you can proceed to tests. Put the workpiece on the table of the device and press it to the slope. Install the required height of the cutter, turn on the unit and promoter the workpiece.
- After the first pass, turn over the workpiece 180 degrees and repeat the processing.
- Turn the blank by 90 degrees, putting it on the edge, and again repeat the operation.
- Rotate the part 180 degrees and make the final treatment of spike.
As a result, you will get smooth and high-quality spike.
By changing the height of the cutter relative to the site of the adhesive, you can get the spikes of different thickness.
Copy sleeve
If in the configuration to your mill, there was no copying sleeve, then it can be made literally in 30 minutes from the remedies. For the homemade, you will need a metal or duralumin puck, which can be made of sheet metal, and a plumbing threaded extension.
The copier bushing is manufactured in the following way.
- Pick up the nuts suitable for the threader and cut it with a grinder so that it turns out a thin ring. After that, align it on the grinding machine.
- It is necessary to make a round pad for a shell of sheet metal or aluminum 2 mm thick. Depending on the model of the unit, the hole in its sole may have various shapes. In this case, the site should have sections on the sides that are rated on a sharpening machine.
- Streeting the washer on both sides, place it on the sole of the unit.
- Put the unit without removing the washer, vertically and make a pencil space for fasteners through the holes in the apparatus sole.
- Places marked with a pencil must be laid for accurate positioning of the drill.
- First, drill holes with a thin drill, and then the drill corresponding to the diameter of the fastening bolt.
- Dress the puck on the threaded extension and tighten the wrench. Help the part in the vice and cut the extra thread in a nut with a nut with a grinder.
- Helm the item in the vice with the other side and a little shorten it.
- Align the item on the grinding circle, insert into the sole of the device and secure it with screws. The nut-ring should be slightly lower than the sole of the unit.
Milling guides
If you want to choose a very long groove in the workpiece, then you will need a device for a milling driver called a bus. Ready metal tires can be bought in specialized stores. But they are also easy to make with their own hands from plastic, plywood or MDF.
The thickness of the material should be about 10 mm so that the parts can be pulled by screws.
The guide for the aggregate is done very simply.
- Cut on the circular three stripes. One wide, order of 200 mm, and 2 narrow - 140 and 40 mm each.
- Also make a small bar from the same material, about 300 mm long and 20 mm width.
- Put on a wide band the part 140 mm wide, align it along the edge and twist both parts with screws.
- Put on top of a wide band, opposite the screw part, a narrow strip of a width of 40 mm. For accurate positioning, run between the upper parts of the bar width of 20 mm and screw the narrow strip with screws to the bottom part. Thus, it turns out a long tire with a groove of 20 mm wide.
- Take the bar width of 20 mm and screw it to the sole of the machine, as shown in the next photo. For sampling, the groove is selected straight or Figured Line Cutter and fixes in the Cangga of the device.
When all fixtures are prepared, follow these steps. Put the workpiece on the workshop that needs to be processed along the entire length, position the bus on it, securing the clamps. Insert the bar attached to the sole of the mill in the groove of the guide. Run the unit and promoter the workpiece along the entire length.
If you want to choose a deep groove, then the processing occurs in several goals so that the equipment is immersed in the workpiece gradually.
All photos from the article
If you like working with wood or prefer everything repair work Do independently, then you will not hinder the appropriate equipment. For example, you can assemble the lathe, milling, a nipseral machine on a tree with your own hands.
Initially, this task may seem complex. However, reading this article, you change your mind. Especially since the price of the unit will be at times less industrial analogues.
Assembling turning fixture
The assembly method will be like this:
- The basis of the aggregate will be a 3-phase electric motor. Therefore, it should be a three-phase power, otherwise the house will constantly beat the automatic fuse.
- The frequency of rotation engine is no more than 1500 / min.
Note! Different types The drives are connected differently: "Triangle" or "Star". Development difficulty - right choice condenser. Its capacitance must correspond to the engine power.
- Put on the windshield motor shaft for bulk parts and removable analog - for small. Second side of the node lock the corner. There are special peaks on the tables, the blanks are planted with a hammer.
- Next, the workpiece is centered and secure counterclaims. Homemade Tree Machine ready.
In the manufacture of furniture and joinery, parts are most often fastened with each other "on the thorn". There are several types of thickening connections: "Swallow tail", box, round and oval, which allow you to fix parts under the necessary angle or lengthen them. The spike is a rather complicated element, for the manufacture of which a special type of equipment has been developed.
Types of nipsens
The most common in the production of nipseral machines for frame, door and window structures. Equipment can be single or double-sided, passing or refundable. The working bodies perform cutters (vertical or horizontal), saws. The device mills the spikes and recesses for them (eyelet) in elements of wooden structures.
Spikes "Swallow Tail" and the boxes direct are performed on special types Machines created for large enterprises. Such types of fixtures are very reliable and provide long-term operation of products.
Round and oval shape spikes are created on CNC devices operating automatically. CNC machines can perform work in any planes.
- maximum diameter of the processed part;
- the greatest spike width;
- the greatest spike disk;
- type of spike;
- spindle twisting speed;
- engine power;
- dimensions and weight.
The main requirement for a nipsene machine is a high accuracy of operations. Otherwise, the details will not match each other and the connection will not work.
Other areas of use:
- processing of calibrated shields, chipboard;
- overtaking the perimeter of door canvases, window frames;
- fireboard processing;
- production of parquet.
Wood Splicing Machines
This is a special category of epipherase equipment, which is used in production for the splicing of blanks in length. The machine cuts in the ends of the spikes of the seamless shape, processes glue and sends into the press. Wood splicing lines work in automatic mode.
Principle of operation
types of cell type
The billet enters the working surface and is cut into size, after which the eyeles and spikes are formed. The bed is a littered rigid design with clamping devices. It is equipped with a column with working heads that can be put on a test board, saws or cutters.
So that in the process of processing the workpiece does not break through, the automatic device puts the glue layer. Thus, the appearance of chips is preventing. In addition, there may be a mechanism for hollowing the ends of the parts on the nipsens machines.
In the serial production of furniture, an epipherase machine on a CNC tree is used, creating any types of thickening connections. They are easy to configure, do not require long-term training personnel. There are milling machines with a nipseral carriage, comfortable for small-scale production.
Features of operation
- On large production conveyors, this type of equipment is attached to the ceiling. Additionally, the machines are completed with clamping devices, sharing with cutting saws are taken. The part is fed to the ending saws and the processing of a pair of milling calipers ends.
- The feed rate of the billet is regulated by the variator, smoothly.
- For satisfactory processing, the spindle should rotate at a speed of about 7000 revolutions per minute.
- There are several types of equipment, various directions of the guide: by 2; 2.5 and 3 meters.
- The design allows the use of several different tools for wood processing.
- The machine can additionally be equipped with a clamping pneumatic mechanism and a working surface extension.
The video demonstrates the operation of the nipped machine with manual settings:
Review and comparison of models
Characteristics and models of nipseral machines on wood
The nipseral machine is a kind of woodworking machines that are used for the manufacture of faces and spikes in the manufacture of wooden structures. Elements can be processed as for a compound at an angle, while the frame and the box grooves and for the splicing are manufactured, and the grooves of the type "swallow tail" or figured are manufactured.
ShipiPray Tree Machine
Such a machine is usually equipped with a special automated feed mechanism that provides processing into several technological "passes" without the participation of the operator, and the automatic tool change device.
The nipionic wood machine is used both in small workshops and in large mass production. They are indispensable at enterprises involved in woodworking, house-building, as well as the production and repair of furniture.
1 types of epipsene machines
The mechanisms for filing a blank with variable speed allow the use of tools of a small diameter to achieve high accuracy. The use of a replaceable tool is capable ensure the implementation of several dozen operations, Giving the maximum flexibility to all processing settings.
Processes can be managed by a personal computer with memory, diagnostics and a graphical user interface.
Applied nipseral machines are divided into two main types:
Machines of one-way type for one cycle are made of spikes on one side of the workpiece. These machines work according to the positional principle: the workpiece is fixed on the desktop, which makes reciprocating movements relative to the tools (milling cutter and saw) installed on the spindle.
One-sided nipped wood machine
Double-sided type machines make spikes immediately on both billets. They work according to the positional and passing principle, that is, the optipal of the end parts is performed when the workpiece is moved relative to the tool, and the cutting of spikes and the faces is performed using a movable milling unit with a fixed billet.
to the menu
1.1 Characteristics of nipseral machines
The main parameters of the machines are described by their technological capabilities:
- maximum Ship length;
- minimum thicker thicker;
- maximum depth of the eye;
- width of the face;
- permissible size of the workpiece.
In addition, the machines are characterized by the number of spindles, saw diameter, cutter sizes, the feed rate and engine power.
2 Famous manufacturers and popular models
Various models may also differ in additional features, such as:
- software management, including with a computer;
- the presence of an automatic tool change;
- the design of the mechanism of the billet.
2.1 Makita Corporation, Japan
Japanese company "Makita9Raquo; offers a machine with software control "Makita9RAQUO; 5500 S, equipped with two engines for the drive of two pairs of longitudinal and transverse saws. Its parameters provide the required cleanliness of the cutting and the speed of performance.
Makita Raysumovoy Machine
The greatest cutting depth for one pass is 90 mm, with a large depth of spikes (up to 240 mm with width and height of 130 mm) can be simply achieved over several passes.
The machine can work with billets of unlimited length, for which an auxiliary unit is used with adjustable geometric parameters. The machine itself is very compact and easy: the dimensions in the horizontal projection are 560 × 620 mm at a height of 810, the weight does not exceed 68 kg.
2.2 SCM GROUP, Italy
Under the brand belonging to the brand "Celaschi9raquo; Today there is a bilateral machine "Progress9RAQUO;, suitable not only for treating materials from wood and its derivatives, such as chipboard, but also gypsum plates, plastic materials and fiberglass.
In addition to the main operation - the manufacture of spikes using cutters - it can perform cut, profiling and other operations.
Separase Machine Orient
"Progress9Raquo; It can work with the details of over 6 meters long and thickness up to 20 centimeters with the feed rate of up to 1 meter per second. It also has an automatic tool change device and a CNC system, can be easily integrated with other SCM GROUP equipment.
to the menu
2.3 Group of Companies "Magr", Ukraine
The product nomenclature includes modern specialized milling Machine Models "SS-200-160P9RAQUO;, which is designed to perform a transverse spike cutting operation. It can be used in conjunction with ending machines and presss for the splicing of the PSD.
It makes batch processing of parts, which eliminates chips during cutting. Package fixation is performed using a pneumatic device, Shipping step offset by changing the height of the desktop.
to the menu
2.4 Savelovsky "Szdo", Russia
JSC "SDO9RAQUO; It offers high quality equipment made in conjunction with leading world companies producing wood processing equipment. The nipseral machine "SC9RAQUO; -3 is designed for cutting special wedge spikes on the ends of a wooden bar.
Separase furnace Festo.
The machine ensures the execution of a cycle of operations with a displacement of the cutter to one second part of the step, for which a specialized pneumatic system is applied from the Italian company "Camozzi".
SC-3 allows you to process parts with dimensions of 20 x 20 centimeters with thickness to 12 centimeters, full cycle Sliced \u200b\u200bspikes on both sides takes no more than 30 seconds.
to the menu
2.5 How to cut spikes with your own hands without applying the machine?
In this case, you will need a nipseral device. Often, carpenter make homemade nicknames, but today it is possible to purchase an industrial model, for example, "CMT9RAQUO; - 300. With it (if there is an electrical milling mill), you can, applying various templates, get the package you need.
Manual milling devices
To do this, you will also need the required cutter size, More precisely, the range of cutters, from the same manufacturer. Brand "CMT9RAQUO; Belongs to the Italian CMT Utensili SPA Corporation.
Often together with nipsens, the groove machines are used, for example - "BALESTRINI9RAQUO; 2 Cap.
When working with nipsens, it is necessary to use fences that exclude the ingress of parts of the body and clothing into moving parts, and comply with the established safety rules when using electrical installations.
2.6 How does the homemade nipseral machine work? (video)
Jet Tree Machines: Characteristics and Model Selection
Currently, the market shows a fairly wide range of Jet woodworking machines. Such equipment is in most cases.
Models and characteristics of outcrop
The assignment of lengthy machines is the exact processing of the inner (external) surface surface according to a given configuration. The contours received after.
Models and parameters of circular sawing machines from Harvey
Circular saw - an indispensable device on any woodworking enterprise. Now simple "circular" was improved, turning into.
Features of the device and the characteristics of the STD 120m Turning
Woodworking machine STD 120 m is present in many carpentry workshops of schools and vocational schools. It is used to teach children.
Sickness do it yourself
Continuing experiments with my milling ENCOR 850, made a nipseral device - a carriage on the guides for my drilling additive device. The additive himself - https://www.youtube.com/watch?v\u003dge3tz7taqvi in \u200b\u200bgeneral, furniture guides are a wonderful thing: at the expense of the ball (bearing) design, they provide a clear and smooth movement. And if there is no possibility to make a groove in the tabletop, you can always make a slip carriage. Yes, you lose in height (no longer zero clearance), but the slip is maximizes. In this case, the height did not play the role for me, because the rise of the cutter has a non-small range. As a result, I want to say that such a way to cut spikes (for me) the most fast and clean. My site is http://maximkozlov.ru LIVE-channel - http://www.youtube.com/maxrecordslive Group VK - https://vk.com/maxwoodworker Wood winning with Jet 10-20 Plus. Homemade Tree Milling Machine Part 2 HomeMade Milling Machine For Wood. Yuri Chalov | I am visiting # 1. Joinery for circular machine with your own hands for the garage workshop. Device for the millingrer. Drainage. Window clicks. Cable spikes and milling fiolent. Grooves on the circular. Simple adaptation for circular. Spinable whole oak plate | Tokard. Segmenting: Vase from beech and ash | Tokard. Cyclone for vacuum cleaners with your own hands | Cyclone Workshop. HomeMade Router Base (Part 2) is a homemade milling base (part 2). Spined plate of solid ash | Tokard. Insert spikes without Domino. Universal conductor. Separase device. First sample.
YouTube Copyright Policies Restrict This Video From Being Played At this Website.
[F] Share This Video On Facebook
Funnycat.tv © | 2014-2017
Best Funny Cats Videos.
Powered by.
public API "S
Therefore, I decided to assemble a conductor for the manufacture of thorns with a manual milling.
The idea was to make a device for quick and convenient cutting of the grooves for plug-in Domino spikes, because Ready solutions are too expensive.
It all started with the search for a suitable idea on the Internet. Next adaptation of the idea to your needs and, finally, the performance of the drawings.
The principle of operation is simple (see the following photo).
The position of the groove relative to the edge of the workpiece is regulated by blue focus. As it will be a special cabinet.
The width of the groove is determined by the width of the cutter, the length of the groove is the position of the brown tongue valve.
The black item is a copy bush with a width of 40 mm, which goes into the resulting groove.
Next Search for material. It seemed to me a good idea to make a conductor from a sheet of durally 6 mm. Although, probably, you can do from any sheet material - plywood, plexiglas, textolite. The search for a suitable sheet of durally on the local bird market and did not give the result in local metal products: "Suitable pieces are sometimes slipped, but now there is no and when it is not known. Please, call later". On metal bias managed to find the desired material. He was even offered to cut into size, but the problem is that the whole sheet will have to take. And this is first expensive, secondly, where I have been given to the remaining 70% of the sheet.
As a result, I found an IP, which trades on the Internet by leaf duralumin D16T retail. http://dural16.ru/. Maybe who will come in handy.
They can order a piece of the sheet of the desired size and the necessary thickness. But here is not everything smoothly. If you take not the whole sheet, and part, then there is a serious markup.
I bought a suitable leaf of 800 × 500 5 mm thick for 4130 rubles, i.e. 614.58 rubles per kilogram. Yes, not enough.
In parallel with the search for the material, the search for Tokar-milling worker began to search. Seasted on a pair of all-Russian thematic forums in search of countrymen. As a result, I found a couple of dozen accounts, which sent personal messages. Of these, eight people responded, who later sent the drawings with the question of the cost of work. Larction of prices for working with my material turned out to be significant - from two to eight thousand rubles.
As mentioned above, such an adhesive can be made from any sheet material. For example, from plexiglas, textolite or plywood. At the same time you can do the simple manual milling. I decided to make my nickname from Durally, so I had to contact the specialists. It was for them that accurate drawings with the dimensions that someone could seem excessive and complex (although at closer examination it becomes clear that it is not so). These sizes are selected in accordance with the sizes of the freesomerer and under a specific copying sleeve.
Done from Durally - not the cheapest solution both at the cost of the material and the cost of work, but it suits me. It is interesting to observe as a fiction-made product and drawn in 3D materializes and becomes a real product.
As you can see in the following photo, the finished product is very simple. When it is assembled with unexpected complexity. The fact is that in the initial project plate are connected by aluminum rivets with a secret head.
It turned out that finding such rivets on sale - the task is nontrivial. They are not only in ordinary shopping stores, but even in highly specialized stores with fasteners. I had to connect the plates with conventional stretching rivets.
The most cunning design element is the retractable tongue, which is adjusted for the stamp groove length. All the cunning lies only in the need for fitting swallow tail. Otherwise no difficulties in its manufacture. To make it shorter in the main plate made not one, but two holes in which the locking bolt is inserted depending on the required groove value.
At the same time, the position of the groove in the language itself is chosen in such a way that, with any position, the tongue of the outcoss the milling is not rested in the fixing nut-lamb.
For the attachment of the adhesive, collected from 21 mm plywood Tumba presented in the next photo. In the upper part of the couch, two parallel grooves are made for mounting the plate bolts M10, in the passage of the part - the hole for fixing the blanks on the clicks with clamps.
To give the end of the desired stiffness, made an additional crossbar.
After assembly, we get such a device. Before installing, the metal surfaces in contact with the soles and the billets are pre-matured before installation.
Under the plate attached a lane from Durally to the end. This strip expands the possibilities for fastening the blanks to the clicks with clamps.
So far I have no opportunity to arrange a real check, but I think it will cope with my task. Plumbing spikes, despite the fact that they can be purchased ready (http://www.kalpa-vriksa.ru/catalog/vst avnye_shipy_domino_dlya_festool_df500 /) I will do myself. Nevertheless, the cost of one spike is almost 10 rubles - expensive.
Characteristics:
Dimensions - 250x440x112 mm
Weight - about 5 kilograms
Max. Diameter cutters - 37 mm
Max. PAZ Length - 154 mm
The thickness of the base under the mill - 12 mm
Using the nickname, you can make grooves for plug-in spikes in the right place of workpiece
If it is not possible to fix the blank on the nickname, then the movable part of the adhesive is removed and attached to the workpiece.
If there is a need to handle the ends of long blanks, then the adhesive can be put on the side.
Use the nickname is quite convenient and the result is quite high-quality.
P.S. In the comments, I wrote about another nickname made on these drawings. The original message can be found below. I will give only squeezing:
. No need to contact different masters. I made a nickname on your drawings in one day from an aluminum sheet with a thickness of 4 mm. 4 mm The most optimal option for making yourself. Used manual milling, circular saw, file, and email. Only to the plywood bed at the bottom of another aluminum plate fastened. So it is better to mount the milling part, pressing to the upper and lower plate. Aluminum is well cut circular saw and manual milling on small revolutions. Milling with a mill of 8 mm for metal.
From myself I will add that this is an excellent experience of self-making nickname, thanks for your experience.
Dominoes size choose depending on the available cutters. More precisely, two cutters are needed - straight to make a groove, and the steam-corresponding to it to round the edge spikes.
The size of the billets (height and width) caught up with the number of grooves made. Next, twilight the edges and cutting the workpiece into individual dominoes in length depending on the depth of the grooves made minus three millimeters.
It looks like this:
EDITED AT 2015-10-28 06:18 (UTC)
There are no price for your nickname. And there is no need to turn to different masters. I made a nickname according to your drawings in one day from an aluminum sheet with a thickness of 3 mm. Used manual milling, circular saw, file, and email. Only to the plywood bed at the bottom of another aluminum plate fastened. So it is better to mount the milling part, pressing to the upper and lower plate. And with a copying sleeve of 19 mm, it will not be convenient to work, it is not seen that the freserving. 36-40 mm is the thing that needs. Thank you very much for the idea and drawings. There is no better on the Internet.
I apologize for the fact that I have not introduced and I turned out anonymous. My name is Constantine, I am 73 years old. Look at the junction made by your drawings in one day. Here is a link to my photos in classmates. https://ok.ru/profile/355387415108/album/8 15584508996 Aluminum is well cut in a circular saw and a manual milling on small revolutions. Milling with a mill of 8 mm for metal.
Separase adaptation to the milling hand
Many woodworkers dream of buying perfect nipseral adaptation to the mill to do quickly and accurately spike straight shapes or shapes swallow tail. Such factory devices can do a lot more than simple box spikes. One example is semi-blind spikes (on the photo on the right below). Such a device will perform any semi-blind connection of the swallow tail. So if
You are familiar with how the conductor works, then you are on the way to mastering this technique. With the help of the proposed templates in the set, you can make any half-blade connection and it works in about the same way as in a typical box - only has small differences. But today, let's look at how to make a device, which will help to make simple box spikes.
Separase adaptation to the milling mill with constant size.
In each carpentry workshop, it is simply necessary to have a nipseral adaptation to the mill for the manufacture of spikes. different sizes. In the manufacture of such a device, it is necessary to understand that it, in order, is manufactured under one specific size of the spikes. It is not difficult to do and it will work like a clock. Required parts - guides for the manufacture of spikes, they are installed on the opposite sides of the body of the device in a checker order and at the same distance from each other. In the manual milling mill inserted a mill with a thrust bearing, which repeats the form of the guides. If the guides are cut out of one size and uniformly mounted into the body of the device, the spikes will be perfectly approaching each other. These spikes have in width size 7/8 ", the spike height is 3/4". Before the start of the manufacture of spikes, install the milling mill in the milling table. Note: A situation may occur when cutters with a thrust bearing will not be available, then the situation will fix the situation for the milling sleeper. The adaptation itself securely secure the clamps on the $ 15 board.
Configured nipples for a milling machine.
How to make grooves in the body of the device for a manual milling chaser at an ideal equal distance from each other and one size? It can be said that this is the usual woodworking operation and the milling machine is the perfect tool for work. The grooves can be located widely, as in the example in the photo, can be located very closely as drawer spikes. It doesn't matter why the grooves are located, the main thing is that the grooves are uniformly - parallel between themselves, in one distance and with the same width. To do this, you need to make a simple device consisting of a piece of MDF on which the milling mill is attached. Such a conductor can be made under one size or with the possibility of adjusting the distance between the grooves, as shown in the photo below.
Knowing how to make a spike groove with a hand mill, you can even produce not only beautiful, but also reliable furniture, but also various wood structures characterized by excellent carrier ability. According to the Schip-PAZ system, not only elements of various furniture (tables, chairs and shelves) are connected, but also the framework of low-rise buildings experiencing significant loads during operation.
In order to manually make a spike on wooden barIt is necessary to provide several conditions:
- reliably fix the workpiece and correctly orient it in relation to the fuser guide sole;
- stop the height of the working part of the cutter in such a way that the tool removes the material of the material of the required thickness from the surface of the processed billet.
Even using this processing, the simplest nipseral device for the milling ager can not only increase its performance and quality results, but also technological process more secure. Especially relevant to the use of such a device, which can be made and with your own hands, in cases where the furniture is made not in single instances, but by series (with the master you have to perform a large number of similar operations with both the same type and with having various shapes and sizes details).
Used tools
Creating spikes and grooves, with which the connection of two wooden blanks will be ensured, it assumes that the sample of material is made on the side surface of the timber or board, the material is made. In this case, all geometric parameters of the elements of the future connection should be strictly constructed.
To perform this operation, a manual milling can use tools with shanks with diameter of both 8 and 12 mm. The most universal in this case is a gauge mill, the cutting part of which works as follows:
- the side surface forms the walls of the groove and side sides of the spike;
- the end side processes the bottom of the groove and removes the material layer of the required thickness from the base of the spike.
Thus, using a tool of this type, you can form on the side surface of the timber or boards as spike and grooves. In this case, their dimensions can be adjusted at a fairly wide range.
In cases where higher demands, grooves and spikes are made to the reliability of wooden parts, and the shapes are made, and the forms called "Lastochka Tail". The grooves and spikes of such a configuration are created using a mob of "Lastochka Tail". Perform the procedure for the formation of grooves and spikes of such a shape with a manual milling agener is also possible, but for these purposes, the devices should be used.
Sampling "Swallow Tail" using a template
To make the question of how to make a groove in a board and a bar or spike on their side surface, did not cause special difficulties, it is better to use a power tool equipped with comfortable side handles, a wide guide sole and the spindle protection option from turning during the replacement process. In addition, it is desirable that the side stopper attended such equipment, due to which the departure of the cutters used with it will always remain constant.
How to make a spike sampling device
When forming spikes on wooden blanks with a manual mill, it is not fixed in space and is summarized to the workpiece manually. That is why it is very important that when using power tools, the processed item was in a device that can ensure not only its reliable fixation, but also the accuracy of spikes formable on its surface.
The design of the simplest device, which is able to cope with such tasks, is:
- several fixed guides (lower, upper, side);
- movable plank, at the expense of which you can adjust the length of the sample.
This device is manufactured, the dimensions of the components of which are selected individually, in the following sequence:
- At the edges of the plywood sheet, the same side vertical elements are fixed, in the central part of which cuts are made.
- On the side elements, the guides are installed on which the sole of the manual milling is installed.
- To limit the handle of the hand mill in the upper guides, the side strips should be fixed.
- On a sheet of plywood playing the role of the device's base, you need to install a movable element, with which the edge of the edge of the processed workpiece will be adjusted. For fixing, you can use a regular screw with a lamb or any other suitable fastener.
In the manufacture of the adaptation of the proposed design, the following points must be taken into account:
- The height of the upper guides should correspond to the amount of thickness of the processed part and the magnitude of a small gap, which is necessary for the installation of the fixing wedge.
- Cutouts in the side vertical elements are performed so width so that it takes into account the length of the thorns formable.
It is possible to work using the adaptation of the proposed design by a manual milling mill of almost any modern model, in the options of which it is possible to adjust the cutting speed, the values \u200b\u200bof the supply and departure of the working part of the tool used.
To create a sidewall tail on the side surface of a bar or board, a device manufactured as follows is used.
- A hole is performed on a sheet of multilayer plywood, from which the cutting part of the cutter "Lastochka Tail" will perform.
- From the bottom of the prepared plywood sheet, a manual milling mill is fixed. To do this, you can use clamps, screws or any other fasteners.
- On the surface of the plywood sheet, according to which the processed workpiece will move, the board is fixed with a thickness of 2.5 cm. It will execute the role of the guide element. This board is a consumable material and is used once with a cut diameter cutter.
Such a device can be installed between two chairs or use to be placed a more convenient and reliable design.
Creating spikes on bars and boards
Applying wood cutters for manual milling and the above-described device, processing is performed in the following sequence.
- The item to be treated is placed on the lower support plane.
- The edge of the details on which the spike will be formed is placed in the cutout of the upper guides and moves to it until it stops into the movable element of the device.
- The movable element is fixed in the desired position.
- Using a wedge element, the top plane of the part is pressed to the upper guides.
- Hand mills are placed on the upper guides.
- The tree with the help of the tool installed on the milling mill is first removed from one side of the spike formable.
- After processing one side, the workpiece is turned over and the formation of the second side of the spike is performed.
Even such an easy-to-design device allows you to process with a hand milling compound "Schip-groove" with high accuracy and performance.
Before starting work, such a device must be configured. This can be done according to the following algorithm.
- The tool installed in the manual milling is lowered to its contact with the surface of plywood bases.
- The thickness of the part is measured.
- The thickness of the workpiece is divided by 4. The result and will be the distance to which the mill must be lifted above the base surface.
Using the Lastochny Tail, the grooves and spikes create half of their thickness, which is explained by the features of this type of connection. To make a groove in a bar and a blackboard, as well as form a spike type "swallow tail", the device also needs to be configured and fix it in the desired position.
Ship connections are one of the most durable (http://www.woodmastermagazine.ru/assets/files/pdf/2008-3/44_51.pdf).
Therefore, I decided to assemble a conductor for the manufacture of thorns with a manual milling.
The idea was to make a device for quick and convenient cutting of the grooves for plug-in Domino spikes, because Ready solutions are too expensive.
It all started with the search for a suitable idea on the Internet. Next adaptation of the idea to your needs and, finally, the performance of the drawings.
The principle of operation is simple (see the following photo).
The position of the groove relative to the edge of the workpiece is regulated by blue focus. As it will be a special cabinet.
The width of the groove is determined by the width of the cutter, the length of the groove is the position of the brown tongue valve.
The black item is a copy bush with a width of 40 mm, which goes into the resulting groove.
Next Search for material. It seemed to me a good idea to make a conductor from a sheet of durally 6 mm. Although, probably, you can do from any sheet material - plywood, plexiglas, textolite. The search for a suitable sheet of durally in the local bird market and did not give the result in local metal products: "Suitable pieces are sometimes slipped, but now there is no and when they will not know. Call back later." On metal bias managed to find the desired material. He was even offered to cut into size, but the problem is that the whole sheet will have to take. And this is first expensive, secondly, where I have been given to the remaining 70% of the sheet.
As a result, I found an IP, which trades on the Internet by leaf duralumin D16T retail. http://dural16.ru/. Maybe who will come in handy.
They can order a piece of the sheet of the desired size and the necessary thickness. But here is not everything smoothly. If you take not the whole sheet, and part, then there is a serious markup.
I bought a suitable leaf of 800 × 500 5 mm thick for 4130 rubles, i.e. 614.58 rubles per kilogram. Yes, not enough.
In parallel with the search for the material, the search for Tokar-milling worker began to search. Seasted on a pair of all-Russian thematic forums in search of countrymen. As a result, I found a couple of dozen accounts, which sent personal messages. Of these, eight people responded, who later sent the drawings with the question of the cost of work. Larction of prices for working with my material turned out to be significant - from two to eight thousand rubles.
As mentioned above, such an adhesive can be made from any sheet material. For example, from plexiglas, textolite or plywood. In this case, you can do with a simple manual milling. I decided to make my nickname from Durally, so I had to contact the specialists. It was for them that accurate drawings with the dimensions that someone could seem excessive and complex (although at closer examination it becomes clear that it is not so). These sizes are selected in accordance with the sizes of the freesomerer and under a specific copying sleeve.
Done from Durally - not the cheapest solution both at the cost of the material and the cost of work, but it suits me. It is interesting to observe as a fiction-made product and drawn in 3D materializes and becomes a real product.
As you can see in the following photo, the finished product is very simple. When it is assembled with unexpected complexity. The fact is that in the initial project plate are connected by aluminum rivets with a secret head.
It turned out that finding such rivets on sale - the task is nontrivial. They are not only in ordinary shopping stores, but even in highly specialized stores with fasteners. I had to connect the plates with conventional stretching rivets.
The most cunning design element is the retractable tongue, which is adjusted for the stamp groove length. All cunning lies only in the need to fit the swallow tail. Otherwise no difficulties in its manufacture. To make it shorter in the main plate made not one, but two holes in which the locking bolt is inserted depending on the required groove value.
At the same time, the position of the groove in the language itself is chosen in such a way that, with any position, the tongue of the outcoss the milling is not rested in the fixing nut-lamb.
For the attachment of the adhesive, collected from 21 mm plywood Tumba presented in the next photo. In the upper part of the couch, two parallel grooves are made for mounting the plate bolts M10, in the passage of the part - the hole for fixing the blanks on the clicks with clamps.
To give the end of the desired stiffness, made an additional crossbar.
After assembly, we get such a device. Before installing, the metal surfaces in contact with the soles and the billets are pre-matured before installation.
Under the plate attached a lane from Durally to the end. This strip expands the possibilities for fastening the blanks to the clicks with clamps.
So far I have no opportunity to arrange a real check, but I think it will cope with my task. Plumbing spikes, despite the fact that they can be purchased ready (http://www.kalpa-vriksa.ru/catalog/vstavnye_shipy_domino_dlya_festool_df500/) I will do myself. Nevertheless, the cost of one spike is almost 10 rubles - expensive.
Characteristics:
Dimensions - 250x440x112 mm
Weight - about 5 kilograms
Max. Diameter cutters - 37 mm
Max. PAZ Length - 154 mm
The thickness of the base under the mill - 12 mm
Using this nickname made
Using the nickname, you can make grooves for plug-in spikes in the right place of workpiece
If it is not possible to fix the blank on the nickname, then the movable part of the adhesive is removed and attached to the workpiece.
If there is a need to handle the ends of long blanks, then the adhesive can be put on the side.
Use the nickname is quite convenient and the result is quite high-quality.
P.S. In the comments, I wrote about another nickname made on these drawings. The original message can be found below. I will give only squeezing:
... There is no need to turn to different masters. I made a nickname on your drawings in one day from an aluminum sheet with a thickness of 4 mm. 4 mm The most optimal option for making yourself. Used manual milling, circular saw, file, and email. Only to the plywood bed at the bottom of another aluminum plate fastened. So it is better to mount the milling part, pressing to the upper and lower plate ... Aluminum is well cut by a circular saw and a manual milling roller. Milling 8 mm mill for metal ...
From myself I will add that this is an excellent experience of self-making nickname, thanks for your experience.