Definition of composites. Classification. Composition and properties of plastics. Liquid extrusion porosimetry
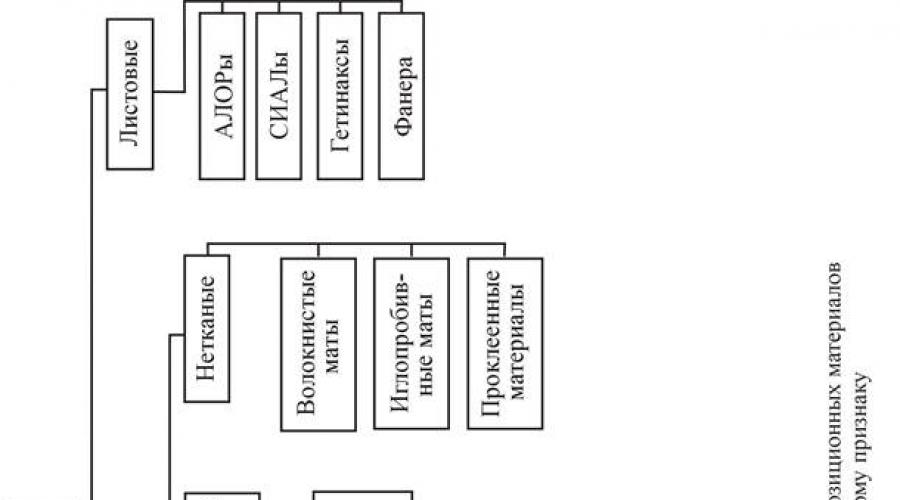
Read also
TO Category:
Industrial materials
Industrial material classification
Classification refers to the distribution of materials, products, properties or phenomena into separate groups, subgroups, classes, subclasses, types, subspecies, types and other categories. The division of materials into these categories is carried out according to their common characteristics. The signs of the classification of materials can be: origin, properties, shape, size, color, method of production, purpose, etc.
For industrial materials, the most common characteristics should be considered the origin, method of production and purpose.
So, dividing materials into separate groups, subgroups, they come to separate types and objects. Knowing the general features of a particular group of materials, one can easily characterize the individual items included in this group.
The classification must comply with the following conditions: a) it must be scientifically substantiated and have practical significance; b) the division of materials into categories should be made only according to one common feature for them; c) should cover the entire range of items; d) the relationship between the individual categories of the classification must be maintained; e) the number of features in each classification category must be consistent with the digital coding capabilities adopted for the national classification of industrial and agricultural products.
Classification is essential. It is necessary primarily to study the properties and other features of materials and products in circulation, to develop general and specific requirements for them, taking into account their purpose, for scientifically grounded drawing up of plans for the production of materials, taking into account the need for them, to study demand and drafting industry applications, to streamline accounting and reporting, etc.
The classification acquires special significance when modern electronic computers are used in the national economy, when coding industrial and agricultural products, etc. The correct classification of materials according to their intended purpose makes it easy to determine the possibility of replacing one material with another.
There are the following types of classification: national, sectoral and educational.
The nationwide classification is used to classify industrial and agricultural products into classes, subclasses, groups, subgroups, types, etc. for coding. The code is a system of symbols for materials using numbers, letters and in combination with each other. This is widely used in the All-Union Classifier of Products (OKP), according to which all products are divided into 98 classes. So, for example, class 22 - polymers, class 39 - tools, class 56 - products of the furniture industry, etc.
The sectoral classification is used for the products of certain industries and has a narrow departmental significance.
The educational classification pursues the goal of gradually studying individual sections of the course "Industrial materials" to obtain general information about the variety of their properties, the nature of processing, purpose and nomenclature.
The nomenclature is a list of materials, products, spare parts for them and their varieties, united by some common feature: origin, purpose, nature of processing, etc. For example, Construction Materials by nature and method of production, there are stone, metal, glass, bituminous, etc. Stone materials, in turn, are divided into natural, ceramic (fired) and non-fired.
The nomenclature of materials can be industry-specific and individual enterprise. The industry nomenclature is much broader than the enterprise nomenclature. It includes a range of materials produced by a number of enterprises in this industry. There are also trade nomenclature, which includes materials that are in the sphere of circulation.
Material nomenclature can be simple or complex. A simple nomenclature includes a limited number of products, and a complex one - a large number of materials, different in type, size, color, design and purpose.
To meet the needs of individual industries and construction, a large number of different materials and products are used, the demand for which is constantly changing.
To fully satisfy it, it is necessary to work on the formation of an assortment of materials and products, that is, their completing according to various criteria, taking into account the need for them of individual enterprises, organizations or the industry as a whole.
The work on the formation of a rational nomenclature of materials is constantly being carried out by departments, research institutes and laboratories. This refers to the use of materials and products with the greatest efficiency under the strictest regime and economy.
COMPOSITES
AS CONSTRUCTION
MATERIALS
Definition of composites. Classification
Of the many options for the definitions of composite materials given in the literature, we present the most concise one.
Composites Are materials consisting of chemically or physically dissimilar components that form a monolith with a clearly defined interface between the components.
The components are divided into two groups (phases):
- filler (or reinforcement) in the form of discrete particles or fibers - forms a discrete phase;
- binder (matrix) - in the form of any material that fills the space between the reinforcement and forms a continuous medium (Figure 1.1).
Figure 1.1. Components of composite materials:
1 - filler; 2 - binder; a- discrete particles;
b- fibers, threads, ropes; v- the cloth; G- sheet material
Armature perceives the main stresses arising in the composite under the influence of external loads, and determines the main mechanical characteristics.
Matrix ensures the joint operation of discrete reinforcement elements, combining them into a monolith, due to their own rigidity and adhesion at the matrix-reinforcement interface. This phase determines the mechanical properties to a lesser extent, but has a decisive influence on the technological characteristics, for example, the possibility of shaping and technological modes.
It should be noted that the concept of "filler" is general and includes not only discrete elements with high strength and rigidity. This concept also includes gas inclusions in the form of small-sized bubbles in the bulk of the matrix material. Such conditional reinforcement does not provide strength, but other functional characteristics, for example, high sound and thermal insulation capabilities. Composites should be distinguished from mixtures and solutions. In the first case, the material is not monolithic, in the second, there is no interface between the components.
Composite materials are classified according to two criteria - materials science and construction.
Material science classification takes into account the nature of the matrix and filler (Table 1.1).
Table 1.1
In the technical literature, composites are divided into classes. Each class was named according to the type of matrix: CMs with a polymer matrix are called polymer (PCM), with a metal matrix - metallic (MCM), with a ceramic - ceramic composite materials (CCM).
First grade composite materials - PCM is the most common in technology. They are based on various polymer resins.
The index PR in Table 1.1 denotes composites consisting of a polymer matrix and reinforcement of mineral origin. These are mainly fibers: carbon (graphite), glass, basalt, asbestos.
The group under the index PO includes polymer CMs with an organic filler. The fittings are presented in the form of aromatic polyamides (aramids). In addition, in materials that are not used in the production of aircraft as construction materials, paper, organic flakes, wood chips (chipboard threads - chipboard), cotton thread (fiberboards - fiberboard), etc. are used.
The combination of a polymer matrix with metal reinforcement is designated PM. Boron fibers are most often used as a filler and, less often, other metals, such as aluminum.
There is no information on the use of composites with a ceramic filler in a polymer matrix (PC group) in the production of aircraft. The name of the CM with a polymer matrix is formed from the name of the type of reinforcement with the addition of the word "plastic". For example: fiberglass, boroplastic, carbon fiber, organoplastic, etc.
Second class composites have a metal matrix: from light metals - aluminum, magnesium and heavy - steel and nickel alloys. The range and scope of use of metal composites is significantly less than polymer.
Today, they are used as reinforcement: in the MR group (with mineral reinforcement) - carbon fibers in combination with an aluminum matrix, materials are not found with an organic filler (MO group). The MM group (matrix and reinforcement made of metals) is represented in the industry mainly by boron aluminum, that is, a combination of an aluminum matrix with boron fiber.
The MK group (with ceramic filler) is little known.
In third grade Various types of ceramics are used as a matrix.
Information about the materials included in the groups KR, KO, KK is very limited. Basically, they are under development and research properties.
In the KM group, various metal powders are used as a reinforcing filler. Such materials are called cermets.
The fourth row of the table contains composites with a matrix other than polymers, metals and ceramics. The most famous composition here is carbon-carbon (CCCM). The armature in it is represented by carbon rods or threads. The matrix is also carbon, but with much lower strength.
Design classification shown in Figure 1.2.
To the first group include composites with reinforcement in the form of discrete particles. Two subgroups can be distinguished here: CM, reinforced with solid particles and gas-filled. Powders, flakes, chopped fibers, microspheres are used as solid particles.
Composites with a polymer matrix and a discrete filler are called "filled plastics".
An effective dispersed filler is a microsphere, which is small-diameter balls ( d= 0.05-0.2 mm) hollow inside and made, most often, of glass.
The second subgroup includes materials filled with small gas bubbles. Depending on the type of matrix, they received the corresponding name: foam plastics (polymer matrix), foam metals, foam ceramics, foam rubber, etc. If the gas bubbles are interconnected, then in the name of the materials the phrase "foam" is replaced by "poro", for example, "poroplastics".
Second group CM is characterized by the fact that the reinforcement has a fibrous structure. This type of CM can be divided into four subgroups: unidirectional composites, woven laminates, fibrous bulk weaves, nonwovens.
Unidirectional reinforcement can be: in the form of a primary thread (obtained immediately after production); filament (twisted) thread; roving, consisting of strands of filaments; tape-threads, interconnected in the transverse direction at a certain distance and forming an elongated flat surface; a rope - obtained by interweaving threads with the formation of a section close to a circle.
The second subgroup includes CM, consisting of layers of fabric, united by a matrix. The reinforcing filler is distinguished by the type of weave and the thickness of the threads.
The third subgroup is characterized by reinforcement, which is a volumetric interweaving of threads or rods. Spatial weaving can be organized with a different number of threads - from 3 to 11. Architectural solutions for creating spatial reinforcing configurations are given in books.
The fourth subgroup contains nonwoven-type filler materials. Nonwovens (Fliss-stoffe - "pile fabric") are chaotically reinforced structures in which staple fibers are connected in one of three ways - gluing, entangling with the formation of frictional interaction, stitching of the fabric with a textile thread.
To the third group highlighted materials with sheet-type filler:
ALORs and SIALs- a combination of alternately interconnected layers of thin sheet metal with layers of fabric (organic or glass), impregnated with a binder. The name ALOR comes from the first letters of the words - aluminum, organoplastic. The English name of this material is ARALL - Aramid Reinborud Aluminum Laminate. The first samples consisted of a high-strength aluminum alloy with a thickness of d = 0.1-0.3 mm, between which a fabric of Kevlar-49 aramid fibers was located.
SIALs consist of thin (0.25-0.6 mm) aluminum sheets and intermediate layers of fiberglass with a thickness of 0.2-0.4 mm. In Western Europe and the USA, such materials go under the name GLARE.
Getinax- layers of paper serve as a filler, binder - polymer resins.
Plywood- a combination of thin sheets of wood (veneer), laid in different directions with layers of binder.
The type of reinforcement and the form of laying largely determine the technology of manufacturing products from CM:
- for dispersed-filled composites, pressing methods are used in press chambers and injection molding machines;
- products from fibrous materials are obtained, most often, by applying them to mold-making mandrels;
- sheet CMs are processed by methods borrowed from the technical processes of processing metal parts - stamping, cutting, etc.
CLASSIFICATION OF MATERIALS.
Functional properties:
Physical (durability during operation)
Mechanical (depending on the type of material: TV, liquid, gas, plasma)
Chemical (state in certain environments and T)
Biological (effects on the respiratory system and human physiology)
Technological (applied processing processes)
Aesthetic properties - engineering and psychological (optimization of materials and objects to the psychophysiological characteristics of a person):
Shape geometry
Proportionality
Color background
Lightness
Saturation
Texture
Texture
Economic properties (analyzed when optimizing using objects with other materials):
Static application
Dynamic
Patentability
Groups of materials based on their characteristics:
Origin:
Natural (natural)
Artificial (created on the basis of natural)
· Types of products (roll, piece ...)
Raw materials (mineral, organic)
· Appointment (construction, construction and finishing, decorative and finishing ...)
· Scope (household appliances, construction, interior, exterior, sewing clothes ...)
* When classifying materials from neighboring groups, there is no clear boundary between them, and the material can be equally attributed to both groups.
** The classification of materials and products by purpose is the most convenient, it allows you to compare options for possible solutions and choose the most rational ones. But it does not cancel division on other grounds.
COMPOSITION OF CLAYS FOR INDUSTRIAL PRODUCTION.
Clay composition. Clay rocks, in terms of their chemical composition, consist of ...For the production of refractory products, refractory clays and low-iron bauxites are used, which have a number of advantages over clays.
In the production of cement, mainly low-melting clays, mudstones and shales are used, which are part of the cement charge. ...TYPES OF CASTING.
Lost wax casting is a process in which to obtain castings ... Chill casting is metal casting carried out by free casting of chill molds. Kokil - metal form with ...NATURAL AND ARTIFICIAL MATERIALS, FIELD OF APPLICATION.
Natural (natural) materials - ex. stone materials, other rocks (clays, sands, etc.). Natural materials rarely used without preparation. They almost always undergo technological processing (e.g. grinding, screening, remelting, machining, etc.)
Natural building materials
Where stone and wood used to be the main building materials, today their structural or static characteristics are largely ... Of course, not every type of stone or wood is suitable for every construction. How ... On a par with natural materials you can also put those that are used in combination with others ...Artificial building materials
The artificial material according to this definition is, for example, glass. Without glass or glass surfaces it is impossible to imagine ... Concrete is also artificial material... Regardless of the frequent ... Often, when evaluating synthetic building materials and their descriptions, the following interpretations are used: what in fact ...METALS, NON-METALS AND COMPOSITE MATERIALS, THEIR COMPOSITION AND CHARACTERISTICS.
Characteristic properties of metals: · metallic luster (characteristic not only for metals: it is also ... · good electrical conductivityMETAL POLISHING.
Approximate modes of metal polishing: Circumferential speed of polishing wheels, m / s: Steel, nickel, chromium 20-35 m / s ... Specific pressure on the treated surface, kg / cm2: Steel, nickel, chromium 1-2 kg / cm2 Copper, brass , bronze 0.8-0.3 ...Chemical polishing
During the polishing process, it is recommended to stir the solution or shake the parts in the container. This makes it possible to eliminate the accumulation of gas bubbles ... The disadvantages of such polishing include the difficulty of correcting ...Electrochemical polishing
To carry out electrochemical polishing of the workpiece, ... Removal of large protrusions 3 is called macro-polishing, and dissolution of microscopically small irregularities 4 - ...CASTING OF METAL UNDER PRESSURE, SURFACE CHARACTERISTICS.
Die casting of metals- a method of making castings from alloys, in which the alloy takes the form of a casting, quickly filling the mold under high pressure from 7 to 700 MPa. This method is used for alloys non-ferrous metals(based on zinc, aluminum, copper, magnesium, alloy tin-lead) due to their low melting point and also for some steels. Products can weigh from tens of grams to tens of kilograms.
Application
Manufactured by injection molding:
· Parts of automobile engines (including aluminum blocks, carburetor parts);
· Details of plumbing equipment;
Parts of household appliances (vacuum cleaners, washing machines, phones);
· Earlier - parts of typewriters.
Also, injection molding is used in the manufacture of computers.
Technical process
Press forms
Foundry molds ( Press forms) are usually made of steel. The shape of the mold cavity is chosen to be similar to the outer surface of the casting, however, dimensional distortions are taken into account. The mold also contains ejectors and movable metal rods that form the internal cavities of the products.
Casting machines are divided into two types - with a hot and cold pressing chamber.
Hot chamber casting machines
Zinc alloys are generally cast in hot chamber machines. The chamber is immersed in the melt. Under a relatively weak pressure of compressed air or piston, the melt from the chamber is forced into the mold.
Cold chamber casting machines
Such machines are used for die casting of aluminum, magnesium, copper alloys. Casting into molds takes place under a pressure of 35 to 700 MPa.
Advantages and disadvantages of the method
· high performance; · High quality of the surface (5-8 classes of purity for aluminum ... · exact dimensions of the cast product (3-7 classes of accuracy);A) Physical properties.
Density ( specific gravity) of the original rock is defined as the ratio of the resting mass mineral matter without pores and voids to its volume. To determine the density, a rock sample is crushed and sieved through ... When determining the density in a volumetric meter, a sample weighing 80 g (m1) is weighed out of dried powder. Then in the volume meter, ...DECORATION OF CERAMIC PRODUCTS IN RAW FORM.
POROSITY AND WETTABILITY OF THE MATERIAL, CHARACTERISTICS.
It is a dimensionless value from 0 to 1 (or from 0 to 100%). 0 corresponds to a material without pores; 100% porosity is unattainable, but possible ... The pores, as a rule, are filled with vacuum or gas with a density significantly ...Determination of porosity
Porosity is determined by the formula:, where:
· - true density sample material, kg / m³
- mass of the sample with pores, kg
· - sample volume with pores, m³
The volume of the sample is determined by hydrostatic weighing in the case of large samples with closed pores and measurement in the case of samples of regular shape.
Methods for measuring the characteristics of the porous structure of a substance
The following methods can be used to assess porosity in biotech applications:
Liquid extrusion porosimetry
Measures pore volume, diameter, size distribution with changes in temperature, external stress, and changes in the chemical environment, including changes in atmospheric humidity. Allows measurement of both hydrophobic and hydrophilic pores.
Capillary flow porosimetry
Measures a wide range of pore sizes, pore size distribution, gas permeability at various temperatures, loading, various chemical environments, including humid atmospheres.
Permeametry
Measures gas, vapor, liquid penetration rates of various chemical compounds over a wide range of temperatures, pressures, concentrations.
Water vapor permeability analysis
Measures water vapor transmission rate as a function of moisture gradient, temperature and pressure.
Vacuapore
The water intrusion porosimeter analyzes through, deaf, hydrophobic pores. Measures pore volume, diameter, distribution. The characteristics of hydrophobic and hydrophilic pores can be determined in combination with mercury porosimetry.
Mercury porosimetry
Measures the volume of through and dead pores, diameter, distribution.
BET sorbtometry
Measures surface area, volume of very small and blind pores, distribution, chemisorption of many different chemical media at different temperatures and pressures.
Pycnometry
Measures absolute and specific gravity materials.
Arising and receiving
The emergence of pores and their development is a complex process of the nucleation of the gas phase in a liquid medium. In a continuous liquid, the formation of a nucleus of a gas phase, ...Influence in industry
Negative
Pores are internal, volumetric defects. Unplanned pores can change the characteristics of the material for the worse: for example, make it less durable or prone to corrosion. But, in particular, in the welded business, volumetric defects do not significantly affect the performance of the joint. Therefore, the content of volumetric defects is allowed in welded seams, up to certain sizes and quantities.
Positive
Innovative biotechnological goods and products are increasingly used in healthcare, medicine, and pharmaceuticals. For example, drugs for ...Application
Examples of using
· Automotive industry
Battery industry
Biotechnology and healthcare
Ceramics
· Chemical industry
Filters and membranes
Food industry
Hydrocarbon industry
Geotextile industry
Production of personal hygiene products
Cotton wool production
Paper industry
Pharmaceutical industry
Metallurgical industry
· Textile industry
Examples of materials
Various foam polymers (expanded polystyrene, polystyrene, penoizol, etc.).
DefoamersALLOYS, THEIR PURPOSE FOR APPLICATION. EXAMPLES
COVALENT AND IONIC BONDING OF MATERIALS.
The characteristic properties of a covalent bond - directionality, saturation, polarity, polarizability - determine the chemical and physical properties ... The directionality of the bond is due to the molecular structure of the substance and ... Saturation is the ability of atoms to form a limited number of covalent bonds. The number of bonds formed ...SILICATE MATERIALS. EXAMPLES OF APPLICATION.
General description of silicate materials
Until the 50s, the only type of silicate autoclave products was silicate brick and small stones made of aerated silicate concrete. However ...Raw materials for silicate materials and products
Today natural silicate materials widely used in construction and industry - both as a raw material and as a final product. Silica serves as a raw material for the cement industry - the base in production ... Quartz sand has also been used since ancient times for the manufacture of glass and ceramics, as various additives and in pure ...METHODS OF METAL PURIFICATION DURING MELTING.
VARIETIES OF STONE MATERIALS MICROSTRUCTURES.
THERMAL CONDUCTING PROPERTIES OF MATERIALS. EXAMPLES OF USING.
Thermal conductivity is the property of a material to transmit heat through its thickness. The thermal conductivity of the material is estimated by the amount of heat passing through a sample of material with a thickness of 1 m, an area of 1 m 2 for 1 hour at a temperature difference on opposite plane-parallel surfaces of the sample, in 1 ° C. The thermal conductivity of a material depends on many factors: the nature of the material, its structure, the degree of porosity, the nature of the pores, humidity and the average temperature at which heat transfer occurs. Closed cell materials are less thermally conductive than communicating cell materials. Fine-pored materials have lower thermal conductivity than large-pore materials. This is due to the fact that air movement occurs in large and communicating pores, accompanied by heat transfer. The thermal conductivity of a homogeneous material depends on its density. So, with a decrease in the density of the material, the thermal conductivity decreases, and vice versa. The general relationship between the density of the material and thermal conductivity has not been established, however, for some materials with a moisture content of 1 ... 7% by volume, such a relationship is observed.
Moisture has a significant effect on thermal conductivity. Wet materials are more thermally conductive than dry materials. This is explained by the fact that the thermal conductivity of water is 25 times higher than the thermal conductivity of air.
Thermal conductivity characterizes the thermophysical properties of materials, determining their belonging to the class of thermal insulation (A - up to 0.082; B - 0.082 ... 0.116, etc.), structural and thermal insulation and structural (more than 0.210). Thermal conductivity of a material can also be characterized by thermal resistance - the value opposite to thermal conductivity.
Thermal conductivity is very important for materials used as walls and floors of heated buildings, for insulation of refrigerators and various heating units (boilers, heating systems, etc.). The cost of heating buildings directly depends on the value of thermal conductivity, which is especially important when assessing the economic efficiency of the enclosing structures of residential buildings, etc.
STAGES OF GOLDING NON-METAL PRODUCTS.
THERMAL PROPERTIES OF MATERIALS. EXAMPLES OF USING.
The most important thermophysical properties of materials for electronic equipment are the ability to remove heat from a radio component - i.e.
1) thermal conductivity;
2) heat resistance (heat resistance).
Heat transfer is known to be carried out by three physical mechanisms. Thermal conductivity is the transfer of heat through a solid. The vibrational motion of atoms has a wave character (phonon is a quantum of thermal energy of longitudinal atomic vibrations). Phonon thermal conductivity is the main one in solids at moderate temperatures, but where there are mobile electrons, there is also electronic heat conduction, and at high temperatures in a solid there is also a photonic transfer of heat. The number of phonons per unit volume depends on: on the heat capacity C (J / m 3 K), on the average phonon path length (of the order of several interatomic distances (1-10 nm) and the speed of motion close to the euke velocity V zv in this material
It is more convenient for calculations
Thermal power transmitted through a transverse platform 1m 2 l = 1 K / mDТ / D, at a temperature gradient
l - temperature gradient, S - area. Dimension of thermal conductivity - J / sec. DТ / DQ / t - power;
In materials with free electrons (metals, doped should be higher, but there are l semiconductors) due to electrons exclusion - C - diamond and BeO - ionic ceramics. For diamond C - 500 W / m. 0.1. Comparatively ~ 1; plastics ~ 360; Al - 200; Si - 130. Glass ~ K; BeO
a cheap heat (or cold) wire for a physical experiment can be made of copper.
But here is an example of the pressure of consumer properties on the designer. Diamond is very expensive and difficult to process, BeO is very toxic (in dusty form) during the production process, which prevents them from being widely used as heat-conducting materials. On the other hand, synthetic aluminum nitride Al N, an analogue of diamond in terms of the type and strength of bonds, is a very promising heat-conducting material.
Thermal expansion and temperature coefficient
HYDROPHYSICAL PROPERTIES OF MATERIALS. EXAMPLES OF USING
The properties associated with the effect of water on a material are called hydrophysical.
Hygroscopicity- the property of a porous-capillary material to absorb moisture from the air.
The absorption rate depends on the temperature and the relative humidity of the air. With an increase in relative humidity and a decrease in air temperature, hygroscopicity increases.
Hygroscopicity is characterized by the ratio of the mass of moisture absorbed by the material at a relative humidity of 100% and a temperature of +20 ° C to the mass of dry material.
Hygroscopicity adversely affects the quality of building materials. So, cement during storage under the influence of moisture in the air crumples and reduces its strength. Wood is very hygroscopic; it swells, warps, cracks from moisture in the air.
To reduce the hygroscopicity of wooden structures and protect them from swelling, the wood is coated with oil paints and varnishes, impregnated with polymers that prevent moisture from penetrating into the material.
Capillary suction- the property of porous-capillary materials to lift water through the capillaries. It is caused by surface tension forces arising at the interface between the solid and liquid phases.
Capillary suction is characterized by the height of the water level rise in the material capillaries, the amount of absorbed water and the suction intensity. When the foundation is in moist soil, groundwater can rise through capillaries and moisten the bottom of the building wall.
To avoid dampness in the room, arrange a layer of waterproofing that separates the foundation from the wall.
With an increase in capillary absorption, the strength, chemical resistance and frost resistance of building materials decrease.
Water absorption- the property of the material in direct contact with water to absorb and hold it in its pores.
Water absorption is expressed by the degree of filling the volume of the material with water (water absorption by volume Wo) or the ratio of the amount of absorbed water to the mass of dry material.
The water absorption of various materials is within wide limits (% by weight):
granite 0.02 ... 1;
dense heavy concrete 2 ... 5;
ceramic brick 8...25;
asbestos-cement pressed flat sheets - no more than 18;
thermal insulation materials 100 or more.
U high porous materials water absorption by mass can exceed porosity, but water absorption by volume is always less than porosity, since water does not penetrate into very small pores, and does not retain in very large ones. Water absorption of dense materials (steel, glass, bitumen) is zero.
Water absorption has a negative effect on other properties of materials: strength and frost resistance decrease, the material swells, its thermal conductivity increases and its density increases.
Humidity- the ratio of the mass of water present in the material to the mass (less often to the volume) of the material in a dry state.
Calculated using the same formulas as water absorption and expressed as a percentage. In this case, the mass of material is taken in a naturally moist state, and not in a state saturated with water.
When transporting, storing and using materials, they do not deal with water absorption, but with their moisture. Humidity varies from 0% (for absolutely dry materials) to the value of complete water absorption and depends on the porosity, hygroscopicity and other properties of the material, as well as on the environment - relative humidity and air temperature, contact of the material with water, etc.
For many building materials, humidity is normalized. For example, the moisture content of ground chalk - 2%, lump - 12, wall materials - 5 ... 7, air-dry wood 12 ... 18%.
Since the properties of dry and wet materials are very different, it is necessary to consider both the moisture content of the material and its ability to absorb water.
In all cases - during transportation, storage and use - building materials are protected from moisture.
Water resistance- the property of the material to maintain its strength when saturated with water.
The criterion for the water resistance of building materials is the softening coefficient Кр = К / Кс - the ratio of the compressive strength of the material saturated with water and the strength of the dry material Кс - It varies from 0 (for clay) to 1 (glass, metals).
Materials with a softening coefficient greater than 0.75 are called waterproof.
Moisture yield- the property of a material to lose what is in its numerical characteristic of moisture yield is the amount of water (in%) evaporated from the sample within 1 day at a temperature of 20 ° C and a relative humidity of 60%.
Moisture yield is taken into account, for example, when caring for hardening concrete, when drying walls and partitions plastered with lime mortar.
In the first case, a slow one is desirable, and in the second, a fast moisture yield.
Water permeability- the property of the material to pass water through itself under pressure.
The degree of water permeability mainly depends on the structure and porosity of the material. The more open pores and voids in the material, the greater its water permeability.
Water permeability is characterized by the filtration coefficient (m / h) - the amount of water (in m3) passing through a material with an area of 1 m2, 1 m thick in 1 hour with a difference in hydrostatic pressure at the boundaries of the wall of 9.81 Pa.
The lower the filtration coefficient, the higher the waterproof grade of the material.
Dense materials (granite, metals, glass) and materials with small closed pores (foams) are waterproof.
For waterproofing materials, it is important to assess not water permeability, but their waterproofness, which is characterized either by the time after which water seeps under a certain pressure through the material sample (mastic, waterproofing), or by the maximum water pressure at which it does not yet pass through the material sample for test time (special mortars).
Air, gas and vapor permeability- the properties of the material to pass through its thickness, respectively, air, gas and steam.
They depend mainly on the structure of the material, defects in its structure and moisture.
Quantitatively, air and gas permeability is characterized by air and gas permeability coefficients, which are equal to the amount of air (gas) (m3) passing through 1 m2 of material 1 m thick during 1 hour at a pressure difference on the surface of 9.81 Pa.
Air and gas permeability is higher if there are more communicating pores in the material; the presence of water in the pores reduces these properties of the material.
Vapor permeability occurs with different vapor content and pressure on both sides of the surface, which depends on the temperature of water vapor and is characterized by the vapor permeability coefficient, which equal to the number water vapor (in g), penetrating for 1 hour through 1 m2 of material 1 m thick at a vapor pressure difference on the surfaces of 133.3 Pa.
Wall and Decoration Materials must have a certain permeability, must "breathe". Sufficient gas and vapor permeability of wall materials prevent the destruction of walls from the outside from frost and subsequent thawing.
Vapor-proof materials are located on the side of the fence, from which the vapor content in the air is greater.
Water-saturated materials are practically gas-tight.
Paints and varnishes either reduce or retain the vapor permeability of building materials.
The lower the vapor permeability of the paint film, the higher its anti-corrosion properties.
Frost resistance- the property of a material in a state saturated with water to withstand a multiple number of cycles of alternating freezing and thawing without visible signs of destruction and without a significant decrease in strength and weight.
Frost resistance is one of the main properties that characterize the durability of building materials in structures and structures. With the change of seasons, some materials, undergoing periodic freezing and thawing in normal atmospheric conditions, are destroyed. This is due to the fact that the water in the pores of the material, when freezing, increases in volume by about 9 ... 10%; only very strong materials are able to withstand this ice pressure (200 MPa) on the pore walls.
High frost resistance is possessed by dense materials that have low porosity and closed pores.
Porous materials with open pores and, accordingly, with high water absorption are often not frost-resistant. Materials in which, after the tests established for them by the standard, consisting of alternate repeated freezing (at a temperature not higher than -17 ° C) and thawing (in water), cracks, delamination, spalling do not appear and which lose no more than 25% of strength and 5% masses are considered frost-resistant.
According to frost resistance, that is, according to the number of maintained freezing and thawing cycles, materials are divided into grades:
MRZ; 15; 25; 35; 50; 100; 150; 200; 300; 400 and 500.
So, the frost resistance grade of the plaster mortar Mrz 50 means that the mortar can withstand at least 50 cycles of alternating freezing and thawing without loss of strength and weight.
It is important to understand that the combined action of water and alternating temperatures is especially dangerous for porous materials. Frost resistance depends on the composition and structure of the material; it decreases with a decrease in the softening coefficient and an increase in open porosity.
The criterion for the frost resistance of the material is the frost resistance coefficient Kmrz = Kmrz / Knas - the ratio of the ultimate strength in compression of the material after testing to the ultimate strength in compression of water-saturated samples that have not been tested, at an equivalent age.
For frost-resistant materials, the mrz should be more than 0.75. It is also believed that if the softening coefficient of the stone is not lower than 0.9, then the stone material is frost-resistant.
MOLECULAR METAL LATTICES.
COMPOSITE MATERIAL, COMPONENTS. EXAMPLE WITH INDICATION OF COMPOSITION.
A composite material, also called a composite material or composite, is an artificially created non-uniform solid material consisting of two or more components that are different in physical and chemical properties that remain macroscopically separate in the finish structure.
The mechanical behavior of the composite is determined by the ratio of the properties of the reinforcing elements and the matrix, as well as the strength of the bond between them. The efficiency and performance of the material depends on the right choice the original components and technology for their combination, designed to provide a strong bond between the components while maintaining their original characteristics.
The most primitive composite material is clay and straw bricks, which were used in construction in ancient Egypt. Spacecraft are examples of the most advanced composites to withstand extreme environments. The most common composite is asphalt concrete or cement with steel reinforcement. We can also find it in the kitchen, where worktops are made of composite material, with granite or marble chips.
The composition of the composite material includes two categories of elements: matrix and reinforcing agent. It should be noted here that the word "matrix" has acquired a somewhat distorted meaning. It is often referred to as the tooling or shape that the product is created from. Further, the word "matrix" is used only in the meaning of a binder in a composite material.
The matrix material surrounds and fixes the reinforcing material, gives the product its shape. The reinforcing substance transfers its mechanical and physical properties to the product, and thus enhances the properties of the matrix. This relationship allows you to create a more perfect material with a set of properties that are inaccessible to each of its constituent materials separately. A wide range of reinforcing and matrix materials makes it possible to create a material with those properties that correspond to the purpose of the product.
Tooling is used to shape the composite material. The matrix material is placed in the tooling together with the reinforcing material. Then the matrix hardens, thereby creating the shape of the product. Depending on what kind of material is used as a matrix, this process is called chemical polymerization or setting.
The term "composite material" is most commonly used to refer to composites based on polymer matrices or resin. Polymers are very diverse, we are interested in several types (named by the name of the main substances in their composition) - epoxy, polyester, vinyl ester, phenolic, polypropylene, etc. The most common reinforcing substances are fibers and bulk substances. The final ratio of the matrix and reinforcing fibers has a great influence on the properties of the composite material. The less resin in the product, the stronger the product. The improvement of technology in the field of molding is aimed at achieving the ideal proportions of components in the material.
Methods of forming products from composite materials
Manual or contact molding, as the most common and cheapest method of creating a laminate, has a number of serious drawbacks: a large amount of resin in the product, which leads to its fragility; difficulty in achieving ideal proportions of matrix and reinforcing substancesVacuum forming
This process uses an open tooling into which the composite components are placed. From above, the equipment is closed with a polymer film (vacuum bag) or a silicone membrane. Then a vacuum is applied. The process can take place at room or elevated temperature and at atmospheric pressure. Variations of this technology use increased air or vapor pressure from the outside of the film (membrane).
Vacuum infusion (vacuum impregnation)
Autoclave. The process uses tooling and a membrane or plastic film. Materials ...RTM (Resin Transfer Molding) Closed Mold Injection
Other types such as pultrusion, winding, SMC (Sheet Molding Compound), DMC (Bulk Molding Compound), open molding ...Products and services
Composite materials have gained popularity, despite their high cost, in industries where mechanical properties must be combined with low weight and the ability to withstand high loads. The most frequently mentioned aerospace components (tails, wings, fuselage, propellers), hulls and oars of ships, car bodies, bicycle frames, rods. More than 50% of the wings and fuselage of the new Boeing 787 Dreamliner are made of composite materials.
PROPERTIES OF LIQUID IN SOAKED AND NON-SOAKED MATERIAL. EXAMPLES
NATURAL AND ARTIFICIAL MATERIALS. EXAMPLES OF USING.
By the type of raw materials, building materials are divided into natural and artificial, mineral and organic.
Natural, or natural, building materials and products are obtained directly from the bowels of the earth or by processing wood materials. These materials, in the manufacture of products from them, are given a certain shape and rational dimensions, without changing their internal structure, chemical and material composition... More often than others, wood and stone materials and products are used from natural ones. In addition, natural bitumen or asphalt, reeds, peat, fire and other natural products can be obtained in a ready-to-use form or by mechanical processing.
Artificial building materials are divided according to the main feature of their hardening (formation of structural bonds) into:
Non-firing - materials, the hardening of which occurs
runs at normal, relatively low temperatures with
crystallization of neoplasms from solutions, as well as mate
rials, hardening of which occurs in an autoclave
at elevated temperatures (175 ... 200 ° С) and water pressure
steam (0.9 ... 1.6 MPa);
Roasting - materials, the formation of the structure of which occurs in the process of their heat treatment mainly due to solid-phase transformations and interactions.
This division is partly arbitrary, because it is not always possible to define a clear boundary between materials.
In non-fired conglomerates, cementitious binders are represented by inorganic, organic, polymeric, and also mixed (for example, organomineral) products. Inorganic binders include clinker cements, gypsum, magnesia, etc.; to organic - bituminous and tar binders and their derivatives; to polymer - thermoplastic and thermosetting polymer products.
In conglomerates of the roasting type, ceramic, slag, glass and stone melts play the role of a binder.
Organic binders make it possible to obtain conglomerates that differ: according to the temperature of their application in construction - hot, warm and cold asphalt concrete; for workability - hard, plastic, cast, etc.; by the size of aggregate particles - coarse, medium and fine-grained, as well as finely dispersed.
Polymeric binders are important components in the manufacture of polymer concretes, building plastics, fiberglass and others, often called composite materials.
The classification of artificial building materials (conglomerates), united by a general theory, is expanding with the emergence of new astringents, development of new artificial aggregates, new technologies or significant modernization of existing ones, creation of new combined structures.
HIGH QUALITY STEEL, ITS COMPONENT COMPOSITION.
HAZARDOUS IMPURITIES IN METALS, THEIR INFLUENCE ON THE QUALITY OF THE PRODUCT.
TYPES OF METALLURGICAL FURNACES, THEIR PURPOSE.
MECHANICAL TREATMENT OF METAL.
separation of metals, primarily cutting with hacksaw blades, band saws, milling cutters, etc. special purpose for cutting sheet, profile andHomogenizing annealing.
dendritic or intracrystalline segregation, which can lead to: 1. Decrease in plasticity, due to the release of nonequilibrium brittle phases. 2.Reduction of corrosion resistance and development of electrochemical corrosionComplete annealing.
previous processing (casting, hot deformation or welding), softening the steel before cutting and reducing stress to give the steel certain characteristics. In general, type II annealing is carried out forLaser cutting of metal
materials based on electrochemical, electrophysical and physicochemical effects. Oxy-oxygen cutting, arc-penetrating plasma cutting and other physicochemical separation methods provideMETAL WELDING METHODS.
INDUSTRIAL METHODS OF METAL CASTING, GIVE EXAMPLES.
Foundry- one of the oldest and until now the main methods of obtaining metal products and blanks for various industries. Cast parts are used not only in mechanical engineering and instrument making. They are used in house building and road construction, are household and cultural items. This is due to the fact that this method makes it possible to obtain blanks and parts from different alloys of practically any configuration, with any structure, macro- and microgeometry of the surface, weighing from several grams to hundreds of tons, with any operational properties. If necessary and economically justified, the required indicators are achieved without the use of other technological processes (machining, welding, heat treatment and etc.).
At the present time, to obtain cast parts, several dozen technological processes and their variants are already used, which have a sufficiently wide versatility or are suitable for the manufacture of a narrow range of certain castings. Historically, these methods have been divided into conventional ones, by which they most often mean casting into sandy-clay molds, and special ones - these are all other types of casting. With an increase in the number of methods and options for obtaining castings, there is an increasing need for a clearer and more detailed classification of them according to the main general features in order to systematize the presentation of the essence of different methods in order to facilitate the understanding of the principles laid down in them and the creation of new more effective ways casting.
The main features of the conventional traditional method of casting in sandy-clay molds can be considered such important characteristics of the casting mold - the main tool of the technological process, such as the fact that it is one-time and detachable. The casting mold is made of dispersed refractory materials, hardened during manufacture by mechanical, chemical, physical or combined methods. An additional, but obligatory feature of casting into sandy-clay molds is that the mold is filled with melt by the usual gravity method from above from a ladle through a conventional gating system.
Other characteristics of the form (volumetric, shell, flask, flaskless, caisson, etc.) - the composition and properties of molding mixtures, methods of compaction or hardening, characteristics of castings and alloys for their production, production scale, etc. - determine only options for this technological process and types of equipment for specific operations.
The specified technological process of casting in sandy-clay molds and options for its implementation are the subject of the first part of the discipline - "Foundry".
Of the many varied special types casting, in the first place, it is advisable to distinguish methods with characteristic features that differ from the usual traditional technology of casting in sandy-clay molds.
Let us first note the processes with sharply different features of the casting mold.
First group- casting into one-time one-piece casting molds from dispersed materials while maintaining the gravity method of filling the mold from above from the ladle through the gating system, as in the traditional method.
A distinctive feature of these methods is the use of a one-time model, which is destroyed in any way to remove it from an integral mold before filling the mold with melt or even during the process of filling the mold. This group includes investment casting, burnout, soluble and gasification casting methods. Lost wax casting is currently the most common in this group, while a new and developing process is casting using models from photopolymer materials.
Second group- casting into semi-permanent or permanent split molds while maintaining the gravity method of filling the mold from above from the ladle through the gating system.
A common feature of these methods is the use of a demountable mold, consisting of semi-permanent or permanent and disposable elements. The design of the mold must allow the removal of the casting without damaging the reusable mold elements. The main method in this group is chill casting. There is also a known method of casting in carbon (graphite) forms. For reusable mold elements, other materials can apparently be used.
A characteristic feature third group methods is the presence of an additional effect on the melt when filling the mold and solidifying the castings. In this case, the type and design of the casting mold are determined by the requirements for castings and methods of exposure to the melt and crystallizing castings. These methods include the following:
a) pressing metal into a mold with high speeds by a piston system - injection molding. This method provides for the use of only metal detachable casting molds (molds), the use of rods and shaping inserts made of dispersed refractory materials is not excluded;
b) methods of casting with controlled, relatively low gas pressure - casting under low pressure, with back pressure, vacuum suction, etc. In these methods, you can use detachable and non-detachable casting molds from any materials with sufficient refractoriness and strength;
c) centrifugal casting of shaped castings is also associated with the possibility of using a variety of known designs of casting molds. However, in centrifugal casting of bodies of revolution (pipes, bushings, sleeves, etc.), molds of a special design are usually used - molds;
d) methods based on other principles of filling molds include squeeze casting, immersion casting of molds in a melt, etc.
The impacts on the melt poured into the mold, noted in points a), b), c) and d), continue after the filling of the form. This contributes to a certain increase in the density of castings and an improvement in the quality of their surface.
Similarly, it is possible to single out the methods in which the most significant effect on the melt during the crystallization period. They are used to obtain especially dense castings and castings with a special microstructure.
Fourth group- casting under all-round gas pressure (autoclave casting) using casting molds from various materials; die casting with crystallization under pressure (liquid stamping), in which metal molds are most often used.
Fifth group- casting methods using the effect on the melt, which has a significant effect on the formation of the microstructure of castings. These include methods using electric and electromagnetic effects on the melt before, during or after the melt enters the mold, processing it with ultrasound, etc.
Sixth group form methods based on the formation of properties of castings in continuous and semi-continuous casting processes. These processes include: continuous casting using stationary and movable molds; melt casting and semi-continuous casting, used to obtain castings of constant profile along the length; electroslag casting, casting with successive filling; freeze casting, etc. to obtain shaped castings.
Seventh group- methods for producing castings with various special properties, which include: reinforcement of castings, production of castings from composite materials, etc.
In the production of cast blanks, special types of casting take a significant place. Currently, 70 - 75% of the total production of castings (in tons) is obtained by the conventional method of sand casting and only 25 - 30% by "special" methods. However, these data do not accurately characterize the volume of production of castings using special types of casting. The methods of special casting are used to produce medium-sized castings from ferrous metals and the overwhelming majority, usually lighter, castings from non-ferrous alloys. Therefore, in terms of the number of castings obtained, special methods are not inferior to the usual method of sand casting.
PROCESS AND EQUIPMENT FOR MANUAL FORGING OF METALS.
TYPES OF METAL CONNECTIONS.
METALS CUTTING METHODS.
METHOD OF GALVANIZING TECHNOLOGY, COATING CHARACTERISTICS.
INDUSTRIAL CLAY FORMING.
COMPOSITION OF THE COMPOSITE MATERIAL. EXAMPLE OF A COMPOSITE, ITS APPLICATION.
Composite material (composition, KM) - an artificially created inhomogeneous solid material consisting of two or more components with a clear interface between them. In most composites (with the exception of layered), the components can be divided into a matrix and the reinforcing elements included in it. In composites for structural purposes, the reinforcing elements usually provide the necessary mechanical characteristics of the material (strength, stiffness, etc.), and the matrix (or binder) ensures the joint operation of the reinforcing elements and their protection from mechanical damage and an aggressive chemical environment. The mechanical behavior of the composition is determined by the ratio of the properties of the reinforcing elements and the matrix, as well as the strength of the bonds between them. The characteristics of the product being created, as well as its properties, depend on the choice of the initial components and the technology for their combination.
As a result of combining the reinforcing elements and the matrix, a composition is formed that has a set of properties that reflect not only the initial characteristics of its components, but also includes new properties that isolated components do not possess. In particular, the presence of interfaces between the reinforcing elements and the matrix significantly increases the fracture toughness of the material, and in composites, in contrast to homogeneous metals, an increase in static strength leads not to a decrease, but, as a rule, to an increase in fracture toughness characteristics.
A variety of reinforcing fillers and matrices are used to create the composition. These are getinax and textolite (laminates made of paper or fabric glued with thermosetting glue), glass and graphite plastic (fabric or wound fiber made of glass or graphite, impregnated epoxy adhesives), plywood ... There are materials in which a thin fiber made of high-strength alloys is filled with an aluminum mass. Bulat is one of the oldest composite materials. In it, the thinnest layers (sometimes filaments) of high-carbon steel are "glued" together with soft low-carbon iron.
Recently, materials scientists have been experimenting with the aim of creating more convenient in production, and therefore more cheap materials... Self-growing crystalline structures glued into a single mass with polymer glue (cements with additives of water-soluble adhesives), thermoplastic compositions with short reinforcing fibers, etc.
The fields of application of composite materials are not limited. They are used in aviation for highly loaded parts (sheathing, spars, ribs, panels, compressor and turbine blades, etc.), in space technology for units of power structures of apparatus, for stiffening elements, panels, in the automotive industry for lightening bodies, springs, frames, body panels, bumpers, etc., in the mining industry (drilling tools, parts for harvesters, etc.), in civil engineering (bridge spans, prefabricated elements of high-rise buildings, etc.) and in other areas National economy.
The use of composite materials provides a new qualitative leap forward in increasing the power of engines, power and transport installations, and reducing the weight of machines and devices. Composite materials with a non-metallic matrix, namely polymer carbon fibers, are used in the ship and automotive industries (racing car bodies, chassis, propellers); bearings, heating panels, sports equipment, computer parts are made of them. High-modulus carbon fiber is used for the manufacture of parts for aviation equipment, equipment for the chemical industry, in X-ray equipment and others. Carbon matrix carbon fibers replace various types of graphite. They are used for thermal protection, aircraft brake discs, chemically resistant equipment. Boron fiber products are used in aviation and space technology (profiles, panels, compressor rotors and blades, propeller blades, helicopter transmission shafts, etc.). Organofibers are used as an insulating and structural material in the electrical and radio industry, aviation technology, etc.
Consumer goods
Reinforced concrete is one of the oldest and simplest composite materials
Fiberglass and CFRP fishing rods
Fiberglass boats
Car tires
Metal composites
Sport equipment
Bicycles
Alpine skiing equipment - poles and skis
Hockey sticks and skates
Kayaks, canoes and paddles to them
Medicine
Material for dental fillings. The plastic matrix serves for good filling, the glass particle filler increases wear resistance.
Mechanical engineering
In mechanical engineering, composite materials are widely used to create protective coatings on friction surfaces, as well as for the manufacture of various parts of internal combustion engines (pistons, connecting rods).
CLAY PROPERTIES.
Clay plasticity is the ability of clay dough to take a given shape without cracking and stably ... Natural clays contain various impurities, such as quartz, calcite, micas, ... Binding ability - the property of clays to retain plasticity when mixed with non-plastic materials. This quality ...METAL CASTING METHOD.
Tools for molding and fixtures for casting by model: molding tools (tools used for filling the mold and removing ... Accessories for casting by models: Flask - frame (box without bottom) with molding ... Casting materials. Artistic casting involves the technology of use, for the most part , alloys, and not ...PROCESSING OF METALS UNDER PRESSURE, CHARACTERISTICS.
STRUCTURES OF LEVELS OF STUDYING THE PROPERTIES OF MATERIALS.
MECHANIZED METHODS OF DECORATION OF INDUSTRIAL CERAMIC PRODUCTS.
STAGE OF DECAPING METAL.
STAINLESS STEEL, ITS COMPOSITION, PROPERTIES. EXAMPLES OF USING.
Stainless steel is a complex alloy steel, sufficiently resistant to corrosion in so-called aggressive environments, including atmospheric conditions. The main alloying element is chromium (Cr (12-20%)). To enhance its corrosion properties and impart the necessary physicochemical properties, stainless steel is alloyed with nickel (Ni), titanium (Ti), molybdenum (Mo), niobium (Nb) and other elements.
About corrosion resistance of stainless steel can most often be judged by the content of the main alloying elements - chromium and nickel. With chromium content in stainless steel more than 12% of the alloys will already be stainless both under normal conditions and in mildly corrosive environments. If the chromium content is more than 17%, such alloys are corrosion resistant in more aggressive oxidizing (and not only) environments (for example, in nitric acid conc. Up to 50%).
Corrosion resistance of stainless steel is explained by the fact that a thin protective film of oxides or any other insoluble compounds is formed on the contact surface of the chromium-containing alloy with the medium, which prevents the environment from acting inside the alloy. In this case, both the uniformity of the metal and the corresponding state of the surface, as well as the absence of stainless steel susceptibility to intergranular corrosion (ICC). Since excessively high stresses in parts and equipment, as a rule, cause stress corrosion cracking in a number of aggressive media (especially those containing chlorides), they sometimes lead to destruction.
In strong acids (sulfuric, phosphoric, hydrofluoric, as well as in their mixtures), complex alloyed types of stainless steel and alloys with a higher nickel content with the addition of molybdenum, titanium, copper in various combinations. For each specific conditions (concentration of the medium and temperature), the appropriate grade is selected of stainless steel.
By chemical composition stainless steel subdivided into chromium, chromium-nickel and chromium-manganese-nickel alloys.
Chrome stainless steel finds application as a structural material for valves of hydraulic presses, turbine blades, fittings for cracking units, cutting tools, springs, household items.
Chromium-nickel stainless steel used in various industries. We especially note the following properties of such austenitic grade stainless steel:
1. Surface of stainless steel, due to its structure, it is of high quality and does not require additional processing for use in food production.
2. Chromium-nickel austenitic stainless steel does not magnetise, which makes it easy to identify it from other alloys, as well as use this property in industry. In general, stainless steel is used in almost all spheres of human activity, from heavy engineering to mechanics and electronics.
Of particular note steel 12Х18Н10Т(close foreign analogues - 304 AISI, 321 AISI). About applied to welded structures in various industries, for household appliances, v Food Industry (stainless steel - an irreplaceable material for equipment for processing, storage and transportation food products), in construction (stainless steel structures) and architecture of industrial buildings and shopping centers, in the chemical and petrochemical industries.
Stainless steel available the following standard products: stainless steel pipe, stainless sheet, stainless strip, stainless angle, stainless mesh, stainless hexagon, etc.
Stainless steel is, above all, a very practical material, at the same time, this material is both aesthetic and noble. Due to the variety of grades and types of surface, stainless steel able to meet absolutely any requirements that apply to construction stainless steel structures and finishing materials.
PHYSICAL AND MECHANICAL PROPERTIES OF WOOD.
The characteristics of wood in relation to the design of furniture are determined mainly by its physical and mechanical properties.
Physical properties of wood
An important decorative property and diagnostic feature is the color of wood., The characteristics of which vary widely (color tone ...Mechanical properties of wood
characterize its ability to resist external forces (loads). These include strength, hardness, deformability, impact strength.
Strength
Strength is the ability of wood to resist destruction under mechanical stress. It depends on the direction of the acting load, wood species, density, humidity, presence of defects and is characterized by ultimate strength - the stress at which the sample collapses.
There are the main types of force action: tension, compression, bending, shearing.
Hardness
Hardness is the ability of wood to resist the penetration of harder bodies into it.
The main strength indicators of wood
In terms of specific tensile strength along the fibers, i.e. strength per unit mass, wood is not inferior to structural steel and ...METHODS FOR REMOVAL OF HARMFUL IMPURITIES IN METALS.
PLASTIC METHODS OF ART WORKING OF METALS.
LIGHTING DEVICES USED LIGHT SOURCES.
CLASSIFICATION OF ROCKS.
Natural stone materials are obtained from rocks, deposited in the upper layers of the earth's crust in the form of continuous massifs and accumulations of debris of various sizes. Stone building materials are obtained by mechanical processing of rocks by splitting, sawing, crushing, trimming, grinding and polishing, therefore, their properties mainly depend on the quality of the original rock, its chemical, physical and mechanical properties... The quality of the rocks from which road building materials are made, in turn, depends on the mineralogical composition, structure, texture and freshness of the rock.
By geological origin (genesis), rocks are divided into three main groups with subgroups:
1) Outcasts(magmatic) - primary:
Deep (intrusive) - granite, syenite, diorite, gabbro, etc.
Outpouring (effusive) - diabases, porphyries, basalts, tuff lavas, etc.
2) Sedimentary- secondary:
· Mechanical, detrital deposits: 1) loose - boulders, crushed stone, gravel, sand; 2) cemented - sandstones, conglomerates, breccias.
· Organogenic and chemical formations - various limestones, dolomites, magnesites, gypsum, anhydrite.
3) Metamorphic(modified) - gneiss, marbles, quartzites.
Chemical studies of the composition of rocks in the upper layers of the earth's crust revealed the predominance of silica SiO2 - 59.12% and alumina Al2O3 - 15.34%, followed by calcium oxide CaO - 5.08%, sodium oxide N2O - 3.84, oxide iron FeO -3.80; magnesium oxide Mg -3.49; K2O - 3.13; Fe2O3 -3.08% and some other oxides and chemical elements. As can be seen, the rock-forming minerals of igneous rocks are diverse in their chemical composition. Out of about 2500 different minerals, about 50 are rock-forming.
The main rock-forming minerals are distributed in rocks used in construction in approximately the following proportions: feldspars(orthoclases and plagioclases) - 57.9-59.5%; hornblende, augite; olivine, coil - 16.8%; quartz - 12 - 12.6; mica 3.6-3.8; calcite (lime spar) - 1.5; kaolinite and other similar minerals - 1.1%, etc.
Rocks are more or less homogeneous mineral aggregates that make up the earth's crust, consisting of one or more minerals, Rocks consisting of one mineral are called simple or monomineral (quartzite, gypsum), and from several minerals (granite, basalt, gneiss ) - complex or polymineral.
Igneous rocks.
Chemical composition igneous rock is also diverse and consists mainly of silicon, aluminum, iron, calcium, magnesium, potassium and sodium. By ... From the magma that did not come out to the surface of the earth and solidified at a depth, under it ... Deep rocks.Sedimentary, rocky rocks.
According to the conditions of formation, sedimentary rocks are divided into rocks of mechanical deposition, chemical sediments and organogenic formation. From a wide variety of cemented sedimentary rocks here ... Sandstones consist of small grains of minerals (quartz), cemented by siliceous, calcareous, clayey, ...Metamorphic (modified) rocks.
Gneisses are similar in mineralogical composition to the granites from which they were formed, and differ from them in shale constitution. Gneisses, possessing a large ... Marble consists of intergrown calcite crystals with admixture of magnesite and others ... Quartzites were formed from siliceous sandstones, in which quartz grains were directly intergrown with each other. Quartzites ...SEDIMENTARY, MAGMATIC AND METAMORPHIC ROCKS. EXAMPLES OF USING.
MAGMATIC AND MECHANICAL ROCKS OF MINERALS. EXAMPLES OF USING.
ORGANOGENIC ROCKS OF MINERALS. EXAMPLES OF USING.
VISUAL METHOD FOR DETERMINING THE PROPERTIES OF MINERALS. EXAMPLES
STRUCTURAL ORDER OF JEWELRY STONES.
STRUCTURAL AND PHYSICAL PROPERTIES OF DECORATION STONES.
CRITERIA FOR ASSIGNING MINERAL TO PRECIOUS STONES.
CONCRETE, ITS COMPOSITION, PROPERTIES, PURPOSE AND COMMODITY CLASSIFICATION.
HYDRAULIC AND AIR BINDING AGENTS. EXAMPLES OF USING.
METHODS FOR DECORATIVE FINISHING OF WOOD PRODUCTS.
COMPOSITION AND PROPERTIES OF PLASTIC MASS.
CLASSIFICATION OF POLYMERS.
METHODS FOR LEVELING THREAD SURFACE ON STONE.
61. ACHROMATIC COLORS - white-gray-black colors that are absent in the color spectrum and differ only in lightness, cat. human consciousness ... 62. WATER RESISTANCE OF MATERIAL - sv-in material to resist for a long time the destructive action of moisture at periodic ...What will we do with the received material:
If this material turned out to be useful to you, you can save it to your page on social networks: